Shuttlesysteem als mijlpaal in ‘never ending journey’
DRiV belicht roadmap voor magazijnautomatisering
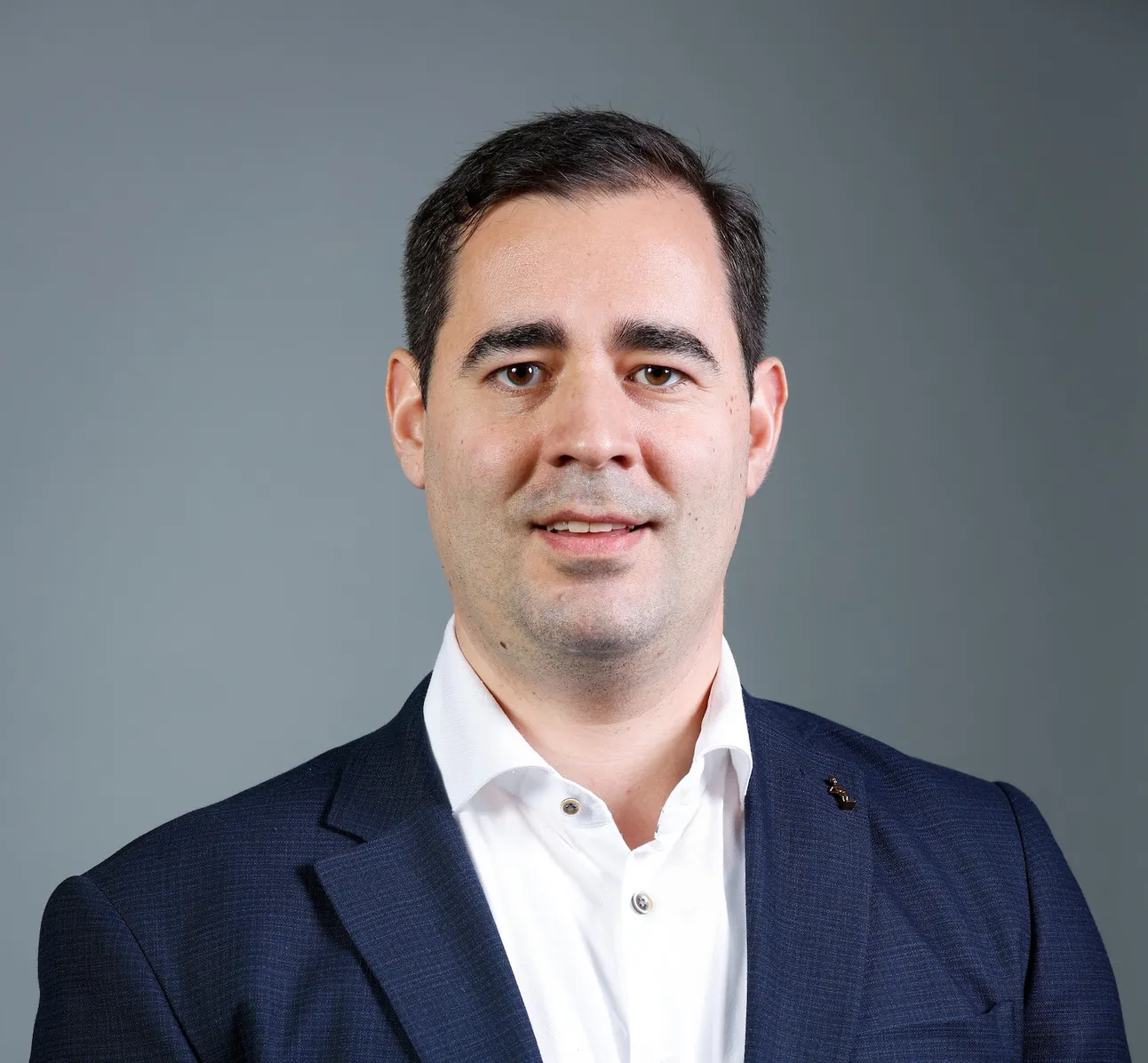
Thomas Thys, senior program manager - supply chain operations EMEA bij DRiV: “We hebben veel tijd gespendeerd aan het gedetailleerd in kaart brengen van onze volumes en stromen, want uiteindelijk is alles aan elkaar gelinkt. Als we de zaken met een geautomatiseerd systeem wilden omgooien, moesten we weten welke impact dat op onze operaties zou hebben.”
