‘Factory of the future’ met honderd jaar ervaring
ZF Wind Power hertekent kijk op productie en logistiek
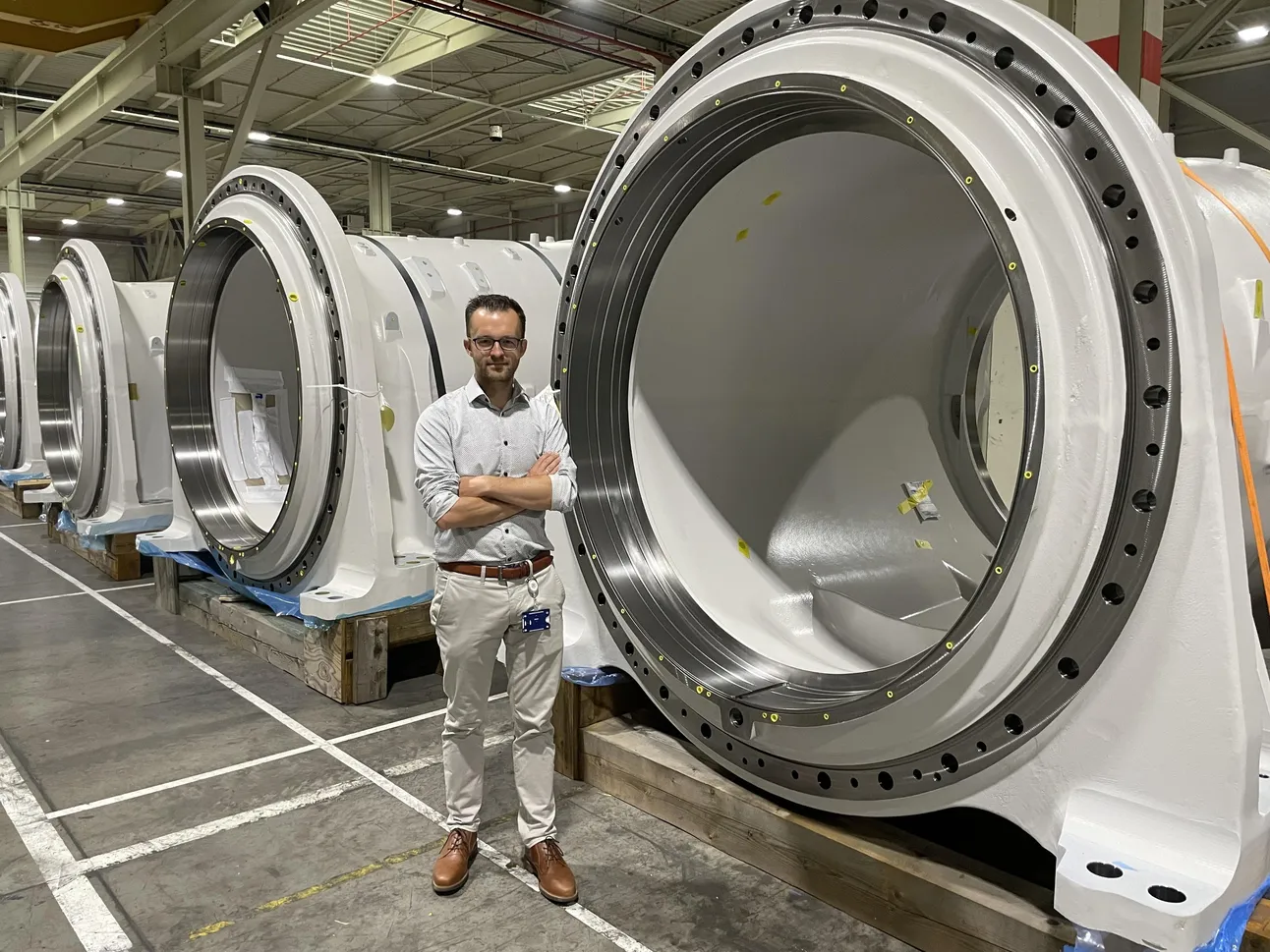
Sinds enkele maanden mag ZF Wind Power zich een ‘Factory of the future’ noemen. Agoria kende het bedrijf uit Lommel die titel om verschillende redenen toe. Met de productie van tandwielkasten voor windturbines levert ZF Wind Power niet alleen essentiële onderdelen voor een industrie die concreet meewerkt aan de energietransitie, het bedrijf doet dat met een visie die ook zelf op een duurzame toekomst is gericht.
