Digitale transformatie ondersteunt groei
Didak Injection gaat voor automatisering met geïntegreerd WMS en MES
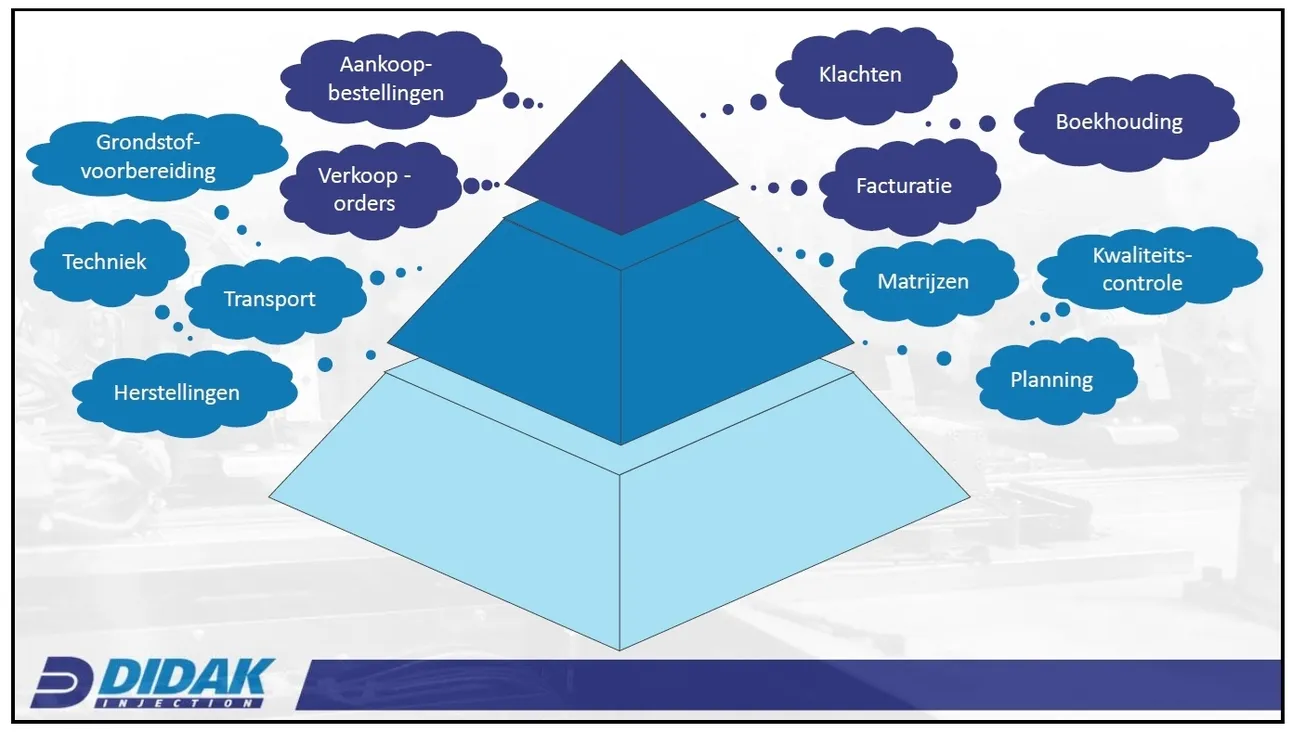
Wat doe je als groeien steeds moeilijker wordt? Met die prangende vraag worstelde het kunststofproductiebedrijf Didak Injection in 2018. Een van de verlossende antwoorden luidde toen: maximaal automatiseren. Zo gezegd, zo gedaan. Vandaag zorgt een geïntegreerde WMS- en MES-oplossing mee voor de digitale transformatie van het spuitgietbedrijf. “Pen en papier zijn bij ons definitief verleden tijd”, klinkt het.
Didak Injection, gevestigd in het Kempense Grobbendonk, legt zich al meer dan een halve eeuw toe op de productietechniek van het kunststofspuitgieten. Het bedrijf produceert volcontinu, zeven dagen op zeven, in een vijfploegensysteem. In het kader van dat productieproces verbruikt Didak Injection zo’n 25.000 ton aan materiaal per jaar, waarvan een kwart gerecycleerd is. Het spuitgietbedrijf beschikt ook over eigen installaties om bestaande kunststoffen te vermalen voor hergebruik in nieuwe producten.
