Supply chain optimalisering via slimme ontwerpen en simulaties
Etex transformeert supply chain management
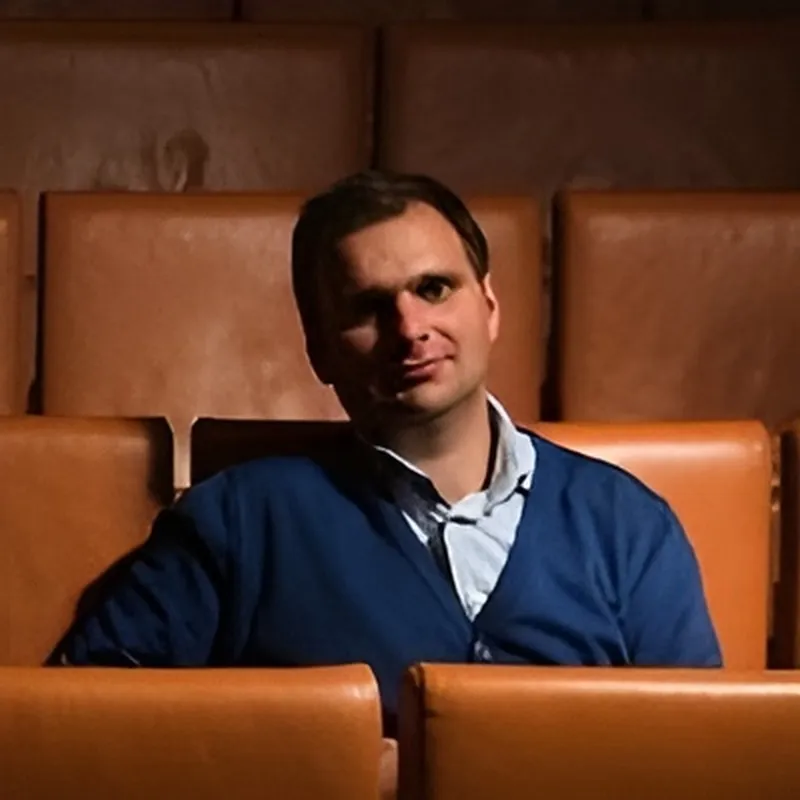
Noel Vranckx, head of global supply chain bij Etex: “Complexiteit in supply chains is tegenwoordig de norm in plaats van de uitzondering.”
In zijn transitie naar een multinationale onderneming ging bouwmaterialenproducent Etex op zoek naar een geïntegreerde aanpak om de supply chain rond zijn 250 productiesites en distributiecentra efficiënter te organiseren. Wat begon als eenvoudige Excel-berekeningen, is geëvolueerd naar een datagedreven methode voor optimalisering en simulatie, waarbij in de toekomst het belang van AI toeneemt. De actualiteit bewijst – helaas – dat die oefeningen geen overbodige luxe zijn.
Familiebedrijf Etex, met hoofdvestiging in Vlaams-Brabant, is momenteel in volle transitie naar een multinationale onderneming. De groep biedt bouwmaterialen aan via vijf divisies: ‘Building Performance’ (droogbouw, pleisters en composieten, vezelcement, passieve brandbeveiliging), ‘Exteriors’ (vezelcementmaterialen), ‘Industry’ (isolatie- en brandbeveiligingsoplossingen voor de industrie), ‘New Ways’ (offsite-bouwtechnologieën voor hout- en staalbouw) en ‘Isolatie’. Hoewel het bedrijf niet beursgenoteerd is, hanteert het wel vergelijkbare rapporteringseisen, vertelt Noël Vranckx, head of global supply chain bij Promat, dat onderdeel is van de Etex-groep.
De voorbije jaren heeft Etex supply chain optimalisering als nieuw begrip omarmd. Met 250 fabrieken en distributiecentra wereldwijd die tot enkele jaren geleden allemaal afzonderlijke winst- en verliesrekeningen hadden, drong een meer geïntegreerde benadering zich steeds meer op. “Zolang elke divisie maar winstgevend was, dat was het idee”, aldus Noël Vranckx. “Iedere lokale afdeling kon wel enkele ‘quick wins’ realiseren, maar van een geavanceerde aanpak voor optimalisering was geen sprake.”
