De weg van seriële naar parallelle planning
Brisa Bridgestone stroomlijnt operaties met ICRON
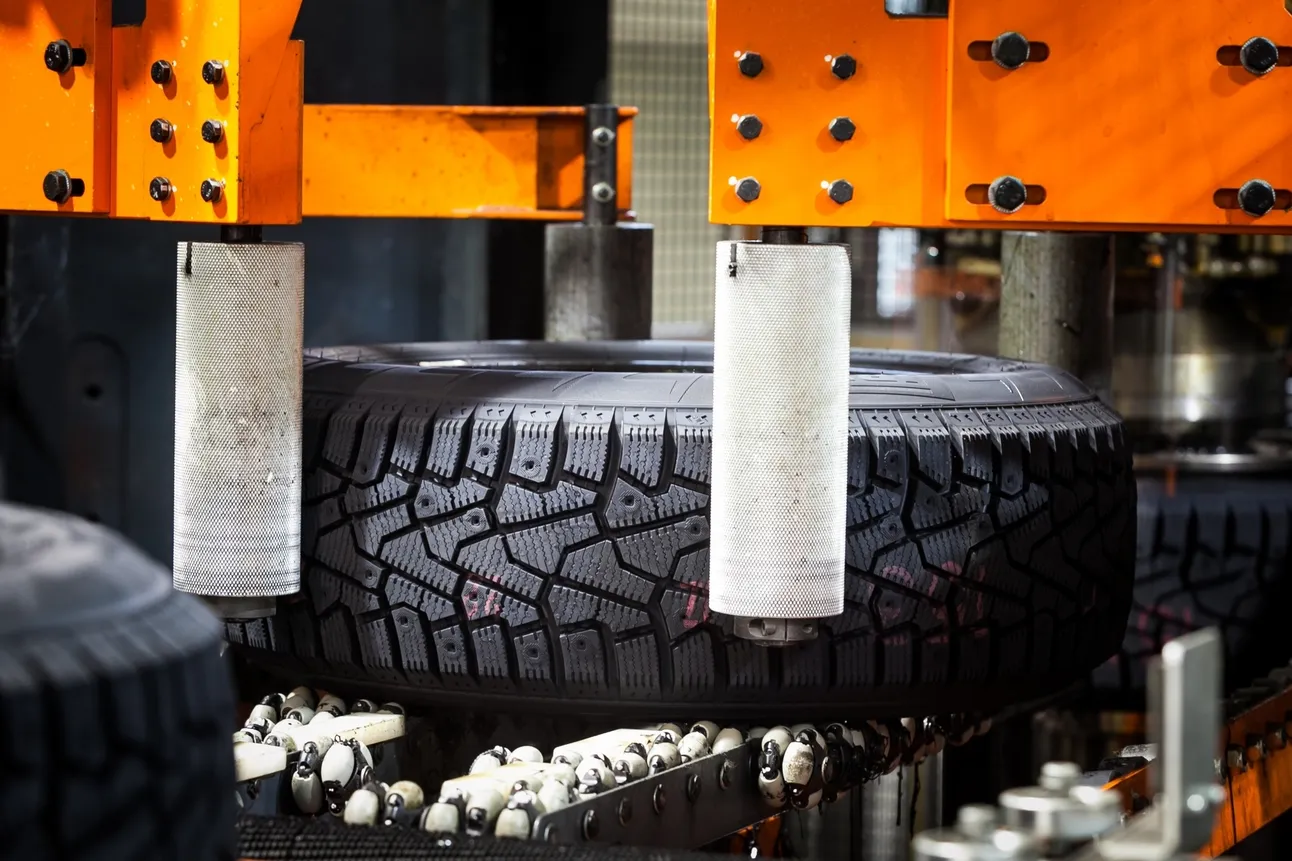
Tien procent meer productiecapaciteit. Dat is een van de belangrijkste resultaten sinds de optimaliseringssoftware van ICRON zijn intrede deed bij Brisa Bridgestone. Daarnaast kan het productiedepartement nu ook meer diverse orders vlotter aan. Wat begon als het zoeken naar een tool om een solide planningsbasis voor de productieactiviteiten te scheppen, is intussen uitgegroeid tot een partnership dat ‘continuous improvement’ nastreeft. Tekst en uitleg bij de samenwerking krijgen we van Murat Hepdurluk, directeur Industrial Engineering bij Brisa Bridgestone, en Alfred den Besten, vice president Global Marketing bij ICRON.
