Matrijscombinatie afgestemd op productieorder
Resilux optimaliseert planning met APS
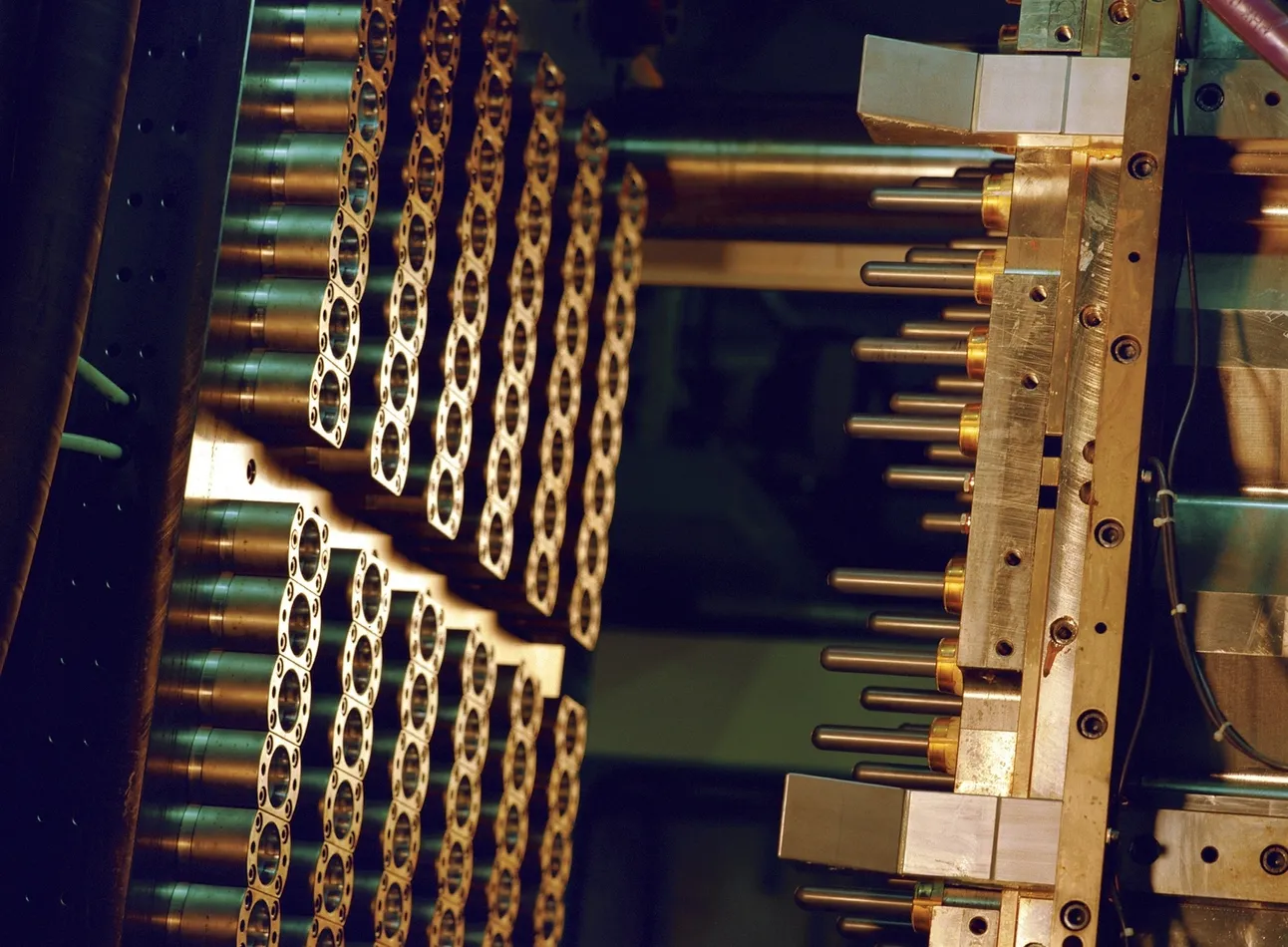
Resilux is een wereldspeler op de verpakkingsmarkt van PET preforms en flessen voor food en non-food. In het productieproces van het bedrijf is de exacte combinatie van verschillende matrijscomponenten cruciaal. Om die verschillende onderdelen optimaal aan de verschillende productiesites en orders toe te wijzen, heeft Resilux zijn planningstraject geoptimaliseerd met behulp van een APS-tool (advanced planning & scheduling) van Actemium.
