We moeten de hele supply chain ‘virtual twinnen’
Omron en Dassault bundelen krachten voor industriële innovatie
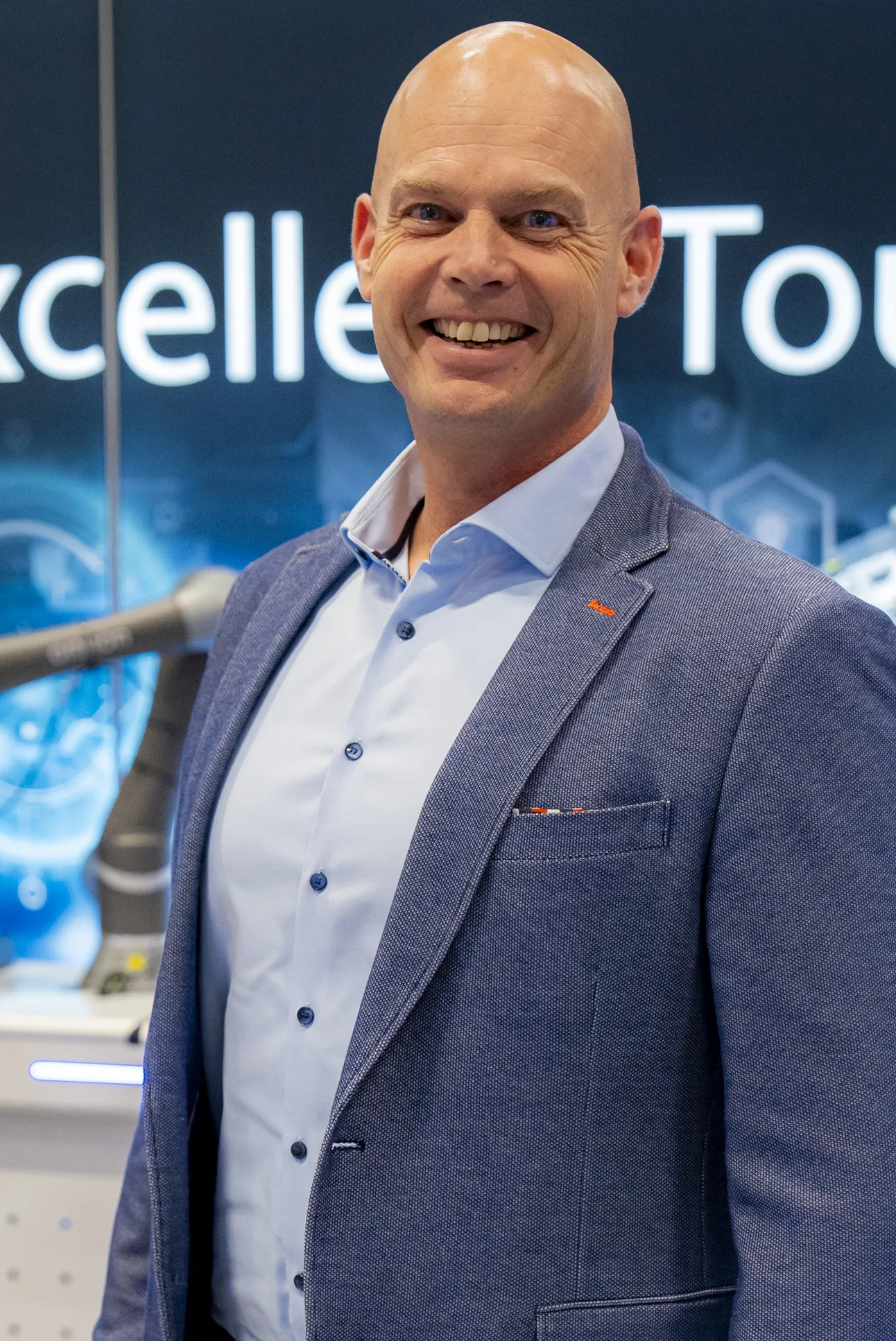
Maarten Mooi, general manager van Omron Benelux: “We geven industriële automatisering anders vorm. Om het even heel scherp te stellen: een PLC vervangen door een PLC mist voor ons elke vorm van relevantie.”
