Magazijn met oog voor lange termijn
Dassy Europe zet stap naar shuttlesysteem binnen groeistrategie
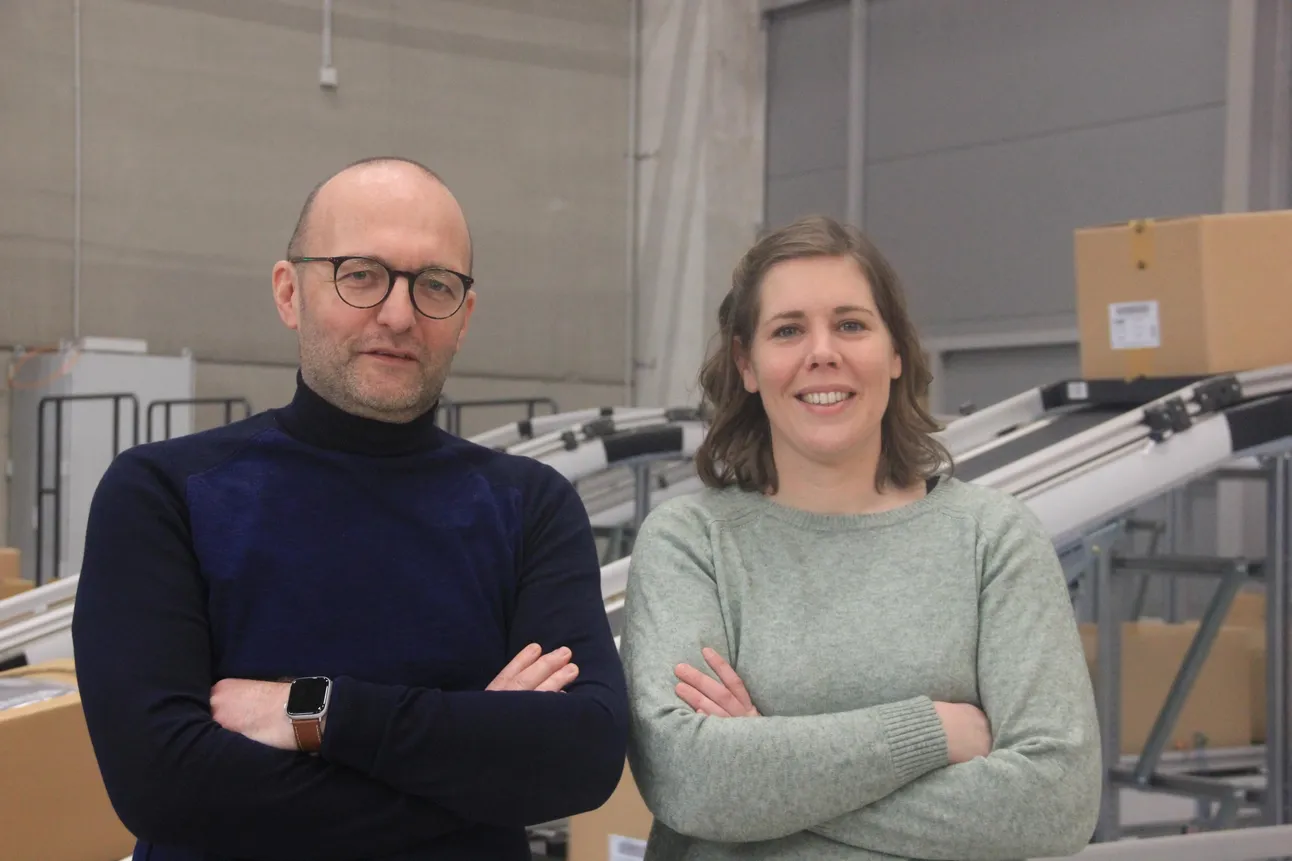
Een compacte opslag met slimme sturing. Dat is de basis van het distributiecentrum van Dassy Europe in Brugge. Dat dit concept de producent van werkkleding geen windeieren legt, blijkt wel tien jaar na de oprichting van het magazijn. Ondanks de snelle groei slaagt de ambitieuze kmo erin telkens een versnelling hoger te schakelen. De meest recente stap is de implementatie van een shuttlesysteem, dat is afgestemd op fijnmazige orderpicking. Een verhelderende blik op de stapsgewijze groei krijgen we van Hanne Bouckaert en Nico Delmulle, respectievelijk warehouse operations manager en senior manager supply chain bij Dassy.
