Magazijn in goede vorm
Chocolate World optimaliseert opslag en picking met Kardex
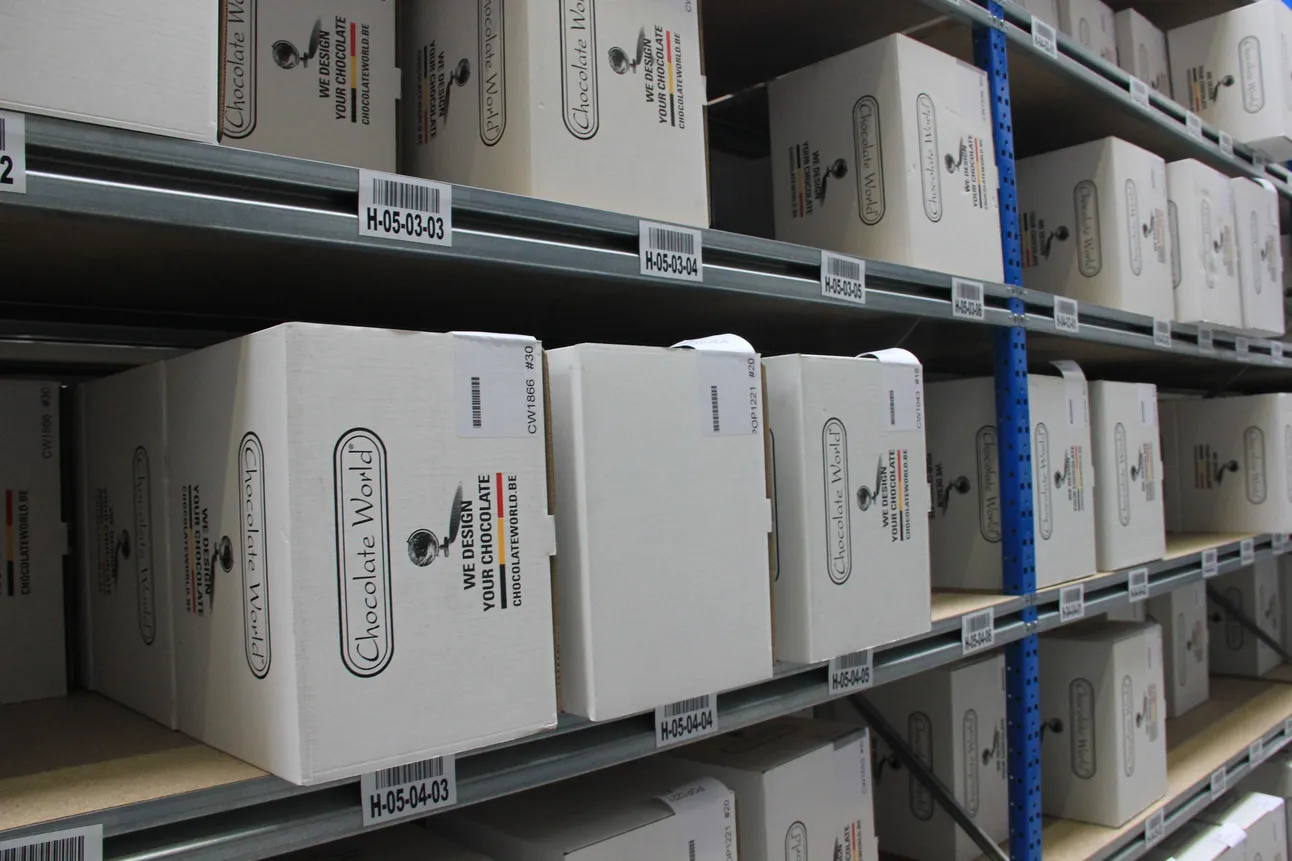
Toen Chocolate World op zoek ging naar een nieuwe ruimte voor zijn productie- en opslagactiviteiten, besloot de organisatie meteen ook een grotere efficiëntie in te bouwen. Daarop centraliseerde het bedrijf alle activiteiten in één gebouw en maakte het werk van een beter voorraadbeheer en dynamische orderpicking. Blikvanger in het nieuwe magazijn is de Kardex Remstar LR 35, een semi-automatische oplossing die een compacte opslag en efficiënte stukpicking van chocoladevormen garandeert. Achter de schermen kreeg Power Pick Global, het warehouse management system van Kardex, de verantwoordelijkheid om de magazijnstromen in betere banen te leiden.