ZF Wind Power bouwt tandwielkasten voor windturbines en andere industriële toepassingen. Het bedrijf is gevestigd in Lommel en maakt sinds 2011 deel uit van het Duitse ZF Friedrichshafen. Op de site in Lommel is het internationale hoofdkwartier van ZF Wind Power gevestigd. Behalve in Lommel heeft het bedrijf nog productievestigingen in India en China, naast nog eens twee productievestigingen in China en Duitsland die het in 2015 van Bosch overnam. Verder zijn er serviceafdelingen in verschillende landen, waaronder de Verenigde Staten. Alles samen telt ZF Wind Power vijf productiesites, waar 3.500 medewerkers instaan voor een productievolume van ongeveer 4.500 tandwielkasten per jaar. Zowat duizend daarvan zijn afkomstig uit Lommel. Op die grote site – het terrein beslaat achttien hectare – zijn 930 medewerkers actief.
Hoewel het vandaag tot een Duitse groep behoort, heeft ZF Wind Power zijn roots in ons land. Tot 2011 was het bedrijf actief onder de naam Hansen Transmissions. De geschiedenis van die onderneming gaat terug tot 1923, toen een bescheiden atelier in Antwerpen reservestukken voor versnellingsbakken en transmissies op maat begon te maken. Eind de jaren 1930 verhuisde het bedrijf naar Edegem. Ingenieur David Hansen, die zijn carrière in het atelier startte, bedacht en patenteerde onder meer een standaardisatiesysteem voor transmissiesystemen. Al in 1979 startte het bedrijf – intussen bekend als Hansen Transmissions – als eerste in de markt met de productie van tandwielkasten voor windturbines. Het bouwde er in 2003 een compleet nieuwe fabriek voor in Lommel.
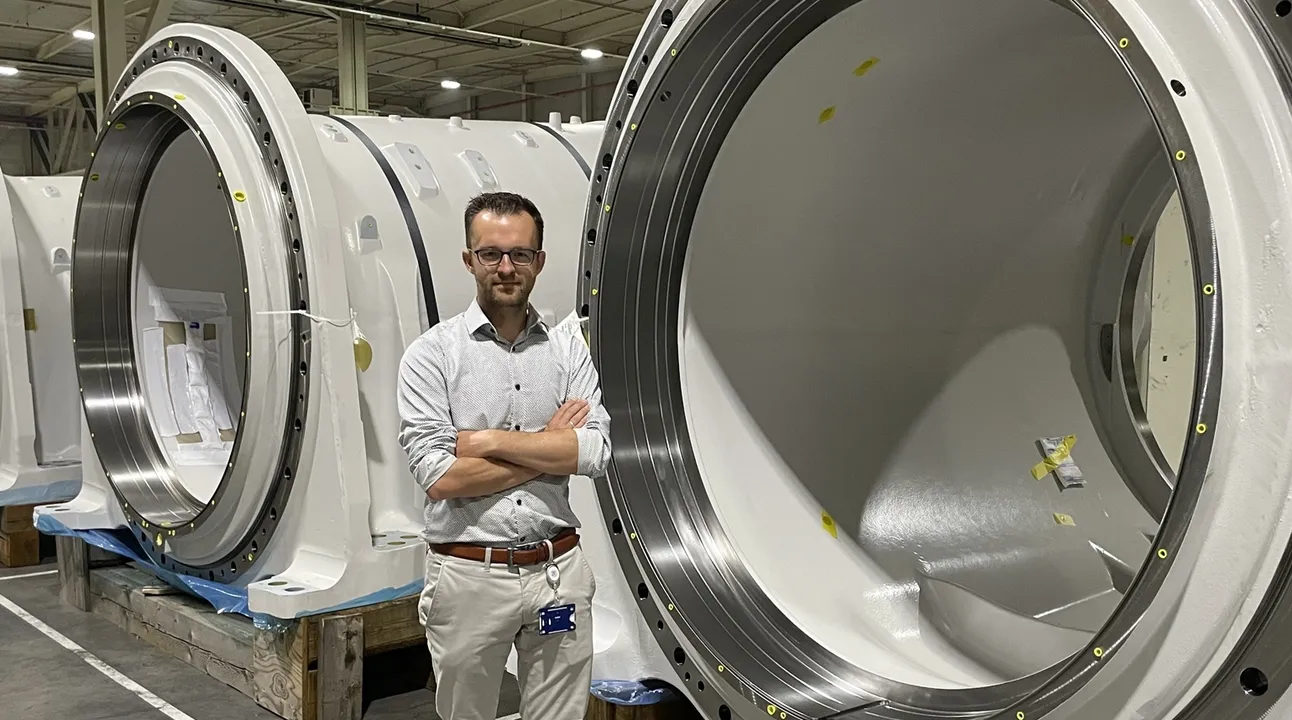
Alles in groot formaat
