Magazijnautomatisering in de koellogistiek
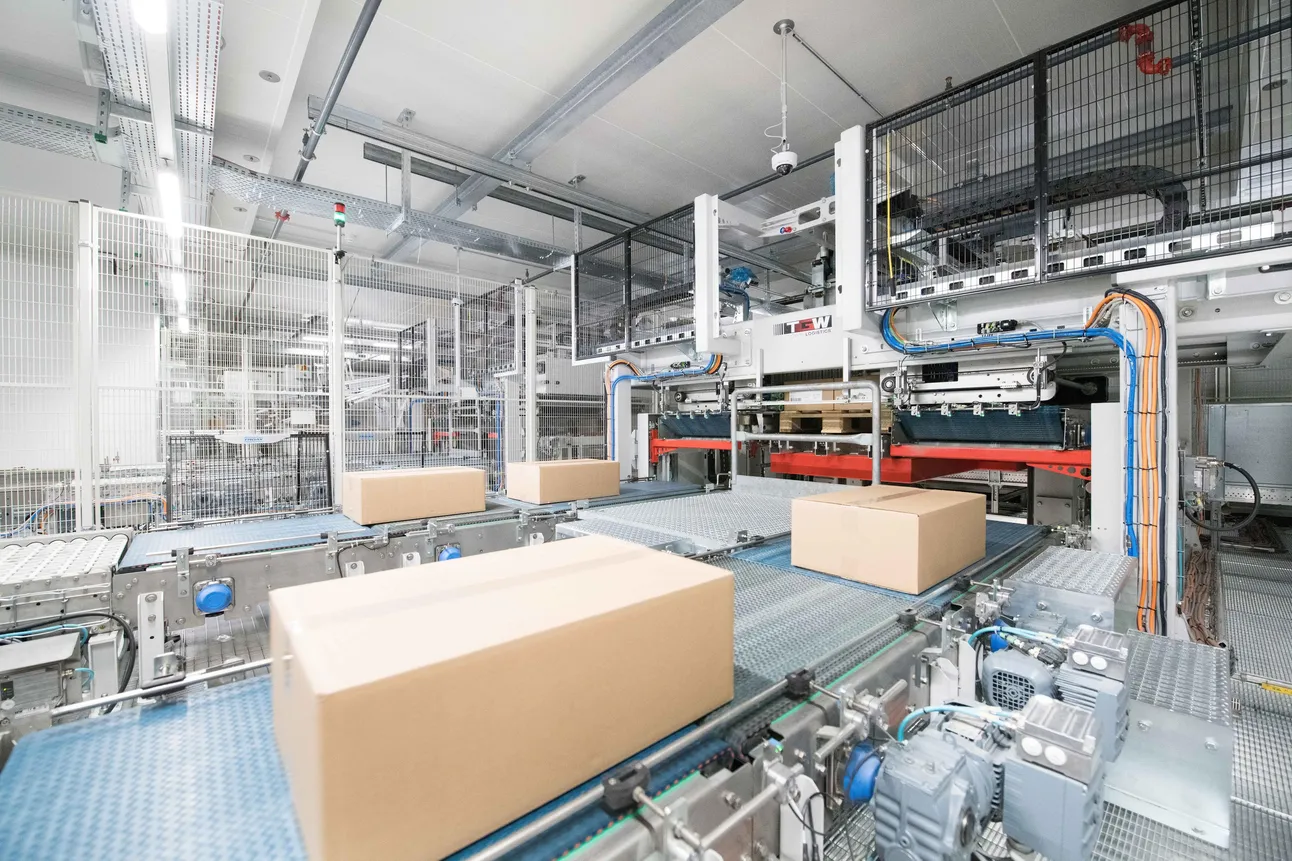
(Advertorial) Steeds meer bedrijven maken gebruik van automatisering in magazijnen voor vriesproducten. Michael Schedlbauer, Industry Manager for Grocery bij TGW Logistics Group, ziet verschillende redenen voor deze evolutie.
De coronapandemie zorgde in 2020 voor een onevenredig hoge groei in de sector van de koellogistiek. Mensen kookten vaker thuis en kochten meer diepvriesproducten zoals groenten of vis. Tegelijkertijd steeg de vraag naar levensmiddelen. In de VS groeide de vriessector met maar liefst 20 procent. Ook cijfers in Duitsland weerspiegelen deze trend.