Vandaag maakt Chocolate World enerzijds chocoladevormen uit polycarbonaat, anderzijds biedt het zijn klanten diverse machines om chocolade te bewerken (zie extra). Tijdens haar dertigjarige bestaan is de onderneming sterk geëvolueerd, zo blijkt al snel als we Hans Bruyndonx, aankoopverantwoordelijke bij Chocolate World, vragen naar de achtergrond van het bedrijf.
Belgische bodem als basis voor groei
Het waren de broers Vermorgen die het bedrijf in 1985 op de Kielsevest in Antwerpen oprichtten. De productie van de chocoladevormen vond toen nog in Portugal plaats. Toen de huidige vennoten, Jan Neven en Filip Buelens, in 1995 de firma overnamen, besloten ze de productie naar België over te hevelen. “Al bracht die beslissing hogere loonkosten met zich mee, we hebben wel meer vat op de kwaliteit van onze producten gekregen. Dat is voor ons, samen met klantenservice, het allerbelangrijkste”, vertelt Hans Bruyndonx.
Met het besluit om in België te gaan produceren nam niet alleen de kwaliteit toe, ook de productie kwam in een hogere versnelling terecht. Enerzijds werden er steeds grotere aantallen gemaakt, anderzijds stegen de diversiteit en de variëteit van het productportfolio. “De nieuwe eigenaars reisden de wereld rond om onze producten aan de man te brengen, waardoor ook de internationale activiteiten een snelle expansie kenden. Momenteel blijft ongeveer 30% van onze producten in de Benelux, de rest is voor export bestemd”, voegt Hans Bruyndonx eraan toe.
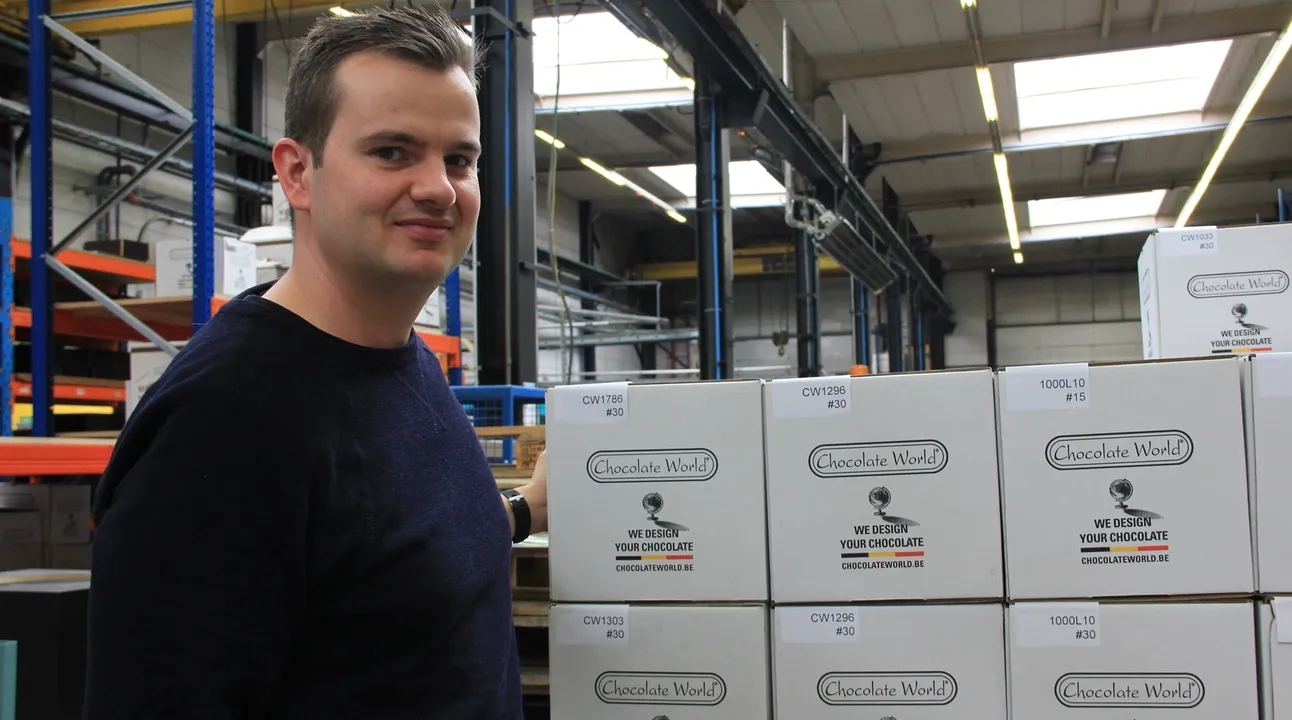
De stap naar centralisatie
Een drietal jaar geleden begon die snelle expansie Chocolate World parten te spelen. Op dat moment had Chocolate World zijn winkel en opslagruimte in de Lange Elzenstraat in Antwerpen. Dat magazijn begon uit zijn voegen te barsten. Bovendien was de manier van werken er niet ideaal.
