Wanneer lonen automatische laad- en lossystemen?
VIL en Universiteit Antwerpen brengen mogelijkheden in kaart
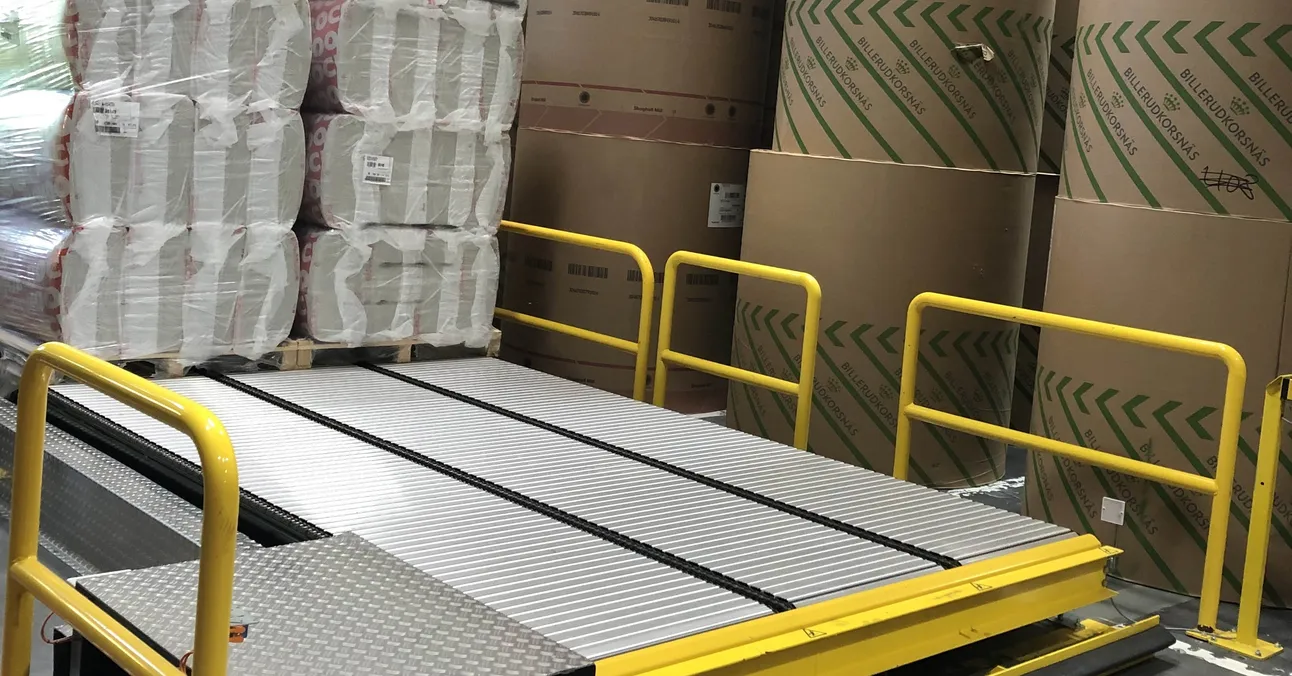
In de meeste bedrijven verloopt het laden en lossen van vrachtwagens nog manueel. Dat is evenwel een arbeidsintensief en tijdrovend proces. Samen met de Universiteit Antwerpen (UA) nam VIL de bestaande laad- en lossystemen onder de loep. Tijdens dat zogeheten OptiCharge-project werd duidelijk dat automatisering aan de laad- en loskade op verschillende vlakken voordelen biedt, maar dat veel afhangt van de technologie, de goederen en de bedrijfsspecifieke context. In het kader van het onderzoek werd ook een tool ontwikkeld om een idee te krijgen van de rentabiliteit van dergelijke systemen.
Zowel verladers als logistiek dienstverleners zien laden en lossen doorgaans als een noodzakelijk kwaad. Zo wachten vrachtwagens dagelijks een aanzienlijk aantal uren bij magazijnen tot de lading geladen of gelost is. Gezien het nijpend tekort aan en de hoge loonkosten van chauffeurs, weegt dat op de efficiëntie van logistiek dienstverleners. Naast het feit dat dit proces tijd in beslag neemt, is het risico op fouten, schade en ongevallen reëel. Als het mogelijk is dat proces op een rendabele manier te automatiseren, dan is dat dus het overwegen waard.
