The Cornerstone of Stacking and Retrieving
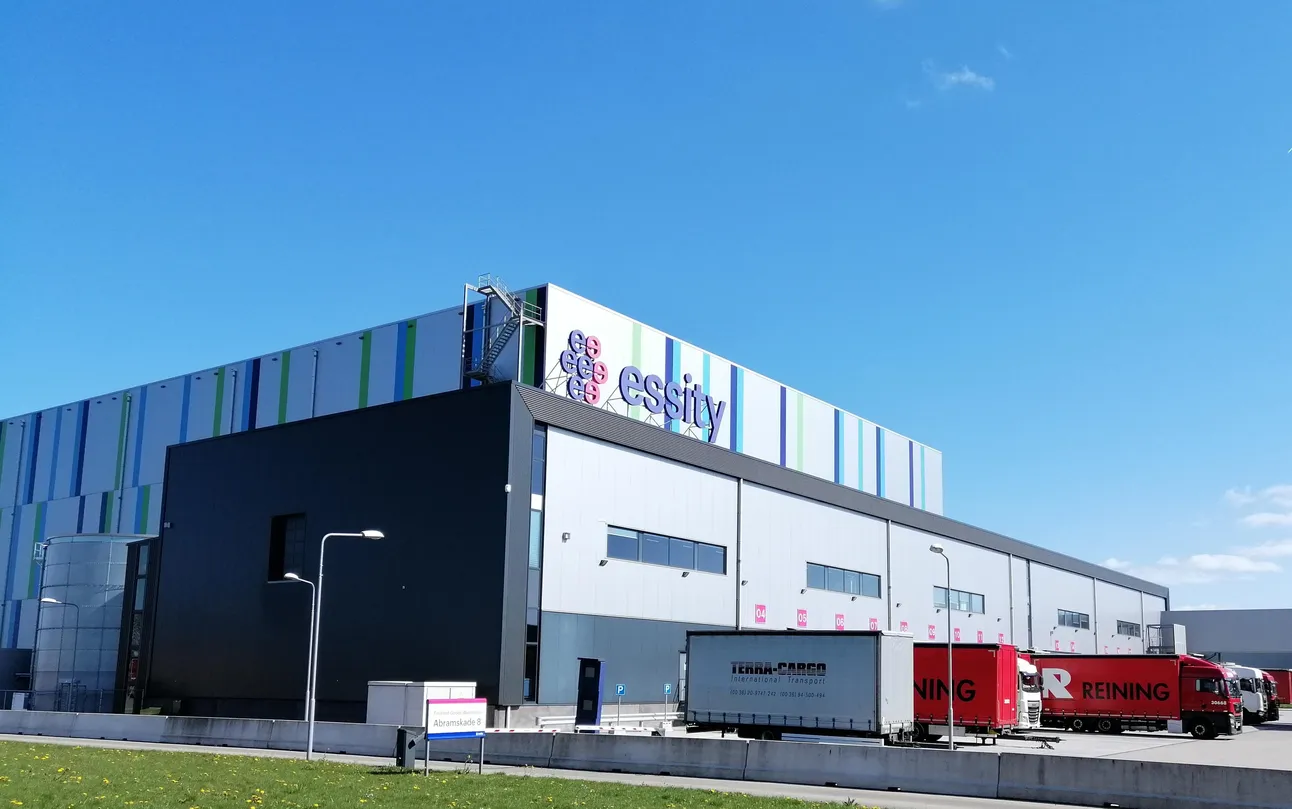
Leading hygiene and health company, Essity facility in Hoogezand has a strategic position within the group. It is the key site where Libero pant diapers and incontinence products in the TENA Pant and TENA Lady lines are manufactured. Approximately 550,000 pallets are produced in Hoogezand annually for distribution worldwide.
Having outsourced the warehousing of these products for the past 15 years, Essity decided to bring the activities back in-house for strategic reasons. “By handling the activities ourselves, we maintain control over our processes and products, and we can safeguard the quality of both warehousing and distribution for long term success,” explains Richard Fernhout, Logistics Manager. “Furthermore, it reinforces our strategic position within Essity.”
For the project, the company acquired a neighboringplot of land and then approached a number of all-round suppliers to design the most suitable ‘total solution’ for the specific logistics scenario at Essity Operations Hoogezand. “The concept had to provide us with sufficient storage and handling capacity for the next ten years,” adds Fernhout. “We purposefully opted for automation because of the cost benefits it offers and because we want to be able to run the warehouse operation with minimal employees.”