Toen DRiV zijn automatiseringstraject in Willebroek aanvatte, wist het bedrijf wel waar het startte, maar niet waar het zou eindigen. Vast staat wel dat de keuze voor de OSR, het shuttlesysteem van Knapp, een sleutelmoment was. Dat systeem vormt vandaag de basis voor alle volgende automatisering die DRiV bij zijn verdere groei moet helpen. Tijdens Supply Chain Innovations in Antwerpen gaf Thomas Thys, senior program manager - supply chain operations EMEA bij DRiV (Tenneco Group) tekst en uitleg bij het volledige traject.
DRiV is een van de vier divisies van de OEM- en auto-onderdelenproducent Tenneco Group, naast Clean Air, Powertrain en Performance Solutions. Binnen de groep legt DRiV zich toe op de aankoop, productie en distributie van onderdelen voor de ‘automotive aftermarket’. Dat gaat van uitlaten tot onderdelen die gelinkt zijn aan de remmen, de wielophanging en de motor. Het bedrijf heeft een portfolio van meer dan dertig bekende merken onder zijn vleugels, zoals Champion, Ferodo, Monroe en Walker. Liefst veertien van die merken zijn meer dan honderd jaar oud.
Wereldwijd doet DRiV een beroep op 17 productiesites en 29 internationale distributiecentra. Er werken in totaal ongeveer negenduizend medewerkers voor het bedrijf. Het distributiecentrum waarvan Thomas Thys het automatiseringstraject belicht, situeert zich in Willebroek. De ligging van dat magazijn, dicht bij de havens van Antwerpen en Rotterdam, de luchthaven van Brussel en belangrijke snelwegen naar Duitsland, Frankrijk en Nederland, maakt het een uitgelezen uitvalsbasis voor leveringen binnen West- en Oost-Europa en naar het Midden-Oosten en Noord-Afrika.
“We willen de leidende speler zijn in een zeer volatiele wereld. Om dat waar te maken, moeten ook onze warehouses state-of-the-art zijn, zodat ze klanten op een uiterst efficiënte en vlekkeloze manier kunnen beleveren”, steekt Thomas Thys van wal. “Een geautomatiseerde omgeving moest ons ook helpen bij de ondersteuning van onze e-commerce partners. Aangezien e-commerce orders vaak maar enkele eenheden per picklijn tellen, is automatisering een must om dergelijke activiteiten efficiënt te maken en betaalbaar te houden. Daarnaast wilden we de afhankelijkheid van menselijke werkkrachten voor groei en flexibiliteit afbouwen. Het is immers niet altijd evident voldoende medewerkers te vinden en te houden om onze operaties te ondersteunen of om met de bijhorende volumeschommelingen om te gaan.”
Weg van het manuele warehouse
Het vertrekpunt was een conventioneel warehouse van ruim 27.000 vierkante meter. Pickvoorraad werd er op verschillende verdiepingen in rekken opgeslagen en met trolleys verzameld. Die trolleys met producten werden vervolgens naar een consolidatiezone gebracht, waar de orders werden klaargemaakt voor verscheping. Er waren wel conveyors om het transport van bakken en stukken te ondersteunen, maar verder was er geen enkele vorm van ‘goods-to-man’ automatisering voorhanden. Wel bood het WMS van Manhattan Associates al de nodige aansturing.
“Dat we moesten automatiseren om meer toekomstbestendig te worden, was zeker”, vertelt Thomas Thys. “De vraag was vooral welk type automatisering het best bij ons paste. Daarbij moesten we rekening houden met enkele beperkingen. Het was bijvoorbeeld niet mogelijk het bestaande magazijn uit te breiden.”

