Kwantumsprong door vergaande automatisering
Ecoline investeert fors in volautomatisch magazijn en IT-integratie
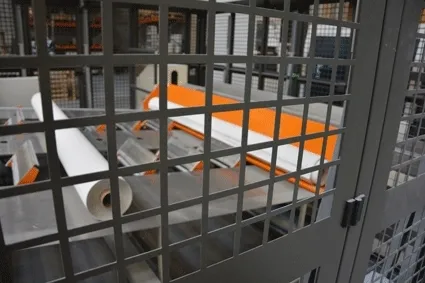
Als kleine kmo realiseerde Ecoline een groots logistiek automatiseringsproject: de bouw van een hoogbouwmagazijn met wisselrijdende kraan en de integratie van de productie- en magazijnbewegingen via een WMS- en MES-implementatie. Aan de basis van het project liggen gunstige investeringskansen, maar ook plaatsgebrek en een familiale langetermijnvisie. De West-Vlaamse producent doet het verhaal uit de doeken, samen met zijn projectpartners: Egemin Automation, Logflow en Objective International.
Ecoline is al 25 jaar actief in de wereld van non-woven poetsdoeken, poetspapier en traditionele poetslappen. Het bedrijf produceert met 35 medewerkers – naast de maatproductie – meer dan 300 verschillende referenties die naar meer dan 20 landen worden verzonden. Dat gaat van producten op rol tot vlakke doeken en speciaal gevouwen poetsartikelen. De organisatie maakt voornamelijk private-labelproducten voor de industrie en groothandel, maar heeft ook een eigen B-merk.
Het automatiseringsverhaal gaat terug tot 2008. Ecoline had toen 13.000m2 oppervlakte aan bedrijfsterreinen, maar werd in zijn groei geremd door plaatsgebrek. De aankoop van het laatste braakliggend stuk grond naast het bedrijf bood perspectief. Weliswaar stelde het management zich de vraag hoe het de extra oppervlakte het beste kon benutten. “We hadden al vier keer gebouwd op de site in Wevelgem. Indien we terug voor de klassieke vorm van warehousing kozen, zouden we hoogstens tien jaar verder kunnen. Dat staat haaks op de langetermijnvisie die we als familiaal bedrijf hanteren. Bovendien waren we op dat moment in onze familiegroep overgekapitaliseerd. Mede door de economische crisis was het aanlokkelijker om ons geld te investeren dan op de bank te laten staan. De combinatie van die verschillende elementen was voor ons belangrijker dan een zwart-op-wit bewezen Return On Investment (ROI). Mochten we ons enkel daarop hebben gebaseerd, dan stond er vandaag geen hoogbouwmagazijn”, weet Christophe Vanneste, CIO van Ecoline.
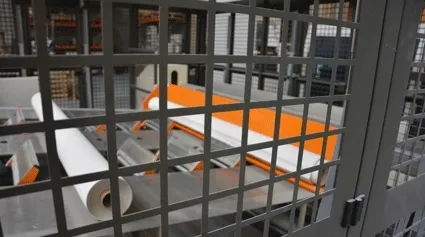
In de hoogte
In 2010 legde het management de eerste contacten met Egemin Automation, gespecialiseerd in magazijnautomatisering. Aanvankelijk werd enkel gekeken naar de bouw van een hoogbouwmagazijn, maar omdat Ecoline ook op zoek was naar een oplossing om vrachten klaar te zetten en pallets uit de productie te halen, werden ook AGV’s (Automatisch Geleide Voertuigen) in de opzet betrokken.
Het hoogbouwmagazijn is 26 meter hoog en telt zes gangen met 16.000 palletplaatsen waar dubbeldiep gestockeerd kan worden. In het hoogbouwmagazijn rijdt een wisselrijdende kraan. “Op zich is een wisselrijdende kraan vrij traag. Daarom deelden we het hoogbouwmagazijn op in een bufferzone en een stockagezone. ’s Nachts zet de kraan de producten klaar voor de volgende dag in de bufferzone, zodat de kraan overdag niet telkens helemaal naar achteren in het magazijn hoeft te rijden. Daardoor kan de kraan overdag wel erg snel en efficiënt pallets aan- en afvoeren”, legt Henk Deloof, Commercial Manager Benelux bij Egemin, uit.