Sinds zijn ontstaan in 2007 is Dassy uitgegroeid tot een internationale speler op het vlak van professionele werkkledij. Vandaag heeft het bedrijf het volledige proces, van ontwerp tot logistiek, in eigen handen. Een eigen Belgisch R&D-team staat in voor de creatie van de collecties, die worden vervaardigd in het eigen productiecentrum. Dat ligt in Sri Lanka, waar maar liefst 1.800 mensen werken. Het distributiecentrum in Brugge levert aan ongeveer 1.350 professionele verdelers in meer dan twintig landen. Op het hoofdkantoor in Brugge zijn een tachtigtal medewerkers actief, waarvan twintig de logistiek in het magazijn in goede banen leiden.
Stap naar eigen distributiemagazijn
Toen Dassy besloot in Brugge een eigen magazijn op te richten, had het bedrijf nog geen idee waar het vandaag zou staan. Daarom wilde de organisatie een zo flexibel mogelijk magazijnconcept, waar het alle richtingen mee uit kon. Om daarbij te helpen, nam Dassy het consultancybureau Logflow in de arm.
Nico Delmulle: “Ons hoofdkantoor lag toen in Oedelem, maar was veel te klein aan het worden. De logistieke activiteiten besteedden we uit aan een logistieke dienstverlener in het Antwerpse. We waren ervan overtuigd dat we een competitief voordeel konden creëren door onze logistiek in eigen handen te nemen. We hadden een productportfolio van 3.500 SKU’s, maar zagen dat aantal toen al gestaag groeien.”
De ideale stek voor het nieuwe distributiecentrum vond Dassy op een lap grond van één hectare in de Industriezone Herdersbrug, langs de Pathoekeweg in Brugge. Daar werden in eerste instantie een magazijn van 6.000m² en 1.500m² aan showroom en kantoren op gebouwd.
Groei in drie fases
Tot op vandaag kunnen we drie fases in de snelle groei van de kmo onderscheiden. Elke keer werd verder gebouwd op de vorige fase, wat een organische, continue uitbreiding mogelijk maakte.
Hanne Bouckaert: “In het masterplan dat Logflow tien jaar geleden voor ons uitstippelde, werd een langetermijnvisie vastgelegd zowel qua lay-out als werkingsprincipes. Ook de nodige WMS-functionaliteit om het magazijnconcept te ondersteunen, werd toen bepaald. Op basis daarvan hebben we gekozen voor het pakket van Vanboxtel software. Tot op vandaag biedt dat pakket de nodige flexibiliteit om ons dynamische magazijnconcept te ondersteunen.”
Fase 1: bouw van het manuele magazijn
Het initiële magazijn ziet er op het eerste gezicht zeer rechttoe rechtaan uit, met enerzijds palletrekken en anderzijds een collimagazijn. De drijvende kracht achter het palletmagazijn was – en is nog steeds – het ‘picking on demand’ (POD)- principe. Dat houdt in dat in de smalle gangen zowel combitrucks als orderpickers werken. Doordat het magazijn in verschillende zones is opgesplitst, bevinden de ‘fast movers’ zich in een andere ruimte dan de ‘slow movers’. Verder fungeren de grondlocaties als picklocaties voor fast en ‘medium movers’, maar dankzij de combitrucks kunnen trager bewegende producten ook op hoogte worden gepickt.
De slimme WMS-aansturing, maakt dat alle activiteiten op een veilige manier kunnen plaatsvinden. Zo verloopt de picking van hoger gelegen goederen met de combitruck in batch. Na die ‘pre-picking’ worden de goederen in een aparte zone klaargezet voor de orderpickers. Als de pre-picking rond is, kan worden gestart met de picking van de fast en medium movers op de grondlocaties. Op die manier wordt vermeden dat combitrucks en orderpickers tegelijkertijd in de gangen actief zijn.
