Genetisch voorbestemd voor duurzaamheid
Gyproc houdt rekening met de toekomstige generatie
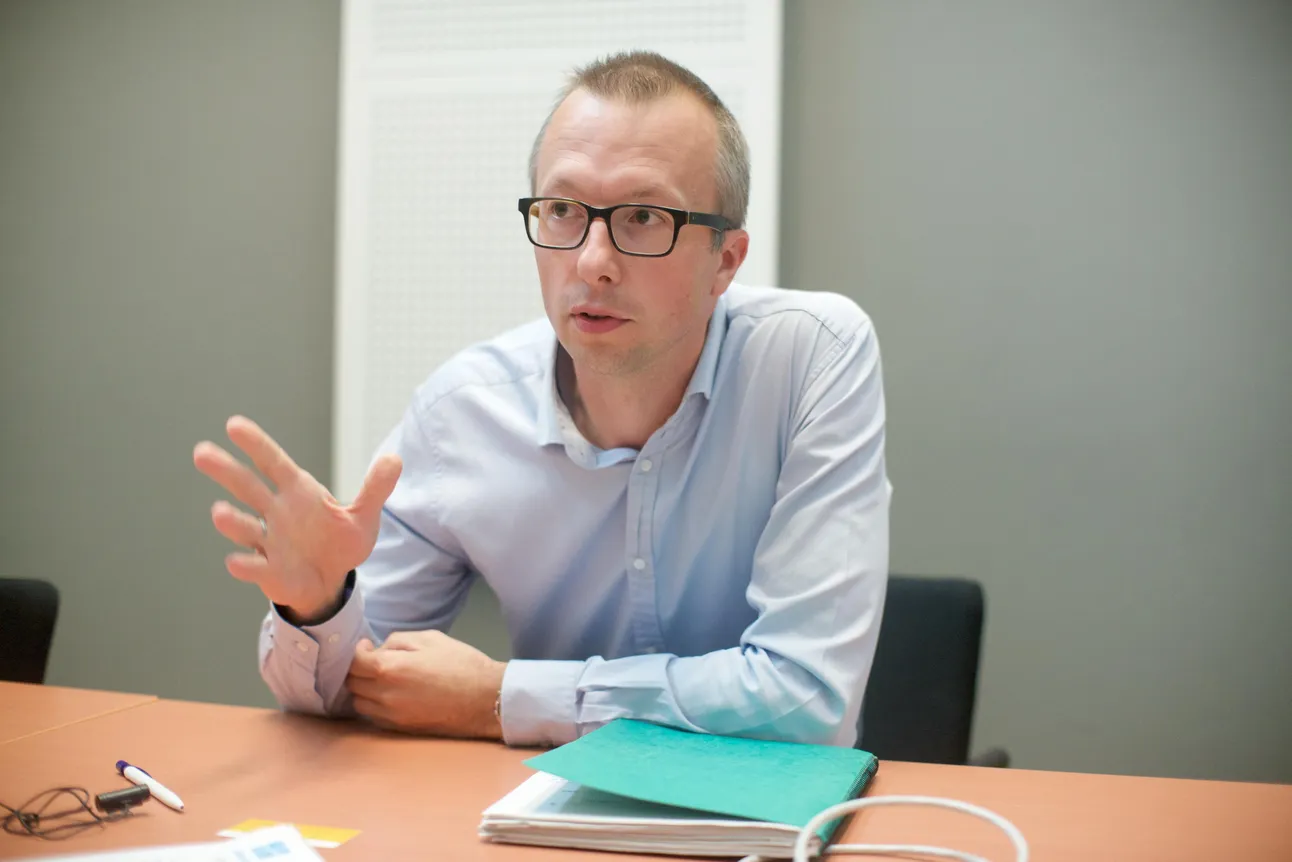
De Wase gipskartonproducent Gyproc, dochter van de Franse bouwgroep Saint-Gobain, trekt sinds enkele jaren de kaart van duurzame onderneming en tracht dat doorheen zijn hele waardeketen te verspreiden. Het bedrijf is een van de weinige met een cradle to cradle (C2C) certificaat en nam in de aanloop daarvan met Tom Rommens een dedicated duurzaamheidsmanager in dienst.
