Klaar voor groeiende e-commerce
Westvlees kan tot de helft sneller leveren dankzij automatisering
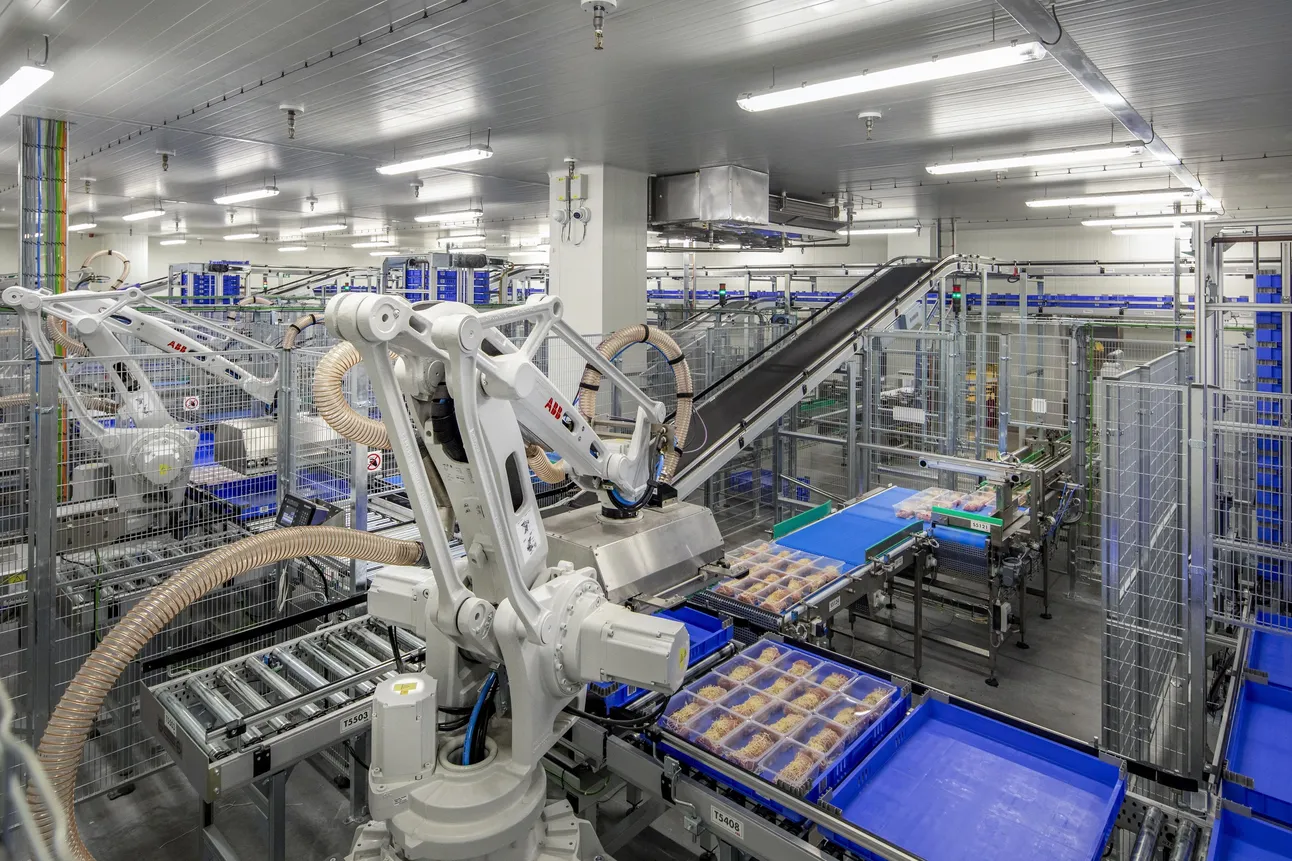
Ondanks haar eerder conservatieve imago is ook de vleesverwerkende industrie vandaag volop in beweging. Daar zitten de veranderende consumentengewoonten voor veel tussen. Zo stelt het vleesverwerkende bedrijf Westvlees uit Westrozebeke vast dat de verkoop van voorverpakt vlees duidelijk in de lift zit. Om zijn klanten en retailers beter te kunnen bedienen, nam het bedrijf technologiepartner ABB Robotics in de arm om de interne logistiek te helpen optimaliseren.
