Duracell Belgium steekt power in innovatie
Belgische vestiging als modelbedrijf voor wereldwijde groep
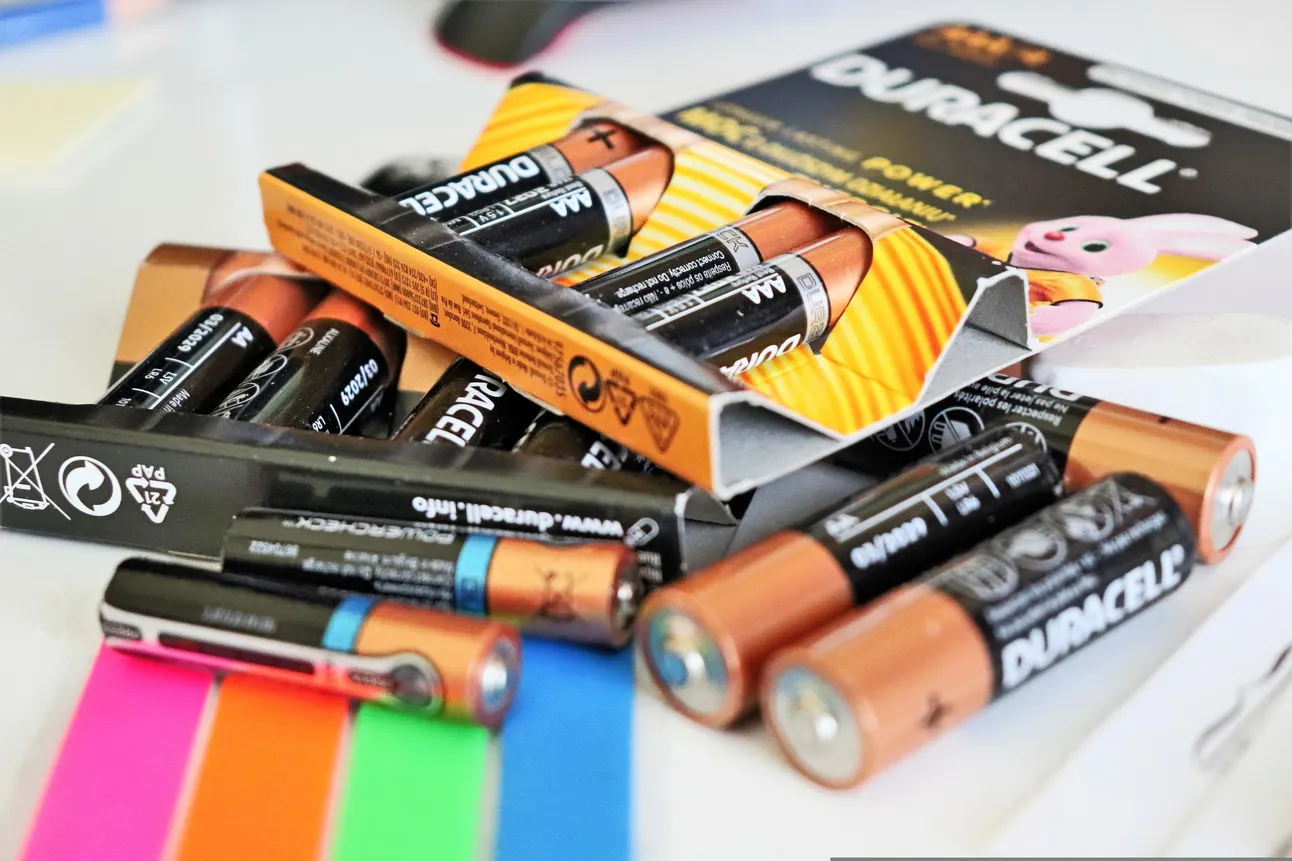
Al generaties lang is Duracell een begrip in ons land. De producent van alkalinebatterijen is sinds 1967 in België actief. Van de vier vestigingen die het bedrijf wereldwijd heeft, bevindt de enige Europese fabriek zich in Aarschot. Dankzij een digitale transformatie slaagde de vestiging erin om concurrentieel te blijven ten opzichte van haar Aziatische zusterbedrijven.