In het shuttlesysteem vinden we het gros van de fast movers terug. Via deze oplossing wordt liefst zestig procent van de orderlijnen gepickt, tegen een snelheid die zeven keer zo groot is als bij de traditionele manier van orderpicken.
Wikken en wegen
In een eerste fase werd de bestaande situatie geanalyseerd en werden de toekomstige noden op een rij gezet. “We hebben veel tijd gespendeerd aan het gedetailleerd in kaart brengen van onze volumes en stromen, want uiteindelijk is alles aan elkaar gelinkt. Als we de zaken met een geautomatiseerd systeem wilden omgooien, moesten we weten welke impact dat op onze operaties zou hebben”, aldus Thomas Thys. “Daarnaast hebben we goede inschattingen trachten te maken van de toekomstige evolutie van de volumes, de orders en de klanteneisen. Denk maar aan de impact van e-commerce en de snelle ontwikkelingen in de automotive markt, met bijvoorbeeld de opmars van elektrische wagens. De automatiseringsoplossing moest ons voldoende flexibiliteit bieden om goed met deze volatiele businessomgeving om te gaan.”
Met die analyses in het achterhoofd werden de beschikbare automatiseringstechnologieën onder de loep genomen. “We hebben de pro’s en contra’s van verschillende systemen bekeken. Zo was in het oorspronkelijke ontwerp van het magazijn in Willebroek plaats voorzien voor een miniloadsysteem, maar omwille van de beperkingen op het vlak van capaciteit en ‘throughput’ zijn we daar toch niet voor gegaan”, licht Thomas Thys toe. “Een andere technologie die we hebben bekeken, is de Autostore. Zo’n systeem was al operationeel op een van onze sites in de VS. Maar voor ons magazijn in Willebroek bleek dat systeem geen ideale fit. Zo biedt een Autostore wel een hoge opslagcapaciteit, maar in de hoogte was dat systeem voor ons te beperkt. En zo waren er nog een aantal argumenten om naar een andere oplossing uit te kijken.”
Een shuttlesysteem paste beter in het logistieke plaatje van Willebroek. Dat is een automatisch en compact opslag- en orderverzamelsysteem (AS/RS – automatic storage and retrieval system), waarbij de goederen in bakken worden opgeslagen. Shuttles zorgen voor de horizontale bewegingen van de bakken, liften staan in voor de verticale bewegingen.
Thomas Thys: “Met een shuttlesysteem konden we de voorziene sectie van honderd op tien meter optimaal benutten. Zo liet de oplossing toe de volledige hoogte van twaalf meter te gebruiken en voor een opslag van drie bakken diep te gaan. Dat zou ons ruim voldoende opslagcapaciteit bieden. Met het systeem is het ook mogelijk de locatie van de pickstations vrij te kiezen, wat bij een Autostore-systeem niet het geval was geweest. Een shuttlesysteem laat ook toe vlot lege bakken naar de inboundzone af te voeren om ze er met nieuwe producten te vullen. Verder kunnen sprinklers worden voorzien in de shuttleracks, wat tegemoetkomt aan de strenge regels op het vlak van brandveiligheid.”
Toen de beste keuze voor het magazijn in Willebroek helder was, kon DRiV op zoek naar de meest geschikte automatiseringspartner. “We wilden in de eerste plaats een strategische partner, niet enkel voor onze site in Willebroek maar ook op andere locaties, mocht daar in de toekomst behoefte aan zijn. Een leverancier met voldoende schaalgrootte was dus belangrijk”, gaat Thomas Thys verder. “Daarnaast moest het systeem binnen de afgesproken tijdspanne kunnen worden opgeleverd. Er is vandaag veel vraag naar automatisering, waardoor de wachttijden flink kunnen oplopen. Daar wilden wij niet het slachtoffer van worden. Verder hebben we uit de ervaring met automatisering op andere sites geleerd dat een gegarandeerde service – zowel on-site als remote – primordiaal is. En uiteraard moest ook het financiële plaatje kloppen.”
