Een palletstelling die een pallet van 7 ton draagt?
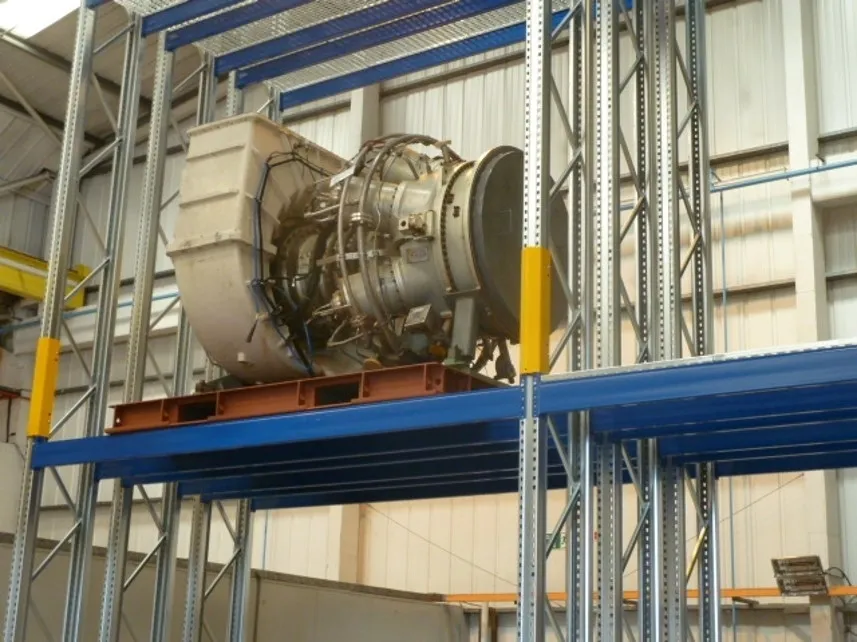
Ja dat kan! Siemens had zijn gasturbines nog nooit eerder in magazijnstellingen opgeslagen. BITO moest een oplossing uitwerken voor zo'n hoog palletgewicht. Dit was ook de zwaarste pallet die BITO ooit heeft opgeslagen, van stevige BITO ondersteuning gesproken!
Siemens verbetert hun service met een nieuw op de toekomst gericht magazijn.
Siemens Industrial Turbomachinery investeerde 54,97 miljoen Euro in het "Teal Park" om hun service- en opslagactiviteiten te handhaven én in een nieuw "Global Service Operation Centre" om gezondheid en veiligheid te bevorderen, om kortere doorlooptijden te leveren en kosten te besparen. En om tegelijkertijd de servicemogelijkheden uit te breiden. Het toekomstgerichte project is op tijd en binnen budget afgerond.
Siemens Industrial Turbomachinery ontwerpt, produceert en onderhoudt kleine industriële gasturbines, ondersteund door vele medewerkers op 3.500 locaties in 90 landen.
1500 daarvan blijven operationeel bij belangrijke klanten in de olie- en gasindustrie, industriële industrie, ziekenhuizen en papierfabrieken.
Om een concurrentievoordeel te behalen in het leveren van een toonaangevende service aan klanten, wat essentieel is voor zakelijke duurzaamheid, investeerde Siemens naast de vernieuwde installatie in het “Teal Park” in Lincoln, voor 14,8 miljoen Euro in de totale projectkosten van de bouw van een nieuw Global Service Operation Centre (GSOC), dit alles om de service en logistieke service te handhaven. De hele logistieke site vertegenwoordigt een investering van 54,97 miljoen Euro.
Naast de hoofddoelstelling een duurzame stock aanleggen van aandrijvingscomponenten, gereedschappen en reserveonderdelen, werden ook de verbetering van gezondheids- en veiligheidsaspecten op de werkvloer, de bedrijfsgroei, snellere doorlooptijd goederen, capaciteitsuitbreiding en kostenreductie in overweging genomen.
De consolidatie omvatte: de verplaatsing van de kleine Siemens onderdelen van de gasturbines, de opslag van motoren en werktuigen die voorheen op een nabijgelegen locatie lagen, alsmede het binnenhalen van de opslag op een andere locatie en de activiteiten van de aëroderivatieve gasturbines van het Siemens-concern.