“Duurzaamheid omschrijven wij als een engagement waarbij we door onze huidige manier van leven en consumeren, de kansen van de toekomstige generatie niet compromitteren”, begint Tom Rommens. “Vertaald naar de activiteiten van Gyproc betekent dat: een gezond product in de markt zetten; dat product op een milieuvriendelijke manier produceren; en de maatschappelijke impact van de bijhorende logistiek tot een minimum herleiden”
Een duurzaam product
Een gipskartonplaat is een duurzaam product dat intrinsiek gezond is, aangezien het voor ongeveer 95% is samengesteld uit gips (een natuurlijk product), voor 4% uit gerecycleerd karton en voor 1% uit onschadelijke additieven.
Gips komt als natuurlijk mineraal voor in specifieke geologische afzetting en is in feite een gehydrateerde vorm van de verbinding calciumsulfaat. Het bestaat in een natuurlijke vorm (te vinden in groeven of mijnen) of in een synthetische vorm, als bijproduct van de industrie. De fosfaatindustrie bijvoorbeeld, heeft als reststroom fosfogips met identiek dezelfde samenstelling als natuurgips. Het heeft zelfs een zuiverdere vorm omdat het afkomstig is uit een chemisch proces. Een ander synthetisch gips is de rookgasontzwavelingsgips (RO-gips), een reststroom die vrijkomt bij de ontzwaveling van rookgassen in bijvoorbeeld steenkoolcentrales.