Maar terwijl er in fabrieken en magazijnen al volop wordt geautomatiseerd, hinkt de laad- en loskade op dat vlak nog achterop. Met het OptiCharge-project wilde VIL samen met de Universiteit Antwerpen als projectpartner die drempel verlagen, door de mogelijke opportuniteiten te onderzoeken.
Helikopterblik op bestaande laad- en lossystemen
Binnen het project voerde VIL een marktstudie uit naar de beschikbare automatische laad- en losoplossingen. Daarnaast werden een business case en proof of concept uitgewerkt bij Barry Callebaut (zie kader).
De beschikbare systemen kunnen we grosso modo in drie verschillende types opdelen: AGV-gebaseerde systemen, one-shot-gebaseerde systemen en semiautomatische systemen.
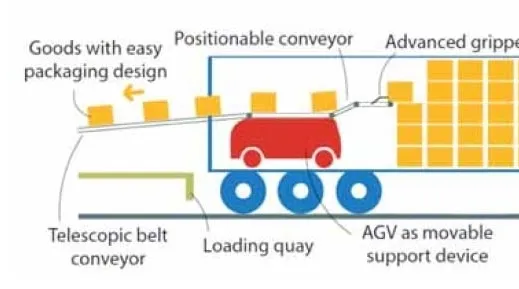
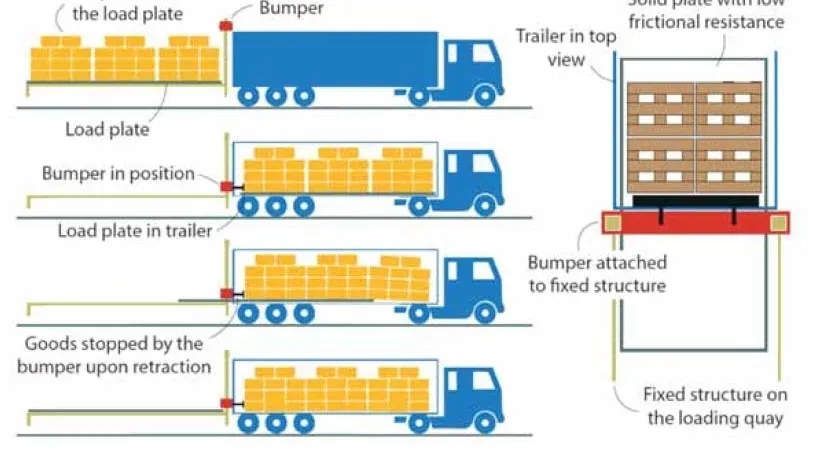
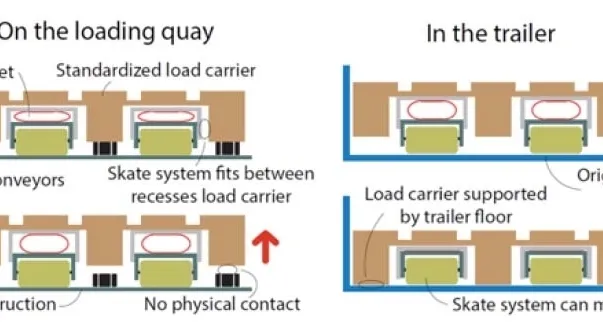
AGV-gebaseerde systemen
Bij AGV-gebaseerde systemen (automated guided vehicles) ondersteunen industriële robots het laad- en losproces. Dat doen ze op zelfstandige basis, met conventionele navigatietechnologieën of meer geavanceerde 360°-visietechnologieën (zoals lidar of sonar). De zogenaamde automatic trailer loading (ATL) AGV kan grote goederen in smalle ruimtes manoeuvreren, waardoor hij vlot automatisch goederen aan de kade kan laden en lossen.
