Flexibele automatisering voor logistieke dienstverlener
DHL experimenteert met nieuwste generatie transportrobots
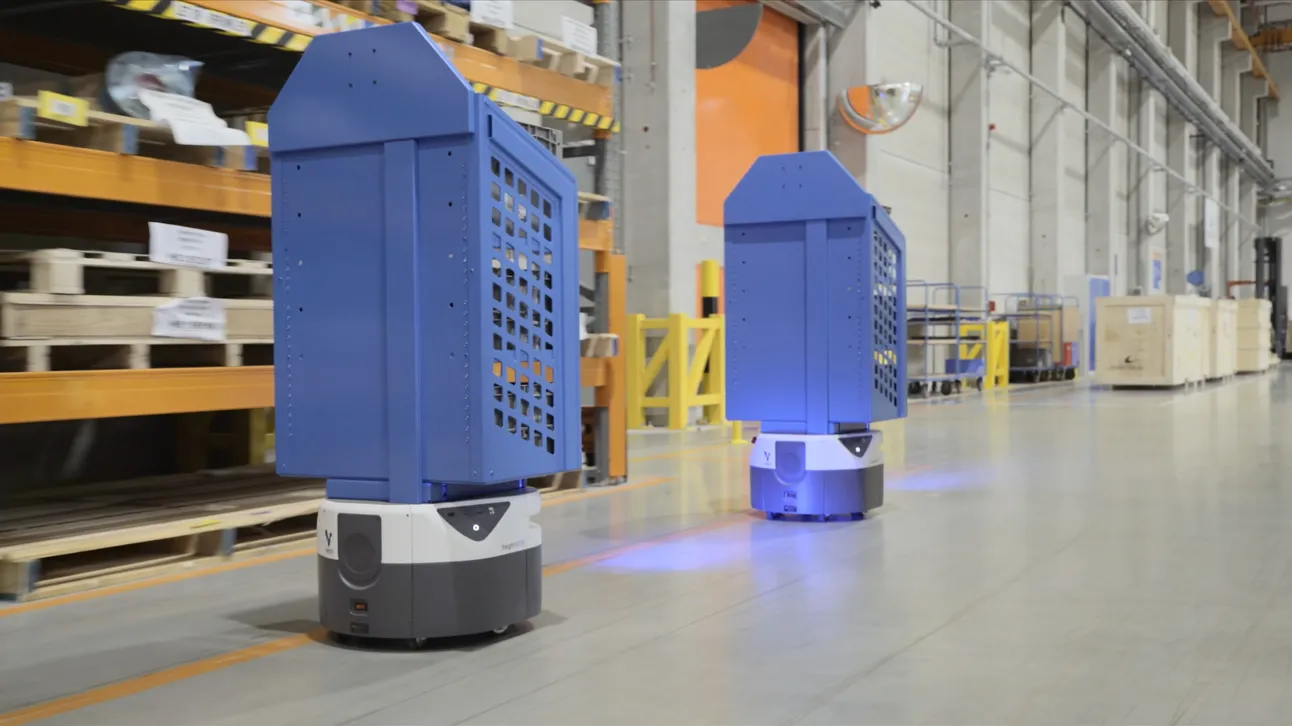
Hoewel automatisering binnen het magazijn belangrijke voordelen kan opleveren, is dat voor logistieke dienstverleners geen evidentie. Vooral hun kortlopende contracten zorgen ervoor dat zij zich niet willen of kunnen binden aan het keurslijf van een sterk geautomatiseerd systeem. Toch is dat voor DHL Supply Chain geen excuus om helemaal niet te automatiseren. Zo lopen bij de logistieke dienstverlener enkele innovatieve projecten met flexibele transportrobots. Bastiaan Snaterse, manager Supply Chain Consultancy & Innovation bij DHL Supply Chain BeNeLux geeft er tekst en uitleg bij.
DHL Supply Chain maakt deel uit van de Deutsche Post DHL Group. Naast DHL Supply Chain bestaan nog enkele andere gekende divisies, zoals DHL Post, e-Commerce & Parcel, DHL Express en DHL Global, Forwarding & Freight. In de Benelux beschikt DHL Supply Chain over meer dan 20 sites, goed voor zo’n 800.000m² magazijnoppervlakte. Daar doen ruim 100 klanten uit diverse sectoren een beroep op de logistieke diensten van deze divisie, die in de Benelux circa 4.5000 medewerkers telt. Daarbij denken we met name aan automotive, technology, engineering & manufacturing, life science & healthcare en consumer & retail.
