Sterk geautomatiseerd, maar toch flexibel
Alpro kiest voor eigen hoogbouwmagazijn
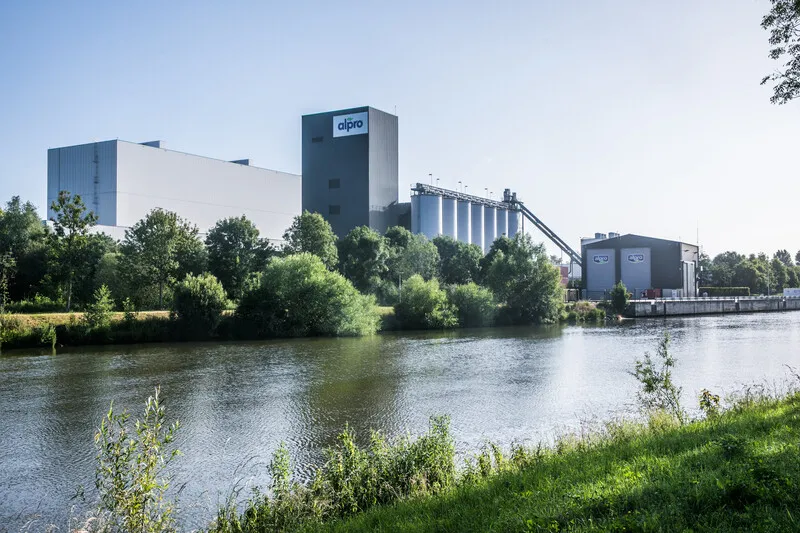
Het automatiseringsvraagstuk stelt de mogelijkheid tot flexibiliteit wel eens in vraag. Het hoogbouwmagazijn dat Van Looy Group voor Alpro realiseerde, toont aan dat het ene het andere allerminst hoeft uit te sluiten. Met onder meer flexibele temperatuurzones en de mogelijkheid om verschillende palletformaten te verwerken, kan de voedingsproducent nu makkelijker op de actuele marktevoluties inspelen.
Alpro is gespecialiseerd in de productie van plantaardige alternatieven voor zuivelproducten. Het bedrijf maakt deel uit van Danone en telt productielocaties in België, Frankrijk en het Verenigd Koninkrijk. De Belgische productie- en logistieke site bevindt zich in Wevelgem, bij Kortrijk. Ze fungeert als een logistieke hub: naast de eigen productie verwerkt en consolideert Alpro er ook supply chain stromen vanuit andere productiesites. Bij de productiesite in Wevelgem bevindt zich een laadkade aan de Leie voor het transport over water. Onder meer sojabonen bereiken Wevelgem via de binnenvaart. Tijdens een bustour, georganiseerd door Value Chain, konden we de werking van de site in levenden lijve aanschouwen.
Van extern magazijn naar eigen hoogbouwmagazijn
Om aan de voortdurende marktgroei tegemoet te komen, besliste Alpro in 2015 de productielijnen uit te breiden. Gezien de beperkte oppervlakte op de site moest het toenmalige magazijn met reachtrucks op de schop. Dat bracht een stevige uitdaging met zich mee voor het team van logistiek manager Wim Muylaert. “De oplossing bestond er aanvankelijk in een groot deel van onze logistieke activiteiten uit te besteden”, vertelt hij. “We laadden de productiepallets vanuit Wevelgem rechtstreeks op trucks, om ze nadien naar onze externe logistiek dienstverlener te vervoeren. Dat traject voltrok zich de klok rond, ook in het weekend. Ook voor de verpakkingslogistiek beschikten we over onvoldoende ruimte. We huurden een magazijn in Kortrijk en stelden er onze mensen te werk. De lege vrachtwagens hielden er op de terugweg van onze logistieke provider halt om de verpakkingen op te pikken en ze bij onze productiefaciliteit af te zetten. Het hoeft niet gezegd dat die operatie met een stevig kostenplaatje gepaard ging.”
