Logistieke sites met visie
Gheys Logistics ruilt traditioneel voor state-of-the-art-beheer
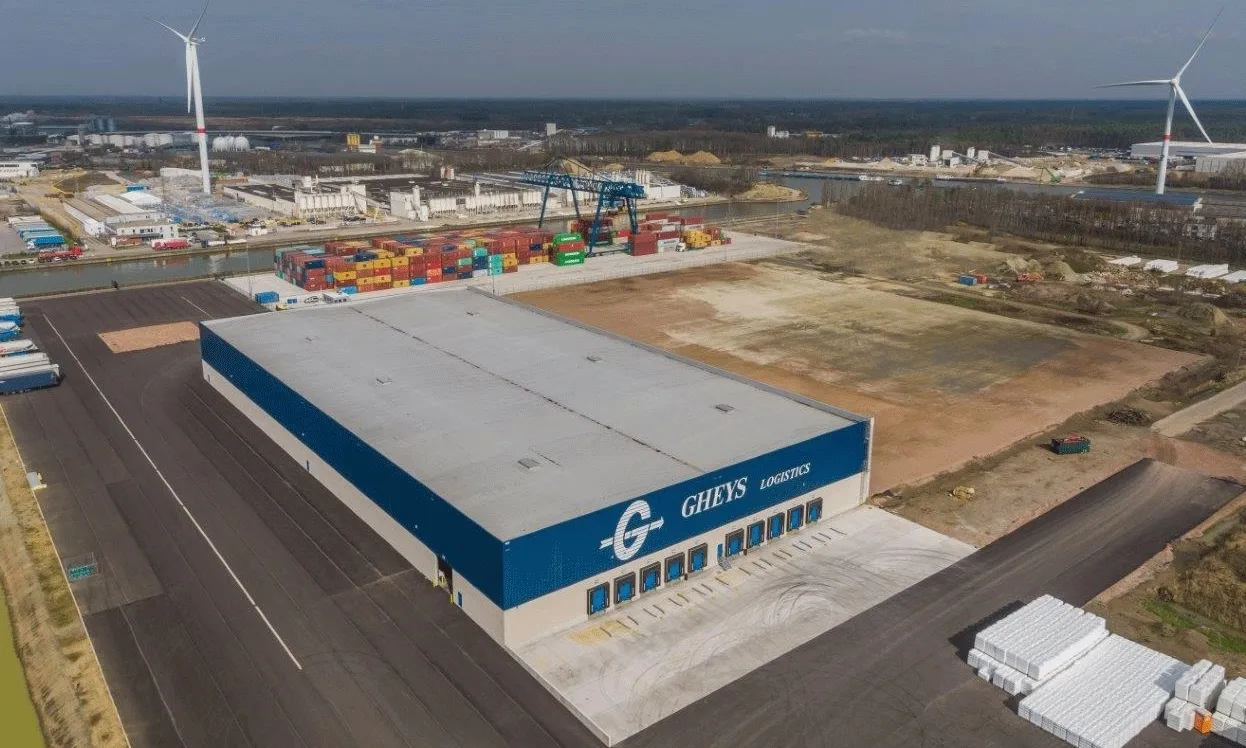
Van oudsher runde Gheys Logistics de processen op zijn sites op een zeer conventionele manier. Toen de organisatie in Beringen tegen haar fysieke grenzen aanliep, besloot Gheys Logistics zijn logistiek slimmer aan te pakken. Om meteen de juiste beslissingen te kunnen nemen, riep het bedrijf de hulp in van consultancybureau Logflow. Op basis van de geleerde lessen werd ook de nieuwe terminal annex warehouse aan het Albertkanaal meteen op de meest efficiënte manier opgezet.
Elk jaar mag Gheys Logistics een structurele groei van 3 à 10% optekenen. Die groei is voor een groot stuk te danken aan de stijgende import van petrochemische grondstoffen (zie ook kader). Een vijftal jaar geleden kreeg de vestiging van Gheys in Beringen het echter steeds moeilijker om het stijgende aantal vrachtwagens op zijn site te slikken.