Hans Bruyndonx: “Toen we dertig jaar geleden met onze eerste vorm zijn gestart, hebben we die op een vaste locatie in een rek gelegd. Daarnaast kwam vorm nummer twee, dan nummer drie, enzovoort. Naarmate er meer artikelen kwamen, werden de pickafstanden groter. Bovendien kregen we steeds vaker met voorraadafwijkingen te kampen. Aanvankelijk deden we alles ook met pen en papier. Een stap in de goede richting was wel de komst van ons ERP-systeem in 2012, een maatwerkprogramma dat ons meer inzicht in onze voorraden gaf. We zijn toen ook met RF-scanners beginnen werken. Helaas had die ERP-oplossing haar beperkingen op logistiek vlak. Zo gaf het systeem ons maar één voorraadcijfer, waardoor we niet wisten of een stuk nu in het magazijn of in onze winkel lag.”
Daarbij komt dat de productiesite zich in Hoboken bevond, wat continu transport van de fabriek naar het magazijn vereiste. “Bovendien werd ook die productiesite te krap. Om bijvoorbeeld grotere vormen voor industriële klanten te maken, waren meer spuitgietmachines nodig en daar was geen plaats meer voor. Ook dat betekende een rem op de groei”, voegt Hans Bruyndonx eraan toe.
Dat alles deed Chocolate World uitkijken naar een andere locatie, waar zowel de productie als het magazijn terecht konden. In de zomer van 2015 verhuisde de productie alvast naar een ruimere locatie in Hoboken, vlakbij de oude fabriek. Een jaar later volgde ook het magazijn. Voor de winkel en showroom werd een stuk bijgebouwd.
Oplossingen voor stukpicking onder de loep
Wat het magazijn betreft, kreeg Chocolate World in het nieuwe pand weliswaar iets minder vloerruimte, maar met zijn acht meter is het wel hoger dan het oude gebouw. Die hoogte wilde de organisatie dan ook optimaal benutten.
Daarnaast was een betere ergonomie voor de medewerkers een aandachtspunt.
Hans Bruyndonx: “Onze vroegere dozen bevatten negentig vormen en wogen 45 kilogram. Dat betekende dat onze medewerkers heel wat gewicht moesten sleuren. In het nieuwe magazijn wilden we gaan werken met kleinere dozen, gevuld met dertig vormen. Tegelijk hebben we ervoor gezorgd dat de nieuwe dozen samen ook goed op een verzendpallet passen, wat vroeger ook niet het geval was. Maanden zijn we bezig geweest om al onze vormen in kleinere dozen om te verpakken. Ook de manier van werken moest beter. In het oude magazijn pickten we zowel dozen als stukken uit de legbordstellingen, wat het proces nog arbeidsintensiever maakte. Daarnaast wilden we een beter voorraadbeheer, zodat we bijvoorbeeld wisten of we een stuk in de winkel of het magazijn konden vinden, wat ons heel wat zoekwerk zou besparen.”
Chocolate World besloot in het nieuwe magazijn naast het palletmagazijn opnieuw een conventioneel rekkenmagazijn voor zijn dozen in te richten. “Wel hebben we enkele maatregelen genomen om er efficiënter te kunnen picken. Zo werken we er niet meer met vaste locaties, maar met dynamische locaties. Bovendien hebben we er de stukpicking weggetrokken, zodat daar in principe alleen nog dozen worden verzameld.”
Om de stukpicking efficiënter te laten verlopen, ging Chocolate World op zoek in het ruime aanbod ‘goods-to-man’-oplossingen. “Het systeem moest in staat zijn zo’n 300 orderlijnen per dag te verzamelen. Geen enorme hoeveelheden, aangezien we vaak volle dozen verkopen. Eerst hebben we de beschikbare miniloadsystemen onder de loep genomen. Al snel bleken die voor ons veel te groot en te duur”, klinkt het. “Vervolgens hebben we ons oor te luisteren gelegd bij aanbieders van liftsystemen. Die systemen waren financieel wel interessanter, maar op het vlak van rentabiliteit en ergonomie niet ideaal. Zo hadden we bijvoorbeeld twaalf lopende meter aan liften nodig om onze 1.500 referenties in dozen op te slaan, wat voor de operator nog steeds behoorlijke loopafstanden betekende.”