Tom Rommens: “Het is dit RO-gips dat Gyproc België als grondstof gebruikt. In die optiek zou je kunnen stellen dat ons gips driedubbel duurzaam is: het is een neutraal en gezond product, wij recycleren de grondstof van een bijproduct dat ontstaat uit een milieuvriendelijk procedé én we beperken de ontginning van natuurlijke delfstoffen.”
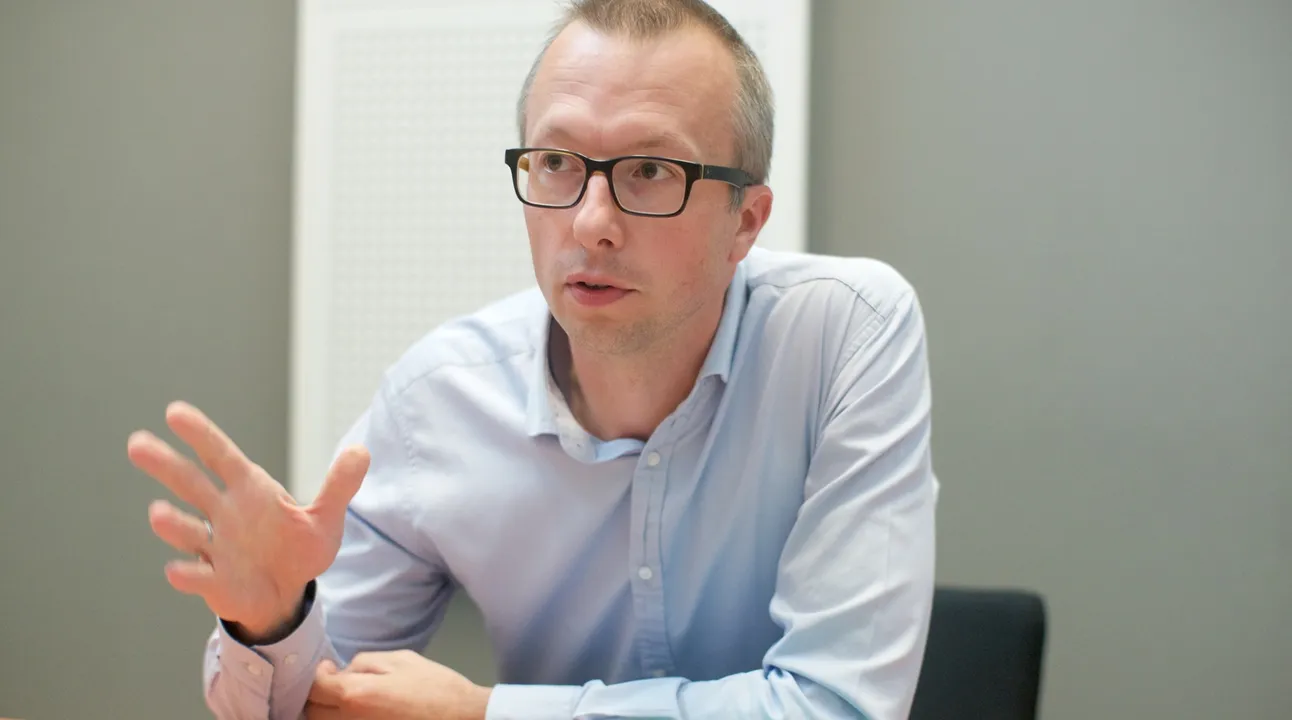
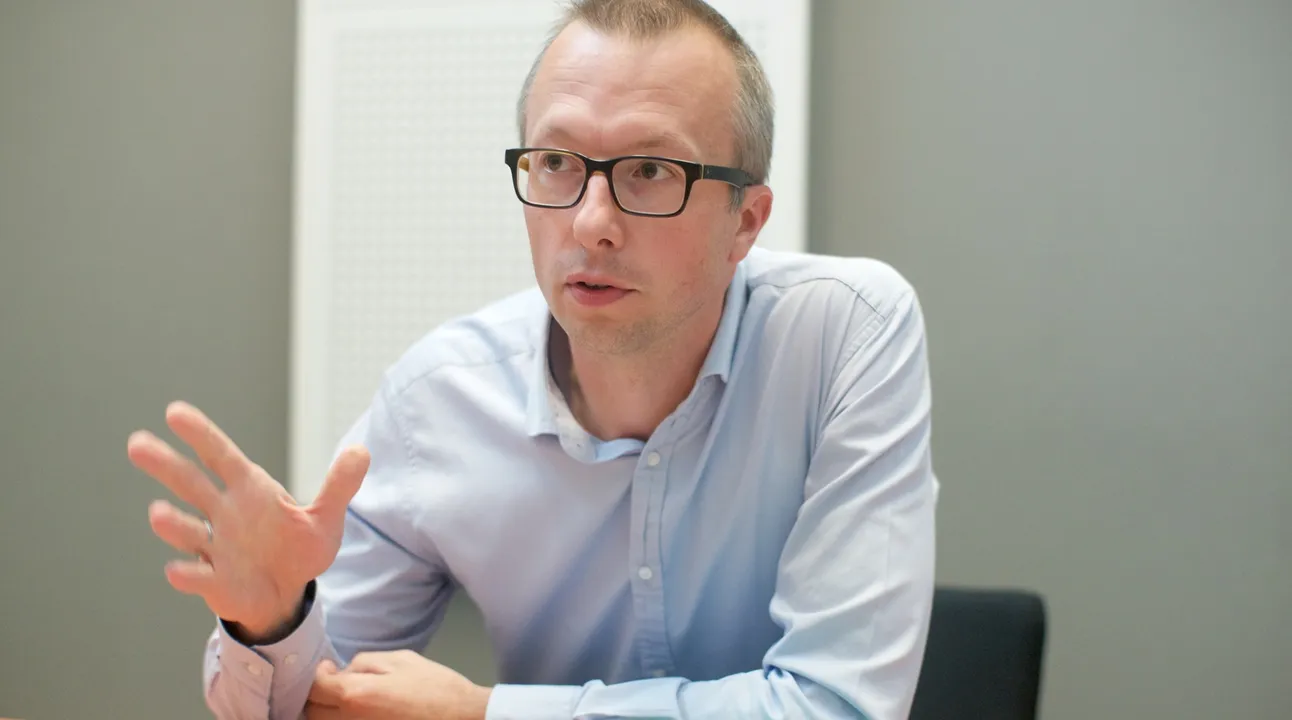
C2C: cradle to cradle
Gyproc was de eerste bouwmaterialenproducent die zijn productgamma liet certificeren: de standaard gipskartonplaat kreeg zijn C2C-certificaat in 2011 en twee jaar later waren alle plaattypes die in Kallo worden geproduceerd, gecertificeerd. Hiermee is de Gyproc-plaat de enige gipskartonplaat ter wereld met een C2C-certificaat.
De kern van de C2C-filosofie is dat een product wordt beoordeeld op zijn volledige levenscyclus. De duurzaamheid van een product hangt dus niet enkel af van zijn samenstelling (zijn alle bestanddelen milieuvriendelijk en duurzaam?), maar ook of ze na hun levensduur op een ecologische manier kunnen worden gerecycleerd, steeds opnieuw. Producten met een C2C-label hebben aangetoond dat ze geen gevaarlijke concentraties toxische stoffen bevatten en daarom zonder enig probleem steeds opnieuw kunnen worden gerecycleerd.
