Minimale ruimte, maximale output
H.Essers belicht meerwaarde van compacte opslagsystemen
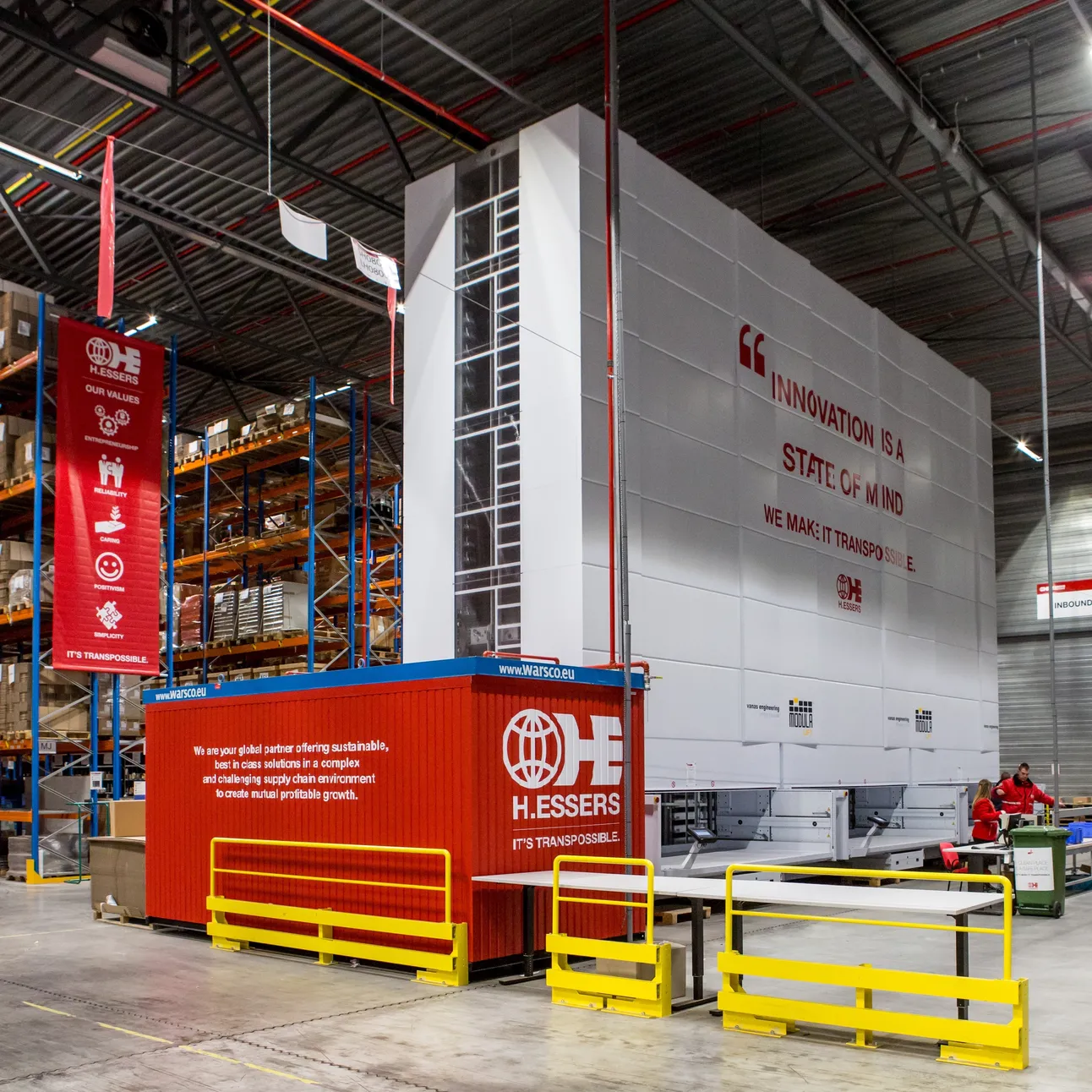
Zoveel mogelijk opslaan op zo weinig mogelijk ruimte. In tijden waar magazijnoppervlakte een kostbaar goed is, wordt dat steeds belangrijker. Maar uiteraard mag dat niet ten koste gaan van de output en de flexibiliteit. Die basisprincipes gelden zeker voor een logistieke dienstverlener als H.Essers, die van een performante logistiek zijn handelsmerk maakt. Operational manager Alexander Stas en Solution Design Engineer Parts Tim Boonen lichten de achterliggende visie toe, evenals twee systemen die op dat vlak intussen hun meerwaarde hebben bewezen in de organisatie, met name de Modula-liften en de Storeganizer.