Omron Industrial Automation werkt al enige tijd aan de ontwikkeling van nieuwe, convergente automatiseringsoplossingen. Daarvoor ging het een samenwerkingsverband aan met de Franse softwareleverancier Dassault Systèmes. De eerste vruchten van die samenwerking kregen we alvast te zien in het Omron European Product Care Centre in ’s-Hertogenbosch, waar de eerste gezamenlijke Europese demotour van beide bedrijven van start ging.
Met hun samenwerking willen Omron Industrial Automation, een onderdeel van de Japanse Omron Corporation, en Dassault Systèmes, actief in 3D-ontwerp en PLM-toepassingen, de werelden van de operationele technologie (OT) en de informatietechnologie (IT) dichter bij elkaar brengen. Die doorgedreven integratie van OT en IT moet niet enkel voor een verdere, versnelde digitalisering van allerlei productieprocessen zorgen, ze moet ook de industriële innovatie in het algemeen stimuleren. “Vanuit die ambitie moet je onvermijdelijk veel breder kijken dan de eigen portfolio, want daar red je het niet langer mee”, zegt Maarten Mooi, general manager van Omron Benelux.
“Ons aanbod is complementair aan dat van Dassault”, benadrukt Tim Foreman, die naast R&D manager bij Omron Europe ook de wereldwijde projectleider voor het partnership is. “We vullen elkaar aan en dat is de logica achter onze samenwerking.” In Nederland leidt Tim Foreman een team van dertig R&D-medewerkers die voor Omron Industrial Automation werken aan de ontwikkeling van industriële pc’s, aanraakschermen en allerlei technologie voor digitalisering, waaronder AI en communicatienetwerken.
AR ondersteunt onderhoud
“We geven industriële automatisering anders vorm”, verduidelijkt Maarten Mooi. “Om het even heel scherp te stellen: een PLC vervangen door een PLC mist voor ons elke vorm van relevantie.” Het is ook niet waar bedrijven op zitten te wachten, stelt Tim Foreman vast. “We merken meer en meer dat grote productiebedrijven niet alleen maar op zoek zijn naar een automatiseringsoplossing met mobiele robots, bijvoorbeeld. Tegelijk zijn ze ook niet alleen maar op zoek naar een oplossing om op een virtuele manier een fabriek te ontwerpen.”
Met de nieuwe oplossingen die Omron en Dassault samen ontwikkelen moeten productiebedrijven de fysieke en digitale wereld op hun productievloer vlotter met elkaar kunnen verbinden en op elkaar afstemmen. Hoewel de klemtoon tijdens de demotour duidelijk op de mogelijkheden van digital – of liever ‘virtual’ – twins lag, kwam ook het gebruik van ‘augmented reality’ (AR) aan bod, meer bepaald ter ondersteuning van predictief of voorspellend onderhoud. Dat moet bedrijven in staat stellen hun operationele processen continu te optimaliseren.