Het collimagazijn is even hoog als het palletmagazijn, maar hier wordt met draadnetlegborden gewerkt. Dassy slaat er referenties op die in kleinere hoeveelheden binnenkomen. Ook in het collimagazijn wordt er zowel vanop de grond als in de hoogte gepickt. In het colli- en palletmagazijn samen werden in de beginperiode zo’n 550 orderlijnen per dag verzameld. Achteraf worden de goederen uit het collimagazijn samengevoegd met die uit het palletmagazijn.
Een van de belangrijkste principes in het magazijn van Dassy is dat binnenkomende producten niet bij de andere voorraad op een locatie mogen worden gelegd. Dat heeft verschillende voordelen. Zo wordt een perfecte ‘tracking & tracing’ mogelijk en kan er ook met verschillende versies van eenzelfde artikel worden gewerkt. Bovendien komen de locaties zo frequenter leeg, wat nultellingen mogelijk maakt. Dat komt de voorraadnauwkeurigheid ten goede.
Bijzonder was ook dat er in de eerste fase al meteen een mezzanine werd voorzien, hoewel dat toen nog niet noodzakelijk was. “Op aanraden van Logflow hebben we bij de bouw gekozen voor 12,5 meter vrij hoogte. Daardoor werd het mogelijk in de toekomst een logistiek concept uit te werken met een optimale vullingsgraad per kubieke meter”, legt Hanne Bouckaert uit. “Het heeft ons weliswaar moeite gekost om de directie te overtuigen van het nut van de mezzanine, maar achteraf bekeken zijn we erg blij dat we hebben doorgezet. Zonder hadden we de groei nooit op deze locatie aangekund.”
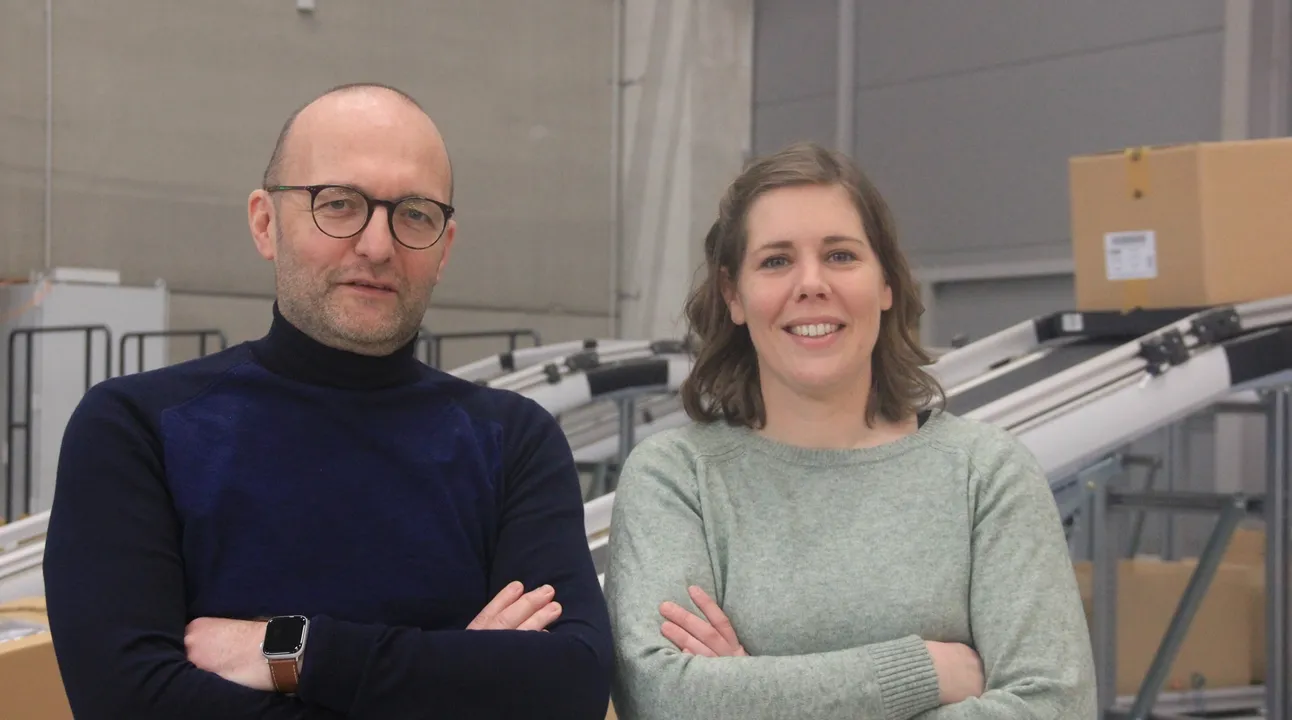
Fase 2: overgangsfase
In de loop van de jaren bleef Dassy gestaag groeien. Er kwamen steeds meer collecties bij. In 2015 vervoegde ook het PBM-assortiment (persoonlijke beschermingsmiddelen) van Proteq het magazijn. Dat bedrijf behoorde al enkele jaren tot Dassy, maar de voorraad zat tot dan toe in Kalmthout. Het grote assortiment van dat bedrijf joeg de voorraad meteen de hoogte in.
Toen het magazijn 1.800 orderlijnen per dag moest gaan verwerken en er 12.200 SKU’s lagen opgeslagen, waren de limieten bereikt. Het was tijd om over te schakelen naar meer picklocaties en een nog efficiëntere werking.