Innovatie vormt de rode draad doorheen de geschiedenis van Duracell. Het bedrijf maakte de batterijen almaar compacter, krachtiger, efficiënter en duurzamer. Daarnaast bedacht het ook unieke innovaties, zoals de Powercheck, waarbij gebruikers zelf het stroompeil in de batterijen kunnen controleren. En uiteraard kent zowat iedereen Duracell ook van de opmerkelijke tv-spotjes die het bedrijf in de loop van de jaren lanceerde; de term ‘Duracellkonijn’ is in Vlaanderen een bekend begrip. Het zorgde er allemaal voor dat Duracell wereldwijd uitgroeide tot een van de toonaangevende batterijmerken.
De vestiging van Duracell in Aarschot telt ruim 450 medewerkers en produceert alle AA- en AAA-alkalinemangaanbatterijen voor Europa, het Midden-Oosten en Afrika. De fabriek groeide de voorbije 55 jaar uit tot een hightech productievloer van maar liefst 42.000 vierkante meter, waar er dagelijks zes miljoen alkalinebatterijen van de band rollen.
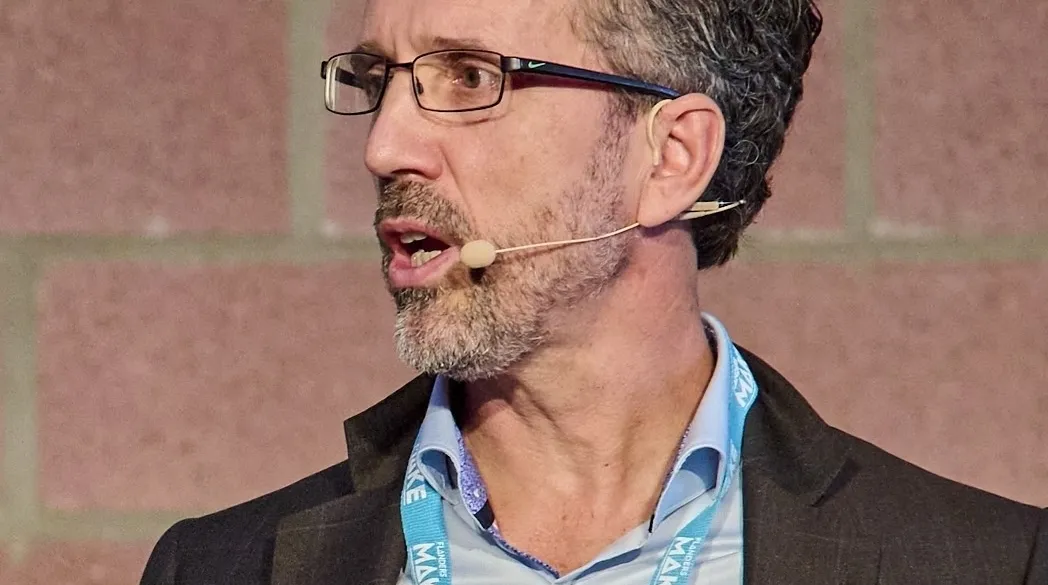
Concurrentie binnen de groep
Ondanks die indrukwekkende omvang en productiecijfers, pakten zich in 2013 donkere wolken boven de vestiging in Aarschot samen. De oorzaak hoeft niet te verbazen: de hoge loonkosten in België en de kosten in de globale supply chain maakten het voor Duracell Belgium, net als voor veel andere maakbedrijven in ons land, moeilijker om te concurreren met fabrieken in lageloonlanden, met Azië in het bijzonder.
Duracell Belgium mag dan wel belangrijk zijn voor de Europese markt, toch boette die positie aan belang in. Niet-bederfbare producten, zoals batterijen, zijn nu eenmaal goedkoop over heel de wereld te exporteren. De gevolgen lieten zich meteen voelen. Duracell Belgium schrapte driehonderd jobs en liep een investering van 75 miljoen mis. “We voerden een nieuw ploegensysteem in om onze rendabiliteit te verhogen, maar dat was onvoldoende om te kunnen concurreren met de lagere lonen in andere landen”, vertelt Jan Casteels, vicepresident bij Duracell Belgium. “Om onze competitiviteit te vergroten zouden pure besparingen niet volstaan. Onze output moest omhoog zonder de investeringen radicaal te verhogen en zonder extra mankracht.”