David Van Craenenbroeck, site manager bij Gheys Logistics: “Vooral de efficiëntie van de zogenaamde koerwerking leed onder de groei. Dat maakte dat we almaar meer problemen kregen met de mobiliteit rond onze wachtparking, waar de trucks komen laden en lossen. Zo hadden we moeite om het overzicht te houden over de status die vrachtwagens hadden, of ze al geregistreerd of beladen waren bijvoorbeeld. De gebrekkige organisatie werkte de congestie op de site in de hand. Onze magazijnaansturing verliep bovendien erg manueel. De heftruckchauffeurs kregen een werkbon en op basis daarvan moesten ze hun opdrachten vervullen. Vervolgens moesten we die werkbonnen administratief verwerken. Dat zorgde geregeld voor fouten en gegevensverlies.”
Dat er iets moest veranderen, was wel duidelijk. Eén mogelijkheid was de wachtparking te vergroten. Op en rond de site van 50 hectare was immers nog voldoende ruimte voor uitbreiding. Gheys Logistics besloot evenwel een andere weg in te slaan en samen met Logflow op zoek te gaan naar mogelijkheden om in de eerste plaats de efficiëntie binnen de huidige contouren van de site te verhogen.
Eric Vandenbussche, directeur van Logflow: “Toen we de werking op ons terrein onder de loep namen, zagen we meteen dat de doorstroming niet naar behoren verliep. In feite merkten we vooral symptomen van inefficiënte operaties. In plaats van die symptomen te bestrijden door – zoals in veel gevallen gebeurt – extra ruimte te creëren, is het beter op zoek te gaan naar de oorzaak. Alleen op die manier kun je werken aan een oplossing op lange termijn.”
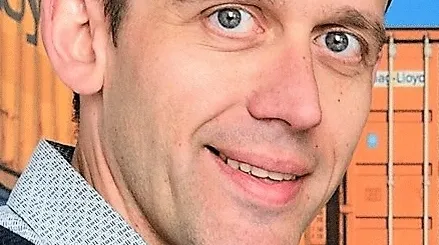
Link tussen wachtparking en magazijn
Om te beginnen werden de activiteiten van Gheys Logistics grondig doorgelicht. In hoofdzaak behandelt de logistiek dienstverlener relatief hoogwaardige goederen met een laag verpakkingsdichtheid, waar weinig detailpicking van toepassing was. Bij Gheys Logistics is een goed volumebeheer dan ook cruciaal om de efficiëntie te optimaliseren en de kosten onder controle te houden. Verder moet Gheys Logistics als logistiek dienstverlener een maximale flexibiliteit kunnen garanderen en op heel uiteenlopende klanteneisen kunnen inspelen. Samengevat komt het er bij Gheys Logistics op aan een evenwicht te vinden tussen de vier cruciale logistieke drijvers: klantenservice, efficiëntie, flexibiliteit en een optimale ruimtebenutting.
“Het belangrijkste probleem – de gebrekkige koerwerking – hadden we zeker kunnen oplossen door enkel en alleen een dock & yard management te introduceren”, weet Eric Vandenbussche. “Alleen waren we in dat geval voor suboptimalisering gegaan. Finaal wilde Gheys Logistics de doorlooptijd van de trucks op de site zoveel mogelijk verbeteren. Dan is het noodzakelijk om ook de link tussen de wachtparking en het magazijn onder de loep te nemen. Beide zijn immers onlosmakelijk met elkaar verbonden.”
Afstand-intensiteitsmatrix geeft inzicht
Om suboptimalisering te vermijden, bracht Logflow de logistieke processen in kaart. “Door tot in detail uit te pluizen hoe Gheys Logistics werkt, konden we de specifieke triggers spotten waarop we moesten werken om de operaties weer gezond te maken”, legt Eric Vandenbussche uit. “Daarbij hebben we alle specifieke kenmerken van de producten en zaken zoals de seriegroottes geanalyseerd.”