Westvlees is een van de acht vleesverwerkende bedrijven, elk met zijn eigen specialiteit, die samen Belgian Pork Group (BPG) vormen. De groep, die ruim een derde (35%) van de Belgische markt voor vers en bereid varkensvlees inneemt, staat ook Europees in de top tien. Wereldwijd exporteert de groep in totaal naar meer dan vijftig landen. Sinds 2012 breidt Westvlees zijn activiteiten ook uit naar de Aziatische markt. Zo mocht het als eerste Belgische producent varkensvlees aan China leveren.
De ongeveer 1600 medewerkers van Belgian Pork Group verwerken jaarlijks meer dan 3,8 miljoen varkens, afkomstig van een 800-tal familiale varkenshouders, tot bijna 3000 verse producten. Alle groepsactiviteiten samen zijn goed voor een omzet van bijna 800 miljoen euro. Met CEO Jos Claeys staat intussen al de vierde generatie aan het roer van het snelgroeiende familiebedrijf.
Snelheid maakt het verschil
De acht productiesites van Belgian Pork Group liggen over heel België verspreid. “Daar is een goede reden voor”, aldus Manuel Goderis, productmanager bij Westvlees. “Wij leveren ultraverse producten met een beperkte houdbaarheid, tot zeven dagen om precies te zijn. Criteria als snelheid en, daaraan gelinkt, nabijheid maken dan echt het verschil. Dan heb ik het over nabijheid tot de klant, in ons geval de retailer, die wij snel moeten kunnen beleveren. Maar ook over nabijheid tot de eigen leveranciers, in ons geval de varkenshouders, die op hun beurt vlot tot bij ons moeten kunnen geraken.”
De hoofdzetel van Belgian Pork Group bevindt zich in het West-Vlaamse Westrozebeke. Daar is ook de productiesite van Westvlees gevestigd, waar 850 medewerkers jaarlijks 1,4 miljoen varkens verwerken tot ruim 140.000 ton varkensvlees. Zij verwerken er niet alleen verse tot panklare gerechten, maar vriezen ze ook in, verpakken ze en etiketteren ze op maat van de klanten. Die klanten zijn afkomstig uit meer dan vijftig landen en voornamelijk actief in de distributie, groothandel en aankoopcentrales, maar ook in de kleinhandel, horeca en cateringsector.
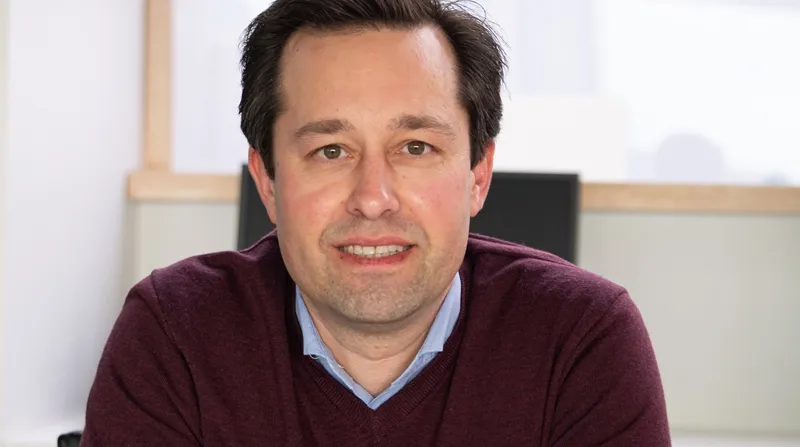
Sector in beweging
“Onze sector is volop in beweging”, stelt Manuel Goderis vast. Niet alleen neemt het aantal slagers jaar na jaar verder af, de consument van vandaag houdt er ook nieuwe koopgewoonten op na en stelt meer of andere eisen. Naast het traditionele slagerskanaal, waarop Westvlees overigens heel hard blijft inzetten, wint het kanaal van de grote retailers, zoals de supermarkten, steeds sterker aan belang. En daar zetten voorverpakte producten overduidelijk de toon. Daarbij gaat het om producten met een verschillende bewaartermijn, een verschillend gewicht, in verschillende verpakkingstypes en -vormen en, last but not least, voorzien van een verschillend etiket. “Voor alle duidelijkheid: wij zijn een privatelabelbedrijf”, merkt Manuel Goderis op. “Dat betekent dat wij voor elk product ook andere labels nodig hebben, in functie van de klant. Ook de prijs van het product kan trouwens verschillen van klant tot klant en zelfs van locatie tot locatie. Wij moeten daarin heel flexibel zijn.”