Twee nieuwe opslagmethodes deden hun intrede. Daaruit kon zo’n 45 procent van de picklijnen worden gepickt, waardoor de druk op de picklocaties in het palletmagazijn afnam. Enerzijds kwamen er op de mezzanine doorrolstellingen om kleine, zeer snel roterende goederen te picken. Omdat per kanaal dozen van één referentie werden opgeslagen, werd het mogelijk de snelst roterende goederen op een zeer beperkt oppervlakte op te slaan. Anderzijds kwamen er voor de opslag van kleine, trager roterende referenties twee verticale liftmodules. Wanneer de ene lift een wissel van het legbord uitvoert, kan de operator aan de andere lift een picking uitvoeren, wat een hoge pickperformatie garandeert.
Om de ontvangst van goederen op de mezzanine te optimaliseren, kwam er een laagdrempelig ‘sort-to-light’-systeem voor pallets. Verder werd een conveyor voor dozen in het magazijn geïnstalleerd. Die moest de pickingzone op de mezzanine verbinden met de verpakkings- en expeditiezone. Geïntegreerd werden een weegsysteem, een automatische dozensluiter en een automatisch systeem om verzendlabels aan te brengen.
H. Bouckaert: “We wisten op voorhand dat dit een overgangsfase zou zijn, tot we klaar waren voor nog meer automatisering. Maar doordat we de meeste van deze oplossingen ook in de volgende fase konden blijven gebruiken, was het kapitaalsverlies minimaal. Uiteindelijk hebben we enkel de doorrolstellingen aan de kant moeten schuiven. De verticale liftmodules konden we nog steeds gebruiken voor de opslag van tags, labels en retours.”

Fase 3: uitbreiding met shuttlesysteem
Want zoals verwacht bleef Dassy verder groeien. Doordat het voorraadvolume en het aantal orderlijnen snel bleven stijgen, werd een paar jaar geleden beslist het bestaande gebouw uit te breiden. In 2014 had Dassy al besloten een aanpalend stuk grond te kopen. Toen de organisatie ook dat stuk grond in de logistieke operaties ging betrekken, wilde Dassy elke vierkante meter optimaal benutten.
De sterk gestegen output en de krapte op de arbeidsmarkt rechtvaardigden in dit stadium een sterke automatisering. In samenspraak met Logflow besliste Dassy een AS/RS-systeem te implementeren. Na een uitgebreide selectieprocedure viel de keuze op het shuttlesysteem van TGW. Dat op het niveau van de mezzanine werd geïnstalleerd.