ZF van zijn kant maakte vooral naam in de automobielindustrie, met de bouw van versnellingsbakken. Het bedrijf zag een opportuniteit in de markt van windturbines. Om daar meteen snelheid te maken, besliste het de marktleider over te nemen: de windafdeling van Hansen Transmissions. “Voor alle duidelijkheid, wij bouwen zelf geen windturbines”, zegt Jan Van Nylen, afdelingshoofd operationele digitalisering bij ZF Wind Power. “De windturbinebouwers kopen bij ons de tandwielkasten die ze nodig hebben voor hun windturbines.” Eenvoudig uitgelegd: de overbrenging in die tandwielkast moet de lage snelheid van de draaiende wieken van de windturbine omzetten in de hoge snelheid waarmee het binnenwerk van de generator draait om elektriciteit op te wekken.
Die koppelreductie laat zich niet zomaar overbrengen door twee tandwielen. Je hebt er een hele reeks voor nodig, behuisd in een tandwielkast. De uitdaging voor ZF Wind Power is dat hun klanten almaar grotere windturbines bouwen. Naarmate de omvang van de turbines toeneemt, groeien ook de krachten die ZF Wind Power met zijn tandwielkasten moet zien op te vangen. Het gevolg laat zich raden: steeds grotere tandwielen en tandwielkasten, met een grote impact op het vlak van material handling, opslag en transport. De grootste stukken in het geautomatiseerde magazijn van ZF Wind Power wegen tot zestien ton. Ze krijgen in het magazijn een plaats op pallets van vier bij vier meter. Evengoed beheert ZF Wind Power in het magazijn ook allerlei kleine bouten en moeren – en alles daar tussenin.
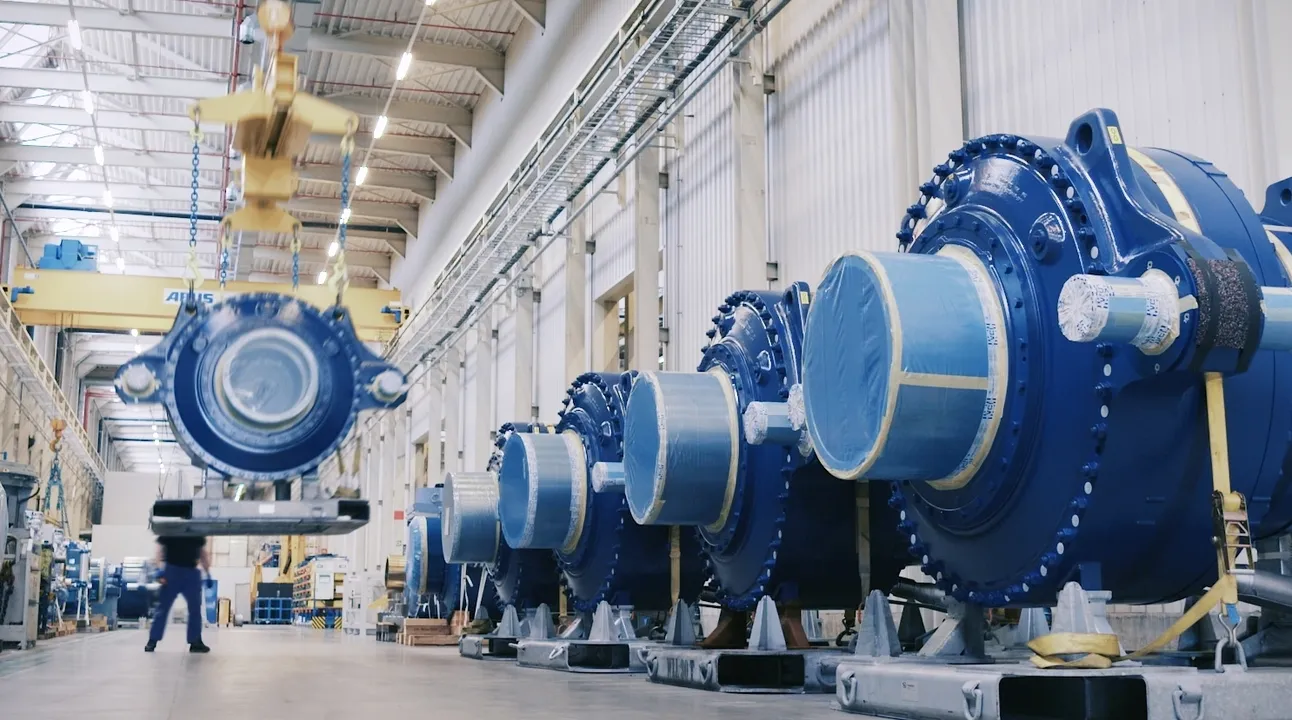
Alles in eigen beheer
ZF Wind Power houdt de productie van de structurele componenten van de tandwielkasten – zoals onder meer de tandwielen zelf – bewust in eigen beheer. De productie van een tandwiel start daardoor in principe in de eigen metaalbewerkingsafdeling, waar ZF Wind Power zelf de nodige gietstukken bewerkt. Ook het verdere bewerken en slijpen van de onderdelen gebeurt in de eigen ateliers. “Tot pakweg vijf jaar geleden produceerden we uitsluitend op maat”, zegt Jan Van Nylen. “De klant legde de plannen van een turbine voor, waarna het aan ons was om perfect op maat een tandwielkast te voorzien.”