“We carefully analyzed and evaluated the remaining concepts.” explains Fernhout. “In addition to the design, the re-palletization method and the WMS played particularly important roles. Furthermore, we had a strong preference for a Dutch-speaking partner, not only in terms of the supplier’s sales representatives but also the service employees. After all, communication is so much easier and clearer – both during and after the project phase – if you speak the same language.”
The solution
Essity chose Swisslog, who in the role of main contractor took charge of the entire project, from design and construction of the new high-bay warehouse – measuring 30 meters high and 120 meters wide with around 27,000 pallet locations. Swisslog is also looking after the after-sales service for complete piece of mind and maximum uptime . “Swisslog scored significantly better than the rest on the assessment criteria,” continues Fernhout. “The proposed re-palletization concept, which included the use of a KUKA layer picking robot, gave us the most confidence in a truly feasible solution.” Re-palletization is a crucial part of the logistics process because Essity supplies its products on various types of pallets and at various pallet heights. “It’s difficult, if not impossible, to build that flexibility into our production process, which is why we decided to integrate it into the downstream logistics process,” says the logistics manager.
The WM6 warehouse management system, recently called SynQ, which is the latest version of Swisslog’s own technologically advanced warehouse management system, also helped to persuade Essity.
The Swisslog monorail is the beating heart of stacking and retrieval
“The clear error follow-up and extensive reporting possibilities particularly appealed to us and unquestionably help us to quickly and definitively solve any problems in the logistics process,” comments Fernhout. “Furthermore, we ‘clicked’ with Swisslog right from the start; they took a proactive problem-solving approach and made useful comments and suggestions. That creates trust.”
The state-of-the-art solution that Swisslog implemented at Essity comprises approximately 1,000 meters of conveyor belts, nine automatic high-reaching cranes, a KUKA layer picking robot and a monorail system. The production departments are connected to the new warehouse by a 500-meter-long bridge which runs across a public highway.
The system operates 24/7, transporting approximately 1,500 pallets of finished products via a conveyor belt – with no less than 243 buffer locations – to the new high-bay warehouse every day, where the goods are stored. The high-bay warehouse and the material handling system have been designed for a maximum infeed of approximately 200 pallets per hour and a maximum outfeed of approximately 300 pallets per hour.
The Swisslog monorail system, with 25 trolleys, plays a central role in stacking and retrieval since it facilitates the transport between the conveyor belts and the dispatch and receiving locations in the high-bay warehouse. Nine automated cranes take care of the stacking and retrieval in the new warehouse. Because the pallets themselves are relatively light – weighing a maximum of 500kg – the cranes are designed with double forks. Moreover, each crane can stack the pallets in a double-deep layout. “This considerably improves both the efficiency and the throughput speed. Even three metre high pallets pose no problems,” states Fernhout. “Around 20 percent of the outbound flow is re-palletized in order to optimally meet individual customer needs and requests,” explains the logistics manager. A vertical pallet transporter carries pallets to and from the first floor, where the KUKA robot performs re-palletization fully automatically at a rate of up to 50 pallets per hour. The new pallets are subsequently transported on conveyors to an automated pallet wrapper, labelled and then returned to the high-bay warehouse for storage. “All orders are prepared one day before dispatch,” continues Fernhout.
The outbound pallets are transported to the dispatch area by the monorail system in preparation for distribution. Each dock has its own dedicated conveyor which only carries the pallets that are associated with that order.
The loading itself is also largely automated and occurs without the intervention of Essity employees. Upon arrival, the truck driver signs in by entering his route number via a touchscreen. The driver is then allocated a dock number and receives a ticket (displaying a QR code) which gives access to the site. As an extra check, the driver re-identifies himself at the dock by producing the QR code. They cannot start loading the goods unless all information is verified. Once all the pallets have been loaded the driver signs out on a terminal, at which point all relevant documentation is automatically printed. The driver cannot leave the site again until all the steps have been performed correctly. “Thanks to the innovative automation and mechanization, we operate with just 12 permanent warehouse employees,” says Fernhout. “If a higher level of non-automated work creates extra demand, we hire in flexible workers.”
Although the far-reaching automation offers countless benefits for Essity, Fernhout acknowledges that it also posed some challenges. “Especially because the project had a very short lead time, plus it was implemented while the rest of the operation was still running,” he says. “there were a few teething troubles that caused a bit of a delay and a few initial problems, and of course people needed time to become familiar with the new technology and software. But everything was ironed out and Swisslog helped us with employee training and support in the first few weeks. Our employees are genuinely proud to be able to work in the new, high-tech environment.”