Brisa Bridgestone verkoopt een uitgebreid gamma aan banden in Turkije en ver daarbuiten (zie extra). Brisa’s fabriek in Kocaeli beslaat maar liefst 361.000m² en is daarmee wereldwijd een van de belangrijkste productiesites binnen de Bridgestone Corporation.
Om winstgevend te blijven, hebben bandenproducenten er vandaag alle baat bij dat ze hun supply chain zo goed mogelijk stroomlijnen. Helaas zijn ook zij niet gevrijwaard van een hobbelig parcours als ze dat doel willen bereiken. Veel heeft te maken met het zeer complexe en competitieve landschap waarin bandenproducenten zich bewegen. “Sommigen denken wel dat een band ‘maar een band’ is, maar niet is minder waar. Er komen steeds meer verschillende types wagens die vaak andere banden vragen. Ook het aantal soorten banden neemt gestaag toe: zomerbanden, winterbanden, ‘intermediate’ banden, snelle en meer duurzame exemplaren, enzovoort”, legt Murat Hedurluk uit.
Stroomlijnen binnen complexe structuur
Net als andere fabrikanten moet ook Brisa Bridgestone met die uitdagingen omgaan. Als we de globale structuur van Brisa’s productienetwerk bekijken, dan kunnen we vier geconnecteerde shops onderscheiden, met name het mixproces, het componentenproces, de sampling en de moulding. Daarbij vormt het eindproduct van één shop het startproduct van de volgende shop. Gaat er iets fout in het mixproces, dan komen dus ook de andere processen in het gedrang. Hoewel de vier shops hun eigen unieke interne plannings- en productieprocessen hebben, moeten ze heel goed op elkaar afgestemd zijn om het juiste product op het juiste tijdstip aan de klant te kunnen leveren. Immers, van zodra het eerste proces is ingezet, is er geen weg terug.
Murat Hedurluk: “Op een bepaald moment begonnen de stijgende volumes en de groeiende diversiteit van producten en klanten ons vanuit planningsperspectief parten te spelen binnen die structuur. De hoge complexiteit in combinatie met een gebrek aan coördinatie maakten het extreem moeilijk voor ons planningsdepartement om werkbare productieschema’s te creëren. We moeten rekening houden met tig factoren en af en toe liep het wel eens fout. Gebrekkige productieschema’s leidden geregeld tot onderbrekingen in het productieproces, wat betekende dat machines op een ander moment opnieuw moesten worden opgestart. Soms moest de machine dan gereinigd worden, wat voor extra vertraging zorgde. Bovendien betekenden verschuivingen soms problemen op het vlak van personeel, aangezien niet elke productiemedewerker eender waar en wanneer kan worden ingezet.”
Die problemen kwamen vooral tot uiting in het ‘second line’ klantensegment, zijnde de distributienetwerken waarbij klanten naar de garage of winkel stappen voor één of meerdere nieuwe banden. Immers, als een klant geen band van zijn favoriete merk kan krijgen, is hij meestal wel bereid om een ander merk op zijn wagen te laten leggen, waardoor de verkoop onverbiddelijk gemist wordt. In het meer voorspelbare ‘first line’ segment, waarbij de banden rechtstreeks door autoproducenten worden aangekocht om op hun voertuigen te plaatsen, is goed plannen minder moeilijk. Wel is het ook in dat segment erg belangrijk om te weten hoe je prioriteiten op het niveau van de klant kunt rijmen met een zo efficiënt mogelijke planning.
In een poging het productieproces te helpen vereenvoudigen, probeerde het verkoopdepartement van Brisa Bridgestone de diversiteit van de producten binnen de plannningscycli te verkleinen door orders meer te consolideren. Die zet bleek evenwel niet ideaal, aangezien ze een negatieve impact had op Brisa’s competitiviteit en het vermogen om een antwoord op specifieke klanteneisen te bieden.
M. Hedurluk: “Aanvankelijk combineerden we een aantal manuele planning & scheduling tools die in huis waren ontwikkeld. Maar die tools waren niet in staat één enkel, naadloos productieplan te genereren dat onze operaties kon optimaliseren. Onze planners werkten in silo’s en stemden hun scenario’s niet op elkaar af. De planningsafdeling van elke shop streefde naar zijn ideale scenario, zonder er rekening mee te houden dat dit een negatieve impact op de rest van de productie kon hebben. Er werd ook te veel op korte termijn gepland. De impact van bepaalde beslissingen op lange termijn – bijvoorbeeld op het vlak van financiën en customer operations – werd daardoor vaak over het hoofd gezien.”