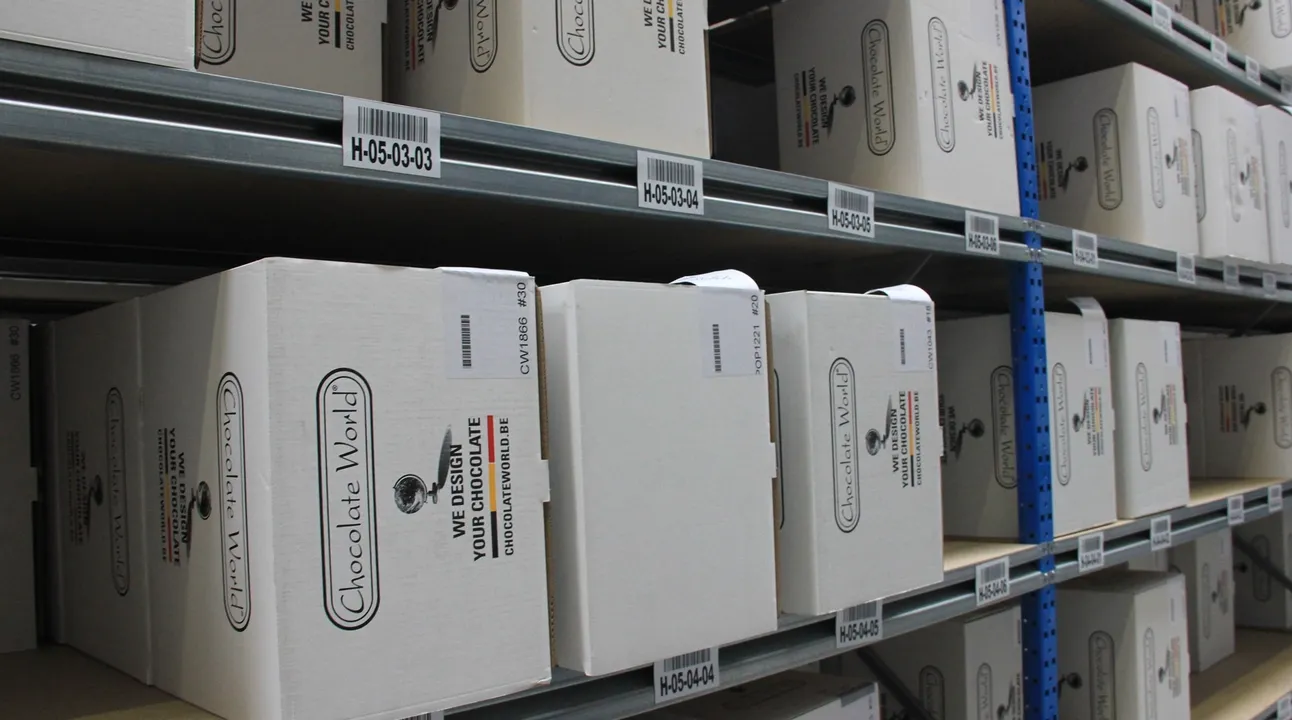
Keuze voor Kardex
Eind 2015 kwam Chocolate World in contact met Kardex, die net een nieuwe semi-automatische oplossing voor orderpicking had gelanceerd, de Kardex Remstar LR35. Enkel in Duitsland werkte al een bedrijf met het systeem.
Hans Bruyndonx: “Je kunt het systeem vergelijken met een miniload, maar dan in het klein. Toen we de installatie in Duitsland hadden bezocht, leek ons dat precies wat we nodig hadden. Hoewel het een uitdaging zou zijn om als een van de pioniers dit systeem tegen de deadline geïnstalleerd te krijgen – het oude gebouw was verkocht en moest tegen augustus 2016 leeg zijn – hebben we toch de sprong gewaagd.”
Samen met de LR 35 heeft Chocolate World ook Power Pick Global, het warehouse management system van Kardex, aangeschaft. “Door dat systeem aan ons ERP te koppelen, wilden we de voorraden en stromen binnen ons magazijn beter gaan beheren. Voor ons magazijn biedt dit WMS ruim voldoende functionaliteit’, zegt Hans Bruyndonx. “Kardex heeft ons ook geholpen bij het uittekenen van de verschillende opslaglocaties: de palletzone, de legbordstellingen met locaties van drie dozen diep, de LR 35 én de winkel met showroom, die per slot van rekening ook een belangrijk gedeelte van onze voorraad herbergt.”