Tot de kernactiviteiten van H.Essers behoren de behandeling van chemische en farmaceutische goederen, evenals hoogwaardige technische producten (zie ook kader). In de magazijnen passeren dus zowel heel kleine onderdelen als IBC’s (intermediate bulk containers) van 1.000 liter met chemische producten. Daarnaast biedt H.Essers waardetoevoegende diensten, zoals het herlabelen van farmaceutische producten.
Uitdagingen in warehousing
“Als organisatie zetten wij hard in op innovatie en digitalisering”, stelt Alexander Stas. “Tegelijk is het onze strategie om enkel nieuwe technologieën toe te passen als ze binnen onze omgeving echt zinvol zijn. Wij zullen die technologieën dan ook niet loslaten op processen die heel goed lopen. Pas als we merken dat bepaalde processen voor verbetering vatbaar zijn of als een klant ons voor een nieuwe uitdaging stelt, bekijken we of bepaalde technologieën of concepten een meerwaarde kunnen betekenen. We geven ook altijd de voorkeur aan de meest pragmatische oplossing van dat moment.”
“Vandaag hebben we een team van een dertigtal mensen in dienst dat samen met de klant onder de loep neemt wat de specifieke noden zijn en hoe we die kunnen waarmaken”, vult Tim Boonen aan. “Daarboven hebben we een business process improvement tak die continu processen tracht te verbeteren. Dat team bekijkt dan specifiek in welke oplossingen we moeten investeren om over pakweg drie jaar onze klanten nog beter te kunnen helpen.”
Wat warehousing betreft, schuift Alexander Stas drie grote uitdagingen naar voren. “Dat we in totaal over meer dan een miljoen vierkante meter magazijnoppervlakte beschikken, betekent niet dat we ze niet optimaal moeten benutten. Zeker in Vlaanderen is uitbreiden allesbehalve gemakkelijk, dus zo compact mogelijk stockeren is primordiaal. Zelfs als we besluiten om toch extra vierkante meters toe te voegen, zullen we proberen die zo snel mogelijk optimaal te benutten”, klinkt het. “Daarnaast is het uiteraard belangrijk om zeer accuraat te werken, zowel wat de ingaande als uitgaande stromen betreft. De systemen die we in huis halen mogen dus geen steken laten vallen. Last but not least, moeten we onszelf uitdagen om steeds efficiënter te werken. De marges in de markt zijn erg scherp en de leadtimes worden korter, zeker nu de e-commercetrends zich ook in de b2b-markt doorzetten. Steeds vaker vragen klanten bijvoorbeeld om op de dag van de cut-off nog te verschepen.”
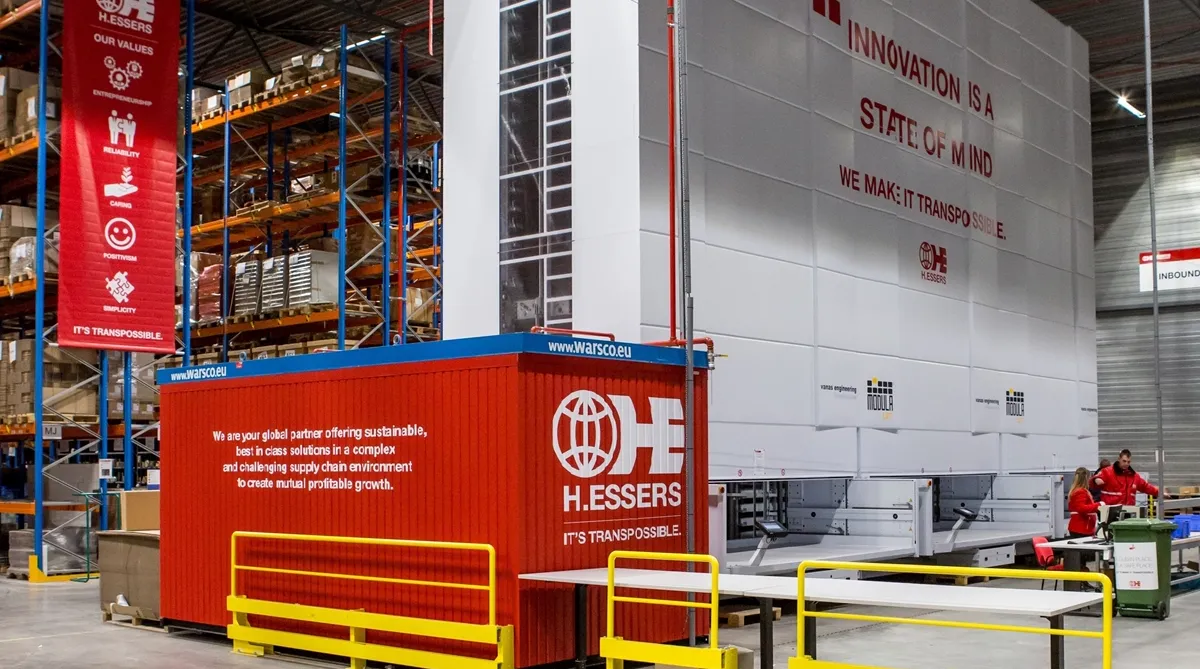
Compacte plug & play oplossing voor palletlocaties
Een van de partners die H.Essers helpt bij de continue zoektocht naar compacte oplossingen, is Vanas Engineering. Een eenvoudige, maar voor bepaalde magazijnomgevingen erg efficiënte oplossing is de Storeganizer, die de aanbieder van magazijnsystemen bij H.Essers implementeerde.