“Omdat er verschillende systemen met elkaar gelinkt zouden worden, moest onze partner bereid en deskundig genoeg zijn om het volledige eigenaarschap over de software en de hardware op zich te nemen. Zo zouden we bij problemen maar één aanspreekpunt hebben”, voegt Thomas Thys er nog aan toe. “Ook was het engagement van onze partner primordiaal. Je kunt nu eenmaal niet alles op voorhand vastleggen en er zijn altijd onvoorziene veranderingen. Dan moet je een partner hebben die daar flexibel genoeg mee om kan en wil gaan.”
Na een grondige screening van de mogelijke partijen, aangevuld met referentiecontroles, viel de keuze op Knapp en zijn OSR Shuttle Evo. Naast het shuttlesysteem kwamen er ook een geautomatiseerde verpakkingsinstallatie en geautomatiseerde labelprinting.
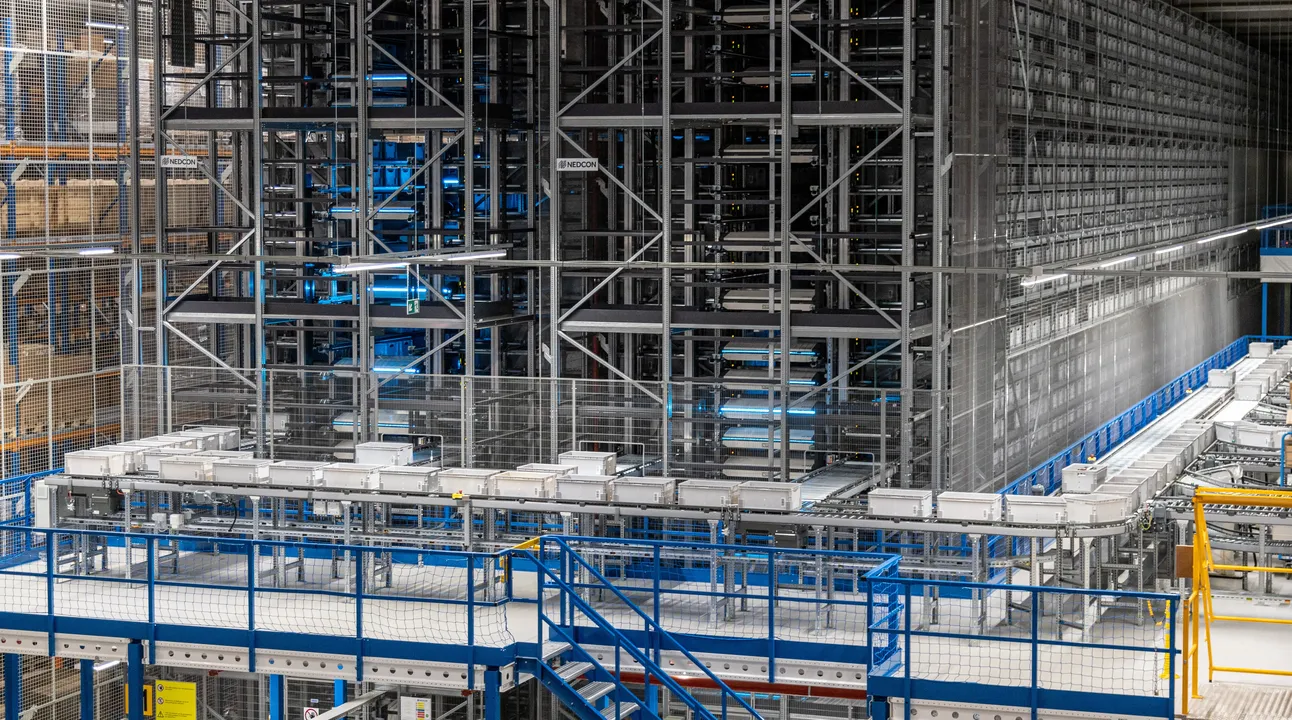
Voor de aan- en afvoer van de voorraadbakken naar de pickstations staan maar liefst 54 shuttles en vier liften in. Samen zijn zij in staat per uur 1.170 lijnen (dubbele cycli) te verwerken.