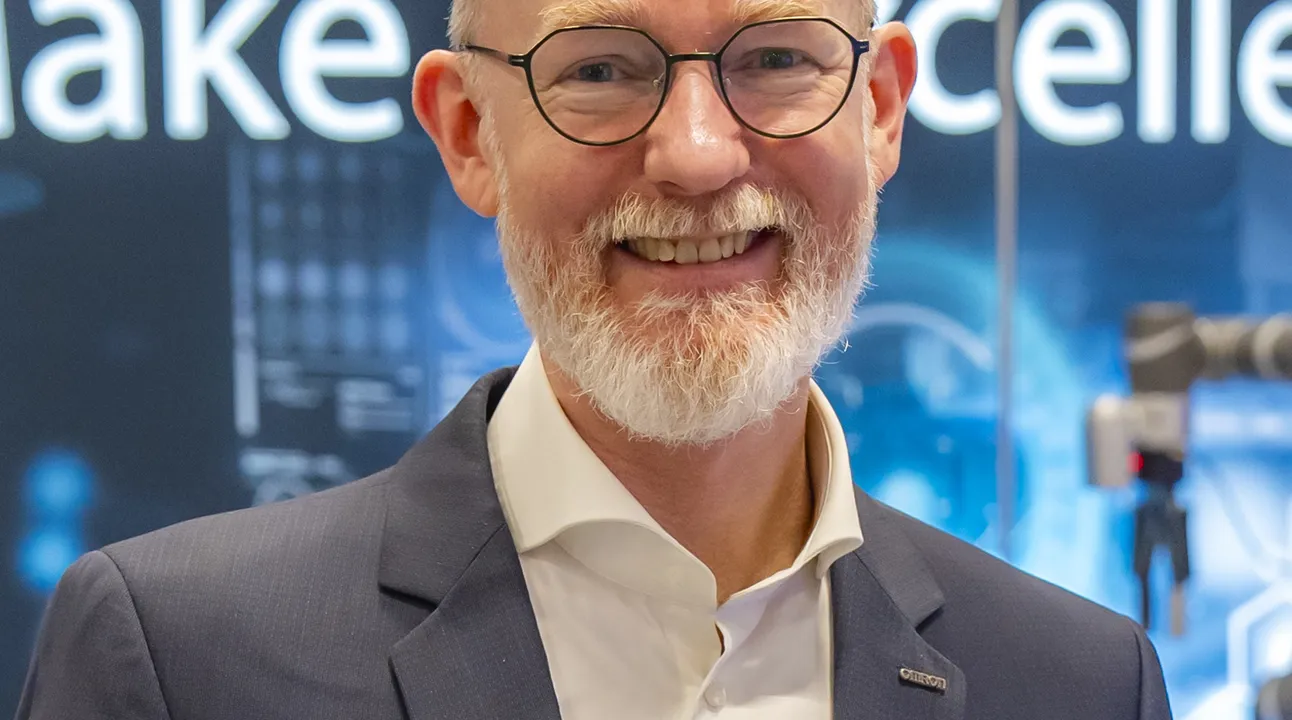
Tim Foreman, R&D manager bij Omron Europe: “Een virtual twin hebben van een machine, een productielijn of zelfs van een complete fabriek is slechts een deeloplossing. Het is niet genoeg en al zeker niet alles. We zullen de hele supply chain moeten ‘virtual twinnen’.”
Digitale of virtuele tweeling?
“Een ‘digital twin’ is weinig meer dan een exacte kopie van je fysieke hardware in een digitale omgeving”, zegt Michiel van den Besselaar, key account manager bij Omron Industrial Automation Europe. “Maar een machine die in gebruik is, die leeft in zekere zin ook. Ze zal bijvoorbeeld verslijten en onderhoud nodig hebben, en ze zal vooral heel veel data genereren. Als je die data, bij voorkeur in real time, aan de digitale tweeling toevoegt, zal ook die digitale tweeling mee-evolueren en krijg je realistischere simulaties. Zo’n levende digitale tweeling noemen wij een ‘virtual twin’.”
In ’s-Hertogenbosch, waar ook de Europese hoofdzetel van Omron Industrial Automation is gevestigd, konden we zelf ervaren hoe de combinatie van virtual twins en diverse automatiseringstechnologieën de productie kan vernieuwen. Meer specifiek kregen we er een inzicht in hoe virtual twins productieprocessen digitaal simuleren. Dat vertaalt zich concreet naar snellere innovaties, kortere opstarttijden en minder operationele risico’s, stuk voor stuk voordelen die essentieel zijn om de concurrentie voor te blijven.