Deze gecombineerde operationele voetafdruk van 12.000 m² zou in het nieuwe 7000 m² magazijn moeten passen en tegelijkertijd ook nog is de operationele efficiëntie maximaliseren.
Siemens is deze uitdaging aangegaan door nauw samen te werken met leveranciers van logistieke systemen. Het resultaat is een innovatieve intralogistieke oplossing voor de opslag en het orderverzamelen van de 15.000 artikelen van het bedrijf. Van moeren & bouten tot zelfs de opslag van 6-tons motoren.
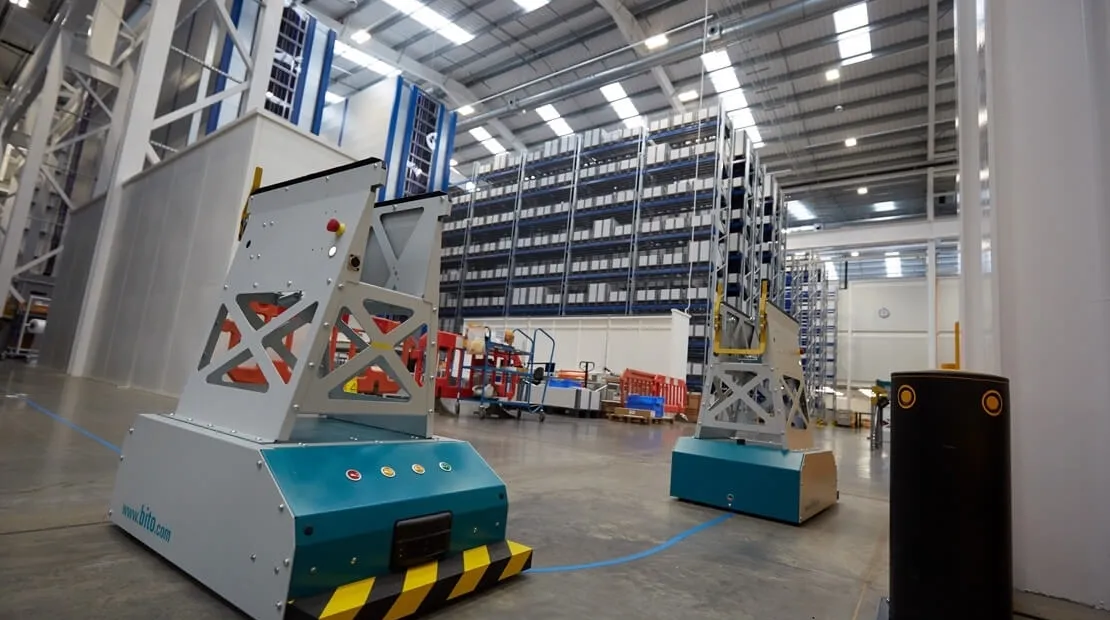
Op maat gemaakte rekken voor motoren verminderen de voetafdruk
Op de vorige locatie werden deze zware turbines op de vloer van de hal opgeslagen, dat nam een grote m² voetafdruk in beslag met een aanzienlijke hoeveelheid verspilde ruimte erboven, terwijl het ook inefficiënt was voor ingenieurs om een specifieke motor te lokaliseren. Om in het nieuwe 7000 m² vloeroppervlak te passen, moest de ‘lege ruimte’ boven de motoren worden gebruikt, terwijl er ook een efficiënter voorraadbeheer nodig was om een vaste locatie aan de turbines toe te wijzen.
Het antwoord was een indrukwekkende palletstelling met 3 niveaus voorzien van 72 plaatsen voor de motoren, bediend door een inductiegeleide zijdelingse lader. Het door BITO op maat gemaakt stellingsysteem met behulp van standaard stellingliggers en staanders, maakt het mogelijk om motoren met een gewicht tot 6 ton en opgeslagen op pallets van 1 ton (speciaal ontworpen door de lokale fabrikant Rilmac), zowel op het eerste legniveau als op de grond te stockeren. De bovenste verdiepingen kunnen tot 4 ton dragen.
