Dutch farm dairy cooperative
RFID enabled “best before date” and RTI management
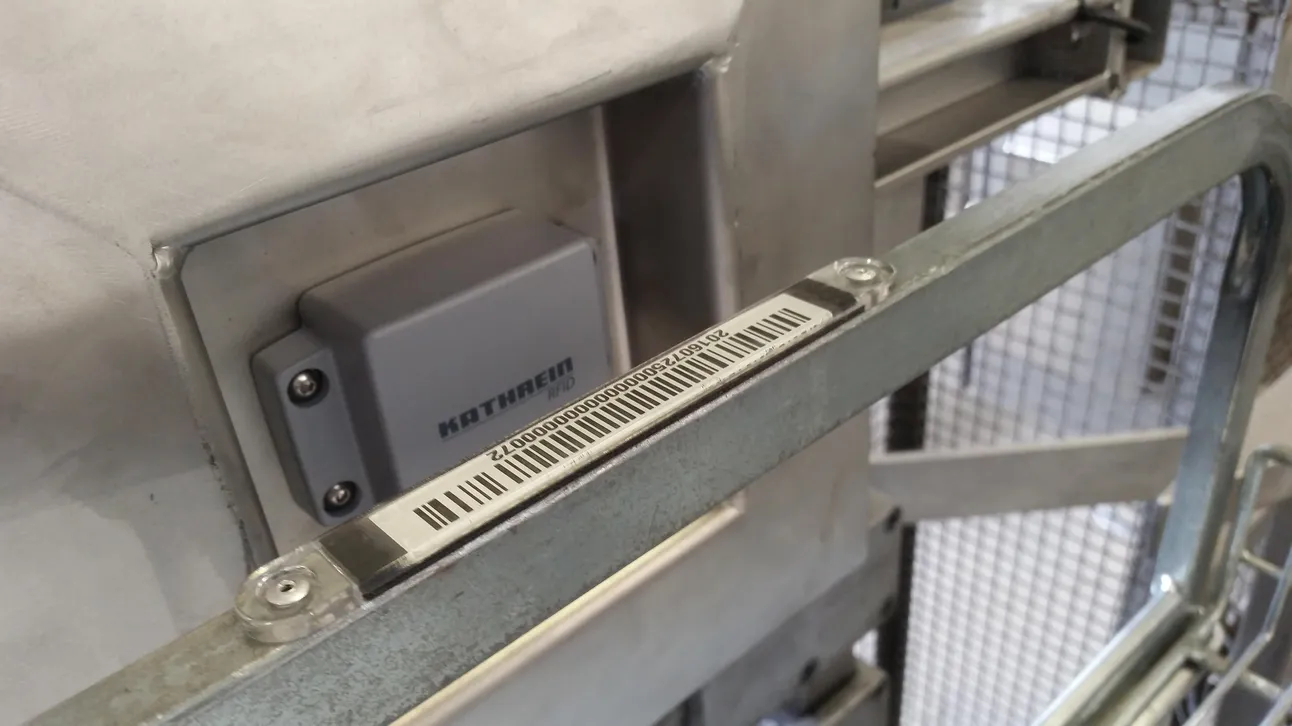
Due to a merger, an expansive dairy cooperative owned by Dutch dairy farmers is rolling out a global ERP template (SAP). This means standardising over 100 subsidiaries in 32 countries,
impacting the way of working of 22.000 employees worldwide. In many places, custom solutions must be implemented that meet the local requirements. At the dairy plant in Rotterdam, RFID technology is used to manage “best before dates” as well as the RICs or RIC’s used for high volume dairy product.
Template SAP roll-out drives local initiatives for process optimisation and efficiency Unique challenges in RTI asset management
At the Rotterdam plant, the company faced a unique challenge. Instead of pallets, returnable transport items, so called roll-in containers or RICs, are used to ship milk, yogurt, custard and more. The key issue is that the (GS1) Serialised Shipping Container Codes (or SSCC) labels that are referenced to the batch numbers, cannot be applied automatically to the RICs. This left the plant to choose from two evils: either not to apply SSCC labels, or to do it manually. But as customers like Jumbo and ALDI are requesting SSCC labels for years, it wouldn’t do to not incorporate serialised container tracking into the new systems deployed in Rotterdam. But doing it manually, requiring at least a 1 full-time equivalent, would not be an option either! The project manager approached Mieloo & Alexander to develop a solution that makes it possible to have SSCC codes on the roll-in cages without adding headcount to the plant, and which integrates seamlessly with the new MES and SAP systems, and offers the benefits of serialised RTI management both to company and its customers. The solution was found in UHF RFID tags, enabling writing and reading of SSCC shipping numbers in the user memory of RFID tags, whilst at the same time also carrying the GS1 GRAI number or Global Returnable Asset Identifier hardcoded in the EPC memory of the RFID tag.