In een afstand-intensiteitsmatrix van de ‘as is’-situatie werden de goederenstromen gemapt en gedefinieerd. Die matrix geeft zicht op de rij- en loopafstanden, de uitgevoerde activiteiten, de operatorgroepen en de ingezette middelen. Tijdens deze oefening werden ook de trajectparameters bepaald. Denken we maar aan de opname en afzet, het aantal dragers per beweging, de snelheid van de uitvoering en de intensiteit van de goederenstromen op dagbasis.
E. Vandenbussche: “Zo’n matrix geeft ons een goed beeld van de aard van de verschillende stromen: over een lange afstand met een hoge intensiteit, over een korte afstand met een lage intensiteit, over een korte afstand met een hoge intensiteit en over een lange afstand met een lage intensiteit. Afhankelijk daarvan konden we de juiste keuzes maken. Zo zullen stromen over een korte afstand met een hoge intensiteit zich eerder lenen voor automatisering.”
Die matrix hielp ook om de operationele kosten te bepalen. “Concreet zijn bij Gheys Logistics dertien medewerkers met de logistiek op de site bezig”, vervolgt Eric Vandenbussche. “Via een arbeidsanalyse konden we uitmaken hoeveel van hun tijd er effectief naar logistieke taken ging. Bij Gheys Logistics bleek er heel wat – lees: te veel – tijd te gaan naar wat wij ‘desorganisatie’ noemen. Daarmee bedoelen we bijvoorbeeld het ophalen van documenten, dockpoorten openen of sluiten, een praatje maken met collega’s, het plaatsen van kegels of het zoeken naar sleutels. Uiteraard zijn heel wat van die zaken onvermijdelijk. Maar terwijl we voor dit type organisaties kunnen uitgaan van een percentage van ongeveer 30%, bedroeg dat aandeel bij Gheys Logistics 40%.”
Op basis van al die analyses bleek al snel dat de problematiek op de site effectief verder reikte dan de wachtparking alleen. “Vrachtwagens stonden bijvoorbeeld relatief lang aan de kade omdat we alles wat we uit de vrachtwagen haalden, met heftrucks meteen op locatie in het magazijn zetten. Niet alleen op de wachtparking zelf, maar ook bij de overdracht van de goederen naar het magazijn knelde het schoentje dus”, illustreert David Van Craenenbroeck. “We hanteerden ook geen ABC-sturing op de goederen naargelang hun rotatie. Dat betekende dat de workload moeilijk uit te balanceren was en medewerkers zich vaak verplaatsten zonder dat ze effectief met een opdracht bezig waren. We hadden sterk versnipperde stromen en geen oog voor dubbelspel. Ook op het vlak van registratie en tracking & tracing was er zeker verbetering mogelijk. Zo hanteerden we een erg manueel locatiebeheer en scanden we niet.”
Daarnaast was er werk aan de winkel op het vlak van het masterdatabeheer.
E. Vandenbussche: “We kunnen gerust stellen dat de mate waarin je een magazijn kunt optimaliseren, recht evenredig is met de kwaliteit van de materdata. Last but not least waren er tal van zaken die een vlotte doorstroming bemoeilijkten. Zo was er geen statusbeheer bij het lossen en laden en had Gheys Logistics het moeilijk om op prioriteiten te sturen.”
Op basis van de grondige analyses kon gericht naar een nieuwe oplossing worden gezocht. Uiteraard werd daarbij rekening gehouden met de groeiverwachtingen en de markten die Gheys Logistics in de toekomst nog wil aanboren.