Oog voor flexibele automatisering
“Zelden hebben we contracten van zeven of tien jaar of langer. Dat zorgt dat we verregaande automatische systemen heel moeilijk terug kunnen verdienen”, begint Bastiaan Snaterse. “Nochtans zijn we een grote voorstander voor innoverende technologieën die een meerwaarde kunnen betekenen voor onze operaties. Robotica, zelfrijdende voertuigen, augmented reality, drones, Internet of Things en big data, het zijn evoluties die we niet schuwen. Binnen onze organisatie is het DHL Trend Research die voor ons continu de belangrijkste ontwikkelingen spot. Omdat wij ons niet kunnen binden aan starre transport- en opslagsystemen, zijn de flexibele automatische transportoplossingen die momenteel hun intrede doen voor ons erg interessant. Misschien moeten sommige van die oplossingen nog wat rijpen, maar we willen ons wel op hun komst voorbereiden.”
Daarom heeft DHL besloten via proefprojecten aan de slag te gaan met flexibele transportrobots in enkele van zijn magazijnen.
Bastiaan Snaterse: “DHL Trend Research is verbonden aan onze innovatiecentra, die we bijvoorbeeld in Duitsland hebben. Die innovatiecentra komen vaak in contact met bijvoorbeeld startups die hun nieuwe oplossingen promoten. Een van die spelers is het Amerikaanse Fetch Robotics, een bedrijf dat nog maar weinig projecten in Europa heeft, maar wel aangeeft vooruit te willen. Daarom wilden we hen een kans geven om zich in een van onze magazijnen te bewijzen. Door kleinschalig met transportrobots te beginnen kunnen we bovendien onze medewerkers geleidelijk aan laten wennen aan een nauwe samenwerking met zelfrijdende voertuigen.”
Pilootproject met Amerikaanse transportrobot
Voor het pilootproject met Fetch Robotics werd binnen de organisatie een site gezocht die interessante stromen heeft om met een transportrobot op te vangen en openstaat voor dit type innovatie. De keuze viel op de site van Kampen, het meest noordelijke magazijn waar DHL Supply Chain in Nederland actief is. Dit magazijn is eigendom van de maritieme solutions en service provider Wärtsilä. DHL verzorgt er de opslag, handling en expeditie van onderdelen, gaande van bouten en moeren tot cylinder liners van 16 ton. Binnen het magazijn vinden we dan ook uiteenlopende opslaggebieden terug. Vanuit één enkele ontvangstzone worden goederen naar het automatische binmagazijn, een bulkstapelzone of klassieke rekken verstuurd.
Binnen die context werd een pilootproject met flexibele transportrobots opgezet voor het transport van kunststof bins, die in de ontvangstzone met onderdelen worden gevuld. Met de robots werd het transport uitgevoerd van de ontvangstzone naar het automatisch binmagazijn, een veertigtal meter verderop. Ook het transport van goederen verzameld uit het automatisch binmagazijn naar de expeditiezone vond met de transportrobots plaats. In de oorspronkelijke situatie werden bins en gepickte goederen verzameld op pallets, die met bemande elektrische pallettrucks werden getransporteerd.
Die trajecten werden binnen het proefproject opgevangen door in totaal vier transportrobots van Fetch Robotics. Die autonome HMIshelf ‘vrachtrobots’ zijn uitgerust met fetchcore, een cloud fleet management software om zich een beeld te kunnen vormen van zijn omgeving. Elk toestel kan maximaal 78 kilo meenemen, aan een snelheid van 2m/s. “In eerste instantie leek me dat traag, maar als je de robots in de praktijk ziet rondrijden, valt dat eigenlijk heel goed mee”, geeft Bastiaan Snaterse toe.