Veel bedrijven investeren momenteel in koellogistiek. De rente is laag en mensen zullen altijd moeten blijven eten en drinken, ongeacht een stijging of daling van het aantal coronabesmettingen. Dit maakt de sector zeer stabiel en bestand tegen invloeden van buitenaf. Langetermijninvesteringen in nieuwe, geautomatiseerde magazijnen zijn daarom de moeite waard. Zo heeft TGW onlangs een project afgerond met de Nederlandse dienstverlener NewCold, die samenwerkt met een gerenommeerde voedingsmiddelen- en drankenproducent.
Op dit moment merken we twee trends in de levensmiddelenretail: centralisatie en insourcing. Het project met Coop in het Zwitserse Schafisheim is een mooi voorbeeld van de eerste trend. Het Zwitserse bedrijf heeft zijn koellogistiek gecentraliseerd en drie regionale distributiecentra samengevoegd op één plek. Bovendien is in het gebouw ook het regionale magazijn voor verse producten voor Noordoost-Zwitserland gevestigd. Dit betekent dat de oppervlakte van 240.000 m2 is ingedeeld is in verschillende temperatuurzones.
Drijfveren voor geautomatiseerde koelmagazijnen
De Total Cost of Ownership verklaart waarom magazijnautomatisering een belangrijk element is in koellogistiek. In de levensmiddelenretail gelden strenge eisen. De pickkwaliteit moet perfect zijn, leveringen moeten op tijd binnen zijn en de koelketen mag niet onderbroken worden. Bedrijven moeten dit zonder haperingen en met één druk op de knop kunnen bewijzen. Als je door automatisering minder afhankelijk bent van de arbeidsmarkt, dan zorgt dat voor extra gemoedsrust bij veel logistiek verantwoordelijken.
Daarnaast is het in West-Europa bijna onmogelijk om medewerkers te vinden om vriesmagazijnen te bemannen. De werkomstandigheden zijn zwaar in de ijskoude temperaturen. Het personeelsverloop is hoog, ondanks de forse loonpremies die in veel landen worden betaald. Het is een enorme uitdaging om medewerkers te vinden, op te leiden en te behouden. Bovendien moet je als werkgever ook rekening houden met de andere richtlijnen in dit werkgebied. In vergelijking met magazijnen op kamertemperatuur zijn werknemers maar gedurende een relatief korte periode in deze omgeving, maar dat is absoluut noodzakelijk om het werk op lange termijn haalbaar en draaglijk te houden.
In deze tijden van ernstige klimaatveranderingen zijn bedrijven zich ook bewust van hun verantwoordelijkheid om zuinig om te gaan met natuurlijke hulpbronnen. Coop bijvoorbeeld kon de uitstoot van CO2 tot 10.000 ton per jaar verminderen door zijn distributiecentra te centraliseren in één enkele, innovatieve, geautomatiseerde en volume-geoptimaliseerde locatie.
Vernieuwend shuttleysteem om energie te besparen
Om ervoor te zorgen dat de shuttlesystemen bij -25°C werken, maakt TGW gebruik van de nieuwste robot- en aandrijftechnologie. De oplossingen zijn specifiek aangepast aan de noden van de klant en bestaan uit meerdere modules. Het proces begint bij goederenontvangst. De gepalletiseerde goederen worden gecontroleerd, voorzien van een label en bij een temperatuur van -25 °C in het hoogbouwmagazijn ingevoerd. Bij het orderverzamelen worden de goederen verzameld en gedepalletiseerd, overgebracht in bakken en opgeslagen in het shuttleysteem. Om de goederen vervolgens te kunnen picken volgens het ‘goods-to-robot’ principe, worden de benodigde artikelen uit de opslag gehaald, de bakken op volgorde gezet en naar behoefte leeggemaakt. Het palletiseren wordt geautomatiseerd met behulp van Autostax-robots. Daarna worden de artikelen volgens verschillende criteria op de ladingdrager van de klant, meestal een pallet of rolwagen, gerangschikt. Tot slot worden de ladingdragers van de klant automatisch vastgezet en in de zone voor uitgaande goederen in de juiste volgorde klaargezet voor het transport met de vrachtwagen.
Meer informatie vind je op www.tgw-group.com
Foto: TGW