Het resultaat was dat Brisa Bridgestone constant tegen onrealistische deadlines aanliep. Uiteraard had dat ook een negatief effect op de tevredenheid van de klant. Daarenboven hanteerde de onderneming een ‘fixed time to plan’ van zes tot acht weken, wat wrevel opwekte bij klanten die een order sneller nodig hadden. “Door de planning over de verschillende shops meer te aligneren en op een geïntegreerde basis te plannen, wilden we enerzijds komaf maken met onze silo’s en tegelijk meer wendbaar worden”, stelt Murat Hedurluk. “Bovendien hadden we de droom om 3% meer te kunnen produceren door onze set-uptijden te minimaliseren.”
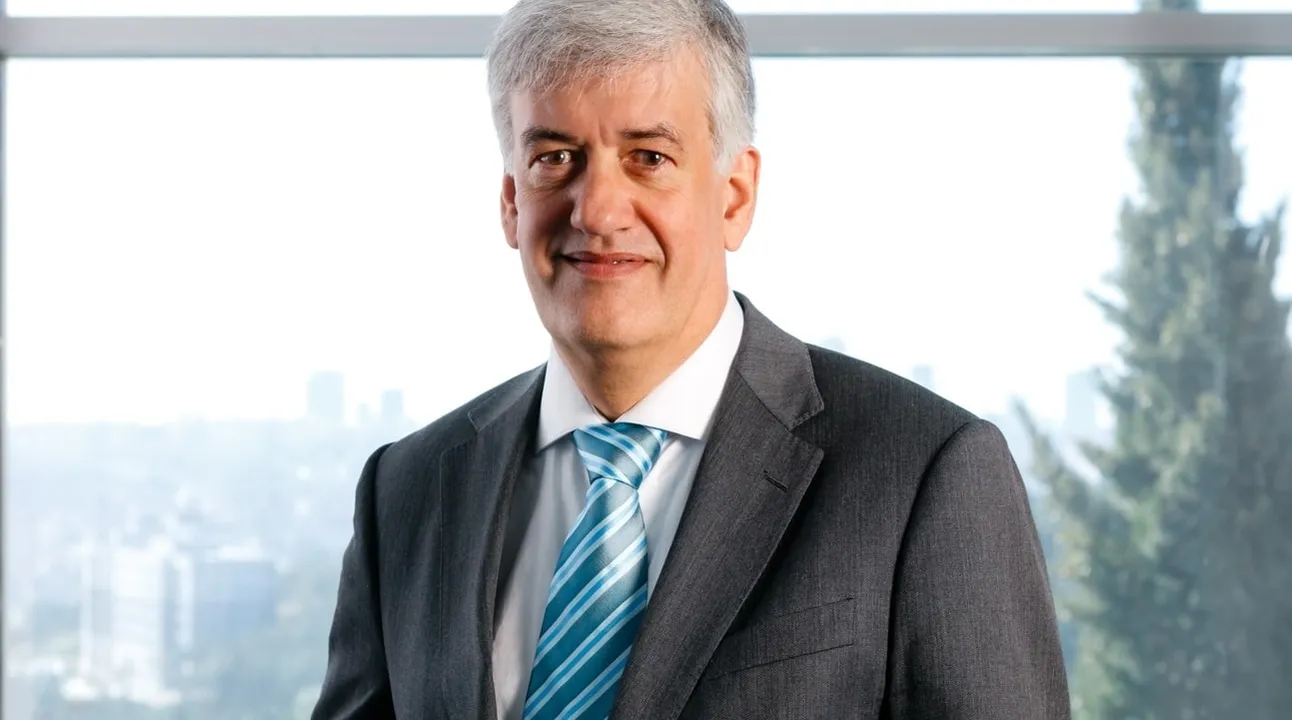
Software ter ondersteuning van geïntegreerde planning
Daarop besloot Brisa op softwarematig vlak het geweer van schouder te veranderen. Met het oog op een efficiëntere planning vroeg het bedrijf aan softwareleverancier ICRON om zijn Manufacturing Decision Optimization oplossing te implementeren. “Daarmee hebben we de organisatie een flexibel platform aangereikt, dat gemakkelijk met bestaande systemen te integreren is”, zegt Alfred den Besten. “De software is gemaakt om de performantie op het vlak van strategische en real-time operaties doorheen de supply chain te verbeteren, inclusief het beheer van materiaal, de productieactiviteiten, de opslag van afgewerkte producten en de logistiek.”