Bij die manier van werken is een duidelijke evolutie merkbaar. “De druk op de kosten neemt toe. Ontwikkeling op maat duurt lang en kost veel. Daarom introduceerde ZF in 2016 modulaire oplossingen in de markt: met vaste standaarden voor grote delen van de tandwielkast en enkel een klein deel van de toepassing op maat. Het is een aanpak die toelaat ook in de productie een stuk makkelijker te schalen.”
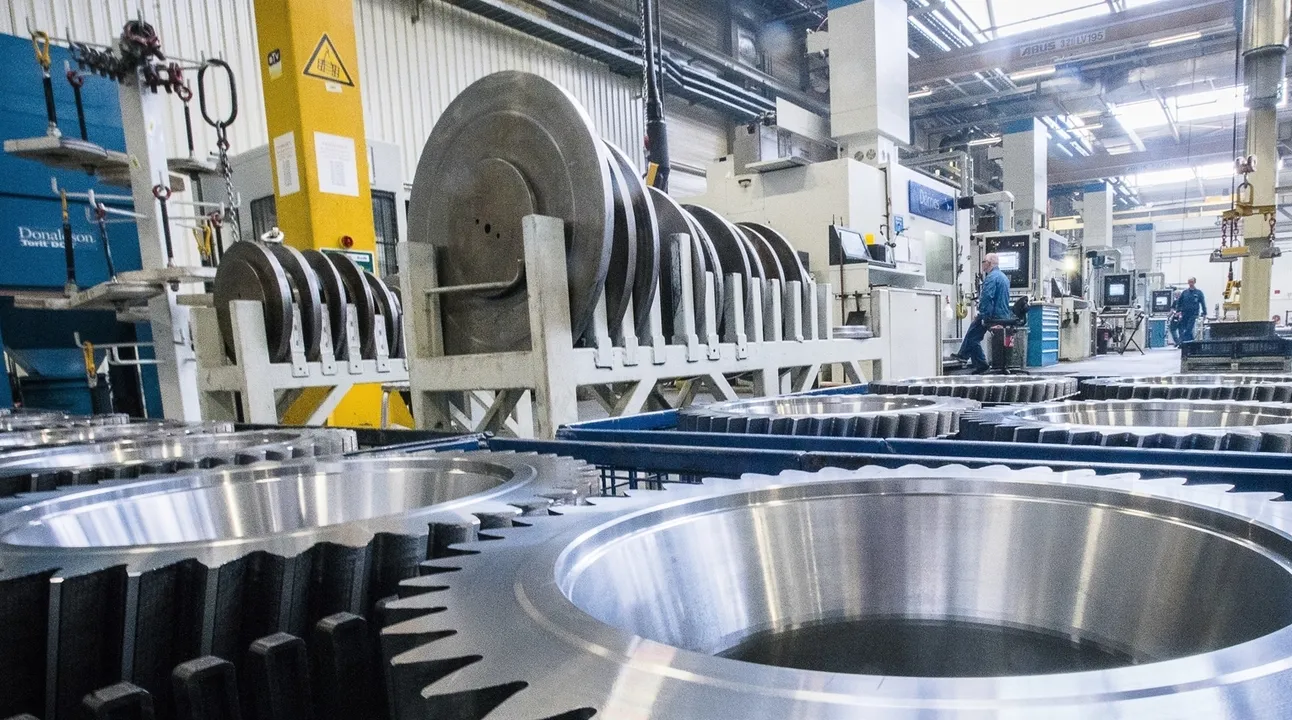
Nauwe samenwerking met de klant
De grootste revolutie die de voorbije jaren bij ZF Wind Power plaatsvond, gaat uit van de nauwe samenwerking met de windturbinebouwer. Het resultaat is een kant-en-klare ‘power train’. “Het gaat niet alleen om de tandwielkast, maar ook om de generator en de koppeling met de wieken van de molen”, legt Jan Van Nylen uit. “We bieden de windturbinebouwer daarmee een essentieel en groot onderdeel van de windturbine aan onder de vorm van een kant-en-klare oplossing.” Maar opnieuw: de impact op transport en logistiek was enorm. Dat bleek al snel toen ZF Wind Power zijn nieuwe benadering in de praktijk bracht voor de Deense windturbinebouwer Vestas. Vroeger stuurde ZF Wind Power zijn afgewerkte tandwielkasten naar Vestas. Dat bedrijf maakt de nacelle, de behuizing voor de powertrain die boven op de toren van de turbine komt. Vestas plaatste de volledige powertrain in de nacelle op zijn site in Denemarken, waarna het geheel naar het windpark vertrok voor installatie.
“Samen met Vestas hebben we dat hele proces hertekend”, zegt Jan Van Nylen. “Vestas stuurt nu een lege nacelle naar het windpark. Ook wij sturen onze powertrain rechtstreeks naar het windpark – niet langer naar Vestas. De montage van de windturbine vindt nu op de site van het windpark plaats.” Het