Optimaal geautomatiseerd orderverzamelen
Overwegingen bij de keuze van een orderpickingsysteem
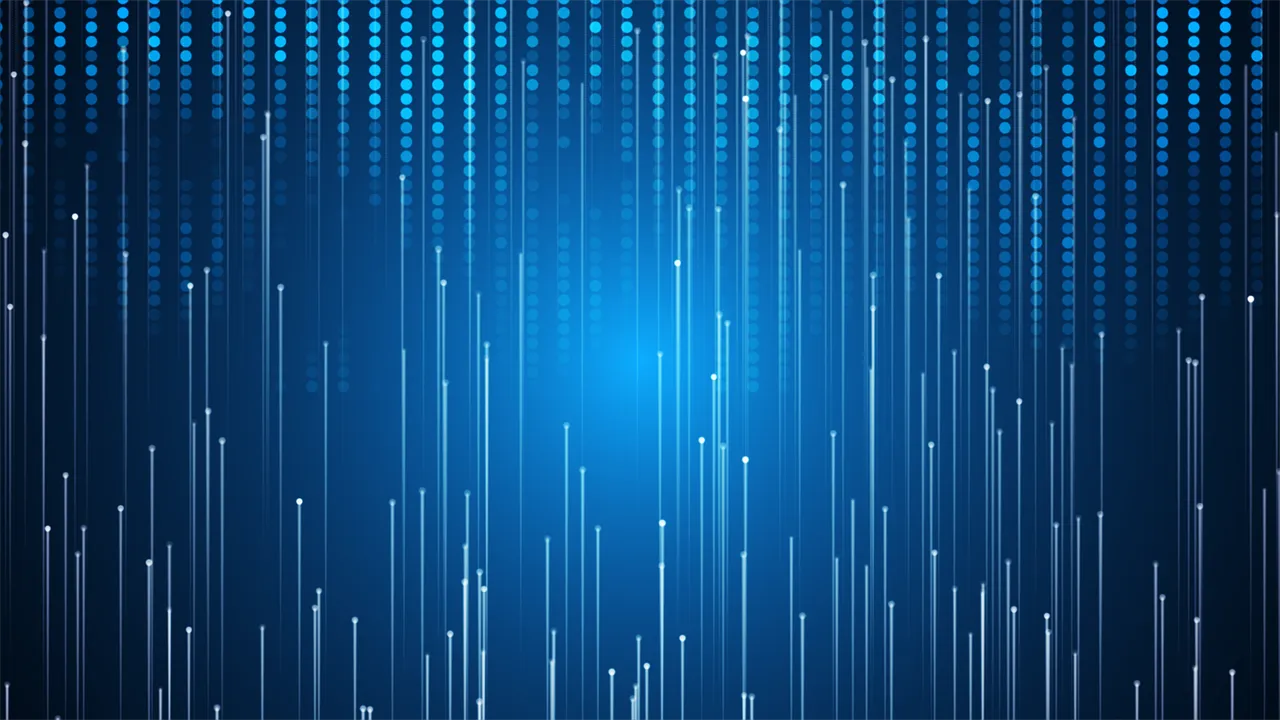
Aangezien orderpicking erg arbeidsintensief is, is het in een conventioneel magazijn ook het duurste proces. Bovendien heeft het de grootste impact op de kwaliteit van het magazijnwerk, gemeten via klantenklachten en voorraadverschillen na controle. Vandaar dat vandaag heel vaak in de richting van automatisering wordt gekeken. Diverse leveranciers zetten diverse oplossingen in de markt, met soms ongelooflijke te verwachten productiviteit. De klant zoekt dan weer naar een balans tussen de investeringskosten en het recupereren daarvan via hogere productiviteit, minder mensen en betere kwaliteit van het werk. Wij brengen een aantal van die oplossingen en concepten in kaart en focussen daarbij op detailpicking van relatief klein goed.
De orderverzamelactiviteit valt uiteen in een aantal verschillende deelstappen waarvoor verschillende oplossingen beschikbaar zijn. We hebben het hier over bewegen, zoeken, grijpen, stapelen en de administratieve verwerking. Op basis van onderzoek blijkt dat in een conventioneel magazijn gemiddeld 55 procent van de tijd in het bewegen zit, 15 procent in het zoeken, 10 procent in grijpen en wegleggen en 20 procent in de administratieve verwerking, inclusief scannen.
Bewegen
Om het bewegen – en dus de afstanden – te optimaliseren, bestaan er verschillende mogelijkheden. Zo kun je de picking via het ABC-principe organiseren, met de mogelijkheid de looproute in te korten door de doorgangen tussen de rekken slim in te zetten, rekken dwars op de hoofdlooproute te plaatsen, te zorgen voor meer aanbod van goederen voor picken per lopende meter route via ‘flow racks’ en legborden, en uiteraard door de goederen naar de orderpicker toe te brengen. In dat laatste geval bewegen de orderpickers hooguit enkele stappen rond een vaste positie en hoeven ze dus zo goed als geen afstanden meer af te leggen.