Naast standaardproducten, meer bepaald herbruikbare en stapelbare bakken en kratten, levert Didak Injection ook honderd procent maatwerk, zowel voor het ontwerp als voor het productieproces. Ook voor de bouw en het onderhoud van de matrijzen biedt het bedrijf een totaalservice. “We stellen een achttal specialisten tewerk in onze matrijzenafdeling, met eigen atelier voor revisies en herstellingen. We hebben ook een vijftiental spuitgietexperts in dienst. Onze logistieke afdeling telt vandaag zes medewerkers”, vertelt Andy Buelens. Sinds begin 2022 is hij als plant manager verantwoordelijk voor het beheer van het machinepark. Voordien stond hij als hoofd Administratie jarenlang ook in voor het ICT- en het kwaliteitsbeheer van het ISO-gecertificeerde productiebedrijf.
“In totaal hebben we momenteel een 180-tal personen in dienst, maar we zijn nog continu aan het groeien”, vertelt CEO Peter Verbist. Met de groei komen natuurlijk ook de uitdagingen. “In 2018 waren we op een punt gekomen dat we wel nog wilden, maar niet meer konden groeien. Puur fysiek en geografisch zaten we op onze bestaande locatie gewrongen tussen het Albertkanaal, de E313, nog een andere grote weg en een buurbedrijf.”
Masterplan 2018-2023
In 2018 zat Didak Injection letterlijk krap bemeten in groeicapaciteit. Een capaciteitsuitbreiding drong zich op. Om die tot een goed einde te brengen, nam het spuitgietbedrijf adviesbureau Logflow in de arm. “Samen met de consultants hebben we toen een masterplan voor vijf jaar uitgewerkt. Daarin formuleerden we een concreet en helder antwoord op de vraag: waar staan we vandaag en waar willen we over vijf jaar staan?”
In dat vijfjarenplan identificeerde Logflow vier strategische pijlers waarop Didak Injection moest focussen om zijn groei te bestendigen. Een eerste pijler was het groeien van de omzet. Marktstudies en investeringen in sales en branding moesten die omzetgroei helpen realiseren. De tweede pijler betrof de eigenlijke uitbreiding van de capaciteit. “Bij die oefening zijn we tot de conclusie gekomen dat we onze productiecapaciteit niet konden verhogen, zonder een deel van onze activiteiten van de bestaande site weg te halen”, herinnert Andy Buelens zich. “Uiteindelijk hebben we onze volledige logistieke activiteit verhuisd en in een aparte opslagruimte een viertal kilometer verderop ondergebracht. Op onze bestaande site beperken we onze activiteiten nu tot de productie.” Om die te optimaliseren, liet Didak Injection bestaande gebouwen afbreken en productiehallen (her)opbouwen. Tegelijk investeerde het in nieuwe machines. Intussen telt het productiepark 41 machines. Dit jaar komen er nog eens vier bij.
De derde strategische pijler bestond in het optimaliseren van de rendementen. Zo kampte Didak Injection met een te groot aantal verloren minuten en een te beperkt inzicht in het eigen productieproces.
Andy Buelens: “Wij hadden niet echt een zicht op waar wij precies aan efficiëntie verloren, waar de bottlenecks zaten en waar wij dus aan rendement inboetten. Dat was voor ons een grote grijze zone. Om het productieproces te optimaliseren, raadden de consultants ook aan het ‘first-time-right’-principe (FTR) uit de Lean Six Sigma-methodiek toe te passen. Alles moet meteen goed zitten. Alle parameters van de machine moeten correct zijn. De grondstoffen moeten in orde zijn. Voor 2018 kwam er te veel nattevingerwerk bij kijken, te veel eigen receptuur van de medewerkers zelf. Maar als de receptuur niet juist zit, komt heel de productie in gevaar. Het volstaat dat één of twee parameters afwijken, en je krijgt niet het gewenste product.”