Siemens had zijn gasturbines nog nooit eerder in magazijnstellingen opgeslagen. BITO moest een oplossing uitwerken voor zo'n hoog palletgewicht. Dit was ook de zwaarste pallet die BITO ooit heeft opgeslagen, van stevige BITO ondersteuning gesproken! Een prototypeprogramma waarbij een ingenieur uit BITO Duitsland betrokken was, produceerde componenten die op de bestaande locatie van Siemens werden getest met de zwaarste motor, een 6-tons SGT-gasturbine, op een pallet die reeds zelf een eigengewicht van 1 ton had.
Het nieuw "Global Service Operation Centre” omvat ook 700 plaatsen met standaard palletstellingen voor bulkopslag en 3650 opslaglocaties in een hoogbouw smalle gangen stellingen.
En tien 11 meter hoge Kardex Remstar XP500 shuttles zorgen voor ruimtebesparend opslaan en ophalen van kleine onderdelen.
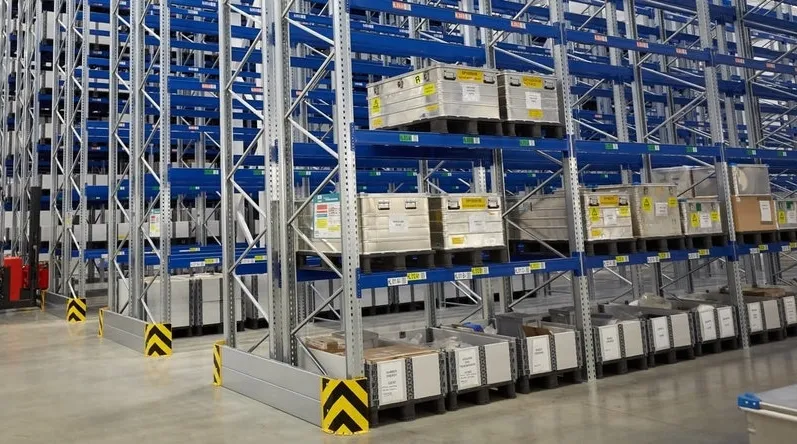
Veilig en efficiënt intern transport
Met het oog op verbetering van gezondheid en vooral veiligheid op de werkvloer, werkte Siemens nauw samen met BITO en Kardex aan een innovatief onbemand intern transportsysteem voor het scheiden van voertuig- en menselijke werkplekken, dat een snelle en veilige goederenbehandeling tussen de inkomende goederen, de Kardex shuttles en de pakstations garandeert.
Zes BITO LEO Locative AGV's (onbemand transportsysteem) circuleren continu zonder wifi simpelweg na het kleven van tape op de vloer, die dient als volglijn. Op de vloer gekleefde barcodes naast de tape, geven elke LEO instructies en leiden hem op betrouwbare wijze naar een overdrachtsstation waar hij zijn magazijnbak deponeert en wachtende pick-up verzamelt.
Als interne transportbakken worden vouwbare bakken gebruikt. De opslagmethode omvat lege bakken boven de LEO-stations met behulp van “stukgoeddoorrolstellingen” als buffer. Wanneer een artikel vanuit goederenontvangst moet worden overgebracht, wordt het artikel uit de bak gehaald en in de daarvoor bestemde bak van een Kardex-eenheid geplaatst. De lege vouwbare bakken worden vervolgens ingeklapt en aan de achterzijde van een doorrolkanaal (stukgoeddoorrolstelling) gevoerd om naar voren te rollen, zodat een lege bak beschikbaar is voor de uitgaande pick-up door een LEO wanneer er productie componenten nodig zijn.