Uiteindelijk werd de LR 35 in september geïnstalleerd, in oktober volgde de implementatie van het WMS. “Dat betekent dat we na de intensieve verhuizing nog een maand op de oude manier hebben gewerkt, met vaste locaties en picking van stuks uit het legbordmagazijn. We hebben toen toch wel moeite gehad om de orders te volgen. Gelukkig heeft die periode niet erg lang geduurd. De komst van de LR 35 en het WMS was dan ook een verademing”, weet Hans Bruyndonx. “Toen we met de dynamische locaties van start gingen en de doos- en stukpicking van elkaar konden scheiden, zorgde dat al meteen voor een enorme efficiëntieverbetering.”
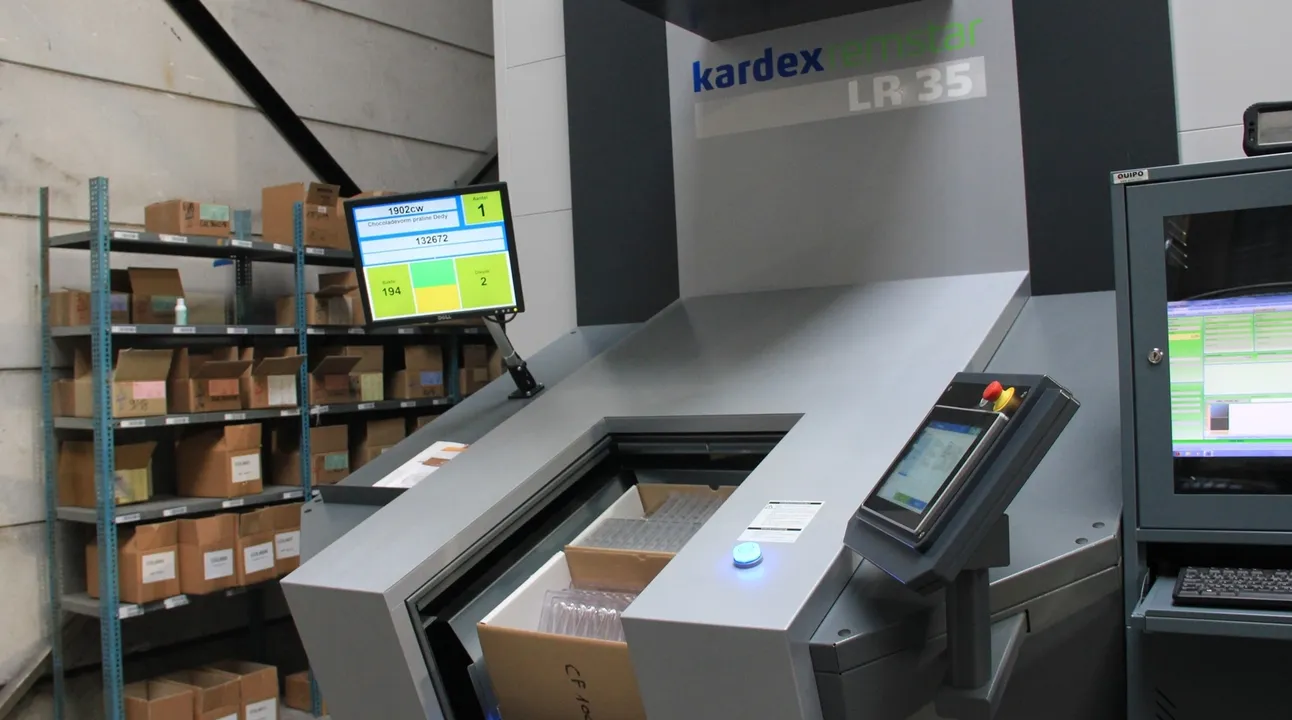
De LR 35: miniload in het klein
Met maximaal 500 orderregels per pickstation is de Kardex Remstar LR 35 vooral geschikt om kleine en lichtgewicht onderdelen met een relatief lage omloopsnelheid efficiënt te verzamelen. Chocolate World koos voor een concept met twee Kardex Remstar LR 35-installaties die de hoogte van het nieuwe magazijn optimaal benutten. In elke LR 35 is er plaats voor 684 trays van 640x440mm. Op elke tray plaatst Chocolate World twee dozen, waarbij elke doos met dertig vormen gevuld is. De twee LR’s samen bieden dus in totaal ruimte aan 2.736 dozen.