Alexander Stas: “Typisch aan veel van onze magazijnen is dat we heel veel rekken hebben. Een Storeganizer-systeem bestaat uit zogenaamde slabs, die we kunnen integreren binnen bestaande palletlocaties in het rek (zie foto). De Storeganizer laat toe kleinere producten op een zeer compacte manier in stellingen op te slaan, wat ons heel wat ruimte bespaart. Bovendien kun je gemakkelijk spelen met producten met een verschillende rotatie, door A-movers in de voorste slabs te stoppen en C-movers in de achterste. Handig is ook dat een Storeganizer op maat gemaakt kan worden: de hoogte en de breedte, de grootte van de vakken, enzovoort. Verder is de Storeganizer een aanwinst op ergonomisch vlak, aangezien medewerkers niet ver hoeven te reiken om bij de producten te kunnen. Ook het verschuiven van de kolommen om bij de juiste slab te kunnen, vraagt weinig moeite. Bovendien hoeven de orderpickers minder afstand af te leggen om verschillende producten te verzamelen.”
Momenteel gebruikt H.Essers al ruim 200 Storeganizer-systemen op verschillende magazijnlocaties binnen de diverse sectoren die de organisatie bedient. “Zeker in een farmaceutische omgeving betekent het een meerwaarde dat je met de Storeganizer producten stofvrij in een stelling kan opslaan”, vertelt Alexander Stas.
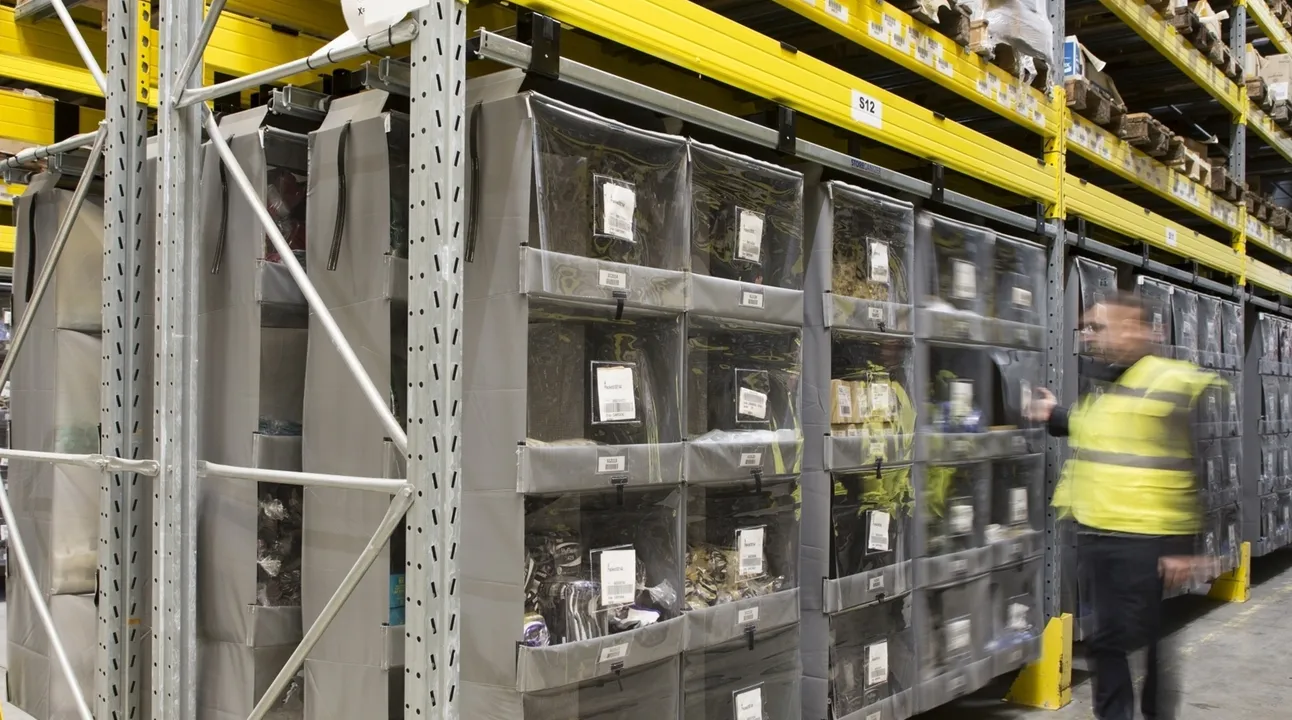
Modula-liften voor compacte opslag van onderdelen
Daarnaast doet H.Essers een beroep op de verticale Modula-liftsystemen die Vanas Engineering levert.