Wel moeten we er rekening mee houden dat een ATL AGV enkel kan werken met gestandaardiseerde ladingdragers, zoals europallets. Ook moet de nodige IT-infrastructuur worden opgezet om de AGV te laten communiceren met bijvoorbeeld het WMS.
Een voordeel is dat het aantal AGV’s kan worden opgeschaald op basis van de noden. De implementatie van AGV’s vereist bovendien weinig of geen aanpassingen aan de kade of trailer. Ook kunnen ze goed inspelen op onvoorziene omstandigheden, zoals het inzakken van de trailervering bij het laden. Bovendien kunnen AGV’s ook voor andere taken worden ingezet, wat de return on investment ten goede komt.
AGV-systemen kunnen ook worden gecombineerd met een transportband. Er bestaan zelfs AGV-systemen met een geïntegreerde transportband. In tegenstelling tot andere toestellen in deze categorie is het daarmee wel mogelijk bepaalde niet gepalletiseerde goederen, zoals kartonnen dozen, te laden en te lossen (zie figuur 1).
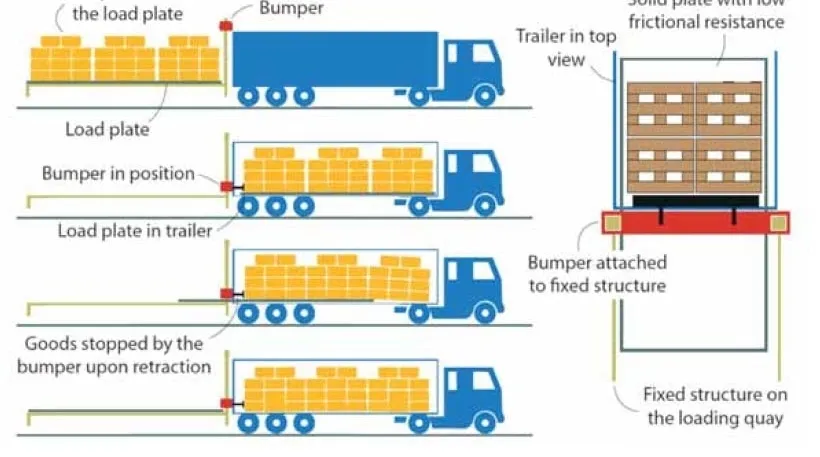
One-shot-gebaseerde systemen
Deze systemen laten toe een volledige lading in één keer in en uit de trailer te laden/lossen. Ze zijn met name geschikt voor volumineuze goederenstromen met een gestandaardiseerde morfologie.
Conceptueel bestaan OSB-oplossingen uit een semi-vaste constructie, die op de laadkade is bevestigd en gekoppeld is aan een verschuifbaar laad- en losplatform dat instaat voor de laad- en/of losbeweging. Je kunt de werking vergelijken met een lange spatel die volledig in de trailer schuift en – afhankelijk van de situatie – het te laden of te lossen goed meeneemt of achterlaat bij het terugtrekken.
De meeste OSB-systeemintegratoren bieden basisconcepten aan, die afhankelijk van de wensen kunnen worden gepersonaliseerd tot een volautomatisch geïntegreerd systeem.
Voor het eigenlijke laden van de trailer moeten bij zowat elk OSB-systeem de goederen worden geordend en gecompacteerd op het laadplatform, zodat de trailercapaciteit optimaal kan worden benut. Meestal gebeurt die ruimtelijke organisatie door het laadplatform zelf.
Belangrijk is wel om tijdens het behandelen van de goederen het hoogteverschil tussen het systeem en de trailer te stabiliseren. Dat is mogelijk door de trailer tijdens het aandokken uit de vering te laten rijden of via een dock leveler. Voor het laden en lossen kunnen verschillende werkingsprincipes worden gehanteerd. Zo kan er worden gewerkt met transportbandsystemen, een multi floor-systeem, een skatesysteem of een skate+-systeem.