Is een stuk uit een doos nodig, dan brengt de kraan de tray met twee dozen naar een afzetpunt. Daar draait de tray vervolgens via een horizontaal carrouselsysteem naar de pickpositie, waar de orderpicker de tray opwacht. Op basis van de instructies op het touchscreen pickt de orderpicker het gewenste aantal producten uit de juiste doos op de tray. De herbevoorrading met nieuwe dozen gebeurt aan dezelfde zijde als de orderpicking. Die vindt plaats op de rustige momenten, als er geen of weinig pickactiviteit is.
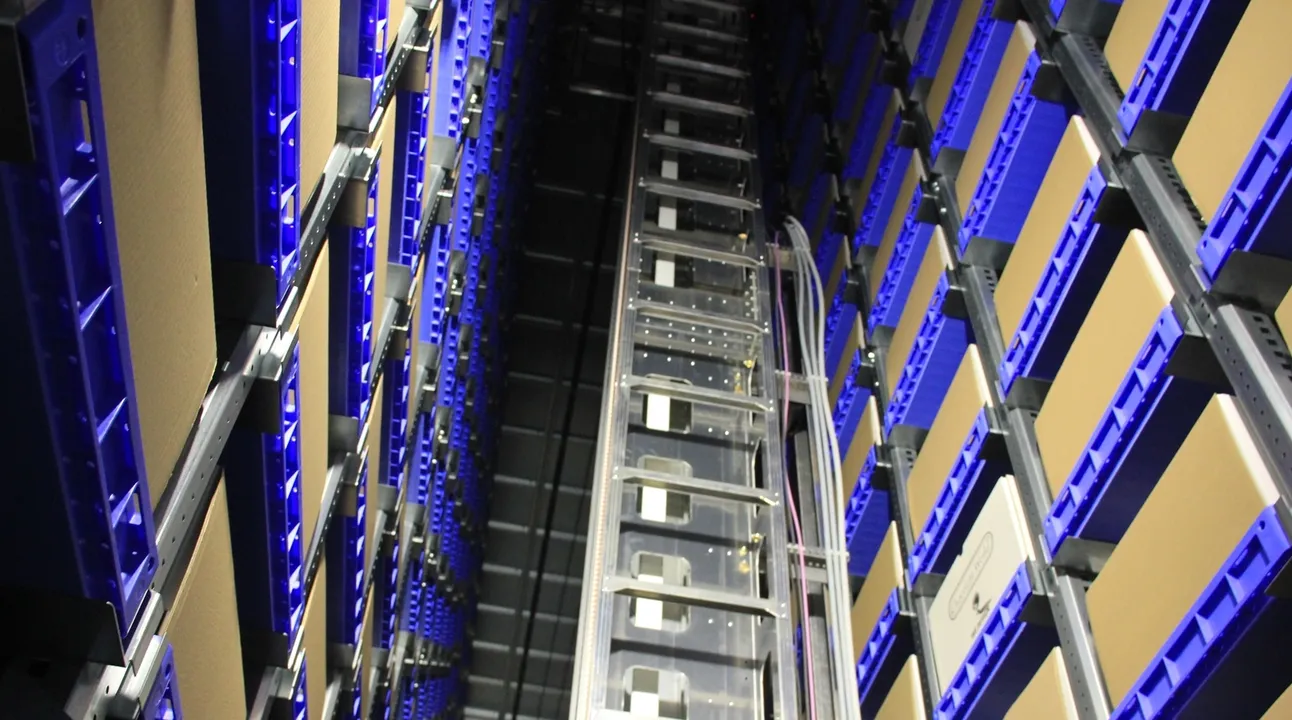
Tijd voor verdere finetuning
Intussen heeft Chocolate World zijn draai in het nieuwe magazijn gevonden. Tegenover de vroegere situatie is een grote vooruitgang geboekt op het vlak van efficiëntie en transparantie. De doorlooptijden zijn versneld, de loopafstanden voor de medewerkers drastisch verkort en de voorraadaccuraatheid is toegenomen. Dat het magazijn nu aan de productie grenst, helpt bovendien om de productie beter op de verwachte verkoop af te stemmen. Bovendien merkt Chocolate World dat de gebruikersvriendelijke systemen het een stuk gemakkelijker maken om tijdelijke of nieuwe krachten in te schakelen.
Een grote vooruitgang is ook dat de winkelvoorraad sinds de komst van het WMS apart kan worden beheerd. Raakt de voorraad van een bepaald artikel in de winkel op, dan wordt er met één druk op de knop een order in het magazijn gegenereerd. “Onze winkelrekken zijn nu ook veel beter gevuld dan vroeger”, vertelt Hans Bruyndonx. “Om een voorbeeld van onze gestegen performantie te geven: vroeger bundelden we onze orders op dag en vaak begonnen we die pas op dag twee te verzamelen. Nu vertrekt een order dat voor 15 uur is ingegeven vaak nog dezelfde dag.”