Tom Rommens: “Dat houdt in de eerste plaats in dat je precies weet waaruit je product is samengesteld. Dat is vaak een probleem in de maakindustrie omdat de meeste producenten nooit 100% zeker zijn van de samenstelling van hun grondstoffen, ook al omdat hun leveranciers er niet happig op zijn hun bedrijfsgeheimen prijs te geven. Met andere woorden, vaak weten ze niet of hun product überhaupt een tweede, derde, vierde… leven kan leiden en weten ze ook niet of de onderdelen van hun product op lange termijn de kringloop al dan niet gaan compromitteren. De C2C-filosofie zegt daarover klaar en duidelijk: wanneer je producten ontwikkelt, zorg er dan voor dat je precies weet wat hun samenstelling is zodat ze een oneindig aantal keer kunnen worden hergebruikt zonder schadelijke nevenwerkingen.”
De moeilijkheid van die filosofie (een leverancier die zijn confidentialiteit moet prijsgeven) is tegelijkertijd haar sterkte omdat je op die manier ook een impact hebt op de andere schakels van de supply chain en een stevige bewustmaking creëert in de volledige waardeketen, zowel stroomop- als stroomafwaarts.
Tom Rommens: “Het huiswerk is trouwens niet af al je het certificaat eenmaal hebt behaald. Voor sommige zaken moet je blijven zoeken naar een nog meer ecologisch verantwoord alternatief. Dat is het engagement dat je als C2C-bedrijf opneemt, blijven zoeken naar de manier om je kringloop effectief op een duurzame manier te laten werken.”
Een gezondmakend product
In België is het vooralsnog niet aan de orde, maar in Frankrijk schrijft de wet voor dat bouwmaterialen zo weinig mogelijk vluchtige organische stoffen (VOS) mogen bevatten om de consument te beschermen tegen allerlei uitwasemingen van producten in het binnenmilieu. “Gyproc is daar in elk geval klaar voor”, weet Tom Rommens. “Op zich scoren we al goed met onze niet-schadelijke gipskartonplaat die bovendien de luchtvochtigheid van nature reguleert, maar daarenboven hebben we een plaat ontwikkeld die bepaalde VOS uit de lucht kan capteren en dus de binnenruimte zuivert. Na uitgebreide laboratoriumtests hebben we die gipsplaten ook in 'real-life' getest. Een klaslokaal in de basisschool van Kallo werd uitgerust met onze Active Air-tegels en na vijf maanden was de schadelijke formaldehydeconcentratie in het klaslokaal met meer dan 60% gereduceerd.”
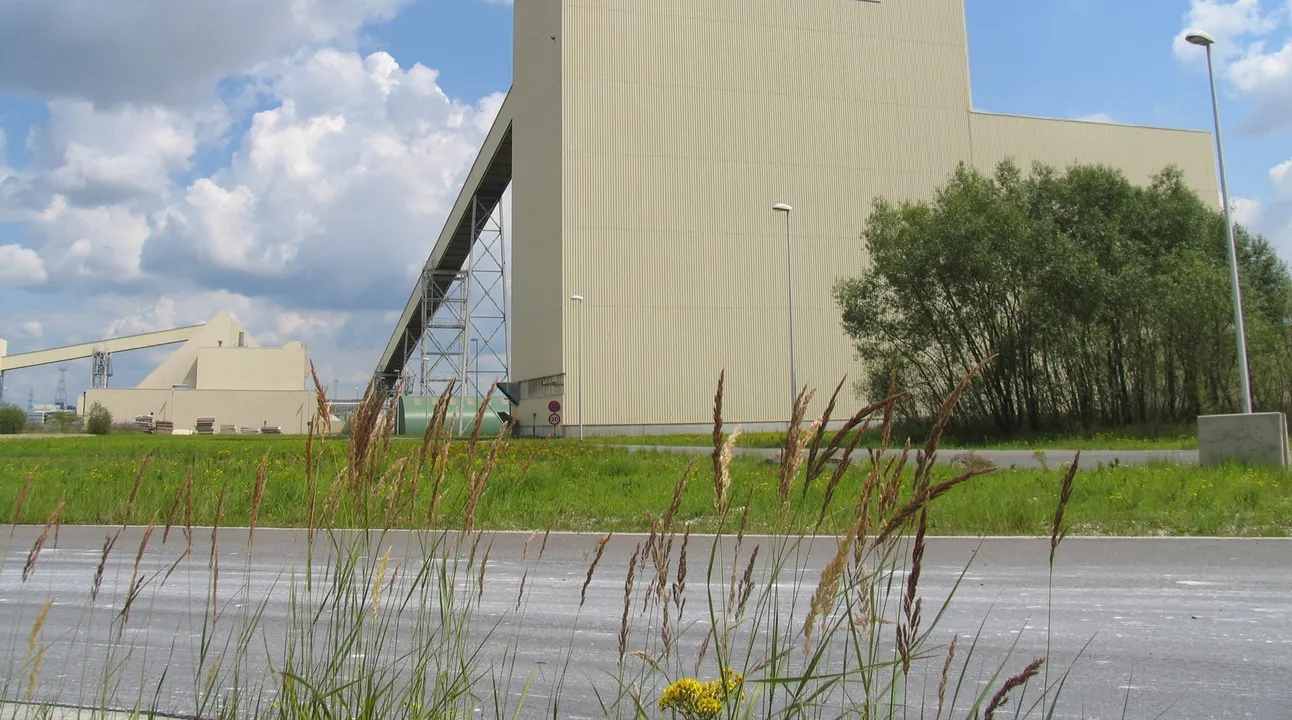
Een duurzame productie