De vestiging zocht het antwoord in een doorgedreven digitalisering en automatisering van de activiteiten die niet voor toegevoegde waarde zorgden, gecombineerd met de versterking van de connectiviteit tussen de diverse departementen en functies.
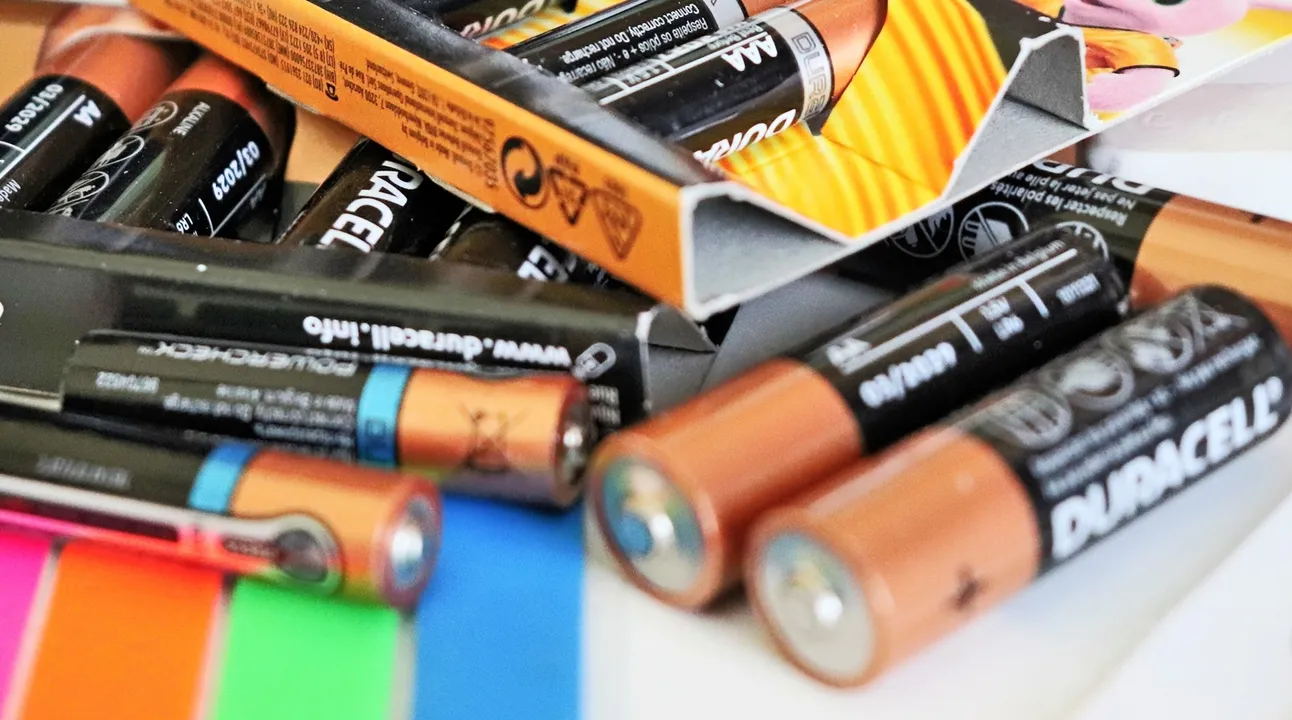
Uniek kenmerk
Voor de Europese markt was het nodig dat de productspecificaties scherper werden gedifferentieerd. De specificaties zijn cruciaal tijdens de productie en kwaliteitscontrole. Duracell Belgium besliste ze op één centraal platform te verzamelen. Op die manier kon het bedrijf een complexere productie aan in vergelijking met de zusterfabrieken. Het kan nu sneller en meer gericht ingrijpen wanneer er zich kwaliteitsproblemen voordoen.