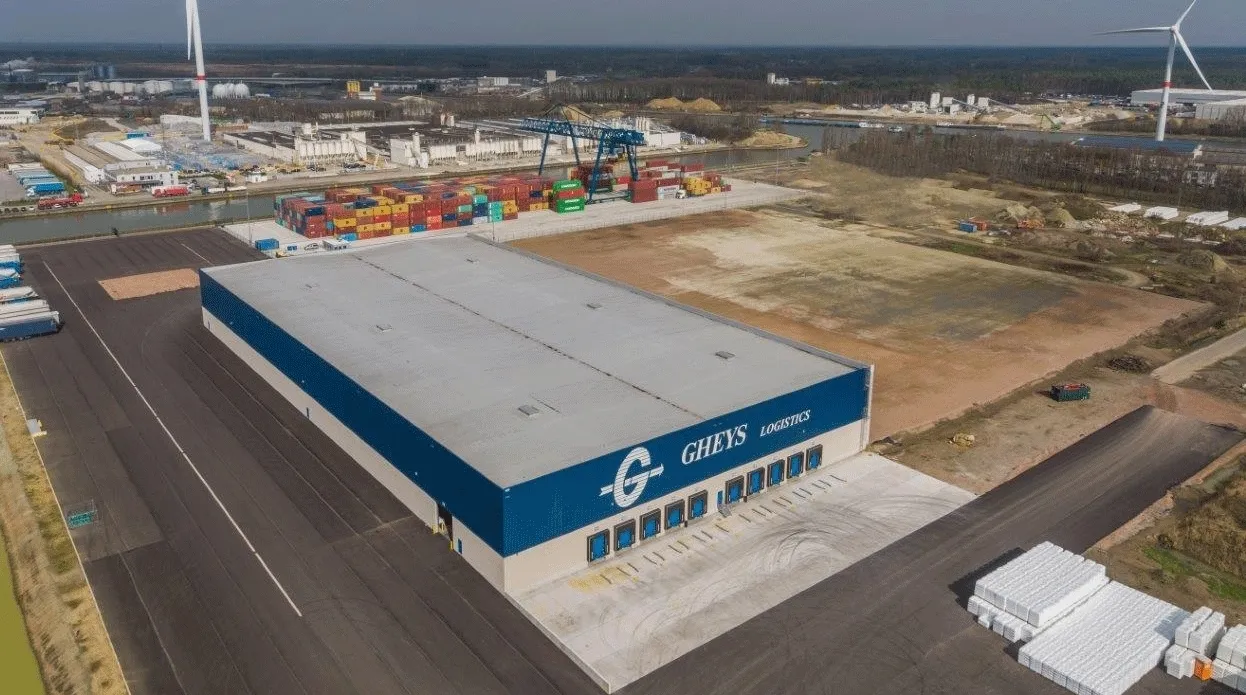
Actie op diverse fronten
Om voor een betere doorstroming op de site te zorgen, werd door C&W Logistics een volwaardig WMS (warehouse management system) op de site geïmplementeerd. Aanvullend werd een gedegen dock & yard aansturing opgezet. Dat dock & yard management moest er bijvoorbeeld voor zorgen dat de vrachtwagens pas naar de kade worden geleid op het moment dat de magazijnmedewerkers effectief klaar zijn om de goederen te ontvangen.
E. Vandenbussche: “Een goed statusbeheer is daarbij heel belangrijk. Het gebruik van ASN’s (advanced shipping notes) en ‘slotting’ is in die context erg zinvol. Zo kun je tijdig de nodige voorbereidingen in je magazijn treffen om de goederen efficiënt te ontvangen en weg te zetten. Bovendien moesten we er rekening mee houden dat er vaak nog heel wat extra zaken moeten gebeuren, zoals het reinigen en de inspectie van de vrachtwagens. Het is efficiënter om die zaken niet aan de kade zelf te doen.”
Met het oog op een nieuwe lay-out werden de verschillende scenario’s tegen elkaar afgezet, op basis van hun efficiëntie en de operationele kosten. Uiteindelijk werd besloten een nieuwe lay-out te ontwerpen in functie van het dock & yard management. Er werd bijvoorbeeld gekozen voor beheer via een centrale wachtparking, veilige operaties met gedefinieerde docks en laad- en loszones en zo weinig mogelijk kruisende stromen.