A. Stas: “Die oplossing hebben we in huis gehaald toen een leverancier van industriële printapparatuur ons vroeg om een wereldwijd onderdelenmagazijn op te zetten. Een eis was dat vanuit de site in Genk dringende stukken vliegensvlug konden worden gepickt om binnen de 24 of 48 uur wereldwijd bij de klanten te worden geleverd. Je wil immers koste wat het kost vermijden dat een drukkerij stilvalt of lange tijd platligt. Voor een spare parts bedrijf gaat het er niet zozeer om heel hoge volumes te verwerken, maar eerder om zeer snel te kunnen handelen als het erop aankomt.”
Een extra uitdaging was dat het hier om een brede waaier aan onderdelen gaat, van piepkleine plastic rondellen tot meterslange stukken voor industriële printers. H.Essers heeft toen drie mogelijke concepten voor het opslaan en picken van de kleinere stukken bestudeerd. Om te beginnen waren dat klassieke rekkenlocaties op een mezzanine, waarbij de picker met een kar zijn pickronde doet. Een andere optie was om heel hoge rekken op een mezzanine te bouwen, waarbij de producten via een man-up-orderpicker worden verzameld. De verticale liftsystemen vormden de derde mogelijkheid.
A. Stas: “We hebben de verschillende voordelen en nadelen naast elkaar gelegd. Enerzijds wilden we op zo weinig mogelijk vierkante meters werken, anderzijds moest het systeem ons de nodige efficiëntie kunnen garanderen. De verticale liftsystemen hebben de strijd vlot gewonnen. Terwijl we bij een klassiek concept ongeveer 500 vierkante meter oppervlakte nodig hadden om die artikelen op te slaan, hebben de verticale liften aan 50 vierkante meter voldoende. De business case toonde bovendien aan dat we het systeem in zes à twaalf maanden konden terugverdienen, waardoor we ook het management gemakkelijk hebben kunnen overtuigen. Uiteindelijk hebben we het project in zes maanden tijd weten terug te verdienen.”
Op de site kwamen uiteindelijk drie Modula-liften met 15.000 locaties van verschillende grootte, verdeeld over ongeveer 210 platformen. Telkens wanneer de orderpicker een bepaald product nodig heeft, wordt het juiste platform aangeboden.
A. Stas: “De operator wordt volledig door het systeem begeleid, zodat we in die zone geen klassieke RF-scanners meer hoeven te gebruiken. Op basis van de aanwijzingen van het pick-to-light-systeem neemt de operator de juiste artikelen. Een laser wijst hem ook meteen de juiste locatie in de lift aan, wat de kans op fouten nog verkleint. Als de operator een product heeft gepickt, bevestigt hij dat via het systeem. Vervolgens draait hij zich om en legt het artikel in de juiste bak volgens de aanwijzingen van het drop-to-light-systeem. Via dat systeem kunnen zes orderbakken tezelfdertijd worden gevuld. Als een order klaar is, gaat een lichtje branden, waarop de bak klaargemaakt kan worden voor verzending en er plaats vrijkomt voor een nieuwe bak.”
De Modula-liften stellen de orderpicker in staat snel en foutloos te werken. Uit metingen is gebleken dat H.Essers via de lift vier keer sneller kan picken dan in een klassieke omgeving. Dat is mede te danken aan het feit dat het volgende platform zich alvast klaarzet terwijl de operator nog aan het picken is. Het systeem impliceert ook dat operatoren niet meer met een karretje rond hoeven te rijden om orders te verzamelen. De medewerkers hebben het systeem dan ook met open armen ontvangen.