nieuwe proces vroeg een grondige aanpassing van het logistieke traject, maar leverde ook meteen een belangrijke vermindering van de ecologische voetafdruk op. “We zitten met onze oplossing nu een flink stuk hoger in de waardeketen. Tegelijk is er echter ook een vangnet weggevallen. Was er onverhoopt een probleem met de tandwielkast, dan merkte Vestas dat op – voor de onderdelen naar de klant vertrokken. Wanneer er vandaag iets niet klopt met de powertrain, komt dat pas op de werf – op het windpark – aan het licht, met een veel grotere impact op de voortgang van de werkzaamheden. Het zorgt ervoor dat we het niveau van de kwaliteitscontrole nog verder hebben verhoogd.”
Nieuwe kijk op logistiek
De nieuwe aanpak vroeg om een andere kijk op de logistiek. Vroeger had ZF Wind Power maar één leveradres voor de producten die Vestas bestelde: de nacellefabrieken van Vestas in Denemarken. “Nu moeten wij – in samenwerking met Vestas – wereldwijd kunnen leveren.” Bijkomende moeilijkheid: een powertrain stuur je niet zomaar met een koerier naar de klant. Het gaat om een gevaarte van negentig ton. Vanuit Lommel gaat het via speciaal transport over de weg naar de haven van Antwerpen. Daar houdt ZF Wind Power een kleine buffervoorraad aan om in geval van nood – mocht er op de werf iets misgaan – toch snel een nieuwe powertrain te kunnen uitsturen. De doorlooptijd van de productie van een nieuwe powertrain bedraagt immers zowat drie maanden. Vanuit Antwerpen vertrekken de powertrains per schip naar de windparken op zee en op land. “In Europa was de vraag naar nieuwe windturbines op land de voorbije tijd wat aan het vertragen, maar het nieuwe REPowerEU-plan zal de vraag weer sterk doen stijgen”, zegt Jan Van Nylen. “De vervanging van oude turbines op land is een interessante markt, maar we verwachten vooral een sterke groei in de windparken op zee.”