Daarnaast kunnen we ook in zone picken en consolideren of aan ‘batchpicking’ doen, waarbij tijdens één looproute meerdere orders worden verzameld. Bij automatisering hebben we het doorgaans over goederen naar een vaste pickpositie brengen om het werk uit te voeren. Dat kan via diverse systemen, bijvoorbeeld shuttlemagazijnen (klassiek of exotec), AS/RS (miniload voor kleinere goederen) of voertuigoplossingen zoals AMR’s (autonome mobiele robots) en dergelijke, die de units waaruit moet worden gepickt tot bij een pickstation brengen. Als dat slim gebeurt, kun je voor één beweging van de automatisering meerdere orderlijnen afwerken.
Tussen de manuele looproute en de vaste pickstations van automatisering in zitten nog toestellen als horizontale en verticale carrousels en liften. Daar bestrijkt de orderpicker een kleine oppervlakte om toch een veelvoud aan artikelen te kunnen picken.
Zoeken
Om het zoeken te optimaliseren, werken we bij een conventioneel systeem aan een logisch en eenvoudig locatiesysteem met visueel herkenbare locatielabels. Alternatief kan worden gewerkt met ‘pick-to-light’ displays, waarbij de locatie waar een operator moet picken, oplicht terwijl het display laat zien welke actie wordt verwacht. Dit systeem verplicht in feite om in zones te picken, aangezien het erg moeilijk aan te sturen is wanneer meerdere operatoren in hetzelfde gebied actief zijn. Ook haalbaar zijn ‘smartglasses’ met augmented reality (AR), die de operator visueel naar de juiste locatie begeleiden om het zoeken gemakkelijker te maken. Dat kan eventueel worden gecombineerd met een positionerings- en routeringssysteem dat de operator op de juiste plek ‘afzet’.
Bij een ‘goederen-naar-de-mens’-oplossing is zoeken uiteraard niet nodig, behalve in het geval van rekken die via AMR’s naar de pickstations worden aangevoerd.
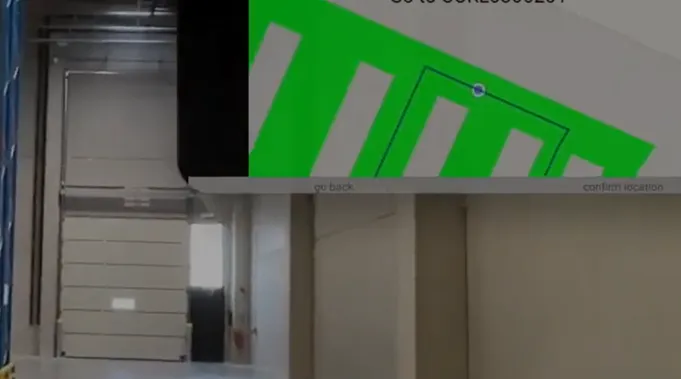
Op basis van positionering is het mogelijk de operator door het magazijn te routeren en op de juiste locatie ‘af te zetten’. (Bron: ART4L en Pozyx)
Grijpen
Om het grijpen te optimaliseren, moeten we ervoor zorgen dat de goederen makkelijk toegankelijk zijn op het schap of in de (automatisch aangevoerde) bak. Acties waarbij eerst een doos moet worden open geplooid of een bak uit het rek moet worden getrokken, hebben hun impact op de productiviteit. Pickrobots gekoppeld aan automatische opslag- en aanvoersystemen zijn vandaag beschikbaar, maar zijn nog vrij duur en kunnen meestal slechts een deel van het gamma behandelen, zodat ook nog bemande posten nodig zijn. Voorlopig is het moeilijk om in die oplossingen rentabiliteit te vinden in vergelijking met geoptimaliseerde manuele grijpoplossingen op bijvoorbeeld pickposten. Maar dat pickrobots in de toekomst steeds meer een rol gaan spelen, lijdt geen twijfel. Ook robotarmen op AMR’s om items van conventionele schappen te picken, is iets wat in de toekomst ongetwijfeld in de gaten te houden is, startend met één arm om dan in een volgende ontwikkelstap naar tweearmige robots te evolueren.