Dat betekent uiteraard niet dat er geen ruimte voor verdere verbetering is.
Hans Bruyndonx: “Alle standaardvormen zitten intussen in het WMS, maar nog steeds zijn we bezig om nieuwe en minder courante producten in te voeren, bijvoorbeeld klein gereedschap voor chocolatiers. Daarnaast probeert Chocolate World het aantal manipulaties in het magazijn nog naar beneden te krijgen. Dat doen we bijvoorbeeld door met staffelprijzen te werken en zo onze klanten te stimuleren om vormen per omdoos aan te kopen. Verder proberen we via het WMS de dozen in het magazijn steeds optimaler te plaatsen met het oog op een zo efficiënt en ergonomisch mogelijke picking.”
Ook de manier waarop Chocolate World met de LR 35 werkt, wordt continu geëvalueerd en geoptimaliseerd. “Al snel zijn we er achter gekomen dat we elke tray best altijd van twee dozen konden voorzien, zelfs al is één ervan leeg. Als we maar één doos op een tray zetten, bestaat immers het risico dat die tijdens het transport begint te schuiven. Om zoveel mogelijk referenties in het systeem op te slaan, hebben we er niet voor gekozen om elk stuk in beide LR 35’s op te slaan. Mocht er zich al eens een technisch probleem met een LR 35 voordoen, dan kunnen we het stuk ook manueel uit het systeem of uit een van de dozen op de legbordstellingen halen”, illustreert Hans Bruyndonx.
“Terwijl we de LR 35 aanvankelijk op basis van de algemene regels hebben laten werken, is het nu tijd om te finetunen op basis van onze specifieke noden. Zo werden producten in het begin zo snel mogelijk gepickt, terwijl wij vooral dozen in de LR 35 willen leegmaken om snel een nieuwe doos te kunnen opslaan. Had je vroeger zes vormen nodig, dan ging de kraan meteen een doos met pakweg tien vormen halen, terwijl wij liever hebben dat ze eerst een doos met vijf vormen haalt en dat we de laatste vorm vervolgens uit een nieuwe doos halen”, gaat hij verder. “We houden in de LR 35 nu ook maximaal nog één doos aan van producten die meestal in dozen of op pallet worden besteld. Zo maken we plaats vrij voor referenties die wel vaak per stuk de deur uitgaan. Zulke zaken kunnen we gemakkelijk zelf aanpassen in het systeem.”
In de nabije toekomst wil Chocolate World als aanvulling op zijn LR 35’s nog een pick-to-light systeem (PTL) van Kardex toevoegen.
Hans Bruyndonx: “Nu verzamelen we de orders uit de LR35 op karren. Het pick-to-light-systeem met twintig locaties zal ons toelaten bijvoorbeeld nog sneller één referentie voor verschillende orders tegelijk te verzamelen. Nu is dat nog niet echt nodig, maar naarmate we groeien, zal dat systeem interessanter worden. De PTL kan ook de foutenlast nog verlagen. Nu is het wel zo dat we elk uitgaand order voor alle zekerheid nogmaals controleren. Onze vormen worden wereldwijd verzonden, dus eventuele fouten van onze kant zijn heel duur.”
Het nieuwe magazijn en oog voor continue verbetering laten Chocolate World vandaag toe om verdere groei in de toekomst op te vangen, zonder dat daarvoor extra medewerkers in dienst genomen moeten worden. “Vorig jaar zijn we bijvoorbeeld met acht procent gegroeid, waarbij de snelle en efficiënte orderverwerking een niet te onderschatten rol heeft gespeeld. Nu we er opnieuw volledig voor kunnen gaan, verwachten we dat die groei zich alleen maar zal doorzetten. Op onze nieuwe site zijn we daar nu helemaal klaar voor”, besluit Hans Bruyndonx.