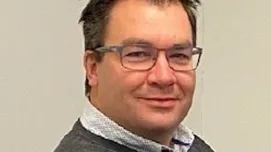
Maximaal automatiseren
De vierde en laatste pijler van het masterplan was maximale automatisering. “We hebben de afgelopen jaren in een geïntegreerde WMS- en MES-oplossing geïnvesteerd. Daarmee hebben we ons voorraadbeheer en ons productieapparaat alvast naar een hoger niveau getild. Daar plukken we vandaag al de eerste vruchten van.” Om ook het verpakkingsproces verder te stroomlijnen, plant Andy Buelens dit jaar nog een automatische wikkelstraat aan dat rijtje van strategische investeringen toe te voegen. Als alles goed gaat, staat er in 2023 ook een investering in automatisch geleide voertuigen, kortweg AGV’s, op het programma.
In zijn zoektocht naar een geschikte leverancier voor het geïntegreerde WMS (warehouse management system) en MES (manufacturing execution system) kwam Didak Injection al gauw bij Objective International uit. De softwareontwikkelaar uit het Oost-Vlaamse Wichelen levert niet alleen poort-tot-poort-oplossingen aan productiebedrijven, maar integreert ze ook zelf bij zijn klanten. “De keuze voor Objective kwam er vooral door het vertrouwen dat de leverancier bij ons opwekte”, weet Andy Buelens. “De mensen met wie we rond de tafel zaten, verplaatsten zich effectief in onze situatie en dachten met ons mee. Bovendien behoedden ze ons ervoor volledig in maatwerk te vallen.”
Didak Injection wil namelijk zoveel mogelijk binnen de standaard werken. “Wanneer Objective naar een volgende versie van zijn Product Suite overgaat, willen we vrij eenvoudig kunnen meegaan. Maar tegelijk wilden we toch ook onze eigenheid voldoende weerspiegeld zien in zo’n standaardprogramma”, merkt Andy Buelens op. “Aan die wens is Objective tegemoetgekomen. Tijdens de analysefase bleek dat de spuitgietbranche voor hen relatief onbekend was, maar al gauw realiseerden zij zich dat onze problematiek in wezen ook die van alle andere spuitgietbedrijven was. Daarop heeft Objective het besluit genomen om voor onze business een extra ‘vertical’ te creëren. Samen hebben we vervolgens naar oplossingen gezocht voor alle specifieke, typische functionaliteit die toen nog niet in hun standaard zat, maar intussen mee erin is opgenomen.”
1 oplossing, 2 systemen
Dat het geïntegreerde aanbod van Objective de volledige scope van logistiek en productie kan omvatten, speelde uiteraard ook mee in de keuze van Didak Injection. “Eerlijk gezegd hadden we in eerste instantie wel gekeken of we niet vanuit ons ERP-systeem konden werken en dat centrale pakket gewoon rechtstreeks aanvullen met een WMS- en een MES-systeem”, bekent Andy Buelens. In zijn streven naar verbetering had Didak Injection zijn vroegere ERP-pakket al ingeruild voor SAP Business One. “Maar we vreesden dat we de volledige scope aan functionaliteit die we voor onze productie en logistiek voor ogen hadden, toch niet in SAP zouden terugvinden.”
Didak Injection gebruikt het ERP-systeem van SAP voor administratieve en boekhoudkundige taken, zoals de verwerking van aankoopbestellingen, verkooporders, klachten en facturen. De geïntegreerde WMS- en MES-oplossing van Objective ondersteunt dan weer een brede waaier aan operationele taken die de productie en logistiek vormgeven en ondersteunen: van planning, grondstofvoorbereiding en kwaliteitscontrole tot techniek, transport en herstellingen. “Alleen het luik dat betrekking heeft op de bouw en het onderhoud van matrijzen moeten we nog afsluiten. Al de rest is intussen opgeleverd. En daarover kunnen wij nu al besluiten dat de samenwerking met Objective ons een grote meerwaarde heeft opgeleverd”, klinkt het.