De productie van een gipskartonplaat is in principe een relatief eenvoudig proces. Gips wordt eerst verhit, waardoor het wordt omgevormd tot pleister (stucco). Dat poeder wordt met water vermengd en aangebracht tussen twee vellen karton die aan elkaar worden gekleefd, op maat gesneden en gedroogd in een droogoven.
Tom Rommens: “Bij het drogen van de platen komt in de droogoven een grote hoeveelheid waterdamp vrij. Een deel van die waterdamp recupereren we en gebruiken het opnieuw in het productieproces. Door de waterkringloop zo gesloten mogelijk te houden, levert ons dat een jaarlijkse besparing van 13.000m3 water op.
De productie op zich vraagt ook weinig energie. De transformatie van gips tot pleister (calcinatie) en het droogproces van de platen gebeurt bij 160°C. We hebben daarvoor wel een constante toevoer van gas nodig, maar dankzij onze warmtekrachtkoppelingsinstallatie kunnen we met een deel van die gastoevoer ook elektriciteit opwekken, waardoor een groot deel van de elektriciteitsbehoefte van onze fabriek wordt gedekt door de WKK.”
Recyclage
Gyproc België was tot begin de jaren 2000 langs het Albertkanaal in Wijnegem gevestigd. Met de nieuwbouw in Kallo, op de Antwerpse Linkeroever, werd al meteen voorzien om de productieafval (platen die zijn afgekeurd, stof van de zaagmachines …) te recycleren.
Vervolgens kwam er in 2009 het Gipsconvenant, waarbij de Belgisch-Luxemburgse Gipsvereniging, OVAM, de Confederatie van Aannemers van Sloop- en Ontmantelingswerken, de bedrijfsfederatie van de circulaire economie en de Vlaamse Confederatie Bouw zich engageerden om jaarlijks 25.000 ton gips te recycleren. Ondertussen is dat cijfer al toegenomen tot 32.000 ton per jaar.
De vestiging in Kallo, en meer bepaald zusterbedrijf New West Gypsum Recycling, dat instaat voor de verwerking van de gipsafval tot bruikbare grondstof, speelt daarin een centrale rol.
Tom Rommens: “De vrachten gipsafval die op onze site worden aangeboden, worden eerste gecontroleerd op verontreiniging en dan worden de blokken en platen gemalen en wordt het papier van het gips gescheiden. De hoeveelheid gerecycleerd materiaal die bij de productie van nieuwe platen wordt toegevoegd, varieert van 10 tot 20%, afhankelijk van het type plaat. Met een gemiddelde van 13% scoren we als een van de beste in Europa; enkel Scandinavië doet het nog beter. We gaan elk jaar een procentje omhoog en het is de bedoeling toch relatief snel 20% recyclagemateriaal te halen.”