H. Bouckaert: “Voor een kmo is de stap naar dergelijke doorgedreven automatisering uiteraard niet evident. Het heeft ook wel wat moeite gekost om de leverancier ervan te overtuigen dat wij dit project konden dragen. Omdat er op dat moment in de buurt geen resources beschikbaar waren, heeft TGW Iberica ons geholpen bij de implementatie. Die samenwerking is vlot verlopen en heeft geleid tot een goed werkend systeem. Ook de koppeling van de software met ons WMS liep van een leien dakje.”
In het shuttlesysteem staan horizontaal rijdende shuttles in voor het wegzetten en halen van dozen in en uit opslagkanalen. Die dozen staan op een uniforme tray, wat enerzijds het transport vereenvoudigt en anderzijds het systeem minder afhankelijk maakt van het formaat en de kwaliteit van de dozen. Via het systeem gebeurt alle stukpicking, behalve als het om dozen met weinig en zwaardere producten gaat, zoals schoenen of helmen. Die items worden nog steeds vanuit het conventionele gedeelte verzameld.
De shuttles voeren de dozen naar de lift, die ze naar beneden brengt, waarna ze via een conveyor hun weg naar het pickstation vervolgen. Daar worden dan de nodige items uit de doos gepickt, waarna de doos opnieuw het systeem ingaat. Het systeem bij Dassy telt drie gangen van 29 niveaus, met aan beide zijden een opslagkanaal. Elk opslagkanaal kan drie trays herbergen, wat goed is voor een opslagcapaciteit tot 54.000 dozen.
De shuttles zelf kunnen via een liftsysteem achteraan in elke gang van niveau wisselen. Met behulp van de 45 shuttles is het mogelijk met één enkel pickstation 400 picks per uur uit te voeren.
Nico Delmulle: “Dit systeem werkt erg efficiënt, zowel op het vlak van inslag, opslag als uitslag. Dankzij het doorgedreven ‘goods-to-man’-principe kunnen we een hoge pickperformantie garanderen, zonder dat de operator zich hoeft te verplaatsen. De operator kan er ook heel ergonomisch werken.”
Sinds de zomer van 2021 is het shuttlesysteem operationeel. Dankzij die automatisering kan Dassy vlot alle bestellingen die voor 12 uur ’s middags binnenkomen, nog voor 17 uur de deur uit krijgen. “Niet dat zulke snelle leveringen in onze business strikt noodzakelijk zijn, maar dat we het kunnen is wel een competitief voordeel. Het zorgt er immers voor dat de dealers hun voorraad in de winkel tot een minimum kunnen beperken”, aldus Nico Delmulle.
Verder doet het shuttlesysteem dienst als buffer. Zo kunnen gepickte dozen er tijdelijk worden ondergebracht voordat ze naar de klant gaan. Via het systeem is het ook mogelijk dozen in de gewenste volgorde (sequencing) bij de pickstations aan te leveren.
Om het shuttlesysteem optimaal te laten functioneren, was een goede wisselwerking met het WMS en het manuele magazijn cruciaal. Zo fungeert het manuele magazijn ook als bulkmagazijn voor het shuttlemagazijn. Om die herbevoorrading zo veilig en efficiënt mogelijk te laten verlopen, werd een palletlift geïnstalleerd, die de pallets vanuit het palletmagazijn naar de mezzanine brengt.
Om ook de aanvoer van dozen naar het shuttlesysteem zo vlot mogelijk te laten verlopen, implementeerde Dassy een gerobotiseerde dozensnijder. “We ontvangen onze goederen in dozen en slaan ze ook zo op. Maar het telkens opnieuw openen en sluiten van dozen aan het pickstation is erg tijdrovend. Daarom hebben we nu een vierassig robotsysteem dat vooraf automatisch de dozen opensnijdt. Zo krijg je een opening die de operator toelaat er vlot individuele stuks uit te picken”, legt Hanne Bouckaert uit. “Het afstellen van zo’n robot bleek evenwel niet evident. Zo moest hij voldoende diep snijden, zonder de inhoud te beschadigen. Omdat we over onze eigen productiefabriek in Sri Lanka beschikken, konden we gelukkig vlot samen het proces optimaliseren. Zo hebben we afspraken gemaakt over het maximale aantal stuks per doos en hebben we gevraagd de binnenflappen te verkleinen, zodat de robot een grotere pickopening kon maken.”