Een team van ICRON nam vervolgens de logica en de functionaliteit van het bestaande planningssysteem onder de loep en integreerde de noodzakelijke elementen van dat systeem in de Manufacturing Decision Optimization Solution. “Bij dergelijke projecten vinden we het heel belangrijk om stap voor stap te werk te gaan. Eerst stappen, dan lopen. Anders loop je het risico dat een bedrijf al snel in alle functionaliteit verdwaalt”, aldus Alfred den Besten. “Naarmate Brisa Bridgestone het pakket meer in de vingers kreeg, groeide ook onze kennis van de bandenindustrie. Zo hebben we in de loop der jaren heel veel van elkaar geleerd. We zijn gestart met het aligneren van de gedetailleerde productieschema’s op een geautomatiseerde manier. Aanvankelijk was dat nog steeds serieel, maar het feit dat de vier entiteiten vlotter zaken met elkaar konden afstemmen, betekende alvast een stap in de goede richting. Door met het systeem te leren werken, kwamen ze bij Brisa uiteindelijk tot één productieschema, waarbij er op alle fronten wordt gealigneerd.”
“Aanvankelijk grepen ook nog veel meer manuele interventies plaats. Je mag niet vergeten dat de planners van een volledig manuele manier van werken komen, dat kun je niet in één klap veranderen”, vervolgt Alfred den Besten. “Nu de planners beseffen dat accuraatheid belangrijker is dan ‘de baas zijn over het systeem’ is de persoonlijke tussenkomst sterk afgenomen. In vergelijking met enkele jaren geleden verloopt de planning nu ook veel sneller. Zo verminderde de tijd om te plannen vorig jaar alleen al met 25%. Die vrijgekomen tijd kunnen ze gebruiken om zaken beter op elkaar af te stemmen.”
Vandaag werkt Brisa Bridgestone op basis van een geautomatiseerde parallelle planning. Dat impliceert bijvoorbeeld dat, wanneer een planner een scenario uitwerkt dat impact heeft op een andere afdeling, hij daar automatisch een waarschuwing van krijgt. Op die manier kunnen beide planners proactief samenzitten om te kijken hoe ze een en ander op elkaar kunnen afstemmen.
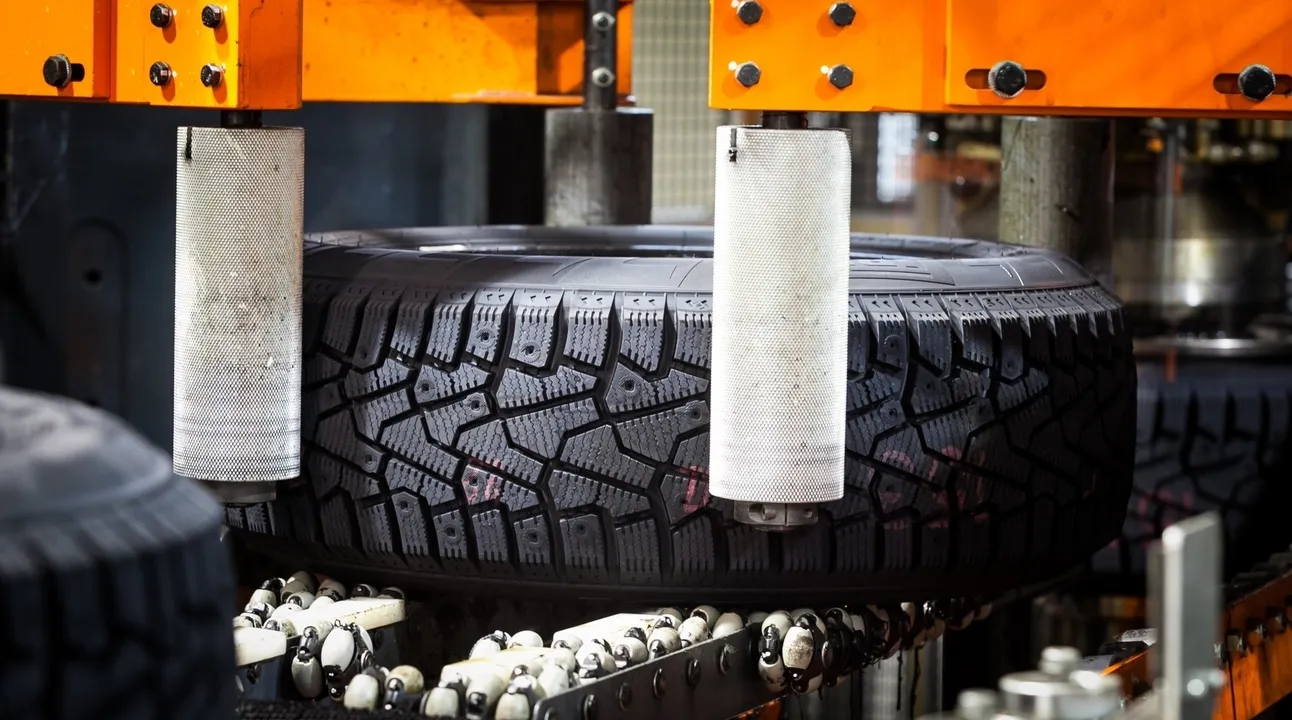
Wendbare basis voor verdere groei
Via het Graphical Scheduling and Modelling System (GSAMS) van ICRON werd een gebruikersvriendelijk platform opgezet dat volledig op de planningsvereisten van Brisa is afgestemd. GSAMS combineert een uitgebreide bibliotheek aan standaard planningsalgoritmes die ICRON in de loop van de jaren heeft ontwikkeld en waaraan continu nieuwe algoritmes worden toegevoegd. Naargelang het scenario of de voorspelling kan het meest geschikte algoritme binnen de modelleeromgeving geselecteerd worden. Daarin kunnen ook beperkingen – bijvoorbeeld op het vlak van voorraad – worden meegenomen.