Daarom begon Etex enkele jaren geleden met het opzetten van slimme netwerkdesigns en -simulaties. Op ruim drie jaar tijd zette het bedrijf grote stappen. “In de beginfase verliep alles nog op basis van eenvoudige Excel-berekeningen, maar gaandeweg evolueerden we naar een technologiegedreven methode met behulp van optimalisering en simulatie, waarbij ook AI een rol begon te spelen”, vertelt Noël Vranckx. “Complexiteit in supply chains is tegenwoordig de norm in plaats van de uitzondering.” Continue verstoringen en gebeurtenissen dwongen Etex ertoe naar het volledige netwerk te kijken in plaats van naar de verschillende productiesites en distributiecentra apart.
Geïntegreerde data
Voor de implementatie van centrale optimaliseringscapaciteiten had Etex dus al bepaalde onderdelen in Excel geoptimaliseerd. “Maar dat was niet voor het volledige netwerk houdbaar”, zegt Noël Vranckx. “Bovendien richtten de simulaties zich voornamelijk op productievariabelen, zoals CO2-uitstoot en logistieke stromen, terwijl er natuurlijk meer factoren meespelen, zoals de materiaalkosten en de cycli van onze steengroeves.” Al snel bleken de Excel-oplossingen onvoldoende omdat de data suboptimaal waren en het vaak maanden duurde om kleine optimalisering-oefeningen ook effectief uit te voeren.
Vandaag is Etex in staat de volledige supply chain te bestrijken, van leverancier tot eindklant, en simulatieoefeningen te houden in een veilige digitale omgeving en in verschillende scenario’s. “Doordat we alle productie- en logistieke data met elkaar verbonden hebben, kunnen we op korte tijd oefeningen maken. De data zijn ook meteen beschikbaar, zonder dat we ze eerst nog uit Excel moeten halen.” Daarvoor was een zeer gestructureerde aanpak nodig. “Dat moet wel als je over 250 productiefaciliteiten en distributiecentra beschikt”, benadrukt Noël Vranckx. Daarbij ging veel aandacht naar het definiëren van de reikwijdte van de data die nodig waren voor het modelleren van optimaliseringsscenario’s en simulatieoefeningen. Vervolgens verzamelde Etex de nodige data door de 250 databases te linken.

Etex beschikt wereldwijd over 250 productiesites en distributiecentra.
Van optimalisering naar simulatie
Etex maakt gebruik van drie types optimaliseringsscenario’s en simulatieoefeningen. De producent hanteert bijvoorbeeld een zogeheten ‘greenfield analyse’ om de ideale locatie van nieuwe productiesites of distributiecentra te bepalen. “Het gaat hier om een vereenvoudigde methode op basis van enkele parameters. De uitkomst geeft eerder een richting aan en is dus niet bepalend.”
Daarnaast is er ook een datamodel voor netwerkoptimalisering. “Dat is ons meest gebruikte model”, aldus Noël Vranckx. “Het gaat om een datagedreven methode om kansen voor mogelijke supply chain optimalisering te identificeren en te valideren, bijvoorbeeld om faciliteitenlocaties te bepalen, transporten te plannen of een masterplanning op te stellen.” Het model neemt daarvoor de belangrijkste variabelen in acht en abstraheert bepaalde vereisten om tot accurate beslissingen te kunnen komen. “We gaan bijvoorbeeld uit van volumes op jaarbasis. Met die gegevens stellen we een twintigtal verschillende scenario’s op die we vervolgens testen. Zo komen we bij de netwerksimulatie terecht, waarbij we aannames valideren via historische data-analyse, zoals de mogelijke effecten van wijzigende transportkosten of andere prijsveranderingen, of plotselinge veranderingen in de vraag.”
Scenario’s aftoetsen
Het verschil tussen de netwerkoptimalisering en -simulatie zit dus vooral in het doel dat die processen moeten dienen: via netwerkoptimalisering wil Etex plannen formuleren of bijsturen, terwijl de netwerksimulatie meer als tool dient om risicoanalyses te maken en nieuwe beleidsscenario’s te testen. “Dankzij de simulatiefunctie kunnen we snel handelen bij een plotse gebeurtenis en kunnen we bijvoorbeeld nagaan wat de financiële impact zou zijn wanneer we voor een andere leverancier kiezen”, licht Noël Vranckx toe.