Een ander voordeel is dat H.Essers A-, B- én C-movers in de liften kwijt kan. “We vonden het niet alleen belangrijk dat we de goederen efficiënt uit het systeem kunnen halen, maar ook dat we ze er zo efficiënt en plaatsbesparend mogelijk in kunnen stoppen”, gaat het verder. “Met de hulp van Vanas Engineering en onze eigen IT-afdeling hebben we een algoritme ontwikkeld waardoor de operator op een dynamische manier kan kiezen waar een artikel het best komt te liggen. De operator die de inslag doet, ziet op zijn dashboard hoeveel locaties van het juiste formaat er voor dat product beschikbaar zijn. Het algoritme doet een voorstel en op basis van zijn ervaring kan de medewerker bepalen of hij dat volgt of een nog betere oplossing ziet. Zo is de lift steeds optimaal gevuld.”
Bij de implementatie van de Modula-liften kwam de meerwaarde van Vanas Engineering als partner extra naar voren.
A. Stas: “We kijken allebei met een engineeringbril naar standaardoplossingen en hebben erg open gesprekken rond de mogelijkheden gevoerd. Onze mensen spreken duidelijk dezelfde taal en dat helpt om zo snel mogelijk te kunnen opleveren. Dat bleek ook tijdens de implementatie van de liften. In mei hebben we de bestelbon getekend, in augustus konden we de eerste lift in gebruik nemen. In amper veertien weken tijd waren we dus klaar voor productie.”
Ook wat de verzending betreft, werd alles in het werk gesteld, om de onderdelen zo efficiënt mogelijk de deur uit te krijgen. In dat kader heeft H.Essers een realtime platform gebouwd voor zes verschillende carriers. Direct na de picking wordt de zending op dat platform aangemeld. Daarbij wordt doorgegeven hoe groot en hoe zwaar het pakket is en waar het precies naartoe moet. Achter de schermen worden de douaneformaliteiten automatisch geregeld. “Via dit gestroomlijnde samenspel van oplossingen kunnen we orders die voor een klant binnenkomen, binnen het uur picken en binnen de twee uur met de pakketdienst meegeven. Zo krijgen we ze ook binnen de vooropgestelde tijd op de juiste locatie, waar ook ter wereld”, besluit Alexander Stas.
TC
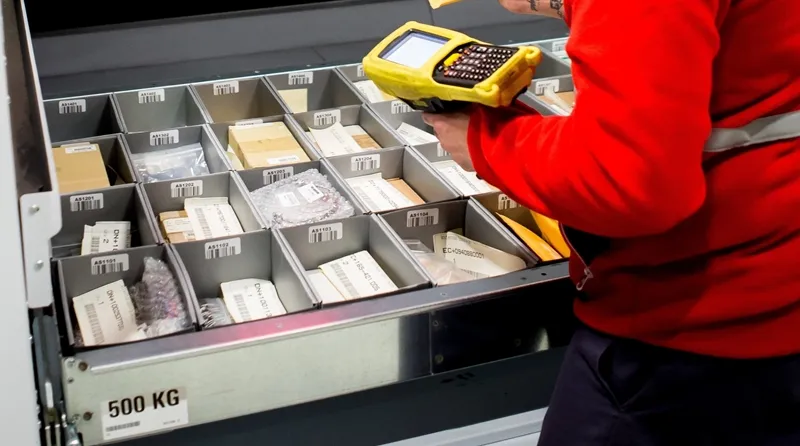
De magazijnactiviteiten bij H. Essers
Traditioneel staat H.Essers – met hoofdzetel in Genk – vooral bekend om zijn transportactiviteiten, waarvan de oorsprong teruggaat naar 1928. Toen startte Henri Essers met veetransport. Pas in 1980 zijn daar magazijnactiviteiten aan toegevoegd. Met de overname van Hessenatie Logistics in 2011 is het aantal vierkante meter magazijnruimte sterk gestegen. Een belangrijke recente aanwinst is de trimodale megasite, H.Essers Dry Port Genk, op de voormalige Ford-terreinen. Daarnaast is de organisatie in Gent gestart met een site die specifiek op de chemiesector is toegespitst. Het logistieke bedrijf streeft ernaar om koploper te zijn binnen zijn strategische segmenten, zijnde Pharma, Chemie, Infra en Parts.
Vandaag versterkt 1 miljoen vierkante meter magazijnen de uitgebreide vloot van H.Essers. Voor de organisatie werken ruim 6.300 medewerkers, waarvan 4.200 in België en 800 in Roemenië. De overige mankracht zit verspreid over de andere zeventien landen waar de organisatie actief is. H.Essers staat erop zoveel mogelijk zelf grip op de zaken te hebben. Zo werden het warehouse management systeem en het transport management systeem in huis ontwikkeld.