“Mijn collega’s en ik zijn steevast jaloers op die typische blikjes cola die heel lang houdbaar zijn, stuk voor stuk dezelfde vorm hebben en allemaal ook evenveel wegen”, vervolgt de productmanager. “Logistiek zijn die heel eenvoudig te behandelen. Bij ons daarentegen kunnen al die parameters variëren. En dat voor een bijzonder breed gamma van bijna drieduizend producten. Dat maakt het een extra grote uitdaging om die allemaal ultravers tot bij onze klanten te krijgen, verwerkt op maat van hun specifieke wensen en voorzien van het juiste etiket.”
Trends en uitdagingen
Naast de toenemende vraag naar personalisatie en de wijziging in het consumptiegedrag, die een sterke groei van de voorverpakkingsactiviteit met zich meebracht, noteert Manuel Goderis nog een paar andere belangrijke markttrends. Mede als gevolg van de coronacrisis kende de e-commerce de afgelopen jaren een opvallende groei, ook in de sector van de verse voeding. Deels wellicht onder invloed van die trend worden ook de bestel- en levertermijnen steeds korter. “Winkels willen zo laat mogelijk bestellen omdat ze dan weten wat ze die dag precies verkocht hebben, om dan liefst de volgende ochtend al beleverd te worden”, klinkt het.
Tegelijk ziet Westvlees zich geconfronteerd met een heel aantal uitdagingen: nieuwe maar ook oude vertrouwde, zoals de loonkosten.
Manuel Goderis: “Ook de juiste profielen vinden, blijft een uitdaging. We hebben meer en meer mensen nodig, maar we opereren vanuit Westrozebeke, in een streek met de laagste werkloosheidsgraad van België. Hier in de regio zijn veel groentebedrijven actief die, net als wij, heel wat handen nodig hebben. Het is dus echt een uitdaging om de juiste mensen te vinden.”
“Capaciteitsgebrek begon ook stilaan een probleem te vormen”, vervolgt Manuel Goderis. “Je bent aan het groeien en dan merk je dat je binnen je bestaande organisatie of productie-eenheid af en toe toch wel tegen de grenzen van je totale beschikbare capaciteit aanbotst.” Tegelijkertijd stelden hij en zijn collega’s ook een aantal inefficiënties vast. “Door de manier waarop we georganiseerd waren, waren niet al onze machines de hele tijd bezet. Maar we konden niet anders, want we waren nu eenmaal zo georganiseerd.”
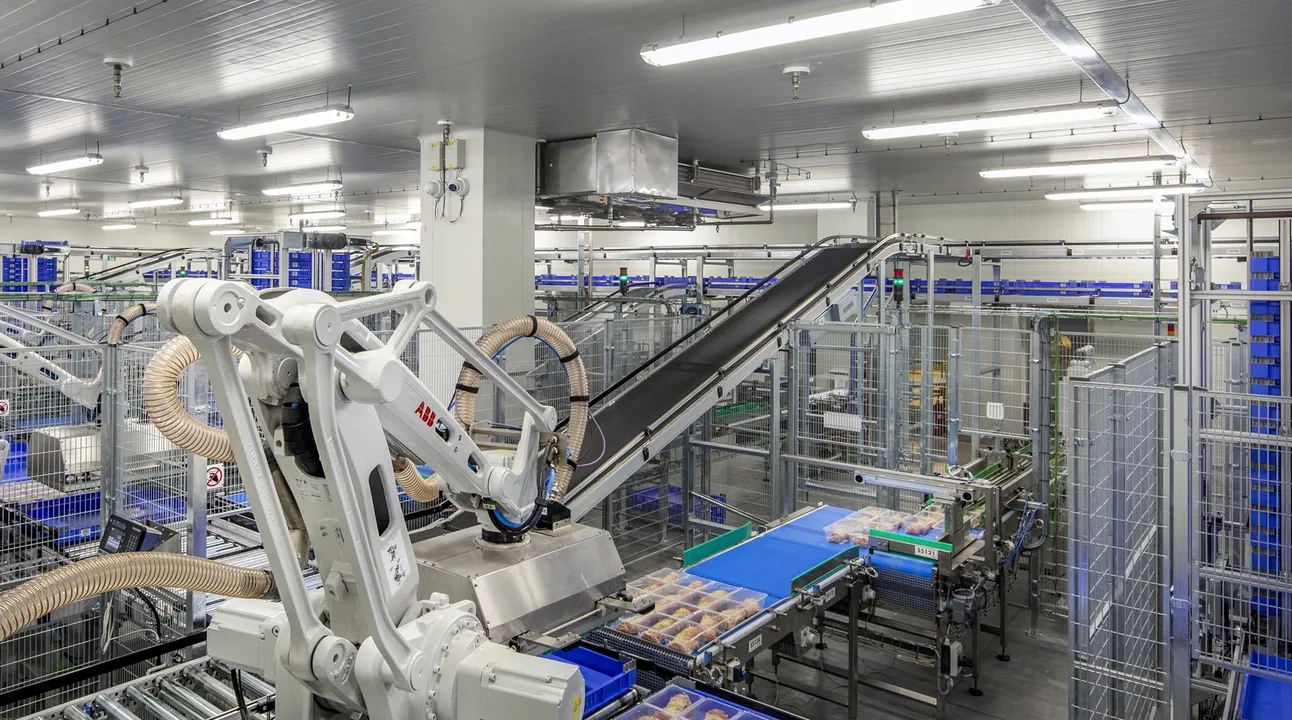
Kanteljaar 2019
Op een gegeven moment drongen er zich ook een aantal vervangingsinvesteringen op.