Aansluitend aan het hoogbouwmagazijn is ook een klaarzetzone met rollenbandjes. Op de goods-to-man pickingpost krijgen medewerkers pallets voor zich, picken ze een aantal dozen en als ze deze afmelden wordt de pallet automatisch terug het magazijn in geplaatst.
Ecoline werkt met een zelfsturend team van vijf techniekers en investeerde daarnaast in reserveonderdelen van de wisselrijdende kraan. “Afgezien van de mast, heb ik ongeveer een tweede kraan staan. Ik heb geen klanten met grote boeteclausules, maar een defect in het hoogbouwmagazijn zou een enorme impact hebben op onze organisatie. Egemin werkt sterk op preventief onderhoud. Voor elk slijtagedeel hebben ze een vooropgestelde levensduur. Mocht er bijvoorbeeld toch slijtage zijn op een wiel, dan zorgt dat niet voor foutieve positioneringen omdat de kraan op de x-as de juiste locatie vindt op basis van barcodes. Op de y-as is er ook nog eens liggercontrole. De kraan heft steeds tot tien centimeter boven de ligger. Klopt dit niet, dan geeft de kraan een alarm. Daarnaast is de z-as eveneens beveiligd: de kraan zit vol sensoren die onder meer nagaan of de pallet exact in het midden van de positie staat”, aldus Christophe Vanneste.
Het hoogbouwmagazijn is operationeel sinds april 2014. Ecoline zag het foutenpercentage drastisch verminderen door deze investering.
Christophe Vanneste: “Wij hebben geen verloren pallets meer. We weten steeds exact wat waar staat. De enige foutmeldingen die we krijgen, zijn de veiligheidsmeldingen. Als er bijvoorbeeld wat inpakfolie over is en de kraan maakt snelheid in de gang, dan kan het zijn dat de folie voor de kruislingse detectiesensoren waait en de kraan in veiligheid gaat, omdat het systeem denkt dat er een verlies van lading is.”
Het hoogbouwmagazijn wordt aangestuurd door Egemins Warehouse Control System (WCS). In de projectfase liep het vast op de integratie tussen het WCS en het ERP. Bij de gesprekken over de verantwoordelijkheden van de verschillende partijen werd niet dezelfde mening gedeeld. Christophe Vanneste besloot om een externe partij aan te trekken, namelijk Logflow, als neutrale scheidsrechter.
Bredere scope
Logflow moest in eerste instantie advies geven over de beste WMS-leverancier voor Ecoline, maar raadde het management ook aan om vooraleer van wal te steken, eerst een stapje terug te zetten. “Logflow wees ons er op dat de bouw van een hoogbouwmagazijn een unieke gelegenheid is om alle stromen in het bedrijf onder de loep te nemen. Wij wilden bovendien een automatisch magazijnproces koppelen aan manuele operaties. Dat wil zeggen dat er een goede synchronisatie moet zijn van de bewegingen en je lay-out daarop moet voorbereid zijn. Dat is ook wat ik vandaag anders zou doen, mocht ik herbeginnen. Ik zou eerst een logistieke analyse laten uitvoeren om daarna pas te spreken over de uitwerking en automatisatie. Alles is uiteindelijk op zijn pootjes terechtgekomen, omdat elke partij het spel fair heeft gespeeld, maar het is toch beter om eerst over verantwoordelijkheden te spreken en dan pas contracten te tekenen”, lacht Christophe Vanneste.
Eric Vandenbussche, Managing Director van Logflow, volgde Egemin op het vlak van het nemen van verantwoordelijkheid: “De leverancier van de hoogbouw kent zijn kranen en de reactiviteit van zijn systeem. Daarvoor moet die partij ook zijn verantwoordelijkheid kunnen nemen. Als het WMS aangeeft dat bepaalde producten nodig zijn, dan moet het WCS toch zelf beslissingen kunnen nemen over wanneer welke goederen gehaald worden.”
Uit de studies van Logflow bleek dat Ecoline naast een WMS-omgeving ook behoefte had aan een MES-oplossing. Daarop schoof Logflow Objective International naar voren als IT-partner, omdat deze softwareleverancier beide oplossingen aanbiedt.
