Distrivers registreert exacte kratinhoud in Distrib WMS
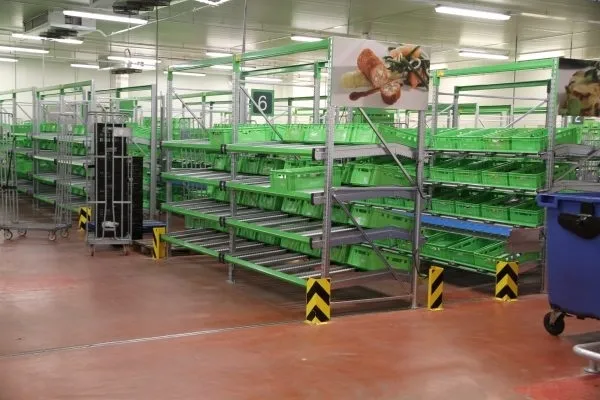
Elke dag opnieuw zorgen bijna tachtig mensen van Distrivers ervoor dat zorginstellingen uit heel Nederland het eten en drinken ontvangen dat ze hebben besteld. De foodgroothandel uit Hoogeveen gebruikte daarvoor jarenlang een systeem, dat vanwege het groeiende aantal klanten niet langer voldeed. Bovendien wilde Distrivers graag een systeem dat tracking & tra-cing van producten op kratniveau kon ondersteunen. De oplossing werd gevonden in een nieuw logistiek concept gebaseerd op het Put to Light en WMS van Pcdata. Het resultaat: een productiviteitsstijging van twintig procent, flinke ruimtewinst, minder fouten en een waterdichte registratie van de kratinhoud.
Distrivers werkt al sinds 2003 met Put to Light van Pcdata. De groothandel uit Hoogeveen gebruikt deze technologie om elke dag honderden zorginstellingen zoals ziekenhuizen en verzorgingshuizen te voorzien van lekker eten en drinken.
De veelal dagverse producten en kant-en-klaarmaaltijden worden in de loop van de dag aangevoerd in het distributiecentrum en nog diezelfde dag verdeeld over klanten in heel Nederland. Elke klant wordt gekoppeld aan een Put to Light display, dat voor elk artikel aangeeft hoeveel stuks de klant heeft besteld. In de loop der jaren voldeed het Put to Light systeem met 288 displays uit 2003 steeds minder goed. Oorzaak was niet alleen de groei van het aantal klanten, maar vooral ook het opsplitsen van orders door diezelfde klanten. Instellingen en ziekenhuizen die beschikken over meerdere afdelingen met elk hun eigen keuken, willen vandaag de dag hun orders per keuken of afdeling uitgeleverd krijgen. Wat vroeger één grote klant was, zijn tegenwoordig soms wel 10 of 20 kleine klanten. Daarnaast ontbrak een waterdicht systeem voor het registreren van de inhoud van kratten. De gevolgen: te weinig ruimte, te veel fouten, een gebrekkige tracking & tracing en bovenal een inefficiënte operatie. “Om alle klanten te bedienen moesten we in twee waves werken. Klanten met een bestelling van maar drie kratten hielden een complete grondlocatie bezet”, vertelt Sietse Buutkamp, operationeel manager van Distrivers. “Sommige medewerkers legden op een dag soms tien kilometer af langs alle Put to Light locaties”, zegt Richard Blauwwiekel, assistent operationeel manager van Distrivers.
2 jaar geleden besloot Distrivers op zoek te gaan naar een andere oplossing. Buutkamp en Blauwwiekel onderzochten de mogelijkheden van verschillende mechaniserings- en automatiseringsoplossingen maar beland-den uiteindelijk toch weer bij Pcdata, leverancier van het Put to Light systeem. Pcdata ontwikkelde een compleet nieuw logistiek concept, wederom op basis van Put to Light en het warehouse management systeem Distrib. “We wisten wat we hadden, en dat was in principe goed. Door opnieuw Put to Light te gebruiken, hoefden we bovendien onze mensen niet opnieuw in te werken”, stelt Buutkamp.
In het nieuwe logistieke concept is het verdeelproces opgesplitst in 2 stappen: een voorverdeling en een eindverdeling. Alle producten worden eerst voorverdeeld over 12 eindverdeelstations, waarna ze per eindverdeelstation over de klanten worden verdeeld. Voor de voorverdeling zijn dichtbij de ontvangstafdeling 5 voorverdeelstations met 12 Put to Light displays ingericht. Elk display is direct gekoppeld aan één van de 12 eindverdeelstations.Voor elk artikel toont het display het totaal aantal stuks dat op het betreffende eindverdeelstation moet worden verwerkt. Dat aantal wordt in een krat onder het display geplaatst. Elk eind-verdeelstation bestaat uit 2 tegenover elkaar geplaatste doorrolstellingen, die per zone ruimte bieden aan 64 locaties, verdeeld over 4 niveaus.Het grote voordeel van de nieuwe werkwijze is dat de volle kratten tijdens de voorverdeling al uit het verdeelproces worden gehaald. Deze kratten, 70% van het totale volume, worden al op de voorverdeelstations gelabeld en direct naar de expeditieafdeling gebracht. “Dat zorgt voor een enorme ontlasting van de eindverdeelstations”, aldus Blauwwiekel.