Resilux is een internationale onderneming met wereldwijd ongeveer duizend medewerkers. Het bedrijf, met hoofdzetel in het Oost-Vlaamse Wetteren, ging in 1994 van start. Resilux produceert PET (polyethyleentereftalaat) ‘preforms’ en flessen. De preforms blaast Resilux – of de klant zelf – in flessen, om die vervolgens af te vullen met water, frisdranken, detergenten, cosmetica en andere producten. Sinds enkele jaren focust Resilux zich ook op de recyclage van PET-verpakkingen en de verwerking ervan tot hoogwaardig PET-recyclaat. De onderneming telt voor de productie van preforms negen productiesites in Europa, goed voor een volume van 7.700 miljoen preforms in 2021.
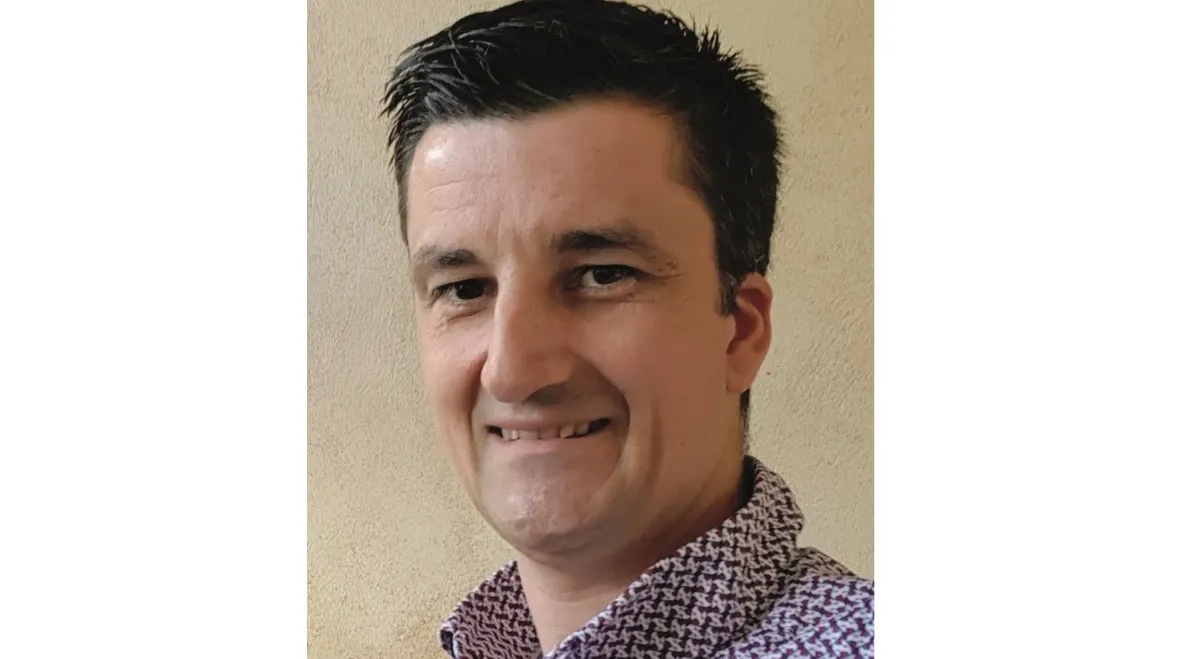
Componenten op elkaar afstemmen
Oliver Minsart legt als director Operational Excellence uit waarom het bedrijf nood had aan een systeem voor advanced planning & scheduling. “Vroeger planden we met Excel”, begint hij. “Dat systeem werkte, maar maakte het moeilijk om de groeiende complexiteit het hoofd te bieden. Om een idee te geven: we beschikken over meer dan honderd injectie- en blaaslijnen, verspreid over negen sites. Die lijnen gebruiken meer dan driehonderd verschillende matrijzen, met een brede waaier van kernen en schuiven. Gezien het hoge prijskaartje van de matrijzen, kopen we de onderdelen niet telkens voor elke site aan, maar verhuizen we ze tussen de verschillende locaties, in functie van de vraag van de klant en de productienood. Een optimale orkestratie over de verschillende productielijnen is dus cruciaal. Op die manier verzekeren we de gewenste leversnelheden voor onze klanten. Om dat te realiseren, moeten we zorgen voor een gestroomlijnde interactie tussen de machineplanning en de matrijsplanning. Vroeger misten we een overkoepelende visualisatie, wat het ons moeilijk maakte om de productieplanning optimaal te organiseren. Het ontbrak eveneens aan opvolging van de onderdelenstatus. Er ontstond een nood aan één versie van de waarheid, waarmee we meteen ook de communicatie tussen de verschillende sites konden reduceren.”