D. Van Craenenbroeck: “In de nieuwe lay-out is verder gezorgd voor een magazijn met een meer logische structuur, in combinatie met betere toewijzing van onze goederen aan de verschillende zones via ABC-allocatie. Producten die diep in het magazijn gelokaliseerd zijn, ontkoppelen we nu van het laden en lossen via een ‘staging in’ en ‘staging out’ zone. Ook voor het inspecteren van pallets – waarbij we elke pallet individueel moeten kunnen bekijken – zijn dergelijke zones interessant. Verder zijn we de beschikbare hoogte beter gaan benutten door niet enkel meer bulkopslag, maar ook opslag in rekken te voorzien. Bovendien werden bepaalde activiteiten en resources gecentraliseerd, bijvoorbeeld voor de producten die na het binnenkomen nog een bewerking moeten krijgen.”
Bij het opzetten van alle taaksturing binnen de nieuwe lay-out, speelt het WMS uiteraard een belangrijke rol. “Het WMS maakte bovendien dubbelspelen en andere efficiëntieslagen mogelijk, wat de reistijden flink heeft verkort”, klinkt het. “De introductie van RF-scanners (radio frequency) maakt bovendien een real-time aansturing mogelijk en heeft ons ook van heel wat papierwerk verlost.”
Zo’n verbeteringstraject mag misschien vanzelfsprekend lijken, toch is het volgens David Craenenbroeck niet te onderschatten: “Het was een zeer intensieve oefening. Je mag ook niet vergeten dat het magazijn hier nokvol stond. Praktisch gezien vormde het een grote uitdaging om de site te reorganiseren én intussen de operaties draaiende te houden. Je stapt over van papier naar scanners, de medewerkers moeten mee zijn in het verhaal, ... We hebben dan ook voor een gefaseerde implementatie gekozen, waarbij we de klanten een voor een in de nieuwe manier van werken integreren.”
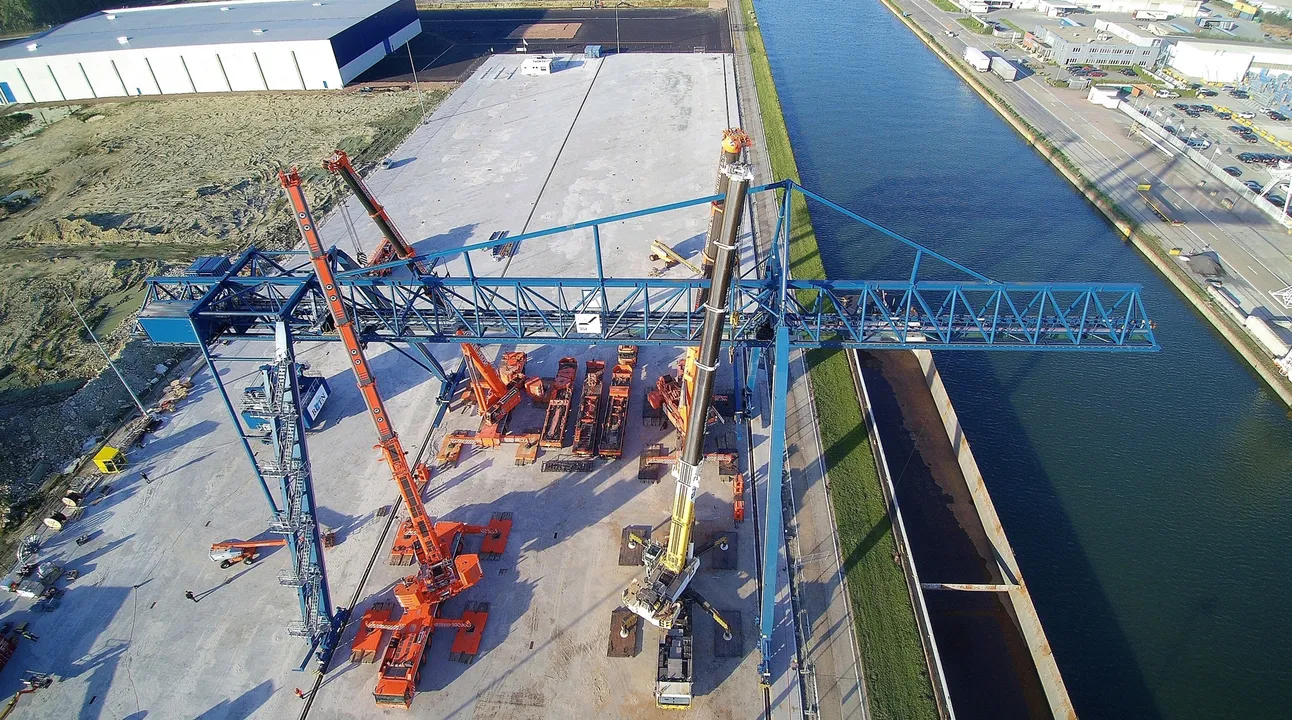
Nieuwe site, zelfde filosofie
De verregaande reorganisatie verhinderde Gheys Logistics evenwel niet intussen nog andere stappen te zetten om de structurele groei op te vangen.