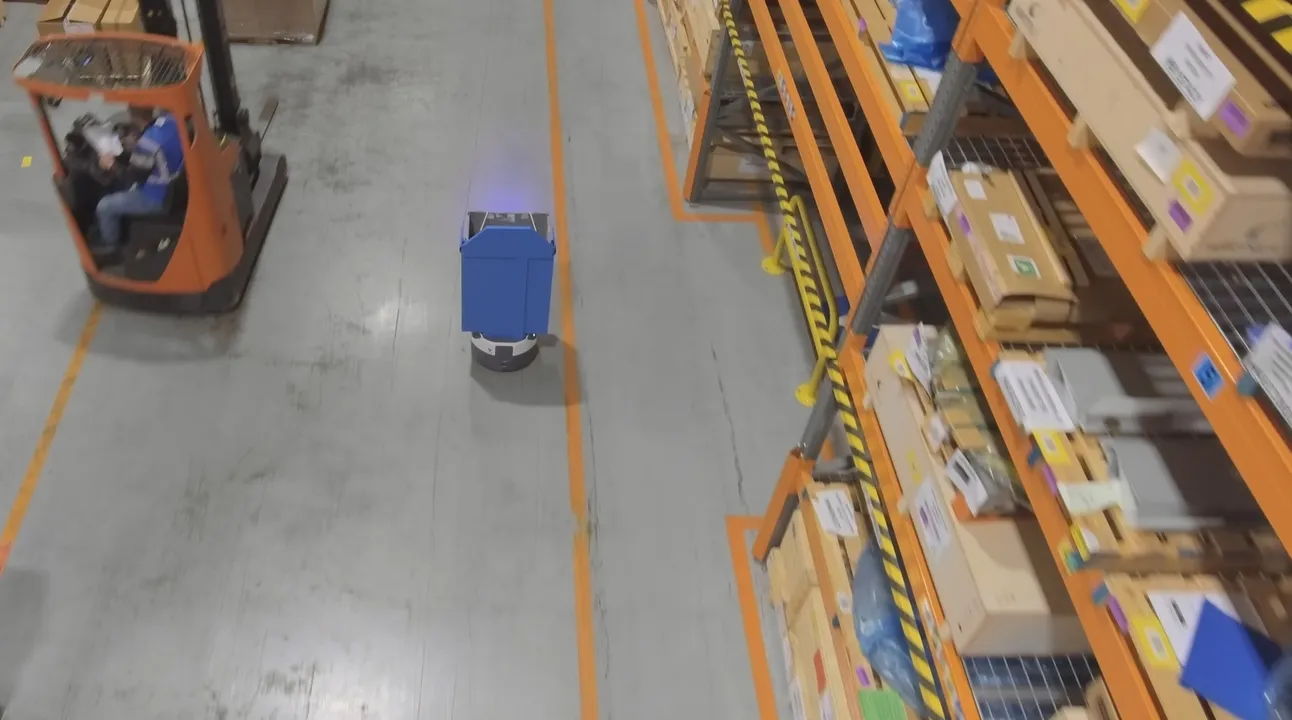
Map & go
Om het systeem te implementeren, moet in een eerste stap het magazijn worden ‘gemapt’. “Dat doe je door met behulp van een joystick het toestel door het hele magazijn te laten rijden. Op die manier bouwt de transportrobot als het ware zijn eigen kaart op, rekening houdend met alle mogelijke obstakels. Die kaart wordt naar de centrale software gestuurd, van waaruit ze naar de andere robots wordt gedistribueerd. Op die manier hoef je het traject maar met één enkele robot af te leggen”, legt Bastiaan Snaterse uit. “Een volgende stap bestaat erin de gewenste routes en de laad- en loslocaties voor de robots aan te geven. Die routes definiëren en de user interfaces maken, ging heel gemakkelijk. We hebben geen gespecialiseerde IT-mensen in onze magazijnen, dus die grote gebruikersvriendelijkheid is voor ons erg belangrijk.”
Dit automatisch rijdend voertuig heeft bovendien een semantisch begrip van zijn omgeving. Zo weet het wat zijn positie in het magazijn is en kunnen er ‘verboden’ zones voor de Fetch worden ingesteld, door die in het systeem rood te markeren. Ook als er omwille van veiligheidsredenen in bepaalde zones trager moet worden gereden, kan dat via een aparte zone worden gemarkeerd. Verdwijnen er in de oorspronkelijke mapping hindernissen, dan kunnen die in de software gemakkelijk ‘weggegomd’ worden.