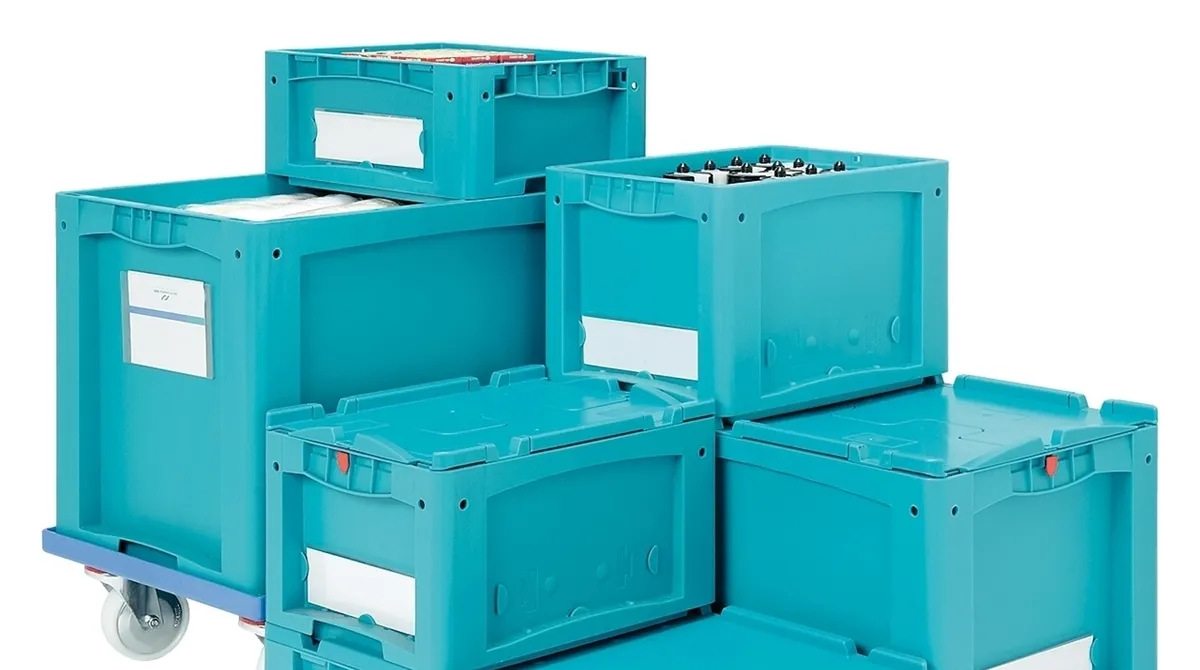
Kleine onderdelen orderpicken
De 10 Kardex shuttles bieden een totaal van 76.800 snelle flexibele opslaglocaties voor kleine onderdelen. Ieder niveau bevat tien 600x400 magazijnbakken, elk niveau kan ook worden onderverdeeld door het gebruik van kunststof verdelers, om het nodige aantal opslaglocaties aan te passen aan het formaat en aantal nodige bakken. Hierdoor kan je per niveau uitbreiden naar 80 bakken en Siemens krijgt hierdoor de flexibiliteit om verschillende formaten van opslaglocaties te creëren.
Bestellingen die in bakken worden verzameld, worden op een station geplaatst in afwachting van de ophaling door een LEO om ze naar het verpakkingsstation te brengen, zodat de arbeiders verder kunnen gaan met hun volgende taak. Deze 'buffer' geeft Siemens ook een duidelijk zicht op het binnenkomende werk in elk van de gebieden.
SAP Warehouse Management Software werkt feilloos samen met de oplossing om de voorraad in real time bij te houden via barcodes.
Op tijd en binnen budget
De bouw van het nieuw Global Service Operation Centre is gestart in mei 2017, met de eerste montage in oktober 2017 en de inrichting van het magazijn vanaf eind november. Voor Kerstmis werden alle stellingen van BITO en de Kardex Shuttles geïnstalleerd. De oplevering van de nieuwe inrichting was 21 maart en is op 2 april in gebruik genomen.
Door uitstekend projectmanagement en communicatie met de betrokken leveranciers werd het GSOC succesvol afgerond binnen het budget en op tijd om een marktleidende service te leveren aan de klanten van Siemens.
Klanten werden geïnformeerd over de voordelen van de nieuwe infrastructuur en door een naadloze overgangsperiode werd het volledige SKU-assortiment van 15.000 SKU's binnen een periode van 6 weken naar de nieuwe locatie verhuisd, terwijl het serviceniveau van de klant gedurende de gehele periode gehandhaafd bleef.