Verder kwam er ook een extra automatische dozensluiter die de verzenddozen naargelang de grootte van het order kan insnijden. Dat vermijdt niet enkel dat er lucht wordt getransporteerd, het laat Dassy ook toe met één enkel doostype te werken.
Tot slot kwam er een nieuwe kaai-infrastructuur, waardoor de inkomende en de uitgaande stroom van elkaar konden worden gescheiden. De nieuwe kade is gericht op het (manueel) lossen van containers vanuit de productiesite in Sri Lanka. Via een boxconveyor kunnen de dozen automatisch naar de mezzanine worden geleid. Om de dozen nog sneller en ergonomischer te kunnen lossen, werd bij Uvo Technologies een telescoopconveyor besteld. Daardoor kunnen de operatoren de dozen al in de container op de telescoopband zetten, op een ergonomische en snelle manier.
Veel hogere throughput op niet zoveel meer oppervlakte
Dankzij de komst van het automatische magazijn kan Dassy vandaag 5.000 orderlijnen verwerken. Dat is uiteraard een gigantisch verschil met de 550 orderlijnen die tien jaar geleden de deur uitgingen. Het assortiment schommelt vandaag tussen 12.000 en 15.000 SKU’s.
Met de uitbreiding heeft Dassy nu een magazijn van in totaal 10.000 vierkante meter ter beschikking voor zijn logistieke activiteiten, waarvan 1.800 vierkante meter voor de pickingactiviteiten is voorbehouden.
N. Delmulle: “Nog steeds blijven we sterk groeien; zo mochten we in 2021 een groei van veertien procent optekenen. Maar we hebben er vertrouwen in dat we op deze locatie ook de verdere expansie aankunnen. We kunnen bijvoorbeeld nog het aantal shuttles uitbreiden en we kunnen een extra pickstation plaatsen. Nu werken we in één shift, dus we zouden een extra shift kunnen inschakelen. Bovendien hebben we nog een stukje grond overgehouden waarop we een hoogbouw silomagazijn kunnen bouwen. We zijn in elk geval erg blij dat we bij elke fase grondig hebben nagedacht over de ruimtebenutting, Zo is in tien jaar tijd onze footprint met slechts veertig procent gestegen, terwijl de omzet is verdubbeld. Zonder een goed doordacht magazijnconcept was dat nooit gelukt.”
TC
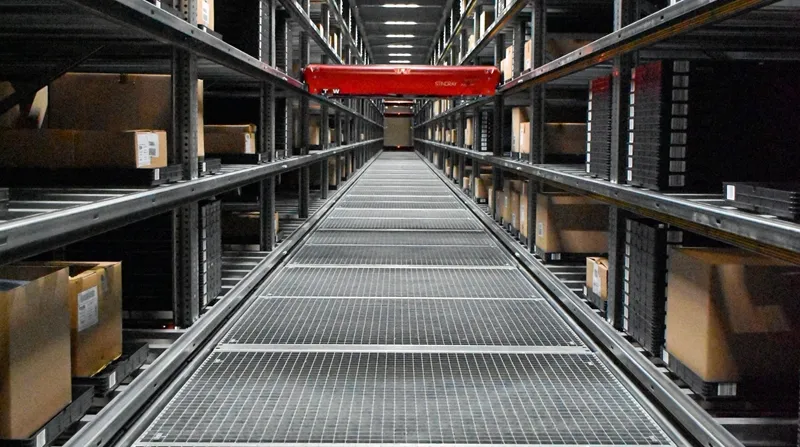