De simulatie van bepaalde scenario’s dient vandaag dan ook vooral als ‘resilience check’, om te zien in welke mate het bedrijf bepaalde schokken kan doorstaan.
N. Vranckx: “De technologie helpt ons ook na te gaan hoe bepaalde optimaliseringsinitiatieven uitdraaien in die scenario’s. De output van de simulaties kunnen we vervolgens ook in onze PowerBI-omgeving binnenbrengen.”
De actualiteit bewijst trouwens dat die scenario’s geen science fiction zijn. Zo werd de kalkfabriek van Etex in het Oekraïense Bachmoet al vier keer door Rusland gebombardeerd.
Bovendien is de netwerkoptimalisering ook relatief eenvoudig en lineair geprogrammeerd, in het geval van Etex gebeurde dat in Python. “De vraag – en mogelijke wijzigingen in de vraag – spelen in elk scenario een grote rol”, gaat Noël Vranckx verder. “Het is mogelijk assumpties te maken over hoe de vraag er over een jaar zal uitzien, maar wat met vraagscenario’s over tien jaar? Hoe verder je kijkt, hoe meer variatie er ontstaat, maar het simulatiemodel maakt het in elk geval mogelijk om alle mogelijke scenario’s op te stellen. Het duurt bijvoorbeeld ook enkele jaren vooraleer een nieuwe groeve operationeel is, dus we moeten wel op de langere termijn kijken.”
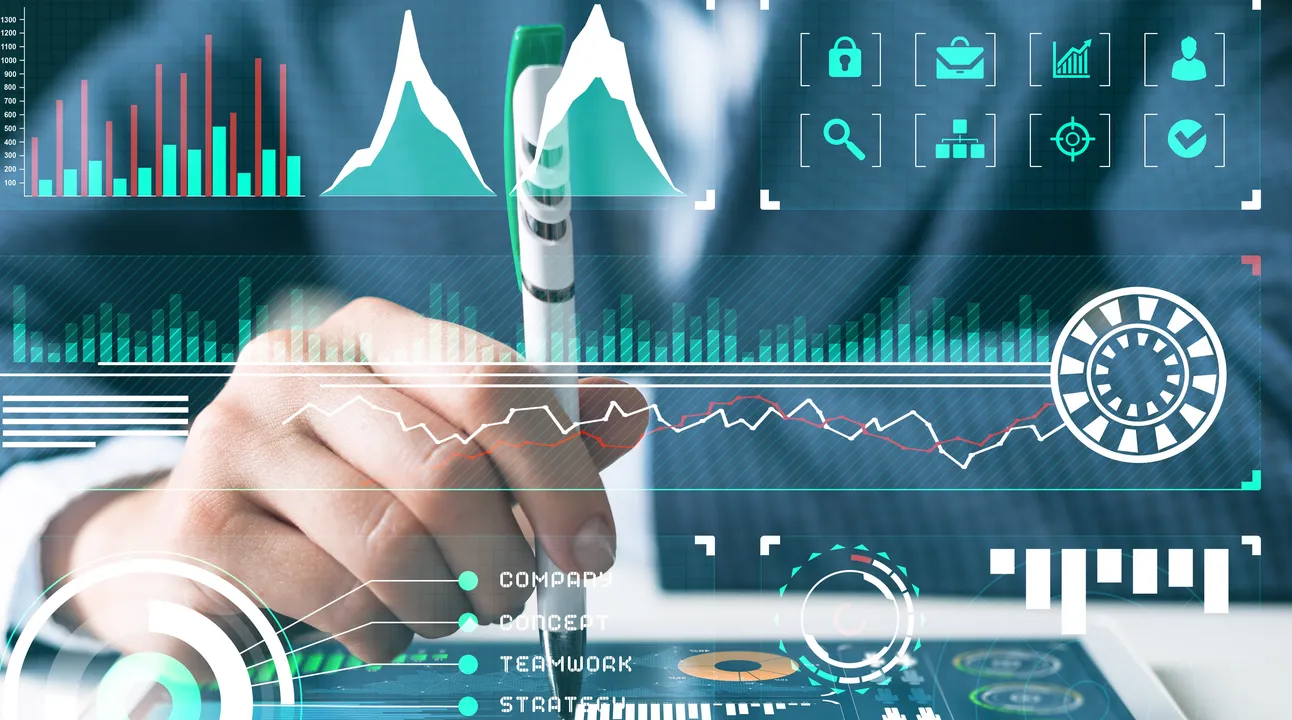
Via netwerkoptimalisering wil Etex plannen formuleren of bijsturen, terwijl de netwerksimulatie meer als tool dient om risicoanalyses te maken en nieuwe beleidsscenario’s te testen.