M. Goderis: “We zijn in de jaren tachtig al begonnen met voorverpakking. Een aantal gebouwen en machines uit die periode waren intussen echt wel aan vervanging toe. En dan kom je op een kantelpunt en kies je welke richting je verder uitgaat. Ga je fundamentele investeringen doen om die oude toestellen te vervangen? Of investeer je in een totaal nieuw concept?”
Westvlees koos voor dat laatste en besloot in 2019 een grondige vernieuwingsoperatie op te zetten. De nieuwbouw in de voorverpakking moest ervoor zorgen dat het bedrijf zich anders kon gaan organiseren.
M. Goderis: “In de loop van de jaren hadden we al wel een en ander geautomatiseerd, maar met de hulp van technologiepartner ABB Robotics wilden we nog sterker kunnen inzetten op automatisering. Tegelijk wensten we vandaag én morgen te kunnen voldoen aan allerlei nieuwe vragen en behoeften in de markt.”
Logistiek proces opsplitsen
“Vroeger werkten wij heel efficiënt, want in lijn”, herinnert de productmanager zich. “Als een worst of brochette eenmaal was geproduceerd, werd het product manueel op een schaal gelegd (in tray). Vervolgens werd het onder beschermende atmosfeer verpakt (MAP sealing: ‘modified atmosphere packaging’), waarna het etiket erop werd aangebracht (‘labeling’). Ten slotte werd het gasverpakte, gelabelde product manueel in een drager gelegd, meestal een EPS-krat (in carrier).”
Die manier van werken bood een aantal duidelijke voordelen, waaronder de hoge mate van efficiëntie. Alleen kon het hele proces wel wat tijd in beslag nemen. “Eén schakel bepaalt immers de snelheid van de hele logistieke ketting”, verduidelijkt Manuel Goderis. “Een medewerker kan niet sneller etiketteren dan dat zijn collega’s de producten in de schalen leggen of die schalen verpakken. Qua flexibiliteit liet dat oude productieproces behoorlijk wat te wensen over.”
Vandaag is de logistiek achter dat productieproces in tweeën gesplitst, met een zogenoemde MLS-buffer (multi-layer system buffer) tussen de ‘MAP sealing’ en de ‘labeling zone’ (zie figuur). De productie gebeurt ook niet langer in lijn. “We hebben ervoor gekozen tussen het verpakken en het etiketteren van de producten een aparte, extra schakel in te voegen”, verklaart Manuel Goderis. “Daardoor valt het hele productieproces nu uiteen in twee losse, gescheiden helften die in principe onafhankelijk van elkaar kunnen opereren.”