D. Van Craenenbroeck: “Om de containers tussen de haven van Antwerpen en Mol op te vangen, hebben we al sinds 2001 een eigen containerterminal. Een paar jaar geleden merkten we dat de capaciteit van die terminal verzadigd raakte, wat met de groeiende volumes problematisch kon worden. Sinds vorig jaar doen we daarom een beroep op de directe waterverbinding tussen de haven van Antwerpen en Beringen, dat langs het Albertkanaal ligt. Met barges worden er containers aan- en afgevoerd via de terminal van operator BCTN, die een langdurig gebruiksrecht heeft op het terrein van 20.000m² dat we een zestal jaar geleden van Dow Chemicals hebben overgenomen. Die nieuwe terminal heeft een capaciteit van meer dan 50.000 containers. Dat geeft ons meteen een ruime marge voor de toekomst en zorgt ervoor dat we nog meer vrachtwagens van de weg af kunnen halen.”
Voor het ontwerp van de nieuwe terminalsite, riep Gheys Logistics opnieuw de hulp van Logflow in. “Dat Gheys Logistics er op die manier een flinke oppervlakte bij kreeg, is uiteraard meegenomen. Maar tijdens ons eerste project samen is ook bij de organisatie het besef gegroeid dat we zuinig met de beschikbare ruimte moeten omspringen en daarom voor de opslag beter de hoogte in kunnen gaan. Met de groei in het achterhoofd, konden we zo vermijden dat er binnen afzienbare tijd weer plaats te kort was”, vertelt Eric Vandenbussche.
De ontwikkeling van deze nieuwe, duurzame site bracht weliswaar een aantal extra uitdagingen met zich mee. Zo staan er twee windmolens op de site, was er centraal op het terrein een stikstofleiding aanwezig en uiteraard moest de containerterminal zelf ter hoogte van het kanaal komen. Een weloverwogen inplanting van alle infrastructuur was dan ook cruciaal.
Omdat Gheys Logistics niet om de stikstofleiding heen kon, werd besloten op die plaats een weg aan te leggen. Daarrond werd de rest van de infrastructuur ingeplant. Op die manier zal de leiding nooit in de weg komen te liggen naarmate de site geleidelijk groeit.
E. Vandenbussche: “De nieuwe site aan het kanaal bevindt zich aan de overzijde van de openbare weg, waardoor een terminal A en een terminal B ontstaat, met elk hun magazijnruimtes, die zich aan weerszijden van de openbare weg bevinden. Het zijn bijkomende uitdagingen om de traceerbaarheid te blijven garanderen wanneer je met goederen op de openbare weg komt, om de goederen zoveel mogelijk op de juiste plaats op te slaan en om een goed dock & yard management te garanderen.”