De flexibele architectuur van ICRON’s Manufacturing Decision Optimization Solution maakt het mogelijk de complexiteit van Brisa’s productieomgeving mee te nemen. Dat stelde Brisa ten eerste in staat de karakteristieke planning en schedulingoperaties van zijn productieshops te optimaliseren. Ten tweede werd het mogelijk de operaties van die afzonderlijke entiteiten te coördineren met het oog op nauwere samenwerking en betere productiviteit in de volledige supply chain.
De software heeft eveneens gezorgd voor een grotere visibiliteit van alle parameters die een rol spelen binnen de productieprocessen.
Alfred den Besten: “De planners hebben toegang tot dashboards die hen via kleurcodes meteen duidelijk maken waar de uitdagingen schuilen. Hoelang zijn de procestijden voor een bepaald product? Waar zitten de bottlenecks in een productielijn? Maar ook het management kan het dashboard op het hoogste niveau bekijken, wat hen een betere basis geeft om beslissingen te nemen. Verder kunnen planners simulaties doen om te zien wat er gebeurt als ze een bepaald scenario uitvoeren. Op die manier zien ze meteen wat het effect van dat scenario op het totale productieproces zal zijn.”
Het platform heeft Brisa Bridgestone intussen een veel grotere wendbaarheid gegeven. Die vertaalt zich naar een grotere productieflexibiliteit en winstgevendheid. “Onze productiecapaciteit is met liefst 10% toegenomen, zonder dat er extra productielijnen zijn bijgekomen”, aldus Murat Hepdurluk. “Bovendien liggen de set-uptijden lager, wat zowel de productiviteit als de operationele kosten ten goede komt. Verder worden de componenten voor de productielijnen efficiënter aangevoerd. Ook de voorraadniveaus zijn gedaald tot het noodzakelijke minimum. In onze business waar de prijs van grondstoffen heel sterk kan schommelen – 20 à 25% is geen uitzondering – is een optimaal beheer van die voorraad uiterst belangrijk. Voorts heeft Brisa Bridgestone sinds de komst van de software komaf gemaakt met de manuele voorraadtelling, die in heel wat andere bandenmagazijnen nog schering en inslag is.”
Heel belangrijk voor Brisa Bridgestone is ook dat het productiedepartement ongeveer 15% meer verschillende orders tegelijk aankan, zonder dat de verkoop orders hoeft te consolideren. Die flexibiliteit speelt ontegensprekelijk in het voordeel wanneer een klant vlugger dan gebruikelijk wil worden beleverd. “Al heel snel na de implementatie hebben we mede daardoor onze omzet met 5% zien stijgen. Maar het is vooral de stijging van de klantentevredenheid met 10% die ons de vleugels heeft gegeven om op hetzelfde elan verder te gaan”, besluit Murat Hedurluk. “We overleggen trouwens nog steeds geregeld met ICRON om te kijken waar verdere verbetering mogelijk is. Dat laat ons toe mee te evolueren op de snelheid van de business.”