De transportrobot signaleert objecten en probeert die met een uitwijkmanoeuvre te passeren. Als dat niet lukt – zelfs niet na een aantal pogingen – stippelt de transportrobot een alternatieve route uit. Is de batterij bijna leeg, dan trekt hij ook zelfstandig naar het oplaadstation. Bij de automatische sturing wordt enerzijds een laser voor langere afstanden gebruikt, anderzijds een 3D-camera voor wanneer het toestel objecten of personen nadert. Voor extra veiligheid zorgt de blue spot, die iets voor hem uit schijnt. Op die manier merken de medewerkers hem steeds tijdig op.
B. Snaterse: “Concreet wijzen we aan een robot een bepaald traject toe vanaf pakweg acht uur ’s morgens tot vier uur ’s middags. Op de robot zelf zit een touchscreen waarmee de medewerker aangeeft dat de robot is volgeladen en dat hij kan vertrekken. Komt hij op zijn bestemming aan, dan geeft een andere medewerker aan wanneer de robot is gelost en hij opnieuw mag vertrekken. Aan de hand van dat display kunnen medewerkers ook de bestemming van de robot veranderen, zodat hij bijvoorbeeld de opdracht kan krijgen om terug te keren of eerst een volgende bestemming aan te doen.
Wärtsilä omarmt Fetch Robotics
De ervaringen tijdens het eerste proefproject waren overwegend positief. De mogelijke productiviteitswinst bleek erg veelbelovend. Volgens de terugverdienanalyses kunnen vier robots ruim 30 kilometer intern transport met operators uitsparen per dag. In ongeveer vijf jaar tijd kunnen deze robots worden terugverdiend.
Een andere grote troef is de grote gebruikersvriendelijkheid. Ook wat betreft het vermijden van obstakels, doet de Fetch wat moet. “In eerste instantie stopte de robot iets te laat naar onze zin, letterlijk net voor je voeten. Daarom hebben we de leverancier gevraagd hem iets eerder te doen vertragen, zodat hij nu al vertraagt van zodra hij een hindernis detecteert”, weet Bastiaan Snaterse. “Verder moeten we ook het verkeersplan in ons magazijn aanpassen, zodat alle medewerkers weten welke paden de robots volgen. Zo willen we medewerkers er bijvoorbeeld attent op maken dat een robot op een bepaald punt naar links kan afslaan. Dat is nog veiliger voor voetgangers en maakt tegelijk heftruckchauffeurs meer attent op het doen en laten van deze ‘zwakkere’ weggebruikers.”
Een aandachtspunt is wel het belang van een goede wifi-connectie. Op zich werkte die tijdens het proefproject prima, tot te veel mensen binnen het gebouw ook het wifinetwerk gingen gebruiken. Op zulke momenten had de robot een tiental seconden nodig om te starten nadat hij een opdracht had gekregen. “Maar het grootste struikelblok was wel dat de Fetch een probleem had met onze veiligheidshesje”, vertelt Bastiaan Snaterse. “Met name voor de lasergeleiding vormen die hesjes een stoorzender, waardoor de robot zich niet meer kan oriënteren. In alle DHL-magazijnen draagt elke medewerker zo’n hesje, dus op dat vlak konden en wilden we niet toegeven. Daarom hebben we dit proefproject even stopgezet, totdat de leverancier het probleem had verholpen.”
Intussen is de transportrobot zo aangepast dat de voordelen groot genoeg zijn om de transportrobot binnen het magazijn van Wärtsilä effectief in gebruik te nemen. “Dit type experimenten doen we steeds in nauwe samenwerking met de klant. Wärtsilä was dan ook nauw bij het proefproject betrokken. Door de positieve resultaten overweegt Wärtsilä nu zelfs de transportrobot in zijn fabrieken te implementeren. Daarom bekijken we nu ook samen met hen voor welke toepassingen we de robots nog kunnen inzetten”, voegt Bastiaan Snaterse eraan toe.
Testen met Effibot
Daarnaast heeft DHL ongeveer een jaar geleden enkele transportrobots van de Franse firma Effidence aangeschaft om er binnen zijn organisatie mee te experimenteren. Intussen heeft de Effibot, de robot van die leverancier, al op een aantal sites proefgedraaid.