“Bij een transportbandensysteem wordt zowel op de laadvloer van de trailer als op de laad-/loskade een transportbandconstructie gemonteerd. Samen zorgen zij voor de overdracht van de goederen”, legt David Ceulemans, post-doc researcher aan de UA, Faculteit Toegepaste Ingenieurswetenschappen uit. “Het multi-floorsysteem werd initieel ontwikkeld voor de behandeling van bulkgoederen, maar is ook geschikt om goederen met andere morfologische vormen te laden/lossen. Hier bestaat de laadvloer van de trailer uit kunststof of aluminium latten om de goederen in de trailer te transporteren.”
“Wanneer je het maximaal transporteerbare gewicht wil behouden of geen actieve mechanische componenten in de trailer wil integreren, dan is het skatesysteem interessanter”, vervolgt hij. Figuur 2 geeft de werking van zo’n systeem schematisch weer. “Het achterliggende principe is geïnspireerd op de werking van een handpallettruck. Daarbij bestaat de volledige lengte van het laadplatform uit kettingbanen en zogenaamde ‘skates’ om de lading in de trailer te schuiven. Naast een laadplatform met skatesysteem heb je hier een opbouwbodem met uitsparingen in de trailervloer. Dat je de laadvloer moet aanpassen, is het grootste nadeel van het skatesysteem. Met een skate+systeem wordt dat probleem omzeild, doordat de ladingdrager zo wordt gepositioneerd dat het systeem vrij kan bewegen binnen de uitsparingen/marges van de ladingdrager (zie figuur 3).”
Semiautomatische systemen
Bij de laatste groep is er nog steeds menselijke interactie nodig. Vooral voor goederen met een lastige morfologie – zoals stukgoed – is die optie interessant. Dit systeem bestaat uit een stevig voetstuk, dat al dan niet vast wordt gemonteerd op de laadkade of verrolbaar is tussen verschillende laaddokken. Aan dat voetstuk is een telescopische arm bevestigd met aan het uiteinde een laadplatform, waar een operator op een ergonomisch verantwoorde manier kan laden en lossen. Een al dan niet in de telescopische arm ingebouwde transportband zorgt voor de aan- en afvoer van goederen tussen de operator en de laadkade, wat tijd uitspaart.
Deze oplossing is eerder een hulpmiddel om het handmatig laden en lossen te vereenvoudigen en ergonomisch te ondersteunen. Toch kan een telescopische transportband waardevol zijn wanneer automatisch laden en lossen niet mogelijk of rendabel is. Het systeem is vooral interessant als er op regelmatige basis containers of trailers met los stukgoed moeten worden gelost of geladen. Het gewicht van het stukgoed dat de operator moet verplaatsen is ongetwijfeld de meest beperkende factor.
Daarnaast bestaan er ‘pick & place’ systemen met manuele ondersteuning. Die houden het midden tussen een telescopische transportband en een AGV met geïntegreerde transportband. In zijn meest eenvoudige vorm bestaat die oplossing enerzijds uit een robotarm en grijper – bestuurd door een operator – en anderzijds een transportband die de goederen afvoert. Dat systeem focust met name op het lossen van los verpakte en gestapelde goederen, waarbij het gewicht te hoog is om handmatig te behandelen.
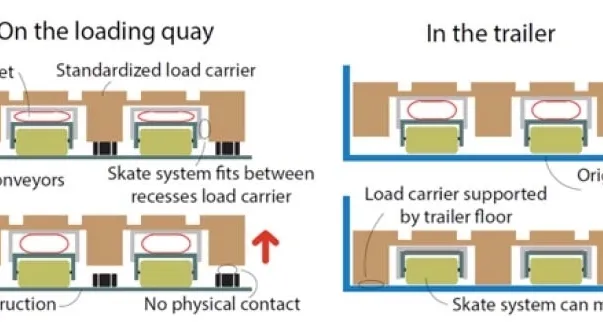
Het juiste systeem op de juiste plaats
Elke technologie heeft voor- en nadelen. Wat het meest geschikte systeem is, is in grote mate afhankelijk van het type lading. Ook de bedrijfsspecifieke context bepaalt mee of een automatische laad- en losoplossing überhaupt haalbaar is.