Om de APS-leverancier te selecteren, schreef Resilux een ‘request for proposal’ (RFP) uit. “Die bevatte verschillende belangrijke krijtlijnen”, legt Olivier Minsart uit. “De tool moest het mogelijk maken de injectie- en blaaslijnen in alle productiesites in te plannen en de matrijzen aan de aangewezen locaties toe te wijzen. We beoogden een integratie van de tool met ons standaard Microsoft Dynamics NAV ERP-pakket en het eigen MES. De implementatie zou niet via een ‘big bang’ verlopen, maar via een wendbare en vloeiende uitrol.” Op basis van de resultaten van de RFP vergeleek Resilux verschillende leveranciers. “We evalueerden aan de hand van demonstraties en inzichten op het vlak van de oplossing, de benadering van de leverancier en de prijszetting”, gaat Olivier Minsart verder.
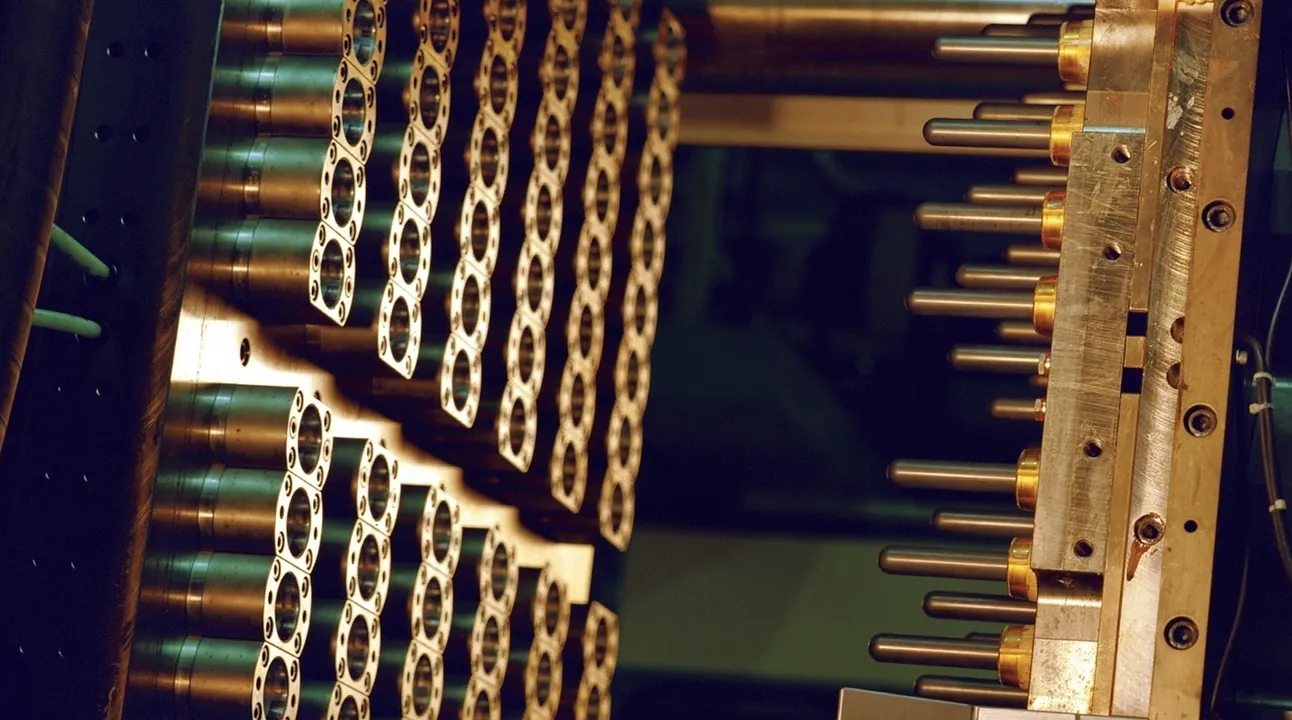
Centrale en lokale APS
Dat denkwerk mondde uit in twee resterende kandidaten. “Die onderworpen we aan een ‘proof of concept’ en het aftoetsen van referenties”, luidt het. “Uiteindelijk kwam het APS van Actemium als beste keuze uit de bus. De voorgestelde oplossing en de architectuur die op een omgeving met verschillende sites is afgestemd, gaven mee de doorslag. Dat gold eveneens voor de kennis en de professionele aanpak van de consultants, net als de gebruikersvriendelijke grafische interface die complexe taken mogelijk maakt.”