Implementatie tijdens lopende operaties
Het volledige automatiseringsproject, van de selectie en de engineering over de installatie tot de ‘go-live’, werd in twee jaar tijd gerealiseerd. Een grote uitdaging was dat het shuttlesysteem tijdens de lopende operaties moest worden geïmplementeerd, wat een erg nauwkeurige planning, implementatie en monitoring vereiste.
T. Thys: “In een eerste fase moesten we een deel van de rekken in het bestaande magazijn afbreken en was tijdens de stabiliteitsstudie vastgesteld dat de vloer niet sterk genoeg was om de installatie te dragen. Daarom hebben we eerst gezorgd voor een nieuwe, supervlakke vloer die over de bestaande heen werd gelegd. Voor de installatie van de Pick-it-Easy pickstations hebben we een mezzanine naast de shuttle-installatie gebouwd. Toen alles vorm begon te krijgen, volgde de interface met ons WMS en de aangrenzende installaties, zoals de verpakkingsmachine.”
De samenwerking tussen het DRiV-team en dat van Knapp verliep vlot. “De operaties tijdens dit intensieve project ‘up and running’ houden was niet altijd evident, maar toch is het ons gelukt. Enkel de dag voor de go-live, toen we alle knoppen hebben omgedraaid, hebben we even een onderbreking ingepland”, vertelt Thomas Thys. “Ook in de nasleep van de coronacrisis, toen sommige componenten duur en moeilijk te krijgen waren, heeft Knapp zijn flexibiliteit bewezen. Samen zijn we toen op zoek gegaan naar alternatieven om ervoor te zorgen dat we op schema konden blijven. Tijdens het traject kwam ook duidelijk het belang naar voren van een partner die de integratie met uiteenlopende oplossingen van verschillende aanbieders in goede banen kan leiden. Uiteraard zijn er onderweg ook discussies geweest, maar steeds hebben we de problemen meteen samen, op een open en oplossingsgerichte manier aangepakt.”
60% van de orderlijnen geautomatiseerd
In het shuttlesysteem vinden we het gros van de ‘fast movers terug’. Via deze oplossing wordt liefst zestig procent van de orderlijnen gepickt, tegen een snelheid die zeven keer zo groot is als bij de traditionele manier van orderpicken. In het systeem zijn er twee gangen, waarin drie bakken achter elkaar kunnen worden opgeslagen. In het systeem zijn 55.000 opslaglocaties voorzien. Voor de aan- en afvoer van de voorraadbakken naar de pickstations staan maar liefst 54 shuttles en vier liften in. Samen zijn zij in staat per uur 1.170 lijnen (dubbele cycli) te verwerken. In de volledig geautomatiseerde verpakkingsstraten worden de nodige documenten automatisch toegevoegd en worden de dozen automatisch op de juiste hoogte afgesneden, gesloten en van een label voorzien.
Sinds de komst van het shuttlesysteem worden onderdelen een stuk sneller en vlotter uitgeleverd. Daardoor kan DRiV zijn veeleisende klanten nu de gewenste ‘state-of-the-art aftermarket support’ bieden.
Intussen is de OSR-installatie ongeveer een jaar operationeel. “Maar dat wil niet zeggen dat we nu op onze lauweren rusten”, verduidelijkt Thomas Thys. “Zo zijn we met Manhattan Associates in gesprek over upgrades voor ons WMS. Wat onze magazijnautomatisering betreft, werken we aan een nog betere ergonomie op de manuele verpakkings- en herverpakkingsstations. Verder bekijken we of pickrobots onze pickperformantie in de toekomst kunnen verhogen. Tegelijk zijn we de mogelijkheden van AMR’s (autonomous mobile robots) aan het onderzoeken om de goederenbewegingen in ons magazijn nog efficiënter te maken. In de iets verdere toekomst willen we bijvoorbeeld evalueren of het mogelijk en zinvol is om nog grotere bakken aan het shuttlesysteem toe te voegen. Het mag dus duidelijk zijn dat magazijnautomatisering voor ons een ‘never ending journey’ is.