Recent liep een pilootproject met de Effibot in het multi-client magazijn in Mechelen, met voornamelijk automotive en technology klanten. Daar was het de bedoeling dat hij een dubbele functie zou krijgen. In eerste instantie is de Effibot gemaakt om pickers via een afstandsbediening – de zogenaamde ‘follow me’ functie – bij te staan tijdens het picken. Zo hoeven orderpickers tijdens de piekmomenten, waar orders binnen 20 minuten uitgestuurd moeten worden, niet over en weer lopen met pickkarren, maar wordt die functie overgenomen door de Effibot. Daarnaast kan de Effibot sinds kort ook autonoom rijden.
B. Snaterse: “We hebben getest of de Effibot in dat magazijn enerzijds de pickers kon bijstaan bij het pick & packproces van auto-onderdelen en anderzijds het autonoom transport tussen het packstation en de staging kon verzorgen. Ook daarvoor hebben we het pand in de bijbehorende software gemapt. In combinatie daarmee hebben we reflectoren langs het traject van de Effibot moeten plaatsen. Voor het autonoom transport van de packing naar de staging moesten we de Effibot ook koppelen aan de kar met de dozen voor verzending.”
Uit dit proefproject bleek dat zowel de ‘follow me’ als de autonome functie van de transportrobot op zich prima werkten, maar dat beide lastig te combineren waren.
B. Snaterse: “Een robot die autonoom rijdt, moet kunnen stoppen als hij een object op bijvoorbeeld een meter detecteert. Wanneer de robot de picker op de voet volgt, moet de afstand uiteraard korter zijn. Het bleek momenteel nog niet mogelijk die toleranties vlot te veranderen tussen de twee functies door. Daarom hebben we het proefproject moeten beperken tot het autonome gedeelte. Maar als we de Effibot enkel voor dat luik in het proces gebruiken, is het toestel niet rendabel. Een ander pijnpunt was dat de Effibot met zijn hoogte van ongeveer één meter slecht zichtbaar is voor onze hef- en reachtruckchauffeurs. Die zaken hebben we dan ook teruggekoppeld naar de leverancier zodat zij daarmee aan de slag kunnen gaan. Op die manier willen we samen met de leverancier tot een product komen dat nog beter tegemoetkomt aan onze wensen en eisen, zodat we tot meer rendabele business cases komen.”
“Als we de resultaten van al onze proefprojecten samenvatten, zijn we ervan overtuigd dat dit soort oplossingen in de toekomst langzaam maar zeker de weg binnen onze magazijnoperaties gaan vinden. Hier en daar moeten uiteraard nog kinderziektes worden weggewerkt, maar als leveranciers daarin slagen, is het best mogelijk dat we nog een versnelling hoger schakelen op het vlak van autonoom transport”, besluit Bastiaan Snaterse.
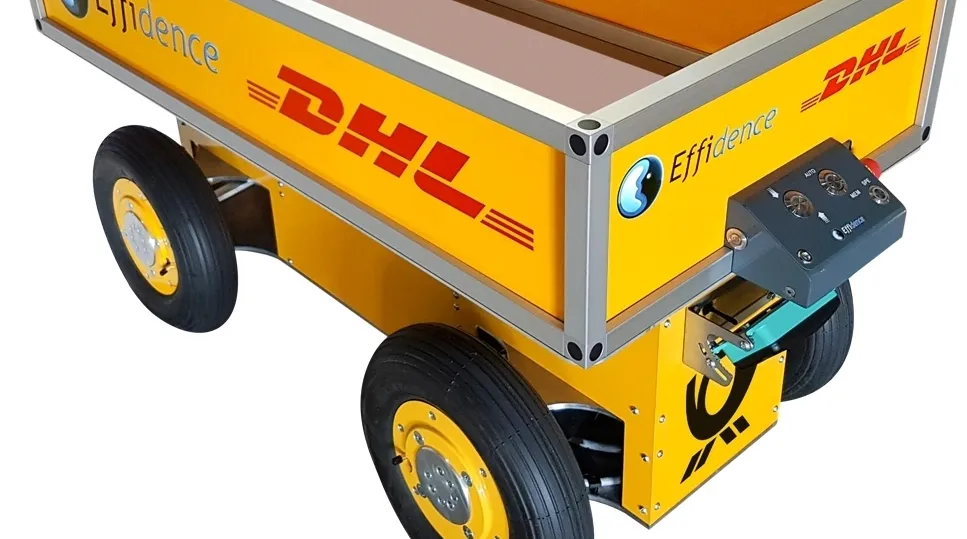