Momenteel werkt ZF Wind Power in Lommel aan prototypes voor de volgende generatie powertrains. Het gaat onder meer om oplossingen voor turbines van 15 MW op zee, waar tot voor kort 6 MW gangbaar was.
Jan Van Nylen: “Het zorgt ervoor dat de powertrain flink groter wordt: zowat 200 tot 220 ton per stuk. Vervoer over de weg is niet meer haalbaar. Die grote powertrains zullen we via de binnenvaart – onder meer via het Albertkanaal – naar Antwerpen brengen. De prototypes die we vandaag testen, gaan over twee jaar in serieproductie. Dat is de toekomst van onze fabriek. Bij de opening van de site in Lommel in 2003 stelde ZF Wind Power dat het daarmee twintig jaar vooruit keek. Dat blijkt perfect te kloppen. Maar om straks met powertrains van meer dan 200 ton te kunnen werken, moeten we bepaalde delen van de fabriek fundamenteel aanpassen, met name om het eindproduct en de onderdelen te kunnen heffen en verplaatsen.”
Duurzame aanpak
Dat ZF Wind Power sinds dit voorjaar de titel van ‘Factory of the future’ mag voeren, heeft het onder meer aan het traject rond ‘integrated engineering’ met Vestas te danken. Dat partnership is intussen verder uitgediept, onder andere op het vlak van kwaliteitscontrole. De uitgebreide elektrische en elektronische testen van de powertrain vonden vroeger bij Vestas plaats. Omdat de powertrains nu rechtstreeks naar de werf van de klant vertrekken, beslisten ZF Wind Power en Vestas om die controle in Lommel te organiseren. “Vestas installeerde bij ons een teststraat en bezorgde onze medewerkers de nodige opleiding”, aldus Jan Van Nylen. Ook het menselijke aspect blijft immers belangrijk. “Als fabriek van de toekomst willen we tegelijk ook de medewerker centraal houden, met onder meer voor iedereen een duidelijk zicht op de rollen en functies die we nodig hebben – en op het groeipad dat naar die specifieke jobs leidt.”
Nog een aspect waarom ZF Wind Power zich als Factory of the future mag omschrijven, heeft te maken met de ecologische inspanningen die het bedrijf levert. “Dat is niet alleen verbonden met onze activiteit, die er uiteindelijk op gericht is windturbines beter en goedkoper te maken – en zo de beschikbaarheid van groene energie te vergroten, het gaat ook om de manier waarop we onze powertrains produceren”, weet Jan Van Nylen. “Onze fabriek draait voor honderd procent op windenergie. In de harderij – waar we het metaal in ovens doen uitharden – stappen we over van gas naar groene stroom. We plaatsen daarvoor een eigen windturbine op ons parkeerterrein.”
De afwerking van de tandwielen – tot op enkele micrometer juist – levert vervuild metaalslijpsel op dat in die vorm niet te recycleren is. De olie die ZF Wind Power bij het slijpen gebruikt, perst het uit het slijpsel. Dat laat toe zowel de olie als het metaal toch te recycleren.
Digitalisering ondersteunt medewerkers
In de toekomst wil ZF Wind Power blijven inzetten op digitalisering om het productieproces verder te verfijnen. “We capteren heel wat data bij de machines die we inzetten. Door die data te analyseren, kunnen we processen sturen, fouten vermijden en kosten verlagen.” Tegelijk zorgt het gebruik van data voor extra ondersteuning van de operatoren. “Zij hebben zeker geen gemakkelijke job. Een operator die de parameters bij een machine moet aanpassen, kan daarbij al eens een foutje maken. Maar een kleine vergissing kan het bedrijf al snel veel geld kosten”, klinkt het. Wanneer het systeem de voorgestelde wijziging kan aftoetsen aan een set tolerantiewaarden, zorgt dat voor extra controle en zo ook voor een betere begeleiding van de medewerkers. Het ultieme doel bestaat erin uit te komen bij een systeem dat een ‘closed loop’ vormt. “Het gaat dan bijvoorbeeld over het aftoetsen van data uit de slijperij om te controleren of de hardingsdiepte van een tandwiel correct is, zonder dat je daarbij manueel die diepte hoeft te meten”, besluit Jan Van Nylen.
Inloggen/registreren
Om deze content te lezen, moet u zich inloggen.
Log in of registeer nu via onderstaande knop en krijg toegang tot deze inhoud.