Distrivers start nu elke ochtend om 5.30 uur met het voorverdelen van de producten. Als om 15.00 uur alle orders voor de volgende dag binnen zijn, komt ook de eindverdeling in een stroomversnelling terecht. Tot 21.00 uur is het dan spitsuur bij Distrivers, ook omdat een grote stroom producten zoals vlees en kant-en-klaarmaaltijden pas in het begin van de avond vanaf de eigen productielocaties van Distrivers worden aangevoerd.
Op de voor- en eindverdeelstations maakt Distrivers gebruik van barcodescanning. Pas nadat een artikel is gescand, toont de terminal om welk artikel het gaat en branden de displays van de klanten die het artikel hebben besteld. Dankzij deze werkwijze is de kans op fouten minimaal. In het oude Put to Light systeem moesten de eindverdelers de artikelen nog handmatig selecteren op een scherm. Met artikelen die sterk op elkaar lijken en soms alleen in gewicht verschillen, is een fout dan snel gemaakt. Tijdens de eindverdeling registreert het WMS Distrib van Pcdata exact welke producten in welke krat belanden. Als een krat vol is, kan de eindverdeler met een druk op een knop een barcodelabel printen waarop de volledige kratinhoud vermeldt wordt. Het registreren en labelen van de exacte kratinhoud is daardoor een fluitje van een cent geworden. Dat stelt Distrivers niet alleen in staat om op kratniveau te kunnen tracken en tracen, maar biedt ook voordelen voor de klant. “Die hoeven niet eerst drie rolcontainers met kratten te doorzoeken als ze een bepaald product willen hebben. Ze kunnen aan het label zien wat in de kratten zit”, aldus Blauwwiekel.
Nu het verdeelproces draait, wil Distrivers het consolidatieproces op de werkvloer aanpakken. Daar moeten nu alle kratten uit de eindverdeelstations per klant worden samengevoegd met de volle kratten die rechtstreeks van de voorverdeelstations komen. “Dan willen we ook Distrib Dock manager van Pcdata implementeren. Met dat systeem kunnen we de kratten en rolcontainers door barcodescanning niet alleen aan de klanten, maar ook aan de vrachtauto’s koppelen. Dan weten we zeker dat de juiste producten in de juiste auto zitten”, vertelt Buutkamp.
Driehonderd manuur
Dankzij het nieuwe concept zijn de uitbreidingsplannen van Distrivers voorlopig weer in de la verdwenen. “Eerst hadden we 288 Put to Light locaties op een oppervlakte van 600 vierkante meter, nu 768 locaties op 400 vierkante meter. De operatie past weer in het pand”, aldus Buut-kamp. Naast het ruimtegebrek is ook het productiviteitsprobleem opgelost. De loopafstanden zijn tot een mini-mum beperkt, waardoor Distrivers 300 manuur per week bespaard op het verdeelproces. “Dat komt neer op een reductie van 20%. Daarvoor is wel een goede planning vereist. De kunst is om de eindverdelers continu aan het werk te houden. Als ze gaan voorlopen op de voorverdelers, gaat dat ten koste van de efficiëntie”, stelt Buutkamp, die verwacht dat de leverbetrouwbaarheid uiteindelijk uitkomt op 99,9%. Tot slot is ook een waterdicht systeem voor tracking en tracing op kratniveau ontstaan. Volle kratten worden al op de voorverdeelstations voorzien van een barcodelabel, de andere kratten krijgen in de eindverdeelstations een label met inhoud erop. Sietse Buutkamp, operationeel manager Distrivers: “Klanten hoeven niet langer drie rolcontainers met kratten te doorzoeken als ze een product willen hebben. Ze kunnen op het label zien wat er in de kratten zit.”
Volgens Buutkamp is de goede samenwerking met Pcdata één van de redenen voor het succesverhaal.
“Omdat we elkaar zo goed kennen, kunnen we snel schakelen. Een half jaar na de start van het project hebben we het systeem in gebruik genomen. Het warehouse is in één weekend volledig opnieuw ingericht. Veel sneller had dat allemaal niet gekund. Dat lukt alleen als je als partners optrekt.”