Aangezien Gheys Logistics als logistiek dienstverlener heel flexibel moet blijven, werd ook op de nieuwe site niet voor een volautomatische oplossing gekozen.
D. Van Craenenbroeck: “Over dat punt hebben we lange gesprekken gevoerd, maar een geautomatiseerd hoogbouwmagazijn zou voor ons momenteel ook mentaal een brug te ver geweest zijn. We hebben in eerste instantie gekozen voor een semi-manueel magazijn, met de mogelijkheid om in de toekomst alsnog een hoogbouwmagazijn te kunnen plaatsen. Daarnaast hebben we gevraagd om in het masterplan ook rekening te houden met eventuele productieactiviteiten in de toekomst.”
De semi-automatisering bestaat uit een smallegangenmagazijn van 70 op 140 meter, met een hoogte van 11,5 meter. In dit magazijn kunnen 15.000 pallets met chemische goederen worden opgeslagen. De aan- en afvoer van de pallets naar de combitrucks werd geautomatiseerd, waardoor rijtijden van de combitrucks verminderen via dubbelspel. Binnen de multidiepe opslagkanalen gebeurt de goederenbehandeling met behulp van vier Atlas-palletshuttles van Stow. Elke combitruck werkt samen met twee shuttles om de in- en uitslag binnen de multidiepe kanalen te realiseren. Door ‘slave pallets’ te gebruiken, is het bovendien mogelijk om verschillende types pallets vlot te behandelen en de kwaliteit van de pallets te ondervangen, wat heel belangrijk is voor automatisering binnen een dienstverleningsomgeving. Ook hier speelt het WMS opnieuw een cruciale rol, zowel om de dubbelspelen op te zetten en de rijafstanden te minimaliseren, als om de vullingsgraad te verhogen met verschuivingsalgoritmes.
“Ook op deze site kiezen we resoluut voor een stapsgewijze aanpak, waarbij we eerst de 10.000 vierkante meter hal 1 met het semi-automatische warehouseconcept zijn gaan ontwikkelen. Het heeft toch anderhalf jaar geduurd voordat de terminal en de eerste hal live waren. Dit jaar nog plannen we de bouw van een volgend magazijn van 12.500 vierkante meter. Net zoals op de bestaande site in Beringen, vertrouwen we erop dat die doordachte en gefaseerde aanpak via het masterplan ook hier op lange termijn de beste oplossing zal bieden”, besluit David Van Craenenbroeck.
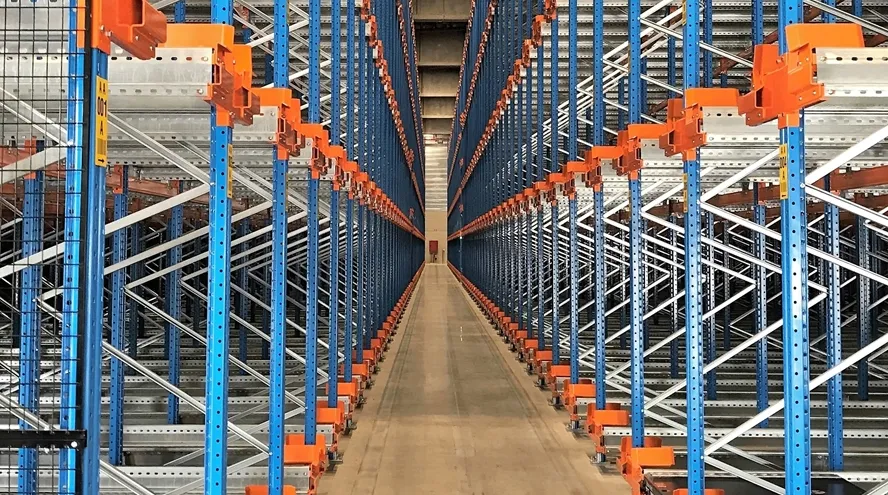