Modula tilt kantoorartikelen op hoger niveau
Lyreco optimaliseert magazijnruimte met verticale liftsystemen
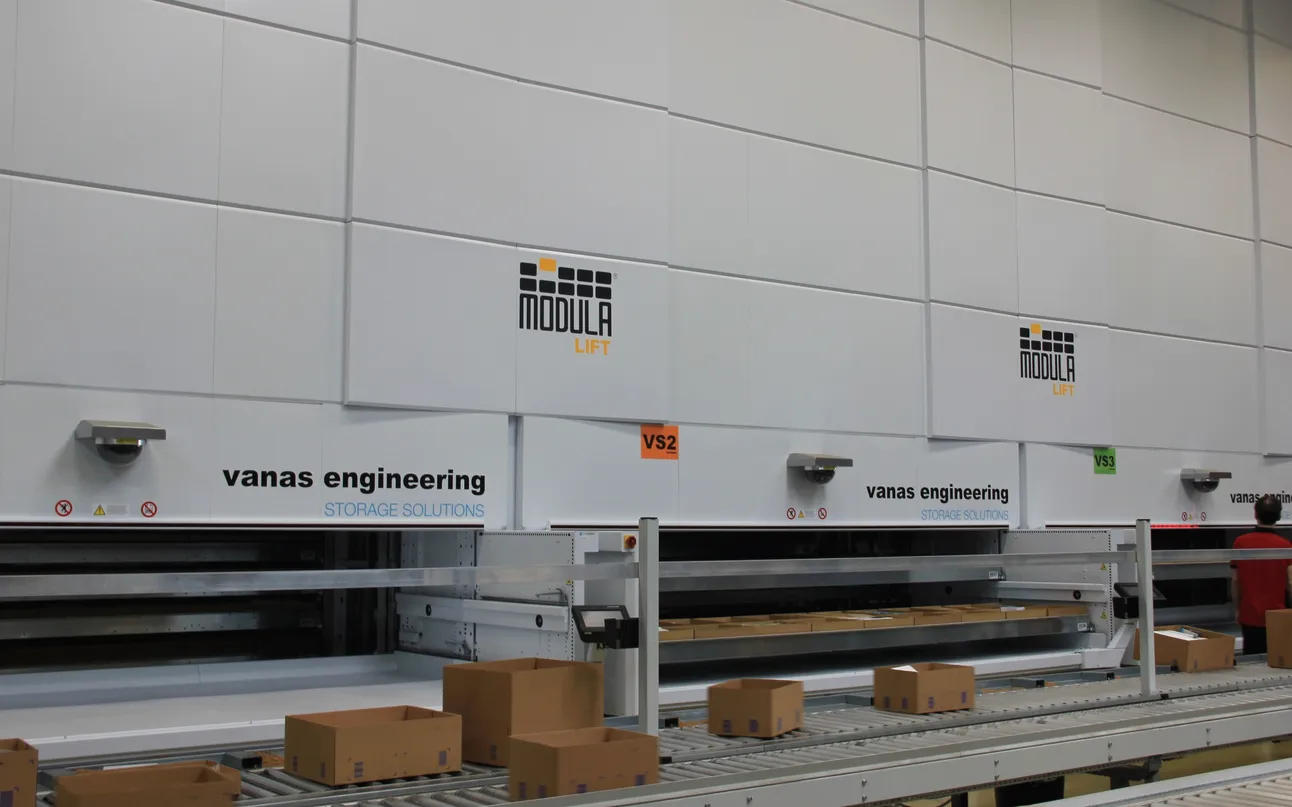
De groei van Lyreco Benelux vormt een grote uitdaging voor het magazijn in Vottem, vlakbij Luik. Om de productiviteit binnen de bestaande magazijnmuren op te drijven, schakelde de distributeur van kantoorartikelen en werkplekoplossingen de hulp van Vanas Engineering in. Die zorgde voor een vlotte integratie van drie verticale Modula-liftsystemen, die recent versterking kregen van nog eens drie exemplaren. Welke voordelen de oplossing op verschillende fronten met zich meebrengt, horen we van William Beauchamp, verantwoordelijke ‘Méthode - Maintenance - Tour - Inventaires’ bij Lyreco.