De logische analyse luidde dat het anders, beter en efficiënter moest. “Gezien de ruimterestricties kwamen we al snel tot de conclusie dat we in de hoogte moesten werken”, blikt Wim Muylaert terug. Na het scannen van de markt nam Alpro Van Looy Group onder de arm voor de realisatie van het project. “We toetsten verschillende varianten af en werkten onze business case uit. Het nam al snel een half jaar in beslag om de nodige bouwvergunningen te verkrijgen. In tussentijd startten we de tendering. Daarna realiseerden we het project binnen een tijdsspanne van een jaar.”
Twee pallets per kraan
Het hoogbouwmagazijn is 45 meter hoog. Dat was gezien de aanwezigheid van het naburige vliegveld zowat de maximale hoogte. Het aanpalende laagbouwmagazijn telt 12 hoogtemeters. “Een automatisch verpakkingsmagazijn vormde geen optie gezien de vele verschillende leveranciers en verpakkingsformaten”, geeft Wim Muylaert aan. Het hoogbouwmagazijn biedt plaats aan 6.000 gekoelde pallets en 24.000 pallets op omgevingstemperatuur. Door middel van een conveyorsysteem is het met de twee productiezones geconnecteerd. Onmiddellijk na de productie transporteren de transportbanden de pallets automatisch naar het hoogbouwmagazijn. Daar volgt een profielcontrole, die onder meer nagaat of de uitsparingen van de pallet conform zijn en of ze niet te fel doorbuigt. Eenmaal het hoogbouwmagazijn bereikt, brengen negen automatische palletkranen met twee lastopnamemiddelen de pallets naar de gewenste locatie.
Dat elke kraan twee pallets tegelijk kan nemen, springt in het oog. “Uit onze berekeningen bleek dat een vereiste om de beoogde laadcapaciteit van tien trucks per uur te behalen”, vertelt de logistiek manager. “Om dezelfde reden zijn de rekken ‘single deep’. Eveneens bijzonder is dat we gewone europallets (80x120 centimeter) en industriepallets (100x120 centimeter) door en naast elkaar kunnen zetten, zonder dat we over afzonderlijke gangen of locaties hoeven te beschikken. Dat verhoogt onze flexibiliteit. Mocht de markt in een bepaalde richting evolueren, dan kunnen we daar zonder grote aanpassingen meteen op inspelen.”
Flexibiliteit is ook aan de laadkades terug te vinden. Naast vaste niet-gekoelde en gekoelde zones beschikt Alpro over een gemengde laadkade, aanpasbaar in functie van de producten die er op dat moment circuleren.
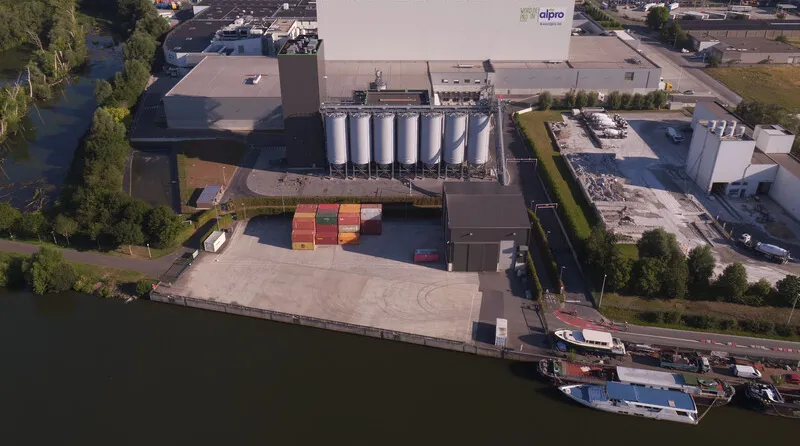
De opslag vindt plaats in een hoogbouwmagazijn en een laagbouwverpakkingsmagazijn.