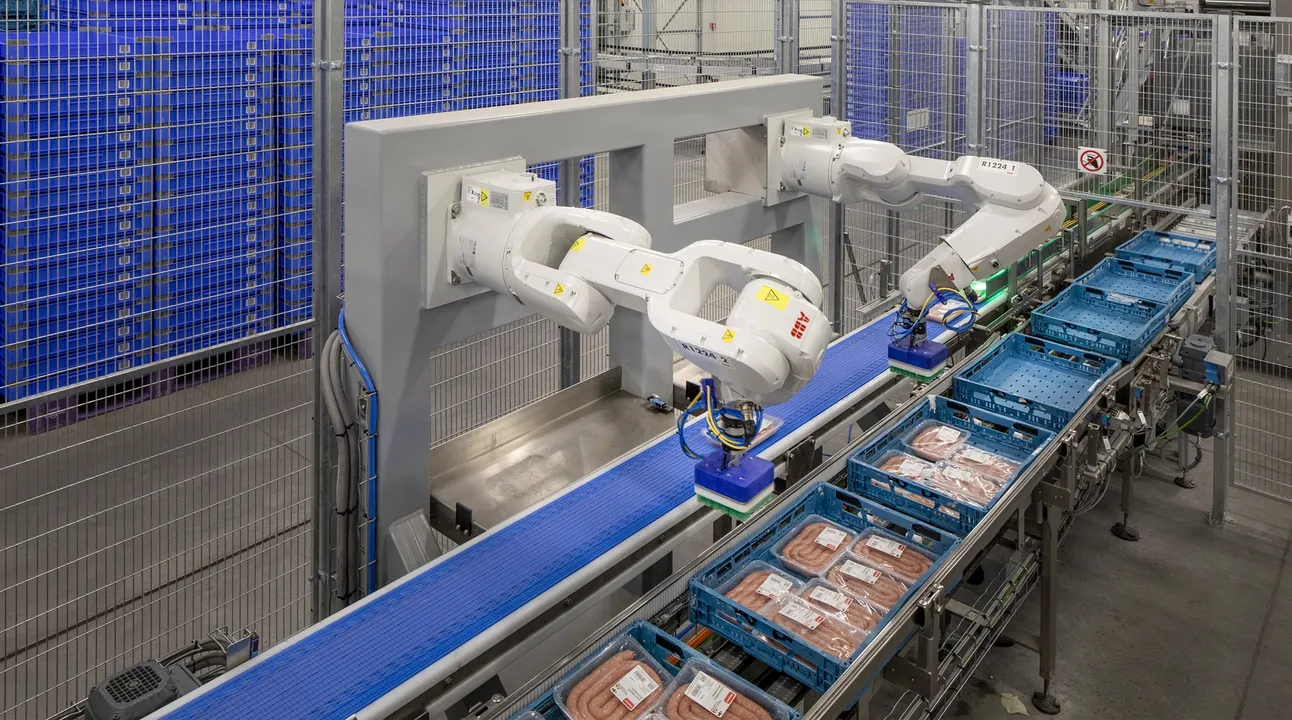
Efficiënt én flexibel produceren
Concreet betekent dit dat de medewerkers van Westvlees ’s morgens vroeg of zelfs ’s nachts al tal van producten kunnen beginnen maken, in schalen leggen en verpakken, maar dat ze zich nog geen zorgen hoeven te maken over de etikettering van diezelfde producten. Als het vlees eenmaal is verpakt, leggen robots de producten automatisch in interne plateaus of tussencarriers en voeren ze vervolgens naar het MLS-buffermagazijn, waar ze voorlopig opgeslagen blijven tot ze naar de etiketteerzone worden afgeroepen. Daar worden ze door robots naartoe gebracht die de producten automatisch opnieuw uit de tussencarriers halen en ze op transportbanden naar de etiketteertoestellen zetten. Eenmaal geëtiketteerd, worden de producten per krat verzameld en via een automatisch liftsysteem naar beneden afgevoerd, waar ze in de expeditieruimte worden gestockeerd, klaar om via de laadkade te vertrekken.
M. Goderis: “Vandaag werken we nog altijd met zeven productielijnen, maar er vindt geen aparte etikettering per lijn meer plaats. We hebben in feite een zone gecreëerd die enkel bestemd is om te etiketteren, om welk type van product of welk formaat van schaal het ook gaat. Dankzij die nieuwe aanpak kunnen we erg efficiënt én flexibel werken en alle schalen die binnenkomen hun juiste bestemming geven. Bovendien kunnen we voortaan veel langer wachten om een bestemming aan een product te geven. Want wat houdt dat in feite in? Een naam, een prijs, een bewaartermijn op een product kleven. Dat gebeurde vroeger direct in lijn, maar doordat ons logistieke proces is opgesplitst, kunnen we die stap in de productie nu uitstellen tot we een order binnenkrijgen. Dan kunnen we ook meteen werk maken van dat etiketteren en het order in kwestie zelfs sneller dan vroeger naar onze klanten uitleveren.”