RFID offers many advantages in logistics processes
The main advantage of the RFID tag lies in its reusability. Like the RIC itself, it can make hundreds of trips from the plant to the customer and back. On each trip, the RFID chip can contain a new SSCC code, relating to the “best before date” of the product on the container, whilst at the same time maintaining the unique identifier of the logistics asset itself. This dataset can be used to streamline the container management and to inform the customer and supply chain partners of the serialised container codes.
Custom developed on metal tag RFID tag
Unfortunately, a standard on metal tag with the formfactor (max. 9 mm wide and 5 mm high) and read performance of at least 4 meters was not available. Therefore, Mieloo & Alexander selected and contracted Omni-ID to develop a custom tag for the RIC that was tested extensively for read performance, resistance against mechanical impacts, rough handling conditions and cleaning methods and materials.
Automated labelling process on the filling line
Before a RIC is entered onto the filling lines, first the previous SSCC code is overwritten. This not only cleans the old shipping number from the tag, but is also a quality check of the RFID tag. Only then will the container be loaded with cartons of plastic bottles of milk or other dairy products. When the badge is loaded, the SSCC is written to the user memory of the RFID tag, linked to the production order of the MES system. Behind the filling line, containers are pooled on an Electronic Pallet Truck, and moved to the refrigerated warehouse. This marks the transition from production”, managed by the MES to “distribution”, managed by SAP EWM. This transition is recorded and posted automatically by an „RFID curtain” made up of 1 Kathrein RRU4 RFID reader with 4 Kathrein WIRA30 narrow beam antennas. This curtain is installed under the ceiling facing downwards (hence the 4 meters reading distance) between the production and logistics areas. The fixed mounted RFID readers on the production line are also Kathrein readers, RRU4 for the quality check at infeed and M-Aru to program the SSCC’s in the user memory. These readers are managed by noFilis CrossTalk 3.0 middleware. All process logic and integration with MES and SAP is managed by Mieloo & Alexander’s V-Track RFID solution.
Over 30.000 roll-in containers will have to be RFID tagged
Finally, the SSCC codes are scanned again, when the roll-in cages are loaded on the trucks for departures to the plant warehouses, or directly to the DC’s of the retailers like Albert Hein or Jumbo. To that purpose the Zebra MC92 handheld barcode scanner is paired with a Panmobil Scanndy RFID reader with embedded Linux server. This miniature device translates the hexadecimal values of the tag to numeric SSCC’s that are keyboard wedged in to the correct SAP field. After extensive unit, integration and stress testing at the end of 2016 and early 2017, the RFID system was taken into production, together with new SAP and MES systems. During the testing period, all 30.000 RICs were RFID tagged so that each day, 600 RICs can be filled in the Rotterdam plant alone, and encoded with the SSCC number before they leave the plant. To also register the empty stock volumes of the RICs, additional readers are placed at the unloading gates. The RFID system now provides a real-time report on the containers available, ensuring the plant to take timely action when the stock levels drop below a minimum.
The successful RFID solution is garnering interest
In the future, identifying all returnable containers with RFID will present further optimisation potential. Data from RICs can be used to streamline asset management. If each container can be identified and traced, container location becomes possible. The project manager: “If the container has a unique identifier, we can find out which containers are with us and which ones are with our customers. Tracking & tracing our reusable containers leads to cost reduction since the company will not have to repair or replace as many. We can reduce the time each container spends at the customer and increase availability. “ “The interest to use RFID within the company is growing, the project manager says: “together with Mieloo & Alexander we were able to tailor the RFID solution to the processes at the Rotterdam plant and comply with the SAP template. The smooth delivery of this new technology for the company and successful integration into the global ERP system has raised awareness for the benefits of RFID technology within the company, as well as with a number of the retailers using the containers.”