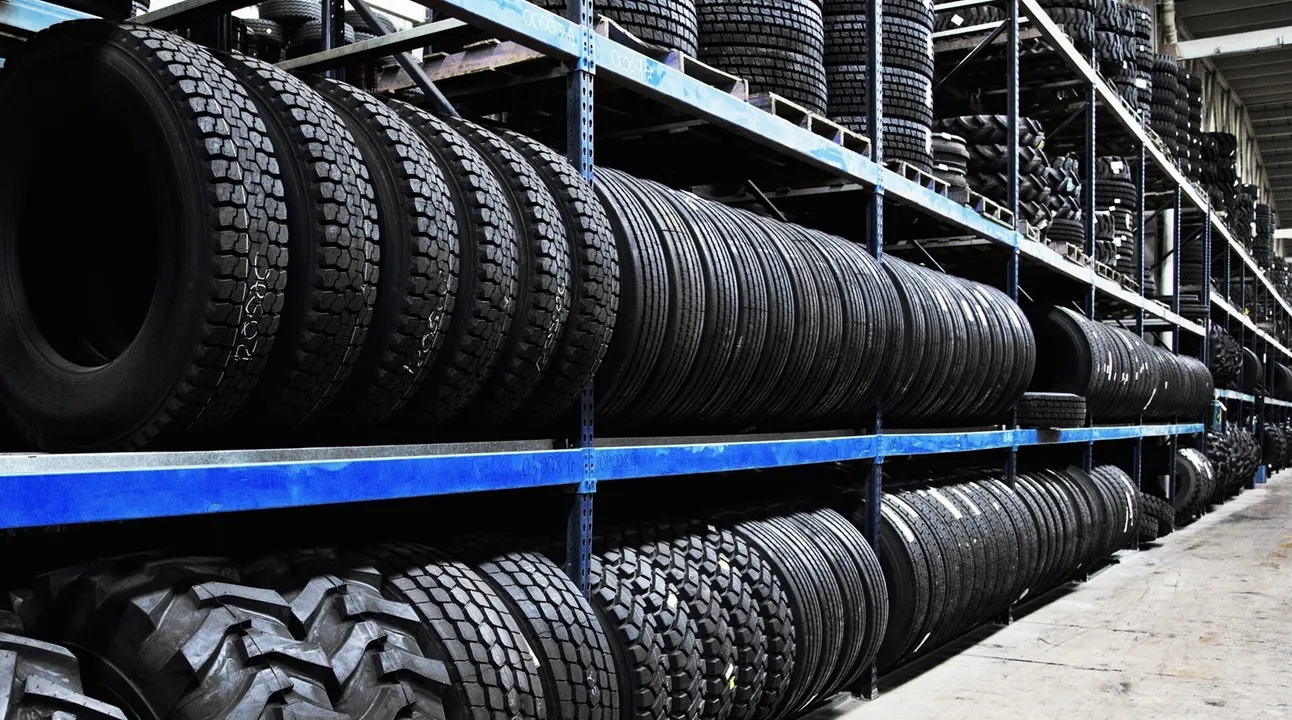
Extra
De banden achter Brisa Bridgestone
Voor de roots van deze Turkse bandenproducent moeten we teruggaan naar 1974, toen Sabanci Holding de onderneming leven inblies onder de merknaam Lassa. De naam Brisa ontstond in 1988 toen Sabanci Holding een partnership sloot met het Japanse Bridgestone Corporation, waardoor de merken Lassa en Bridgestone de handen in elkaar sloegen. Terwijl de focus bij het merk Bridgestone op performance en veiligheid ligt, is dat bij Lassa vooral comfort en duurzaamheid. Daarnaast brengt de producent banden voor diverse types voertuigen op de markt onder de namen Firestone, Dayton en Kinesis. In totaal is het aanbod goed voor zo’n 1.800 referenties, die vooral in Turkije en het Midden-Oosten worden verkocht.
Vandaag staat Brisa op nummer zeven in het rijtje van belangrijkste bandenfabrikanten binnen Europa. Brisa Bridgestone levert producten en diensten via ongeveer 1.200 verkooppunten in meer dan 60 landen. Daarnaast gebruiken autofabrikanten zoals Toyota, Fiat, Honda, Mercedes Benz, Oyak Renault en Ford Otosan en MAN zowel Bridgestone als Lassa als ‘original equipment’ bij de productie van nieuwe voertuigen.