Natuur
De restzones op het industrieterrein worden sinds 2012 in samenwerking met Natuurpunt als biodiversiteitszones ontwikkeld. Daarbij is er vooral aandacht voor inheemse flora en fauna. Op het terrein, vlak bij de ingang, staat er eveneens een gigantisch groot bijenhotel.
Tom Rommens: “We zijn afgestapt van het idee om enkel gazonnetjes rond onze fabriek te zaaien. Alles bij elkaar gaat het om 1,5 hectare grond die we samen met de mensen van Natuurpunt laten herontwikkelen tot natuur omdat het oppervlakten zijn die nooit herbenut zullen worden: op de rand van een perceel waar leidingen onder liggen of die dienen als brandgang voor de brandweer om water uit de dokken te halen.”
Het gras wordt niet meer wekelijks gemaaid en het maaien verloopt in blokken, zodat planten de kans krijgen zich te ontwikkelen en zaad te produceren. Er is ook een herprofilering van het terrein gebeurd door meer reliëf, struiken en bomen toe te voegen voor een afwisseling van licht en schaduw.
Tom Rommens: “Het is voor alle partijen een win-winsituatie. Het kost ons minder aan onderhoud en er is meer natuur, want de biodiversiteit is gestegen, er zijn meer planten en bloemen en daardoor meer insecten en er wordt al eens een zeldzaam vogeltje gespot.”
Tom Rommens ziet in deze ‘kleine stap voor het natuurbehoud in de haven’ grote kansen liggen voor de Antwerpse havengemeenschap: “Wanneer elk bedrijf in het havengebied enkele procenten van zijn groen tot natuurgebied zou omvormen, kunnen we dat in geen tijd met elkaar verbinden tot groene netwerken.”
Duurzame logistiek
Jaarlijks vervoert Gyproc zo’n 800.000 ton materiaal. Het gaat daarbij om de aanvoer van grondstoffen (gips, karton …), de afvoer van afgewerkte producten (platen, pleisters) en intercompany transporten. De totale CO2-uitstoot die met die transporten gepaard gaat, wordt ingeschat op zo’n 4.700 ton per jaar.
Tom Rommens: “De basisfilosofie van de groep om productiesites op te trekken die enkel bedoeld zijn om de lokale markt te bedienen, zorgt er in de eerste plaats al voor dat wij geen lange transporten moeten organiseren. Daarnaast zetten we veel in op de binnenvaart. We zijn gevestigd in de haven en beschikken over een eigen laad- en loskade. De aanvoer van het gips verloopt helemaal via de binnenvaart, behalve bij het recyclagegips. Jaarlijks ontvangen wij ongeveer honderd binnenschepen met RO-gips, voornamelijk afkomstig uit Nederland en Duitsland.”
Drie jaar geleden organiseerde Gyproc een proefvaart om het binnenschip dat uit Duitsland grondstof leverde, ook in te zetten voor het vervoer van de afgewerkte platen naar Amsterdam, in het kader van het ‘Build over Water’-project van het Vlaams Instituut voor de Mobiliteit. Het schip vervoerde 700 pallets, het equivalent van veertig vrachtwagens.
Tom Rommens: “Op zich verliep dat goed, alleen is het voor de groothandel niet altijd evident om zo’n groot volume te ontvangen. Ondertussen hebben we een samenwerking afgesloten met Blue Line Logistics die een Pallet Shuttle Barge inzet met een capaciteit van circa 270 ton, wat qua volume voor beide partijen beter handelbaar is.”
De Pallet Shuttle Barge (PSB) is een nieuw type palletschip dat speciaal werd ontwikkeld om transporten tot 300 ton te verzorgen met diverse soorten pallets, van bouwmaterialen tot consumptiegoederen, stukgoed, rolcontainers, trailers ...
De barge is volledig self supporting met een eigen kraan die de goederen kan laden en lossen. Blue Line Logistics verzorgt voor Gyproc het traject Kallo-Amsterdam, waardoor het bedrijf per transport dertien vrachtwagens van de weg afhaalt.