Op vijf jaar tijd transformeerde de vestiging zichzelf tot een modelbedrijf voor Duracell wereldwijd. “De digitalisering en automatisering van het productieproces vormen ons ‘unique selling point’ ten opzichte van de concurrent, maar ook ten opzichte van de andere vestigingen in de groep”, zegt Jan Casteels. In vergelijking met de andere vestigingen van Duracell is in Aarschot meer hoogopgeleid personeel aan het werk. In combinatie met de zin voor innovatie hielp dat Duracell Belgium om zijn achterstand om te buigen in een voorsprong.
Slimme productie
Vandaag is de fabriek in Aarschot de meest innovatie uit de hele groep.
Jan Casteels: “Tijdens het volledige productieproces generen we data: uit de productielijnen, uit het MES (manufacturing execution system), uit de kwaliteitscontrole en uit het ERP-systeem (enterprise resource planning). Al die gegevens komen in één visueel overzicht terecht, in real time geconsolideerd.”
Na de digitalisering en het combineren van alle bedrijfsinformatie op één platform wil Duracell ook het kwaliteitsmanagement verder versnellen, vooral met het doel productieverliezen te verminderen. “Sensoren worden goedkoper en veelzijdiger en zijn makkelijker in het productieproces te integreren”, vertelt Jan Casteels. “Steeds meer meetpunten zullen het productieproces continu monitoren. Door sensorsignalen te verzamelen en te analyseren – door middel van ‘machine learning’ – maken we de overgang van reactief naar preventief onderhoud. Die datagedreven aanpak zorgt bovendien voor een betere beheersing van de productiekwaliteit.”
Slimme productielijnen zorgen intussen voor de permanente monitoring van vijftien kwaliteitsparameters. Daarvoor zet Duracell Belgium slimme camera’s in: niet onlogisch bij een dagelijks productievolume van zes miljoen batterijen.
J. Casteels: “In plaats van steekproeven te controleren, kunnen we met de slimme camera’s alle batterijen grondig bekijken. Het leverde een systeem van honderd procent kwaliteitscontrole op, waaruit opnieuw heel wat bruikbare data voortvloeien.”
Voorspellend onderhoud
De grote datastromen die het productieproces genereert, bevatten heel wat informatie, en niet alleen over de kwaliteit van de baterijen. Zo is Duracell Belgium zich de laatste jaren sterk gaan focussen op ‘predictive maintenance’ of voorspellend onderhoud. Daarmee slaagt het bedrijf erin de onderhoudswerken op het juiste moment te voorzien, waardoor het de machines zo min mogelijk onnodig stil hoeft te leggen. Door artificiële intelligentie (AI) te gebruiken, is het mogelijk te voorspellen wanneer de machines onderhoud nodig hebben, nog voor er zich problemen voordoen.
Dat Duracell Belgium volop overtuigd is van het potentieel van data en AI, bewijst ook het plan om in de toekomst meer data-analisten en minder onderhoudstechnici aan te trekken.
J. Casteels: “Het is een sprong in het diepe, maar we hebben er het volste vertrouwen in dat we goed terecht zullen komen. Op termijn zullen we dankzij onze investeringen in AI en automatiseringsvaardigheden ons onderhoud verbeteren en zo onze capaciteit verhogen.”
Verder wil het bedrijf ook mee aan de kar trekken van fundamenteel onderzoek rond het gebruik van AI in een productiecontext. “We werken voor verschillende projecten samen met de KU Leuven en het voorbije jaar zijn we gestart een nieuw initiatief samen met VLAIO en Sirris”, illustreert Jan Casteels. “We willen AI gebruiken om ons automatisch aan te passen aan eventuele contextuele verstoringen van onze productieprocessen.”
Digital twin
Het huidige gebruik van data is voor Duracell maar het topje van de ijsberg. Door de vele gegevens die het bedrijf tijdens de productie verzamelt, krijgt elke batterij een virtuele tweeling of ‘digital twin’: een verzameling van datapunten, vastgelegd door de slimme camera’s en laserscanners.
Tijdens de fabricage ondergaat een batterij negen transformaties, cruciaal voor de kwaliteit van het eindproduct. Dankzij de digital twin zal het niet meer nodig zijn om achteraf willekeurige batchmonsters te nemen om in het lab te testen. De automatische controle op de data van elke batterij volstaat. Op die manier kunnen operatoren zeer snel in het proces ingrijpen en zo verspilling voorkomen.