Lyreco werd in 1926 in Valenciennes opgericht door Georges-Gaston Gaspard. In de jaren ’70 kende de organisatie een sterke uitbreiding op Frans grondgebied. Intussen is de Lyreco Group actief in 25 landen op vier continenten. Vanuit het 32.000m² grote magazijn in Vottem krijgen professionele klanten uit België, Nederland en Luxemburg hun bestellingen aangeleverd. Op de site werken een 150-tal medewerkers.
Het assortiment van Lyreco bestaat uit een brede waaier kantoorbenodigdheden, technologische toestellen, meubilair en allerhande facility materiaal. In het magazijn vinden we maar liefst 17.000 tot 18.000 referenties terug. Bestellingen die voor 17.30 uur binnenkomen, worden tot 2.30 uur ’s nachts verzameld om vervolgens via sorteercentra richting de klant te vertrekken. Dagelijks verwerkt het magazijn in Vottem zo’n 23.000 à 24.000 orderlijnen.
Vorig jaar ging Lyreco Benelux op zoek naar de geschikte automatiseringsoplossing om zo de impact van de continue groei op het magazijn op te vangen. Enerzijds stijgt het aantal klanten en bestellingen gestaag, anderzijds wordt het productassortiment steeds breder. “Het aantal referenties blijft maar stijgen. Dat is een bewuste strategische keuze. Zo hadden we tot een paar jaar geleden nog maar een zeer beperkt aanbod qua voedingswaren, hygiëne en persoonlijke bescherming. Vandaag zijn die productcategorieën sterk uitgebreid”, illustreert William Beauchamp.
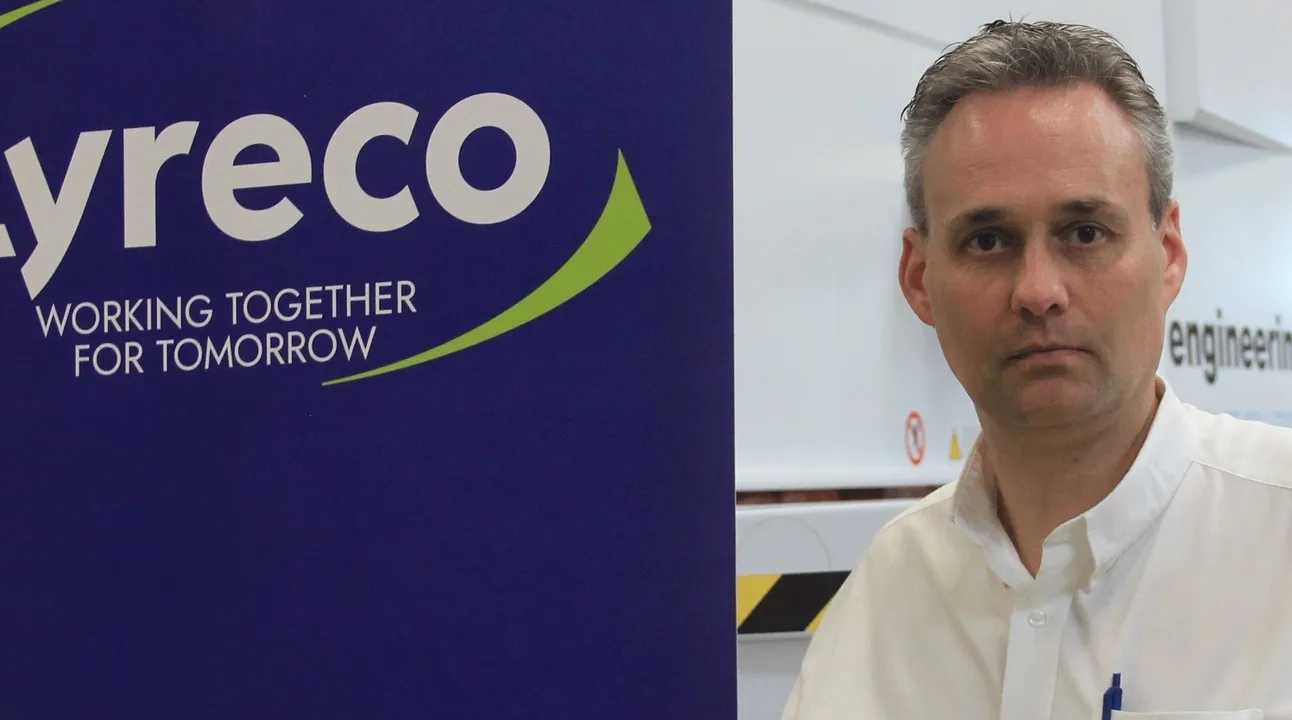
Automatisering met diverse doelstellingen
Na een vergelijkend onderzoek besloot Lyreco de verticale liftsystemen van Modula in huis te halen. Door hun modulaire opbouw laten die stockagetorens toe om de volledige hoogte van het gebouw te gebruiken. Dat liftsysteem werkt als een soort geautomatiseerde schuifladenkast met lades die qua hoogte kunnen variëren, maar steeds naadloos op elkaar aansluiten. Daardoor is erg compacte opslag mogelijk.