Enter AI
Onvermijdelijk komt daar vandaag nog een AI-laag bovenop. “Artificiële intelligentie maakt het steeds eenvoudiger om complexe netwerken te analyseren zonder dat er een trigger nodig is om onderliggende problemen vast te stellen en vervolgens de processen te optimaliseren”, aldus Noël Vranckx. Anders gezegd: dankzij AI hoeft er niet eerst brand uit te breken om daarna de brandveiligheid aan te pakken. Of in het geval van Etex: het bedrijf hoeft die brand niet eerst te simuleren.
Dankzij de verdere ontwikkeling van AI zal het netwerkontwerp steeds grotere proporties aannemen. “AI zal die ontwerptaak volledig overnemen, met begrip van de vragen die we ons vanuit bedrijfsoogpunt stellen en de context daarrond. Vervolgens kunnen we zo ook acties ondernemen.” Hoewel het huidige proces om simulatiemodellen op te zetten enkele weken in beslag neemt, biedt de technologie nu al de mogelijkheid om op korte tijd robuuste optimaliseringen te testen en snel te reageren op verstoringen in de supply chain. “Met AI kunnen we alle mogelijke variabelen en data samenbrengen. Het is de logische volgende stap”, zegt Noël Vranckx.
Terugblikken en vooruitblikken
Verder licht Noël Vranckx nog toe welke lessen het bedrijf uit de oefening van de voorbije jaren trekt en wat dat betekent voor de toekomstvisie van de groep. “Het is duidelijk dat supply chain optimalisering niet enkele een logistieke oefening is. Andere disciplines, zoals finance, productie en productbeheer zijn allemaal betrokken.” Om de mogelijke netwerkoptimalisering en daaropvolgende simulaties behapbaar te houden, gaat Etex uiteraard van enkele vereenvoudigingen en aannames uit. “Het is cruciaal om die te documenteren, want achteraf is het belangrijk de beperkingen en de gevolgen ervan te begrijpen.”
In de toekomst zullen variabelen op het gebied van duurzaamheid aan belang winnen. “Denk aan de CO2-uitstoot van het productie- en transportproces of de energieprijzen, om er maar enkele te noemen”, illustreert Noël Vranckx.
Hoe haalbaar en schaalbaar is het traject dat Etex doorliep op het vlak van netwerkoptimalisering en -simulatie voor andere bedrijven? “Het is misschien eenvoudiger om enkel het productieproces te modelleren en het later uit te breiden met andere processen, maar dat hoeft niet noodzakelijk zo te zijn. De voornaamste vraag die je moet stellen is: snap ik de beperkingen en de gevolgen van bepaalde assumpties en simplificaties? In de praktijk hebben we geleerd dat hoe logischer en beredeneerder je de zaken vereenvoudigt, hoe beter je achteraf in staat bent om iets te verklaren en acties te ondernemen.”
En tot slot: hoe ver ga je in het modelleren van scenario’s? “Het is een tweesnijdend zwaard”, meent Noël Vranckx. “Elk scenario geeft aanleiding tot weer een nieuw scenario en zorgt zo telkens voor een cascade aan nieuwe informatie en vragen. Het komt erop aan op een gegeven moment ‘stop’ te zeggen en een beslissing te nemen. Soms halen de feiten je ook in en zijn bepaalde simulaties zinloos. Zoals de mogelijke impact van een vraagstijging waarvan je denkt dat die structureel is, maar die alweer terugvalt op het moment dat je er simulaties rond uitvoert.”
FF
Inloggen/registreren
Om deze content te lezen, moet u zich inloggen.
Log in of registeer nu via onderstaande knop en krijg toegang tot deze inhoud.