Julie Stuer, projectleider bij VIL: “Om de keuze te vergemakkelijken, raden we aan te vertrekken van de belangrijkste kenmerken waar de ideale oplossing aan zou moeten voldoen. Vervolgens kun je die aftoetsen met de commercieel beschikbare systemen (zie figuur 4).”
De grootste troef van de OSB-systemen is wel de snelle laad- en lostijd. Zij zijn in staat een trailer binnen de vijf à tien minuten te lossen. AGV’s daarentegen werken een pak langzamer.
Je moet er wel rekening mee houden dat de meeste laad- en losoplossingen een zekere ruimte op de laadkade in beslag nemen. Bij ATL AGV’s is dat niet het geval. Samengevat kunnen we dan ook stellen dat een ATL AGV-systeem vooral interessant is bij discontinue goederenstromen en waar de multi-inzetbaarheid een troef is en de fysieke ruimte op de laadkade een beperkende factor.
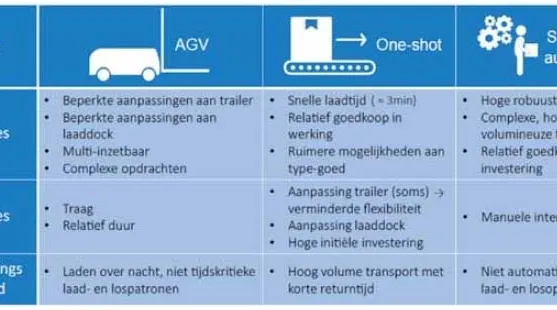
ROI-hulp voor laden en lossen
In het kader van het project ontwikkelde het departement Transport en Ruimtelijke Economie van de UA een ROI-tool om bedrijven te begeleiden. De tool houdt rekening met de potentiële kosten en mogelijke kostenbesparingen. De belangrijkste resultaten die je uit de tool kunt halen zijn de ROI na tien jaar, de geschatte break-evenperiode en het totale volume aan behandelde pallets tegen de kostendekkende prijs. De tool behoudt daarbij steeds het gebruik van vorkheftrucks als referentiescenario aan.
Belangrijk is dat de resultaten van de tool generiek zijn. De operationele kosten en de projectkosten zijn uiteraard ook afhankelijk van, bijvoorbeeld, de kenmerken van het magazijn. Die kosten zijn evenwel te gedetailleerd om in de tool mee te nemen. De tool biedt dus een indicatie van de meest aangewezen oplossing, maar voor een gedetailleerde inschatting blijft een diepgaande haalbaarheidsstudie vereist.
TC
Extra info bij het artikel
Proof of concept bij Barry Callebaut
Binnen het OptiCharge-project werd een business case uitgewerkt bij chocoladefabrikant Barry Callebaut, met daaraan gekoppeld een proof of concept. Dat gebeurde in samenwerking met MDR Consult. Het project vond plaats op de productiesite van Barry Callebaut in Wieze. Die site telt zeven productielijnen, die 360 dagen per jaar en de klok rond draaien. Jaarlijks produceert de fabrikant 80.000 ton afgewerkt product. Dat vertaalt zich in 4.000 vrachtwagens die jaarlijks worden geladen en vertrekken naar het centrale DC in Aalst enerzijds en naar drie 3PL-magazijnen in de omgeving anderzijds.
Typerend voor de logistieke infrastructuur op de productiesite is het plaatsgebrek in het buffermagazijn. Er zijn drie laad- en loskades voor de afvoer van afgewerkte producten en de aanvoer van verpakkingsmateriaal. Daarnaast is er een bufferruimte voor maximaal 30 pallets. Het plaatsgebrek, de vele bewegingen en het feit de chauffeurs er zelf hun wagens laden en lossen zorgen voor gevaarlijke situaties. In de ‘as is’- situatie beschikt Barry Callebaut over drie eigen vrachtwagens en vijf trailers.
Omdat die situatie niet meer houdbaar is, staat een intern project gepland waarbij het buffermagazijn in Wieze wordt uitgebreid. Daarnaast moet de bouw van een nieuw DC in Lokeren 60.000 vierkante meter extra opslagruimte bieden. In het verlengde van die uitbreiding wilde Barry Callebaut bijkomende opportuniteiten bekijken om zo efficiënt mogelijk te laden en te lossen.