“Door een virtuele PLC op je echte werkvloer aan te sluiten, kun je een productielijn ontwerpen en testen zonder fysieke hardware toe te voegen, maar ook zonder het risico te lopen op schade aan je bestaande hardware”, weet Michiel van den Besselaar. “Bovendien hoef je de lijn die op dat moment produceert niet stil te leggen om te kunnen testen. Met de kennis die je door al die testen opdoet, kun je je ‘time-to-market’ verkorten. Verder kun je je ook sneller aan veranderingen aanpassen. Dat alles geeft meteen ook de toegevoegde waarde weer van virtualisatie bij het ontwerpen en testen van een flexibele productielijn.”
Magazijnontwerp simuleren
Die virtualisatie hoeft zich echter niet te beperken tot de productielijn alleen. Je kunt diezelfde technologie evengoed benutten om de inrichting van een volledige fabriek te simuleren. “Een van de mogelijkheden om die digitale technologie in te zetten, is bijvoorbeeld bij het ontwerpen van een magazijn”, suggereert Tim Foreman. “Dan kun je allerlei vormen uitproberen. Wie weet is een circulaire vorm wel efficiënter dan allemaal rechte gangen? In de werkelijke wereld gaat niemand natuurlijk zo’n cirkelvormig magazijn bouwen, maar op de computer kun je dat wel. En dan blijkt misschien dat het transport in zo’n magazijn het snelst gaat, want daar zijn de verbindingen nu eenmaal het kortst. Maar een vierkante doos in een rond magazijn plaatsen, dat is dan weer eerder een nadeel, vrees ik.”
Niet toevallig was het simuleren van de bewegingen in het magazijn een van de toepassingsmogelijkheden van de virtual twin die ook tijdens de demotour aan bod kwamen. “Daarbij is het aardige van een virtual twin dat je kunt simuleren in de tijd”, merkt de R&D-manager op. “En niet alleen in reële tijd, maar sneller dan dat. Je kunt het proces als het ware versneld afspelen. Het resultaat van een test waar je normaal gesproken tien weken op moet wachten, kun je nu in een uurtje simuleren. De tijd die je daardoor uitspaart, is misschien wel het grootste voordeel van simulaties met virtual twins.”
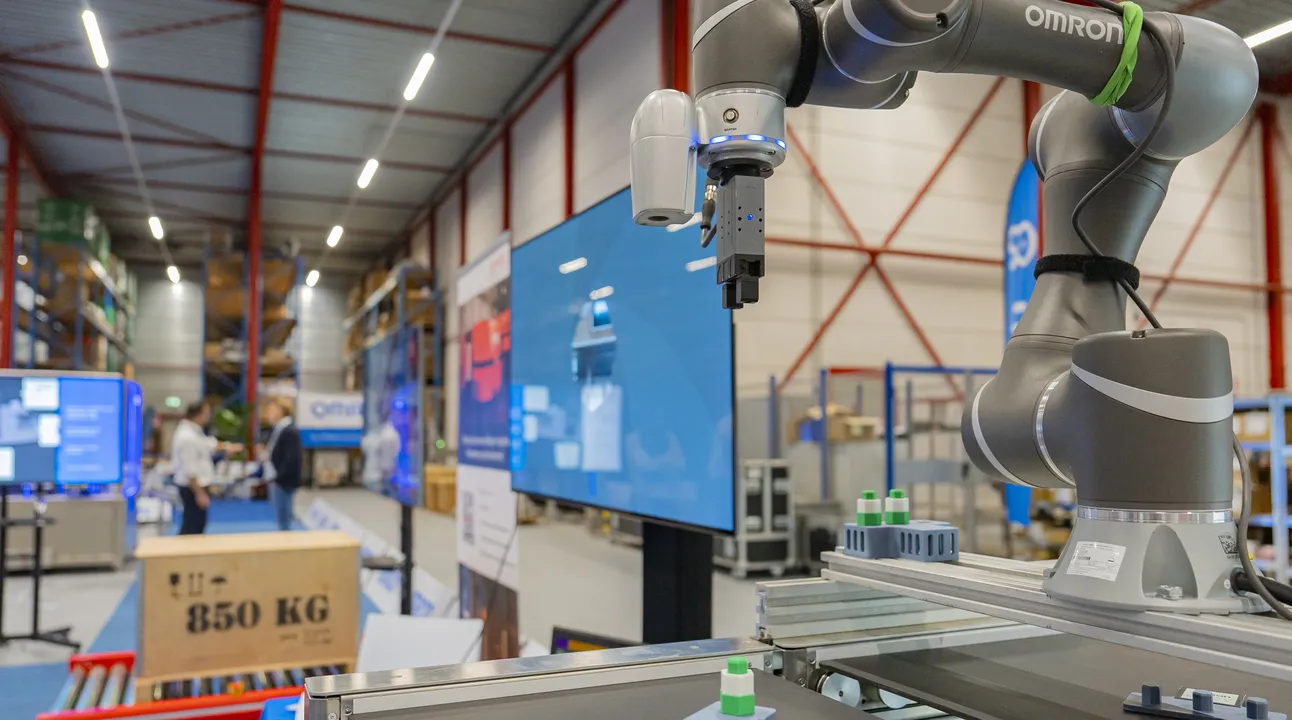