Met het WMS bouwt Ecoline een brug tussen het ERP-systeem en het automatische magazijn. Daarbij wordt extra aandacht besteed aan het behoud van de flexibiliteit van de operaties, met name voor het leveren van kleine volumes met zeer korte levertermijnen. De MES-oplossing zorgt voor de integratie van de productiestromen, zoals de aanvoer van verpakkingen naar de productievloer of de afvoer van producten naar het hoogbouwmagazijn. Daarbij wordt ook de kostprijscalculatie door Objective MES ondersteund, net als de extra waardetoevoegende activiteiten zoals labeling. “De combinatie van WMS en MES leidt tot een volledige traceerbaarheid op alle niveaus: van grondstoffen tot afgewerkte producten”, zegt Koen De Clercq, CEO van Objective International.
De ERP-oplossing blijft wel de master van de data, omdat Ecoline er de voorkeur aan geeft zoveel mogelijk data op dezelfde plaats te beheren. Bij de allocatie van een productieorder worden de routing en de bill of material meegegeven vanuit de ERP-oplossing aan Objective.
Op de werkvloer
Ecoline werkt volledig systeemgestuurd. De supervisor bereidt de pickingstrategieën voor. Eens deze gekend zijn, worden alle taken die binnenkomen automatisch verstuurd en naar de desbetreffende medewerkers of automatische systemen gedelegeerd.
C. Vanneste: “Het is natuurlijk wel mogelijk om in te grijpen door bepaalde taken een andere prioriteit mee te geven, maar op zich is er geen tussenkomst meer nodig. Op de werkvloer staan een aantal touchscreens, zodat onze medewerkers detailinformatie kunnen opvragen. Vandaag staat er nog vrij veel informatie op de schermen. Dat komt omdat we alle informatie die op de geprinte productiebon aanwezig was, overgenomen hebben op het scherm. Op die manier wilden we de overgang voor onze medewerkers minder bruusk maken. De omschakeling is vlot verlopen. Alleen het badgen om zich als werknemer te linken aan een machine wordt nog af en toe vergeten.”
Via de touchscreens kunnen productiemedewerkers indien nodig ook extra voorraad aanvragen. “Daarnaast vragen de productiemedewerkers zelf de moederrol aan. Objective reserveert wel enkele moederrollen voor de productie, maar de operator duwt op de knop om dit te bevestigen. We hebben gekozen om hier toch nog een stukje manueel te werken, omdat bij een verkeerde planning de productievloer anders vol zou staan met volumineuze moederrollen. Ook technische breuken of andere problemen kunnen we niet op voorhand voorspellen. Het is wel zo dat de orders die nog niet actief zijn, al klaar staan in de bufferzone van het hoogbouwmagazijn”, zegt Christophe Vanneste.
Tussen de moederrollen is het soms moeilijk om visueel het verschil op te merken. In de productie hangen gele bordjes op, die net als de moederrol gescand moeten worden wanneer een rol wordt aangebracht. “Vroeger merkten we soms pas na de productie van vijf pallets op dat we de verkeerde grondstof hadden ingelegd. Zulke fouten gebeuren vandaag niet meer. We konden de materiaalfouten met 100% reduceren. Dat zorgt voor veel minder kwaliteitsproblemen achteraf”, aldus Christophe Vanneste.
Fabriek van de toekomst
Een groot pluspunt van de grootse automatiseringsslag is de rust op de werkvloer. “De AGV’s brengen de voorraad aan die op dat moment nodig is, in plaats van voorraad voor dagen ver klaar te zetten. Dat zorgt letterlijk voor ademruimte op de productievloer. Daarnaast draagt ook de visibiliteit van poort-tot-poort bij tot een betere organisatie”, zegt Christophe Vanneste.
Door voldoende opslag te garanderen via een automatisch magazijn met mobiele kraan en in te zetten op efficiënte stromen tussen goederenontvangst, productie, magazijn, picking en verzending maakte Ecoline een grote stap richting ‘fabriek van de toekomst’. De volgende jaren zou het management nog kunnen investeren in een betere datacaptatie van de machines, maar eerst en vooral wil Christophe Vanneste focussen op het commerciële apparaat. “We hebben nu het kader gecreëerd om groei te kunnen opvangen, dus is het ook de bedoeling dat onze omzet de volgende jaren significant toeneemt."