De Modula-liften garanderen Lyreco Benelux een hoge rotatie en doorloopsnelheden, met name voor medium movers. Dankzij de externe werkopening kan het systeem tijdens het picken al een twee lade klaarzetten. Daardoor kan zeer snel van lade worden gewisseld, wat de wachttijden een stuk korter maakt dan bij een systeem met interne afleg.
William Beauchamp: “We hebben gekozen voor machines van acht meter hoog en de maximale nuttige breedte van 4.100 centimeter, omdat zij ons het hoogste rendement per vierkante meter garanderen. Die extra brede lades verhogen ook de kans dat we meerdere orderlijnen vanuit één lade kunnen picken. Met behulp van de verticale liftsystemen kunnen we 20 à 25% sneller werken. Bovendien kunnen we met de oplossing twee à drie keer meer producten opslaan dan in onze traditionele rekken. Momenteel herbergen we 2.000 à 2.500 referenties in de drie machines samen, terwijl we er in de rekken op dezelfde oppervlakte slechts 700 à 750 kwijt kunnen. Uiteraard doen we voor heel wat producten ook nog altijd een beroep op traditionele rekken en doorrolstellingen. Daarbij denken we bijvoorbeeld aan de trage lopers en de producten die niet in de lift passen. De zeer snelle lopers, zoals de populaire blauwe ringmappen, picken we bij voorkeur rechtstreeks vanaf pallets.”
Daarnaast had Lyreco met deze specifieke automatisering nog een aantal andere verbeteringen voor ogen, waaronder een reductie van het aantal fouten tijdens het picken. “Tegenover onze traditionele pickingmethode – op basis van een pickbon – maken we met dit systeem drie à vier keer minder fouten”, klinkt het.
Ook een betere ergonomie voor de medewerkers was een belangrijk aandachtspunt.
W. Beauchamp: “Op dat vlak hebben we niets aan het toeval overgelaten. De dubbele externe afleg zorgt niet alleen voor minder wachttijden, maar maakt ook dat de medewerkers hun rug sparen doordat de lades voor de picking uit de kast schuiven. Op die manier hoeven medewerkers zich niet in de kast te buigen. Bovendien bevinden de plateaus zich op een optimale hoogte, waardoor orderpickers zich niet hoeven te bukken of omhoog hoeven te reiken om producten te kunnen nemen. Verder garandeert de externe afleg een uitermate veilige manier van werken. Er zijn ook extra veiligheidsbarrières voorzien. De snelheid en veiligheid die die externe afleg biedt, was voor ons een belangrijke reden om voor de Modula te kiezen en niet voor een andere leverancier. Binnen de groep hebben we trouwens ook al op andere sites goede resultaten geboekt met de Modula-liften, bijvoorbeeld in Duitsland en Italië.”