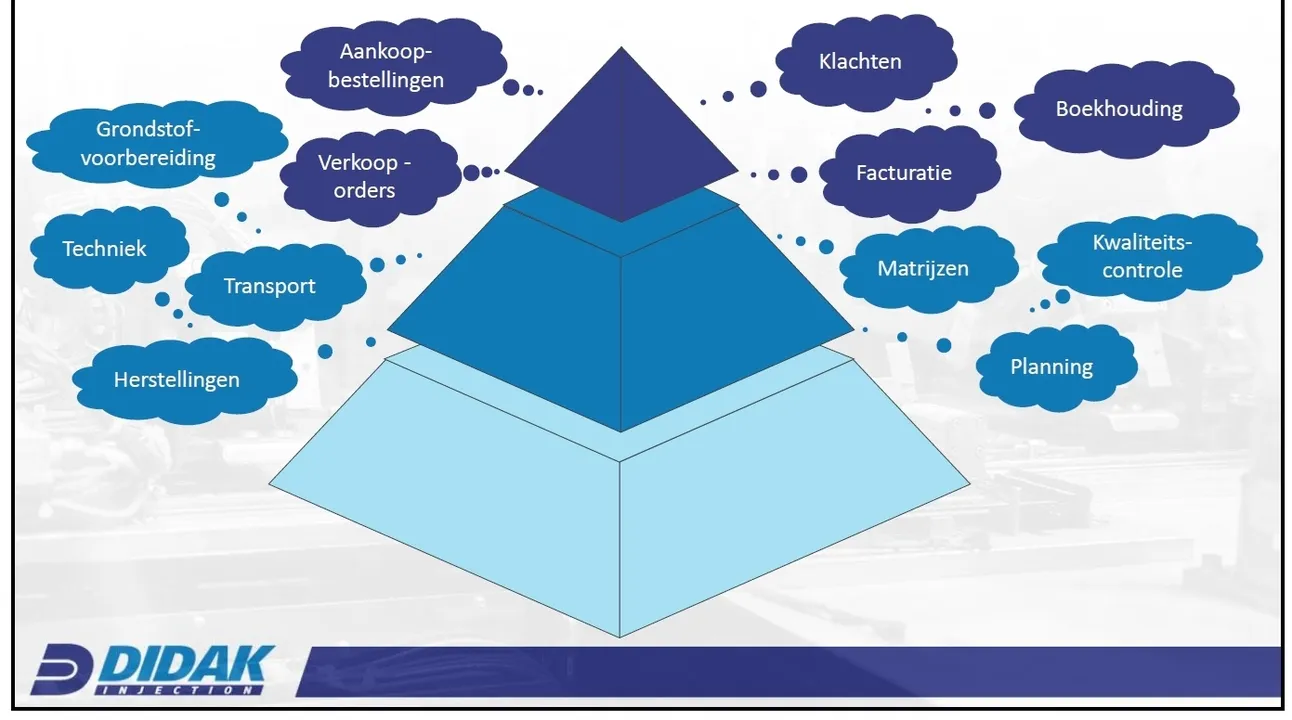
Flexibel, betrouwbaar en transparant
De opgesomde operationele taken verliepen vroeger grotendeels manueel. “We werkten bij manier van spreken nog met pen en papier”, zegt Andy Buelens. “De nadelen van dat gebrek aan automatisering waren helaas legio. Onze verouderde aanpak bracht onder meer soms tekorten met zich mee, die zich concreet konden vertalen in stockbreuken en uiteindelijk zelfs in productiestops. We wisten ook niet altijd precies waar ons materiaal zich bevond of opgeslagen was. Kostprijscalculaties in het kader van offertevoorbereidingen gebeurden met oude, onjuiste data. En nacalculaties deden we hoegenaamd niet. Wat rapportering betreft, was het fragmentatie troef: elke afdeling had zo haar eigen Excel-, Access- of zelfs Word-bestand om in te rapporteren. Verwachte rendementen bleken vaak onjuist ingeschat. En traceerbaarheid realiseren was al helemaal een huzarenstukje.”
Vandaag ziet het operationele plaatje er totaal anders en vooral stukken gunstiger uit. “Niet alleen is onze voorraad steeds up-to-date, hij is ook voor meer dan 99 procent correct en betrouwbaar”, weet Andy Buelens. “De dagelijkse manuele voorraadtellingen in het magazijn zelf hebben intussen plaats geruimd voor automatische voorraadcontroles op afstand. Alle nodige kennis hoeft ook niet langer van onze mensen zelf te komen: we kunnen alle operationele data op elk moment en vlugger dan ooit tevoren uit onze systemen halen voor automatische analyse. Zo vergt het opvragen van informatie over traceerbaarheid nog maar een simpele druk op een knop.”