TC
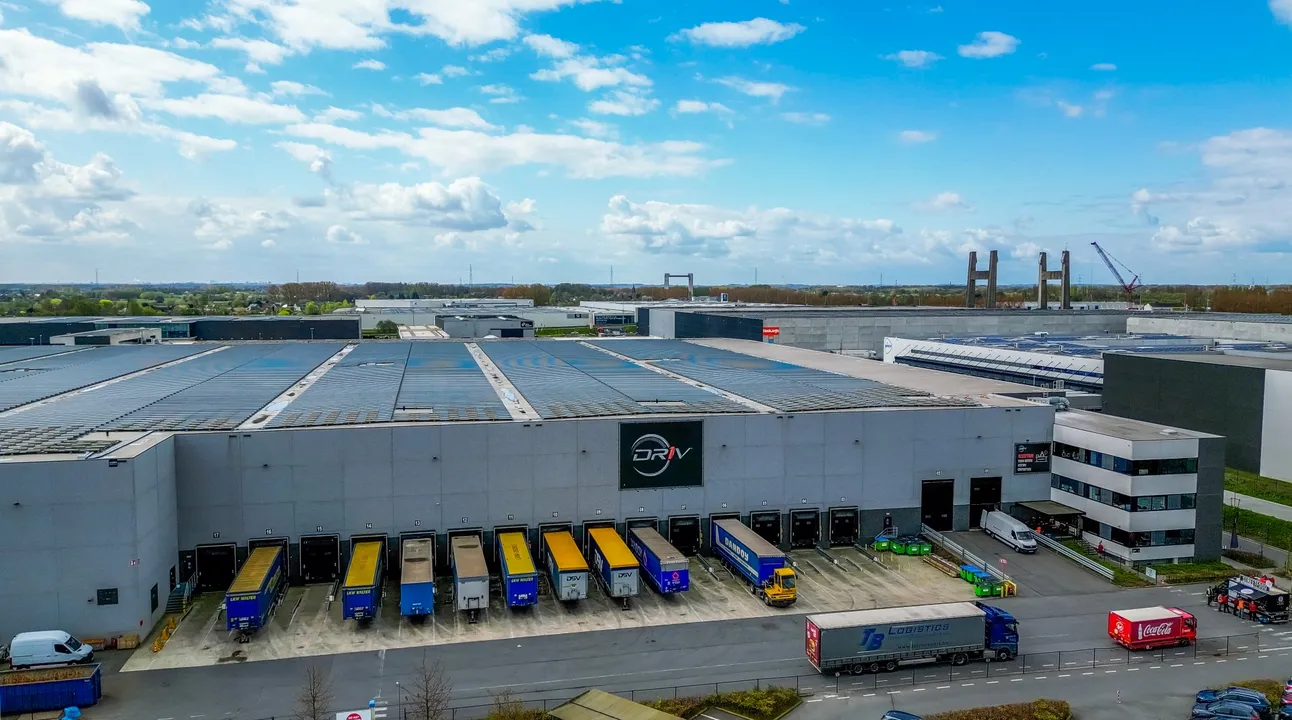
Sinds de komst van het shuttlesysteem worden onderdelen een stuk sneller en vlotter uitgeleverd. Daardoor kan DRiV zijn klanten nu de gewenste state-of-the-art aftermarket support bieden.
Premium
Deze inhoud is enkel leesbaar voor ingelogde Value Chain abonnees.
Heeft u een abonnement op het Value Chain informatiepakket? Meldt u aan via onderstaande knop en lees het gewenste artikel of magazine online.