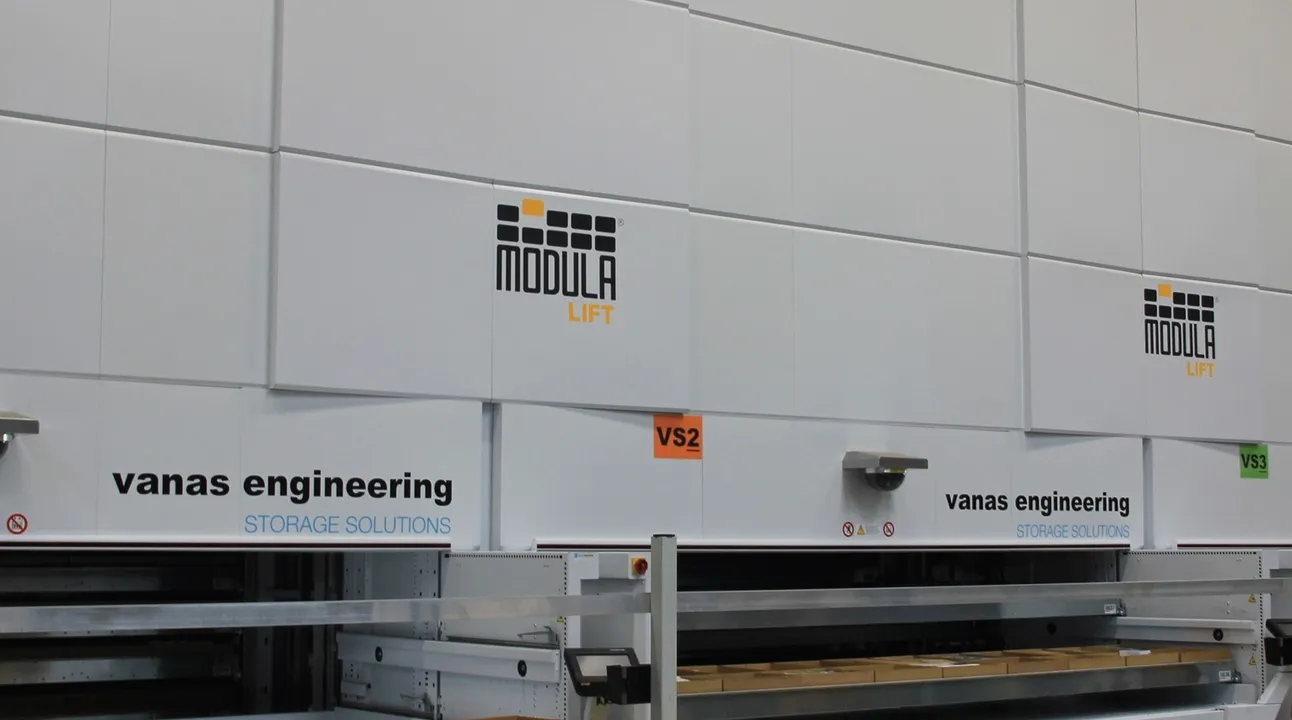
Vlotte integratie
De eerste drie Modula-liften werden vorig jaar geïmplementeerd. Een groot voordeel was dat Vanas Engineering – die het merk binnen de Benelux vertegenwoordigt – de verticale liften probleemloos binnen de bestaande structuur kon integreren.
“De belangrijkste uitdaging was wel de voorbereiding, die bestond in de configuratie van de plateaus en de selectie van de producten die we er het best in stoppen”, weet William Beauchamp. “De eigenlijke montage van de liften was zeer kort. Daarna moesten we uiteraard ook nog alle producten naar de kasten overbrengen. Dat alles is eigenlijk vrij vlot verlopen.”
Combinatie met drop-to-lightsysteem
Eén medewerker kan de drie aaneengeschakelde liftsystemen bedienen. Dat gebeurt in twee shiften. De bedoeling is dat de medewerker de gepickte items legt in de orderdoos, die zich aandient op het drop-to-lightsysteem vlak achter hem. Dat beperkt de loopafstanden tot het absolute minimum.
Op basis van een laser en een led-bar – waarop de naam van het artikel, het aantal te picken stuks én een pijltje naar de juiste locatie verschijnen – toont het Modula-systeem de medewerker exact wat hij moet verzamelen. De verzamelde stuks legt hij in de orderdoos die zich via het conveyorsysteem aan het drop-to-light systeem heeft aangediend. Via dat systeem is het mogelijk tot vijftien klantenorders tegelijk en foutloos te verwerken.
Aan de hand van de kleur die boven de orderbak oplicht, weet de orderpicker in welke van de liftsystemen – met elk hun eigen kleurcode – hij de producten voor die doos moet picken. Per uur kan één medewerker 200 orderlijnen uit de liften halen. Als hij alle items voor de bestelling uit de liften heeft genomen, meldt de orderpicker via de knop dat hij klaar is en duwt hij de doos terug op de centrale conveyor, zodat die zijn weg in het magazijn kan vervolgen. Wanneer alle goederen voor het order in kwestie verzameld zijn, kan de doos tot slot worden klaargemaakt voor verzending.