De belangrijkste resultaten in een oogopslag
Het nieuwe magazijn scheidt de gebieden van menselijke en drukke vorkheftrucks door het gebruik van LEO's voor het vervoer van goederen. Het stopmechanisme op heftrucks en LEO's voorkomt botsingen. LEO's minimaliseren ook de handmatige verwerking.
In termen van financiële voordelen betekent de investering van 452.000 Euro in magazijnstellingen een enorme besparing op de extra 3,4 miljoen Euro die nodig was om het oorspronkelijke plan om een gebouw van 10.000 vierkante meter op de beperkte locatie te bouwen. De stellingen besparen 1500 vierkante meter ruimte, terwijl de Kardex Shuttles in totaal 1200 vierkante meter besparen. Het gasturbinemagazijnrek zelf, heeft geresulteerd in een twee-derde vermindering van de nodige vloeroppervlakte dat in het verleden nodig was voor de gasturbines.
Het voordelige LEO-systeem zonder WiFi, geeft Return on Investment (ROI) binnen een jaar, vergeleken met de typische periode van 5 jaar voor conventionele AGV's. In tegenstelling tot andere onbemande transportsystemen, is de installatie van LEO's eenvoudig en snel waarbij de toestellen, na het kleven van de speciale tape, deze simpelweg gewoon op de tape worden geplaatst, wat volledige flexibiliteit biedt om de tape opnieuw los te trekken en nieuw te volgen routes aan te leggen. Siemens kan indien gewenst uitbreiden door het kopen of huren van extra LEO's direct uit de BITO-stock.
De productiviteit van het personeel op de werkvloer wordt gemaximaliseerd door de overname van eenvoudige transporttaken door LEO's en een vermindering van de verplaatsingstijd met 30%. Een dergelijke productiviteitsstijging kon alleen worden bereikt door twee extra voltijdse medewerkers tijdens de inbedrijfstelling en nog eens drie bij de uitbreiding van de fabriek. De verzamelcycli van de Kardex Shuttles zijn twee keer zo snel als in de voormalige opslagplaats.
Siemens krijgt ook een toekomstbestendig magazijn. Door gebruikmaking van standaard stellingensysteem, kan het gasturbinemagazijnrek op elk gewenst moment opnieuw worden geconfigureerd en het Global Service Operation Centre is ontworpen om, indien nodig, nog vier andere Kardex Shuttles te herbergen.
Uiteindelijk vergemakkelijkt het nieuw Global Service Operation Centre de groei zonder dat er meer personeel nodig is. En het zorgt ervoor dat onderdelen beschikbaar zijn zodat men op dezelfde of de volgende dag klanten kan bedienen om de stilstand tijd, die voor een turbine meer dan 113.000 Euro per uur kan kosten, tot een minimum te beperken. De normale service uren van 07.30 tot 16.00 uur worden verlengd om de piekuren in te dekken. Eventuele aanvragen aan het magazijn worden dezelfde dag nog gepickt en verpakt. Als ze voor 16.00 uur zijn afgerond, worden ze die dag verzonden.
Clive Cox, projectmanager voor Siemens Industrial Turbomachinery, geeft zijn mening over de belangrijke bijdrage van BITO aan het project: "Het team van BITO ter plaatse was zeer efficiënt en werd door de hoofdconstructeur gecomplimenteerd met zijn werkethiek en organisatie, dus vanuit ons standpunt functioneerde het allemaal zeer goed. Wij zijn zeer enthousiast over de kwaliteit van de BITO-producten. Het bedrijf is ondersteunend, zeer responsief en heeft nauw met ons samengewerkt om de service te bieden die we nodig hadden tijdens het complexe project."