AGV’s
Om de efficiëntie van het productieproces te verhogen zonder in extra medewerkers te investeren, keek Duracell ook al snel in de richting van AGV’s (automated guided vehicles) om activiteiten met minder toegevoegde waarde, zoals het eenvoudig verplaatsen van goederen, te automatiseren. “Het was een uitdaging om de AGV’s te integreren met het bestaande automatiseringsproces in de warehouses, maar uiteindelijk zorgden ze wel voor een duidelijke meerwaarde”, blikt Jan Casteels terug. Terwijl de AGV’s automatisch goederen verplaatsen, komt er bij de medewerkers tijd vrij die ze kunnen besteden aan activiteiten die wel een meerwaarde hebben.
Verdere data-uitwisseling
De voorbeelden tonen aan welke weg Duracell Belgium intussen al heeft afgelegd. Voor het bedrijf bestaat de uitdaging er nu in de genomen voorsprong ook te behouden.
J. Casteels: “We hebben een traject voor vijf jaar uitgestippeld. De focus zal er nu vooral op liggen het dataplatform verder uit te werken. We willen het nog uitbreiden, door het niet alleen bij de productieafdeling in te zetten, maar ook om er voordelen mee te behalen bij onze ondersteunende diensten. Vooral de R&D- en engineeringafdeling zullen daarbij winnen.”
Maar Duracell Belgium kijkt ook verder dan de eigen vestiging. “We breiden ons platform ook uit om met klanten en leveranciers informatie uit te wisselen. Op die manier zullen we niet enkel binnen de fabriek geconnecteerd zijn, maar in de hele supply chain”, zegt Jan Casteels. Ook het gebruik van de digital twin staat vandaag nog in zijn kinderschoenen. “Er valt nog steeds winst te boeken op de kwaliteit van de batterijen. En ook de kwaliteitscontrole willen we nog verder digitaliseren aan de hand van een voorspellingsmodel. Het is een kwestie van meer data verzamelen en zo het machine learning-algoritme steeds meer te voeden.”
Mentaliteitswijziging
Ondanks de toenemende graad van digitalisering wijst Jan Casteels erop dat het vijfjarenplan pas voluit succesvol kan zijn als alle medewerkers mee hun schouders onder de innovatie zetten. “We hebben heel hard ingezet op change management om alle medewerkers mee te krijgen in het verhaal. Speciale innovatieteams inspireerden de medewerkers, opdat ze de vernieuwingen volop zouden omarmen.”
Vermeldenswaardig is dat de zoektocht naar innovatie Duracell niet noodzakelijk naar de andere kant van de wereld leidde. Zo is het gebruik van slimme camera’s voor kwaliteitscontrole een Vlaamse oplossing. Hetzelfde geldt voor een toepassing van ‘laser cleaning’ die Duracell inzet om batterijcellen te reinigen. “Dat gebeurde vroeger met de hand, wat erg tijdrovend was en voor weinig toegevoegde waarde zorgde”, meent Jan Casteels. Na de opties te hebben afgewogen – zoals schoonmaken met stoom en CO2 – bleek laser cleaning niet alleen de snelste, maar ook meest milieuvriendelijke methode. “Zo tonen we ook aan dat je niet altijd naar de andere kant van de wereld hoeft om partners te vinden. Hier in Vlaanderen beschikken we over enorm veel expertise en innovatiepotentieel”, klinkt het.
Voor maakbedrijven, zeker in België, komt het er volgens Jan Casteels vandaag vooral op voldoende lef te hebben. Ze moeten de juiste stappen durven zetten. “Het is een proces van vallen en opstaan”, besluit hij. “Probeer niet op voorhand je hele visie gedetailleerd uit te tekenen en te engineeren, maar begin met één project. Identificeer waar je verliezen zitten. Als je eenmaal een aantoonbare en succesvolle evolutie hebt doorgemaakt, kom je in een positieve spiraal van innovatie terecht. En dan is ‘the sky the limit’.”