W. Beauchamp: “Het Modula-systeem is heel eenvoudig te gebruiken. Door alle aanduidingen in combinatie met het touchscreen aan de zijkant – dat een indicatie geeft over de positie van de doos – wijst het zich eigenlijk helemaal zelf uit. Het is voor nieuwkomers en tijdelijke krachten dan ook gemakkelijker om hier op kruissnelheid te raken dan in onze manuele zones, waar we rekken met verschillende configuraties hebben.”
De achterliggende Modula-software laat Lyreco toe om voor een optimale balancering van het systeem te zorgen. Zo wordt rekening gehouden met de maximumhoeveelheden die de picker en het conveyorsysteem kunnen verwerken. Die software is gekoppeld met SAP, het ERP-systeem van Lyreco, dat de orders beheert.
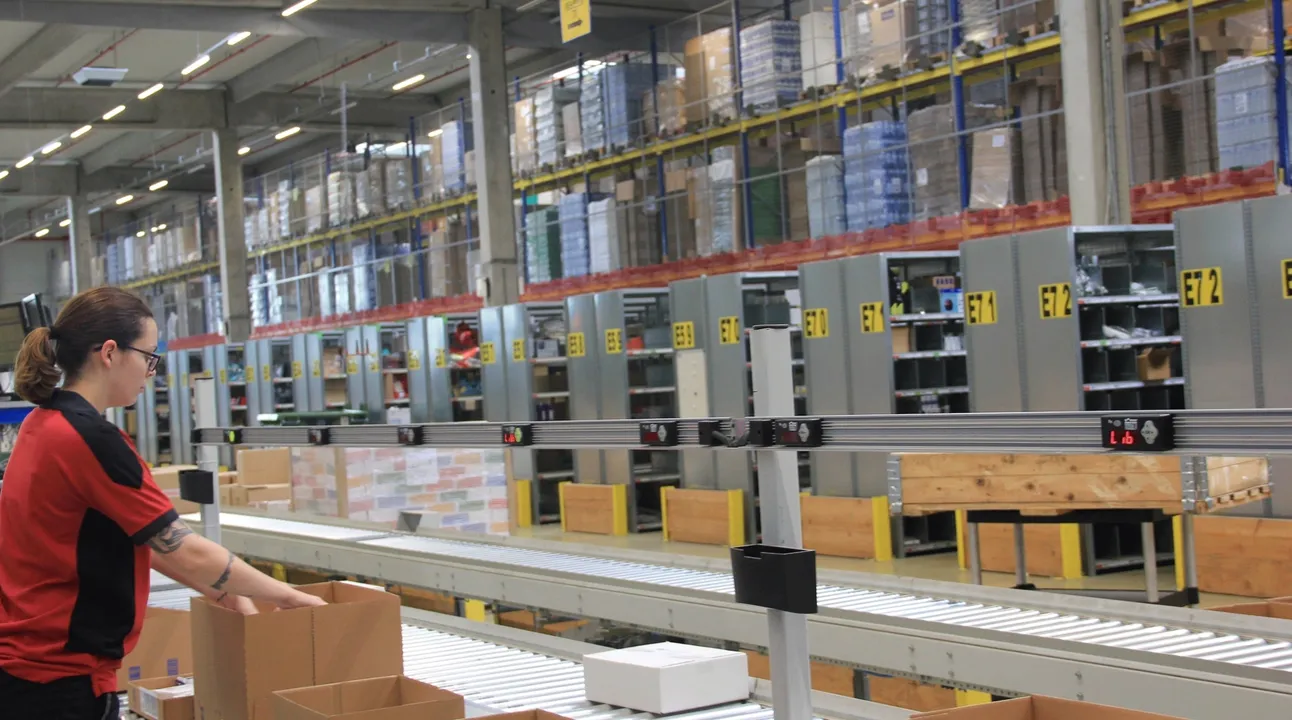
Minder herbevoorrading
Een pluspunt is ook dat het verticale liftsysteem minder frequent herbevoorraad hoeft te worden dan de klassieke stellingen. “We kunnen gerust stellen dat de herbevoorradingsfrequentie hier drie à vier keer lager ligt. Dat komt vooral omdat we in de Modula-liften met dynamische locaties werken. Zo kunnen producten gemakkelijker over verschillende locaties worden gespreid. Handig is ook dat de machine automatisch de voorraad beheert, wat manuele tellingen overbodig maakt. Wel vraagt de herbevoorrading discipline. Op het moment dat de medewerkers de machine vullen, moeten ze nauwgezet de instructies vanuit de software volgen qua plaatsing en hoeveelheden die op één locatie kunnen. Ook hebben we ervoor gekozen om niet tegelijk te herbevoorraden en te picken. Ook dat vraagt discipline. Nu herbevoorraden we de machines tijdens de pauzes van de orderpickers of van 8 tot 9.30 uur, voordat we de orderpicking starten.”