Stap 1: operationele uitdagingen in kaart brengen
Bij dit project kwamen enkele belangrijke operationele uitdagingen naar boven. Zo wordt het afgewerkt product opgeslagen op verschillende dragers, met diverse afmetingen en gewichten. Er werd alvast beslist om bijvoorbeeld ‘big bags’ buiten de scope van het project te houden omwille van de instabiliteit op een pallet. Het moet in de toekomst dus ook mogelijk blijven trailers zowel automatisch als manueel te laden. Daarnaast wilde Barry Callebaut dat chauffeurs op elk moment de staging- en laadcyclus konden afbreken, zodat ze tegen het eind van hun shift met een deelvracht naar het DC kunnen vertrekken.
Ook werd ingeschat welke invloed bestaande en toekomstige projecten op het laad- en losproces hebben. Zo zal na de uitbreiding van het magazijn in Wieze het gewicht van de pallets wellicht hoger worden. Die informatie werd dan ook meegenomen bij de evaluatie van de technologieën.
Aangezien het laad- en losproces al vrij geoptimaliseerd was, konden er geen besparingen op materieel of personeel worden gerealiseerd. Het doel was vooral de impact van de langere afstanden tot het nieuwe DC in Lokeren zoveel mogelijk te beperken. Daarom wilde Barry Callebaut met de automatisering dan ook vooral het aantal ‘round trips’ per shift opschalen of op zijn minst dezelfde frequentie behouden.
Last but not least, eist Barry Callebaut voor projecten een minimale Internal Rate of Return (IRR) van twintig procent en een terugverdientijd van minder dan vijf jaar.
Stap 2: opties analyseren en business case opties evalueren
Op basis van de vereisten en de operationele uitdagingen werden drie mogelijke scenario’s uitgewerkt.
Scenario 1
In het basisscenario werd de manuele laad- en losprocedure aangehouden. Bij dit scenario komt duidelijk naar voren dat het aantal round trips per shift met een factor 1,3 zal afnemen, gezien de grotere afstand tot het toekomstige DC. Daardoor moet er bij de afvoer van hetzelfde totale volume één extra trekker-trailercombinatie worden ingezet.
Scenario 2
In het tweede scenario werd onderzocht wat het effect is wanneer er automatisch wordt geladen op de productiesite in Wieze en manueel gelost in het nieuwe DC in Lokeren. Hier tonen de berekeningen aan dat er een halve round trip per shift kan worden bespaard. Die besparing levert evenwel geen reductie van het aantal trekker-trailercombinaties op.
Scenario 3
In het laatste scenario werd de impact onderzocht wanneer er zowel op de productiesite in Wieze als in het nieuwe DC in Lokeren automatisch zou worden gewerkt. Hier komt een tijdswinst van 66 minuten per round trip naar voren. Daardoor kan er tegenover het huidige manuele laad- en losproces één round trip per shift worden gewonnen. Per shift komt dat neer op een besparing van één trekker-trailercombinatie. Aangezien enkel dit scenario voldoende ruimte bood voor de verdere uitbouw van een business case, werd besloten dit verder uit te werken.
Voor het proefproject werden drie technologieën onder de loep genomen, gebaseerd op het transportbandsysteem: een transportbandsysteem met kettingen, een transportbandsysteem met kettingen en rollenbanen en een transportbandsysteem met lamellen. Met een percentage van iets boven of onder de twintig procent lag de IRR van de verschillende systemen in lijn met elkaar. Met het oog op een optimale belading kwam het transportbandsysteem met kettingen en rollenbaan als beste naar voren.
Stap 3: de proof of concept opzetten
Omdat er op het moment van het proefproject geen bedrijf met transportbandsysteem met kettingen en rollenbaan aan de proof of concept (PoC) kon deelnemen, werd een beroep gedaan op een alternatieve technologie in de vorm van een skatesysteem. Daarbij moest de trailer worden aangepast om op het systeem aan te sluiten. Voor de realisatie van de PoC werd daarom een aangepaste trailer ter beschikking gesteld.