Elke productiesite beschikt over één APS, die via de ‘open source’ berichtenserver RabbitMQ continu geconnecteerd is met de centrale APS. De lokale APS-software is telkens verbonden met het ERP-systeem en het MES voor master data, bestellingen en het monitoren van de processtatus. Op elke site zorgt een lokale planner voor het stroomlijnen van de productielijnen en matrijscombinaties wanneer de matrijzen op de locatie aanwezig zijn. De planner creëert daarbij automatisch een digitale rapportering met productiesequenties, de verwachte matrijsveranderingen en de benodigdheden en veranderingen op het vlak van materialen. Op centraal niveau ontvangt een planner de aanvragen voor matrijzen wanneer die niet op een site aanwezig zijn. Hij plant in het MES eveneens het transport van de matrijzen tussen de verschillende vestigingen.
Het berekenen van de optimale circulatie van de matrijzen vindt in het APS plaats. De uitkomst van die oefening hangt af van de aangewezen matrijscombinatie. De tool neemt de opstarttijden mee in de berekening. De bestelhoeveelheden zijn binnen het APS aanpasbaar, met een synchronisatie met het ERP.
Een demonstratie van de APS-tool bij Resilux leert ons hoe de decentrale planner via een rood gemarkeerde tekstlijn verneemt dat de gewenste matrijscombinatie niet op zijn site aanwezig is. Hij kan ervoor kiezen de uitvoering van het order uit te stellen of – indien mogelijk – binnen de APS-tool over te schakelen op een andere matrijscombinatie. Een waarschuwing brengt de centrale planner ervan op de hoogte dat een site niet over de aangewezen matrijscombinatie beschikt. In dat geval organiseert hij de logistiek om de onderdelen op de vereiste locatie te krijgen. De software maakt het ook mogelijk hoeveelheden aan te passen en de ‘bill of materials’ (BOM) te veranderen, en die wijzigingen ook aan het ERP en het MES door te geven.
Verdere plannen
Olivier Minsart geeft aan dat een geleidelijke opstart van een pilootproject de juiste keuze bleek. Het vormde de opstap richting snelle en succesvolle lanceringen vanop afstand in andere productiefaciliteiten. “APS reduceert het werk en de communicatie binnen onze afdelingen en laat ons toe in te spelen op extra complexiteit en bijkomende parameters”, evalueert hij. “Het project nam wel meer tijd in beslag dan vooropgesteld. Daar droeg de covidpandemie in grote mate toe bij. De uitrol ging ook gepaard met complexere aanpassingen in de ERP- en MES-software.”
“We willen APS ook gebruiken voor de opvolging van onze silo’s en grondstoffen”, vervolledigt Olivier Minsart. “Daartoe moeten we onder meer zorgen voor het scannen van onze big bags die we in silo’s blazen. Ik zie ook mogelijkheden op het vlak van energieplanning en -optimalisering en denk daarbij aan het voorspellen van de productie van onze zonnepanelen en ons energieverbruik. Door de stroomprijzen voor de volgende dag en het piekverbruik aan onze planning te linken, kunnen we onze productie beter afstemmen op de schommelingen van de energieprijzen.”