“Waar je bij het gebruik van dergelijke systemen ook op voorbereid moet zijn, is dat er al eens een storing kan optreden”, stelt William Beauchamp. “Gelukkig gebeurt dat niet vaak en kunnen problemen snel worden opgelost, ofwel door onszelf ofwel door Vanas Engineering, die ons binnen het servicecontract een interventie binnen de vier uur garandeert.”
De positieve ervaringen met het eerste systeem deden Lyreco beslissen om nog eens drie extra Modula-liften in te schakelen. “Die opstelling is in feite een exacte kopie van de eerste installatie”, aldus William Beauchamp. “Die uitbreiding zal ons in staat stellen nog meer referenties efficiënter op te slaan en te verzamelen. Momenteel zijn we bezig om de kasten met producten te vullen. Als ook dat systeem volledig operationeel is, zijn we voorbereid om de verdere groei op een compacte én performante manier op te vangen.”
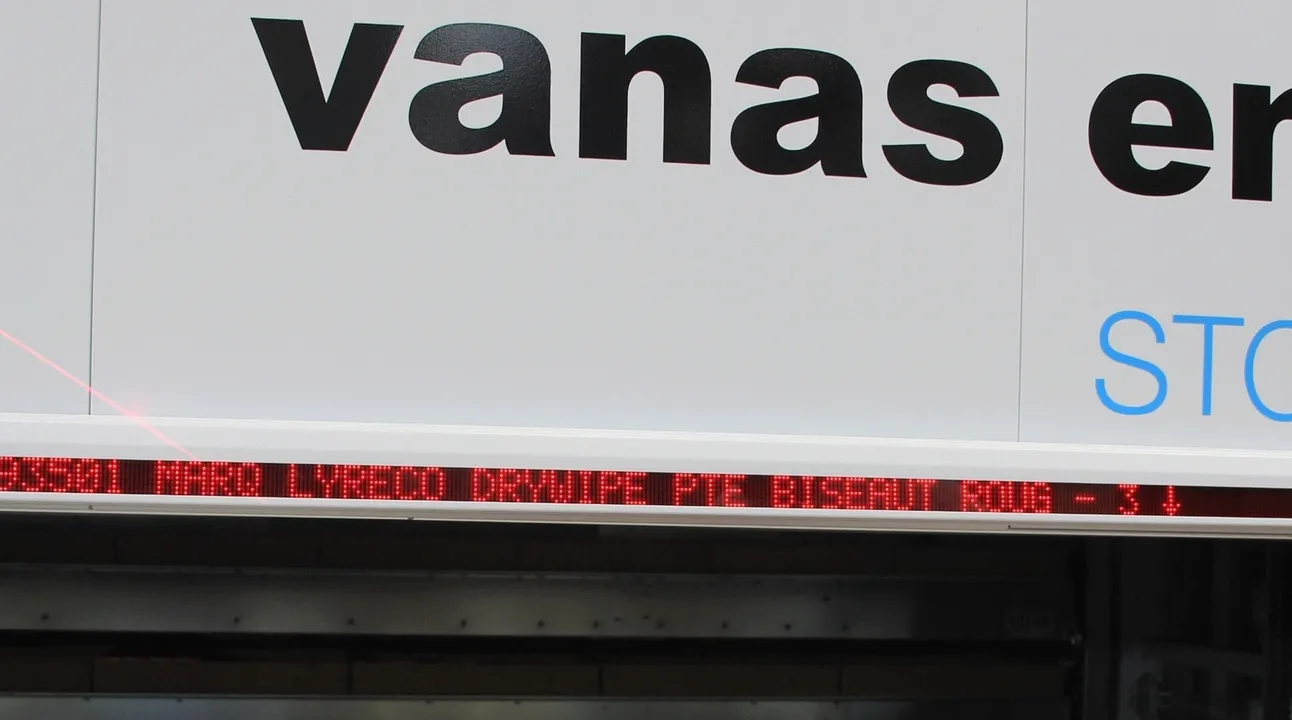