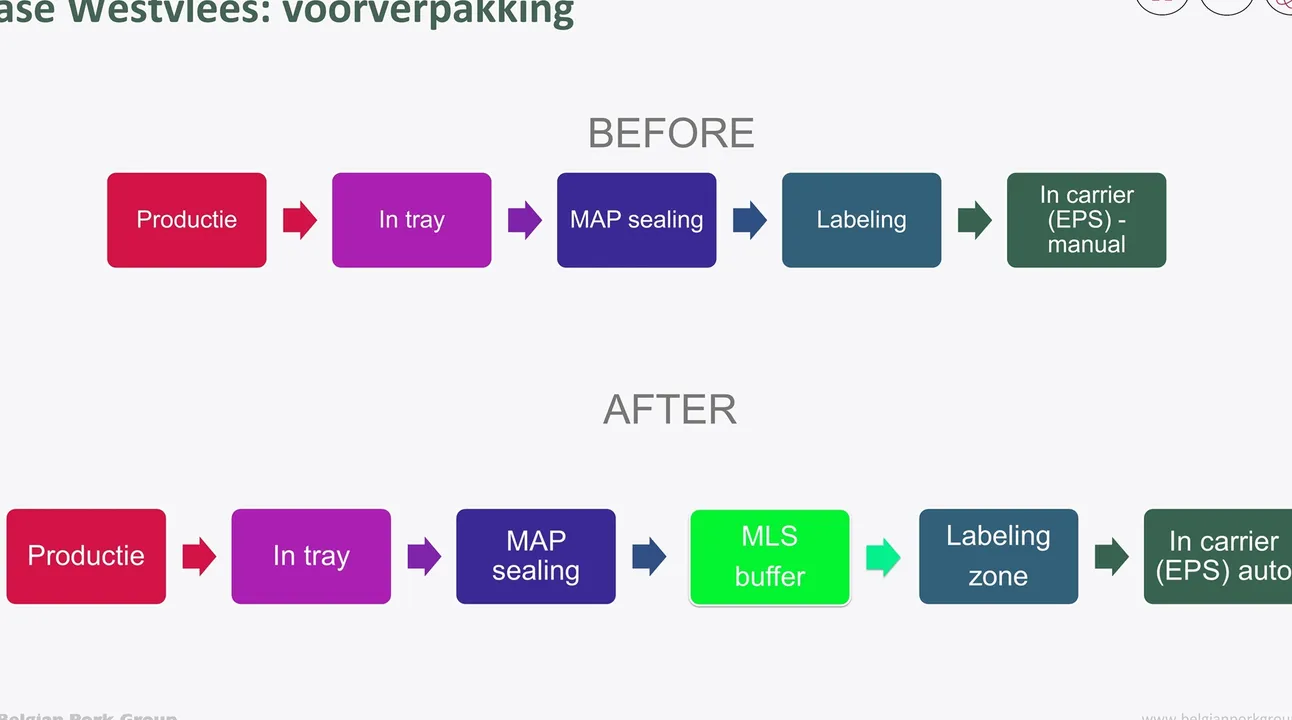
Klaar voor de toekomst
De gerealiseerde procesverbetering bij Westvlees ging gepaard met een doorgedreven automatisering. Daarvoor riep Westvlees de hulp in van ABB, dat gespecialiseerd is in onder meer procesautomatisering en robotisering. “De resultaten van die samenwerking mogen er alvast zijn”, vindt Manuel Goderis. “Zo lag ons servicelevel begin dit jaar net onder de honderd procent. Anders gezegd: wat klanten vandaag bij ons bestellen, raakt zo goed als altijd de volgende ochtend bij hen geleverd.” Daarnaast wist Westvlees de bezettingsgraad van zijn verpakkings- en etiketteertoestellen te verdubbelen. Die laatste kon het bovendien terugbrengen van zeven toestellen – één per productielijn – naar drie toestellen voor de hele etiketteerzone.
“Door de nieuwe manier waarop we ons georganiseerd hebben, zijn we er ook in geslaagd onze totale maximale capaciteit substantieel te verhogen. Een aantal taken of activiteiten die vroeger manueel verliepen, hebben we nu volledig kunnen automatiseren. Daardoor hebben we een achttal medewerkers kunnen vrijmaken voor andere taken. Zij worden vandaag elders in ons bedrijf ingezet. Maar het allerbelangrijkste is toch dat we nu echt wel klaar zijn voor toekomstige ontwikkelingen, zoals een verdere groei van de e-commerce”, besluit Manuel Goderis.
JDP