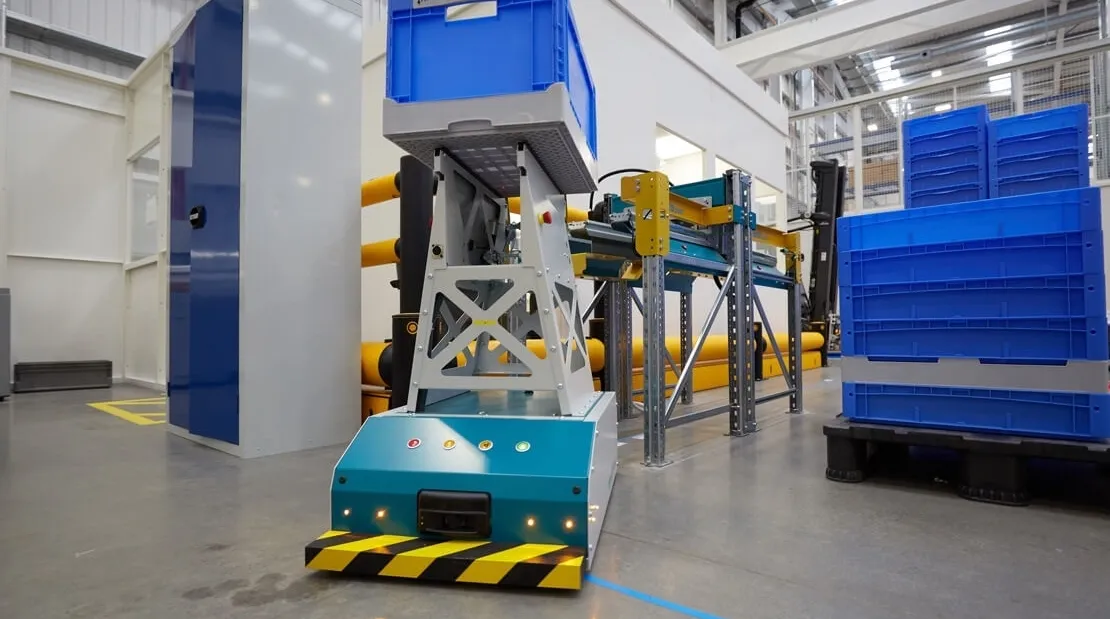
Ook hulp nodig van de systeemexpert?
Met het hoofdkantoor en de productievestigingen in Duitsland is BITO een internationaal opererende fabrikant van opslag- en orderverzamelsystemen. Het productassortiment van BITO omvat alles voor een complete magazijninrichting en toebehoren zoals, legbordstellingen, magazijnstellingen, opslagsystemen en orderverzamelsystemen, magazijnbakken in kunststof en niet te vergeten de LEO Locative het onbemande transportsysteem.
Meer weten: Een expert van Bito helpt graag bij het bepalen van de meest optimale oplossing. Telefoon: +32 3 870 99 00 - www.bito.com
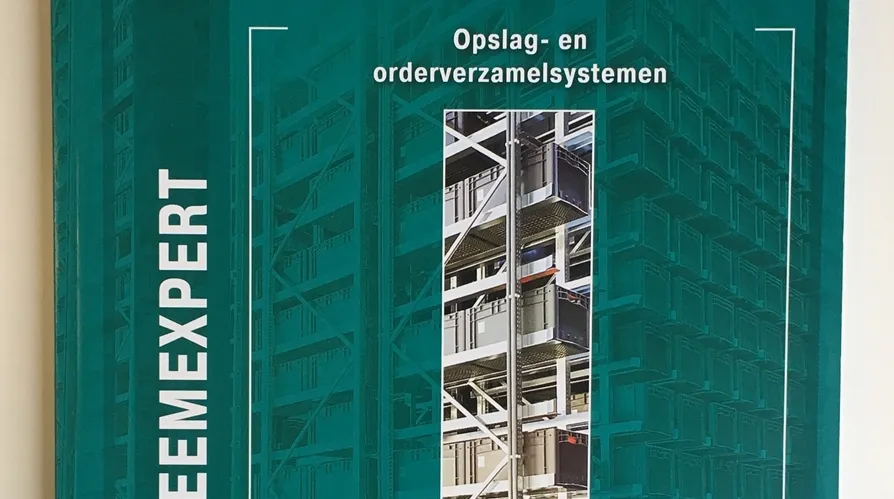
Bito verruimt je kennis
Word lid van de Bito-Community en abonneer je op onze nieuwsbrief. We brengen boeiende onderwerpen, zoals Tips&Tricks bvb. Wat kost magazijninrichting? enz …