Met het one-shot-gebaseerde skatesysteem bleek het mogelijk 26 pallets in tien minuten tijd te lossen. Dat zorgde al voor een aanzienlijke tijdswinst tegenover de 45 minuten die het manueel lossen bij de fabrikant in beslag neemt. Met een transportsysteem met kettingen en rollenbanen zou de productiviteit nog hoger liggen, omdat dat systeem sneller is. Bovendien laat dat toe verschillende pallettypes naast elkaar te laden, wat bij het skatesysteem niet mogelijk is. Om toch de vergelijking te kunnen maken, werd de belading van een vrachtwagen op een bestaand transportsysteem met kettingen en rollenbaan getimed, waarbij de timing bij dit systeem uiteindelijk strandde op twee minuten en dertig seconden. We kunnen besluiten dat bij Barry Callebaut de doelstellingen van de PoC wel degelijk worden gehaald met een automatisch laad- en lossysteem.
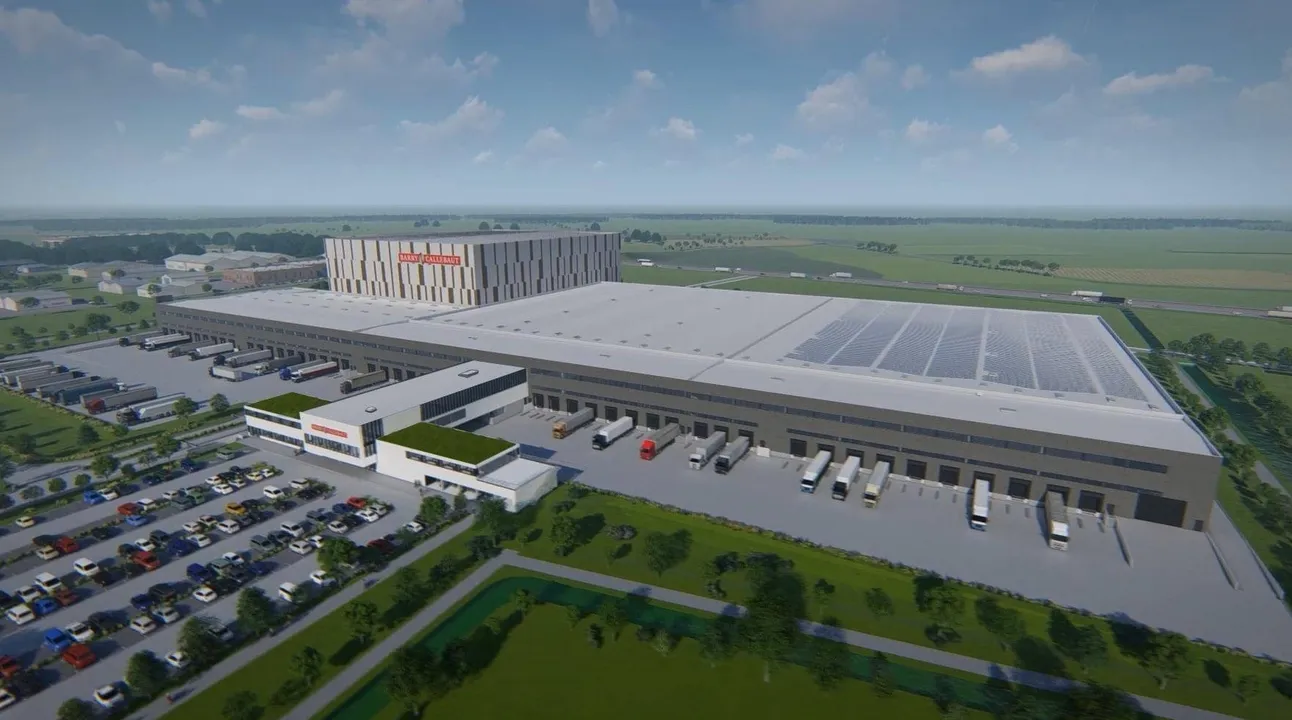