Yard management
Alpro maakt gebruik van yard management. De vrachtwagenchauffeur meldt zich op het wachtparkeerterrein aan en ontvangt een sms met de kadegegevens, waarna hij de site oprijdt. Alpro klopt zich op de borst dat het op die manier 97 procent van de vrachtwagens tijdig laadt en lost. Eenmaal gedockt moet de chauffeur een wielkeg plaatsen, die is verbonden met een auditief alarm en lichten. Is de vrachtwagen niet correct gepositioneerd, dan volgt er een alarmsignaal. Een tweede beveiligingsmechanisme bestaat erin dat de chauffeur verplicht is de sleutels van de vrachtwagen af te geven. Dat moet voorkomen dat de trailer in beweging komt terwijl magazijnmedewerkers de vrachtwagen laden of lossen.
Vrachtwagenchauffeurs mogen het magazijn niet betreden. Alpro rustte de laad- en loszone uit met chauffeurskooien van waaruit chauffeurs de verwerking van hun lading kunnen volgen. Bij het laden van de oplegger maakt Alpro gebruik van een statiefscanner die de aanwezigheid van de juiste pallet op de aangewezen trailer verifieert en registreert. “Op die manier zorgen we er voor dat er achteraf geen discussie ontstaat over het al dan niet aanwezig zijn van een bepaalde pallet”, geeft outbound manager Bo Debruyne aan.
Magazijntreintjes
Opvallende verschijningen in het verpakkingsmagazijn zijn de twee magazijntreintjes. Ze zetten op basis van de input uit het ‘continuous replenishment process’ (CRP) in SAP de verpakkingsmaterialen binnen een tijdsspanne van twee uur op de aangewezen productielocatie af. Elk treintje is uitgerust met vijf wagonnetjes die telkens een pallet bevatten. Ze volgen een vast traject, aangeduid met blauwe lijnen op de magazijnvloer en genieten voorrang op alle andere interne vervoersmiddelen. De treinen beschikken over RFID-tags die de stopposities definiëren. “Vroeger stroomlijnden we dat transport met behulp van afzonderlijke handpallettrucks, die zich niet volgens een vast traject doorheen het magazijn bewogen”, verduidelijkt inbound manager Olivier Reubrecht. “Nu vervoeren we vijf pallets in een beweging en ligt het veiligheidsniveau veel hoger. Ten opzichte van AGV’s hebben de treintjes als voordeel dat ze zich flexibel door onze smalle gangen en bochten bewegen.”
Open aanspreekcultuur
Alpro ziet sterk toe op de interne veiligheid van zijn infrastructuur, goederen en mensen. Elke heftruck- en reachtruckbestuurder moet bij aanvang van zijn shift een digitale checklist invullen met betrekking tot de conditie van het toestel. De voedingsproducent maakt ook gebruik van snelheidsreductiesystemen. Die wil Alpro in de toekomst verder uitbreiden richting slimmere oplossingen, zoals een automatische snelheidsaanpassing in de nabijheid van voetgangers. Wanneer de reachtrucks hoge schokken registeren, treden ze meteen in schildpadmodus. Naast die technische ingrepen focust Alpro op de menselijke inbreng en verantwoordelijkheid. “Bij een bijna-incident verwachten we van onze mensen een veiligheidsmelding. We merken dat die cultuur ingebed raakt en dat medewerkers zelf zoeken naar oorzaken en oplossingen. De volgende stap bestaat in het creëren van een open aanspreekcultuur: elk teamlid moet een collega op een mogelijk risico kunnen wijzen, zonder daarbij de onderlinge relatie te beïnvloeden. Daar werken we sterk aan.”
Naast de jaarlijkse externe rekkeninspectie heeft Alpro intern medewerkers opgeleid voor kwartaalinspecties. “Opnieuw beogen we verantwoordelijkheidszin. Wanneer een reachtruck bijvoorbeeld de stijl van een rek licht raakt, zal dat waarschijnlijk geen risico met zich meebrengen, maar bij een tweede en derde incident in dezelfde zone treedt misschien wel het cascade-effect op en ontstaan er mogelijk wel gevolgen. Daarom gaan we er van uit dat onze heftruckchauffeurs zo’n incident eveneens melden.”
KD
Inloggen/registreren
Om deze content te lezen, moet u zich inloggen.
Log in of registeer nu via onderstaande knop en krijg toegang tot deze inhoud.