Het gebruik van virtual twins laat toe productieprocessen digitaal te simuleren. Dat vertaalt zich naar snellere innovaties, kortere opstarttijden en minder operationele risico’s.
Voorspelbaarheid vergroten
Voor Tim Foreman stopt het potentieel van de virtual twin ook niet aan de poorten van de fabriek. “Een virtual twin hebben van een machine, van een productielijn of zelfs van een complete fabriek is slechts een deeloplossing. Het is niet genoeg en al zeker niet alles. We zullen de hele supply chain moeten ‘virtual twinnen’.” Anders gezegd: de uitdaging beperkt zich allang niet meer tot het automatiseren en digitaliseren van de logistiek in het magazijn. We zullen ook de logistieke stromen tussen de fabrieken moeten aanpakken.
“Binnen R&D zijn wij sowieso begaan met de digitalisering van onze volledige industrie. Op dat gebied neemt Dassault vandaag al een hele grote hap voor zijn rekening, maar er valt nog veel meer te digitaliseren”, maakt Tim Foreman zich sterk. “Zo zou ik bijvoorbeeld willen dat alle onderdelen die in onze fabriek in Den Bosch binnenkomen, van een digitaal paspoort zijn voorzien. Doordat zo’n paspoort precieze informatie bevat over de kwaliteit van elk onderdeel dat hier binnenkomt, kun je je klanten ook makkelijker aantonen in welke toestand het finale product de fabriek heeft verlaten.”
Een van de grootste problemen waar niet alleen Omron zelf, maar ook veel van zijn klanten mee worstelen, is immers voorspelbaarheid. “De voorspelbaarheid van een fabriek is een erg complex gegeven. Het aardige van het feit dat mijn R&D-team in Den Bosch in hetzelfde gebouw zit als een echte fabriek met echte problemen, maakt dat wij beter begrijpen wat die problemen zo allemaal inhouden”, besluit Tim Foreman. “Met simulaties via virtual twins, maar ook met een uniek digitaal productpaspoort zoals de EU dat binnenkort verplicht maakt voor batterijen, kunnen wij die voorspelbaarheid in elk geval al wat vergroten.”
JDP
Premium
Deze inhoud is enkel leesbaar voor ingelogde Value Chain abonnees.
Heeft u een abonnement op het Value Chain informatiepakket? Meldt u aan via onderstaande knop en lees het gewenste artikel of magazine online.