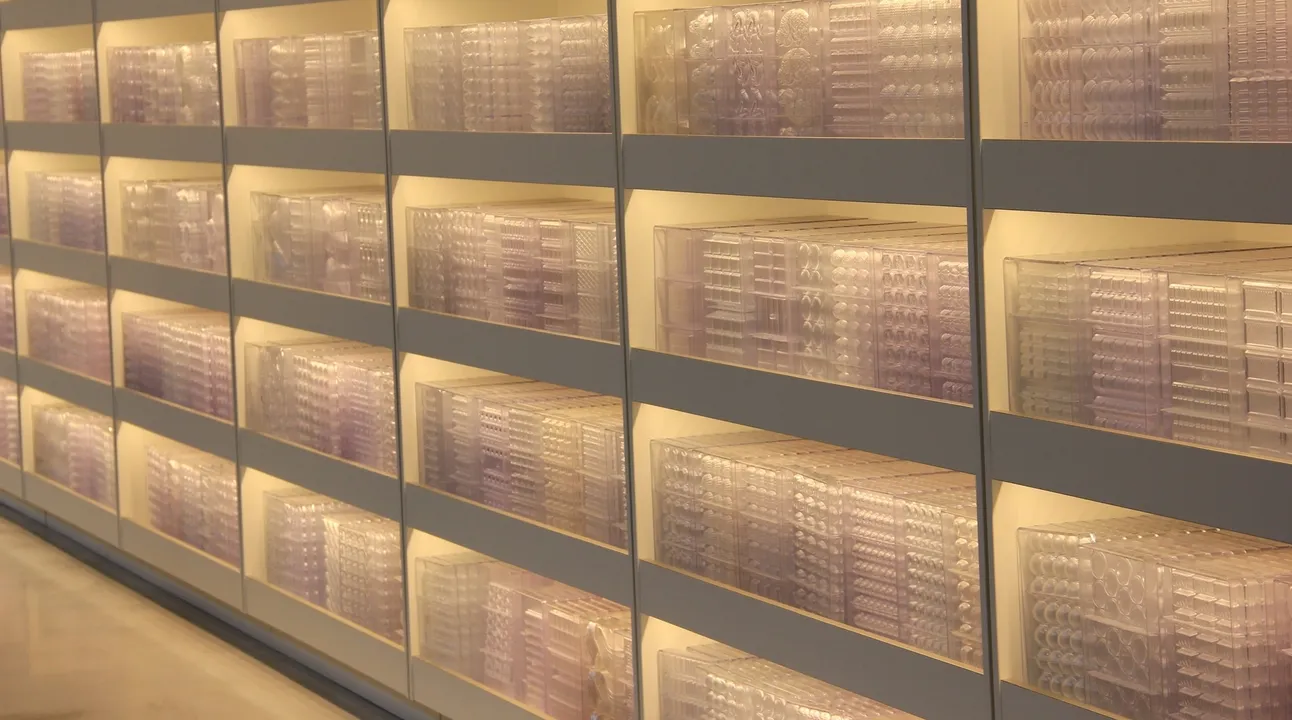
Extra
Chocolate World brengt chocolade ‘in shape’
Ben je als chocolatier of bakker op zoek naar mallen om chocoladefiguren te vormen, dan ben je bij Chocolate World in Hoboken aan het goed adres. Daarnaast levert Chocolate World zijn mallen aan industriële chocoladefabrikanten. De producten van Chocolate World gaan naar meer dan 140 landen. Om zijn producten aan de man te brengen, heeft Chocolate World wereldwijd verkoopkantoren en verdelers.
Wat betreft de chocoladevormen, zijn er naast de permanente collectie ook themagerichte collecties, zoals de Belle Epoque’ dit jaar. Intussen heeft Chocolate World zo’n 1.500 verschillende standaardvormen op voorraad. Het is ook mogelijk mallen volledig op maat van de klant te makenaarmee het mogelijk is honderden pralines tegelijk te vormen. Daarnaast produceert Chocolate World tevens siliconen vormen om snoep te maken.
Om chocolatiers of bakkers te helpen om gemakkelijk hun eigen chocoladefiguren te maken, biedt Chocolate World diverse machines aan. Zo kunnen ze met Chocolate World’s automatische tempereermachines chocolade perfect afsmelten tot de juiste temperatuur, om er daarna de juiste vorm aan te geven. Chocolate World werkt verder aan een ‘bean to bar’-concept, waarmee chocolatiers op basis van geroosterde cacaobonen hun eigen chocolade kunnen maken, om zo nog meer hun eigen touch aan de producten te geven. Daarnaast biedt Chocolate World met ‘Your Chocolate Factory in a Box’ een complete productieoplossing aan – met onder andere een tempereertoestel, smeltkast, koelwerkbank en vormen – voor wie zijn eigen chocoladeatelier wil starten. In Chocolate World’s ‘Belgian Chocolate School’ kunnen zowel beginnen de als ervaren chocolatiers terecht voor individuele opleidingen op maat.