“Tegenwoordig doet zich zelfs eerder het omgekeerde voor”, vervolgt Andy Buelens. “Zo zijn het steeds vaker de logistieke en productiesystemen die onze medewerkers aansturen, niet andersom.” Het zorgt ervoor dat Didak Injection zijn logistiek – dankzij de implementatie van het WMS – met een kleiner team aanstuurt. “Maar de belangrijkste winst is toch wel dat we naast flexibeler en betrouwbaarder ook merkelijk transparanter zijn geworden in onze operaties. We weten vandaag een pak meer en hebben een duidelijker zicht op onze productie en logistiek: op wat er goed gaat, maar vooral ook op wat er fout loopt en mogelijk beter kan. Dat alles maakt dat we die productie en logistiek nu ook efficiënter, doelgerichter en in real time kunnen aansturen en opvolgen.”
JDP
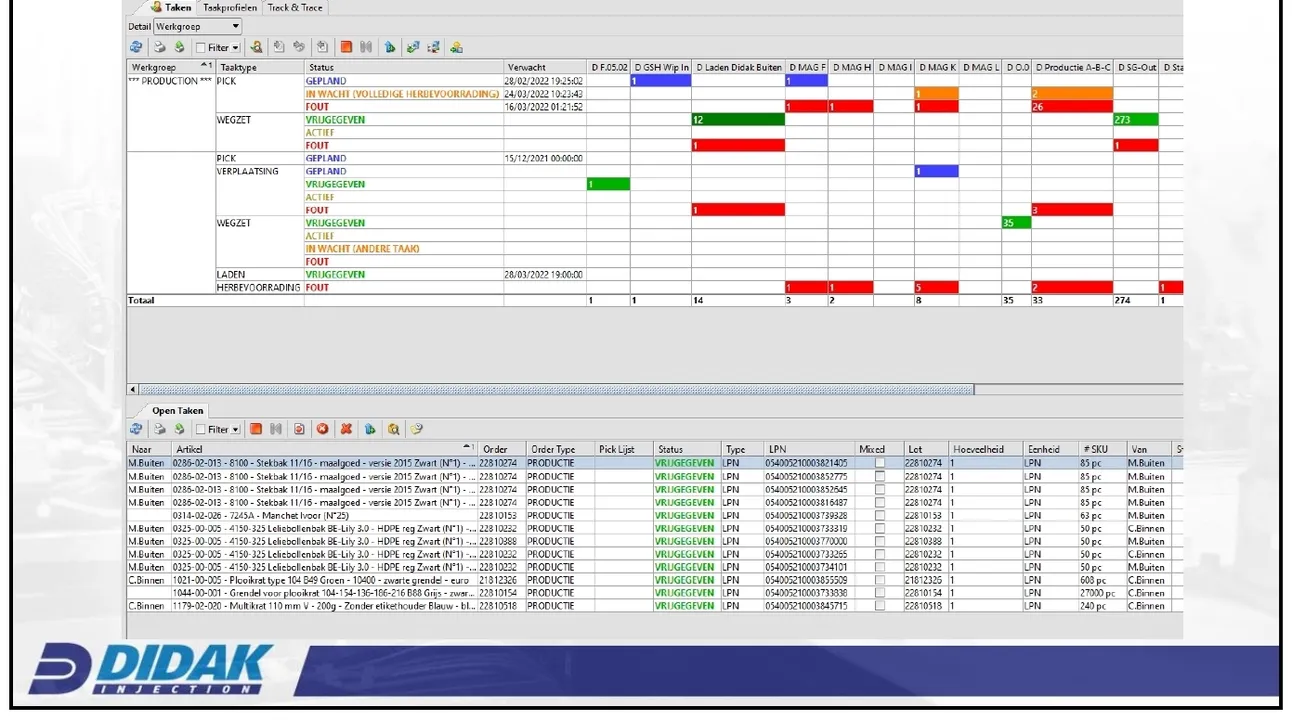