Tom Rommens: “We zijn in 2013 ook in het Lean & Green-programma van het VIL gestapt en zetten ons dus dagelijks in om de uitstoot in onze logistieke keten te verminderen. Daarvoor werken we nauw samen met onze logistieke dienstverleners. De wegvervoerders zorgen ervoor dat hun chauffeurs de cursussen eco-driving volgen en dat zij niet met een verouderde vloot rijden. Daarnaast zetten wij bij onze intercompany transporten sterk in op het multimodaal vervoer. Producten van zusterondernemingen die wij op de Belgische markt verkopen, laten wij waar mogelijk via het spoor of de binnenvaart aanleveren.”
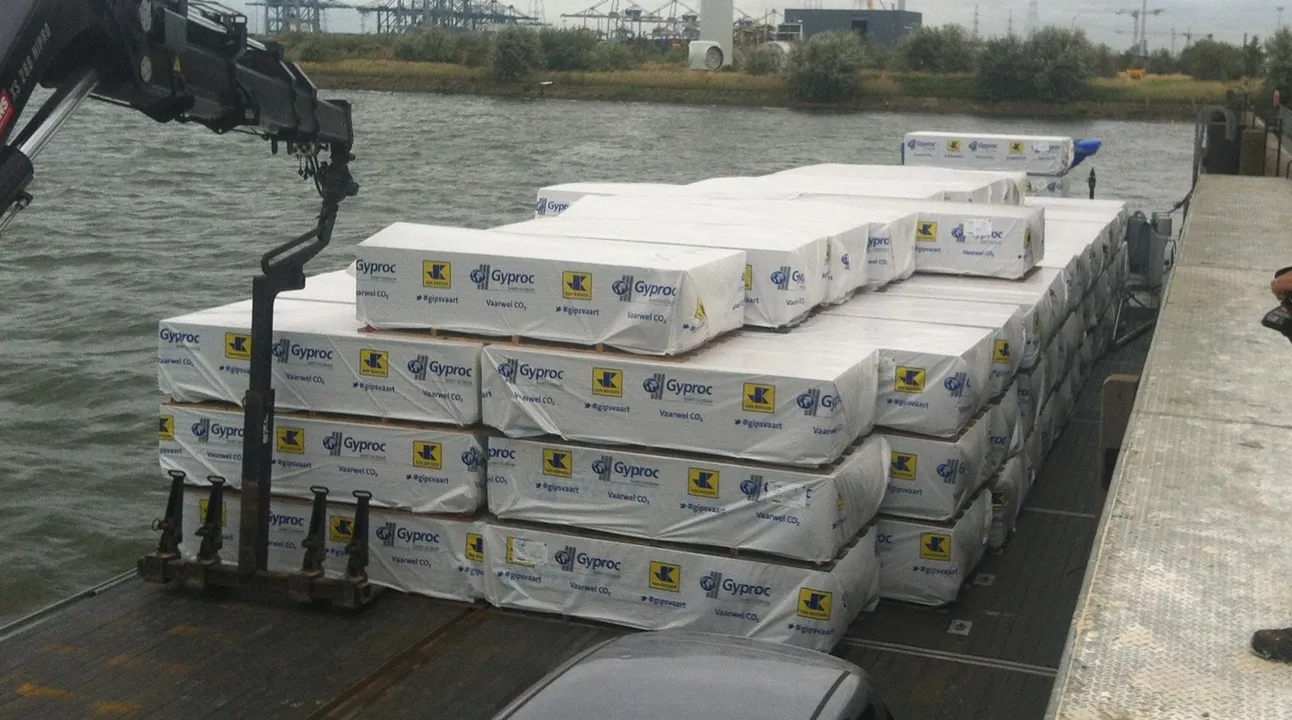
Kaderstuk: Lean & Green
In 2012 introduceerde het Vlaams Instituut voor de Logistiek (VIL) het Lean and Green programma waarmee het bedrijven ondersteunt die zich ertoe verbinden de CO2-uitstoot van hun transport- en logistieke activiteiten op vijf jaar tijd met 20% te doen dalen. Het VIL begeleidt hen bij het schrijven van een plan van aanpak dat door de VUB (departement MOBI) wordt geëvalueerd. Wordt dat plan goedgekeurd, dan ontvangen zij de Lean & Green award. Slagen zij er na vijf jaar daadwerkelijk in de CO2-uitstoot te verminderen en kunnen zij daarvan de nodige bewijzen aanleveren, dan krijgen zij de Green & Lean Star.
Ondertussen telt Vlaanderen 74 bedrijven met een Lean & Green award en hebben er 12 een Lean & Green Star behaald.