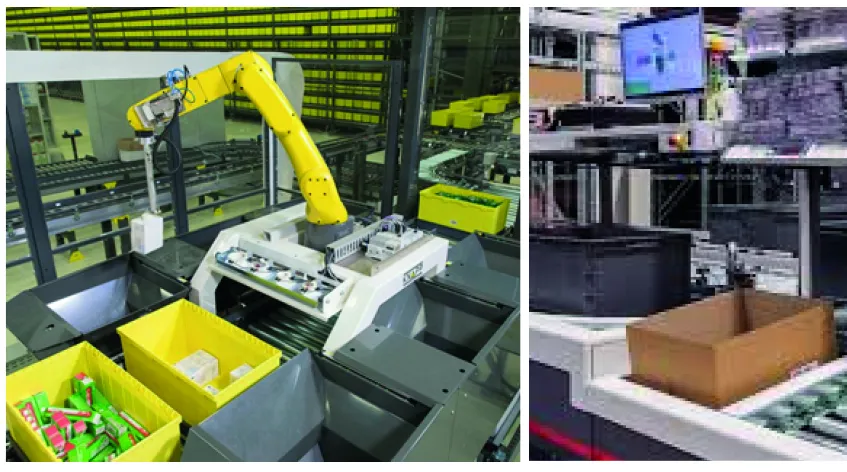
Links: Pickrobot (Bron: Knapp)
Rechts: Pickstation gekoppeld aan automatisering (Bron: Savoie)
Er bestaan ook diverse robotoplossingen om dozen of bakken van schappen te picken en ze vervolgens naar een pickstation te brengen. Ook het picken van pallets met robots is iets waar oplossingen beginnen te spelen, maar dat is allemaal nog vrij nieuw.
Stapelen
Stapelen of het wegleggen van de gepickte items op een pallet, in een doos of in een bak is vandaag het minst geoptimaliseerde deel van het pickingproces, zowel bij manuele als bij geautomatiseerde oplossingen. De meest kostenefficiënte manier van de combinatie picken-verpakken is de items direct in de verzenddoos te leggen. Vaak zijn er verschillende types in gebruik en geeft het WMS middels ‘cubing’ aan met welk type verpakking de picker een order moet starten (of een doosopzetter de doos moet maken).
Bij vrij ‘storten’ in de verpakking kunnen zich evenwel een aantal problemen voordoen. Zo kan de doos te krap zijn om ongeordend de volumes te verwerken. Bovendien geeft dergelijke chaotische vulling meestal aanleiding tot bijkomende activiteit op een packstation omdat de inhoud vaak toch nog opnieuw moet worden gestapeld voor transport, met tijdverlies tot gevolg. Ideaal hebben de orderpickers de discipline om de goederen in de doos netjes tegen mekaar aan te duwen, zodat eerst de bodem en vervolgens de rest van de doos naar boven toe wordt opgevuld. Tegenwoordig is er ook software beschikbaar die ideale stapelpatronen van te picken goederen kan berekenen en dat, bijvoorbeeld via smartglasses of een tablet, ook visueel aan de operator kan voorstellen.
Administratieve verwerking
Bij de administratieve verwerking hebben we met twee niveaus te maken:
- controle van de juiste locatie/het juiste artikel en de juiste (doos van) bestemming via scanning;
- het aanpassen van de status van een pickinglijn en afboeken van de voorraad op locatie in real time op voorwaarde dat er met wifi wordt gewerkt.
Bij de geautomatiseerde goederen-naar-de-mens-systemen krijgt de operator slechts één unit aangeboden om uit te picken. Op die manier worden foutieve artikelen of verkeerde locaties uitgesloten, uiteraard op voorwaarde dat aan de inboundzijde alle handelingen correct zijn uitgevoerd.
Om te voorkomen dat de verkeerde hoeveelheid van een item wordt gepickt, kun je ofwel onder de pickbak ofwel onder de verzendeenheid een gewichtscontrole uitvoeren. Daarbij wordt de weging normaal gezien ‘getriggerd’ door een operator die op een knop drukt. Als je meerdere orders uit een aangeboden eenheid kunt picken, is die gewichtscontrole aangewezen onder de pickbak. De operator bevestigt dan de juiste bestemming via (drop-to-light) knoppen. In dit geval wordt de administratieve verwerking vrijwel volledig tijdens het uitvoerende proces afgehandeld, wat de snelste manier van werken is.
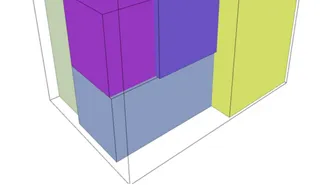
Visualisatie van een doosvulling (Bron: Optioryx)
Bij minder geautomatiseerde systemen wordt gebruik gemaakt van barcodes of soms ook RF/ID om zowel de controle als de bevestiging uit te voeren. Ook hier zijn diverse oplossingen beschikbaar, bijvoorbeeld handenvrije oplossingen zoals ‘wearable’ scanners, al dan niet met een display en in combinatie met een terminal, mobiele telefoon, voice oplossing of smartglasses.
Financieel aantrekkelijk
Aangezien bij een manueel systeem met picken uit legborden, visueel zoeken van de locatie, manueel grijpen en wegleggen en administratief verwerken via een terminal gemiddeld tussen de 60 en 80 lijnen per persoon per uur worden gepickt (afhankelijk van het type goederen en de systeemondersteuning), kost een orderlijn, enkel voor de picking, gemakkelijk tussen de 0,4 en 0,5 euro bij all-in manuurkosten van 30 euro. Om die kosten te optimaliseren, moet je de productiviteit verbeteren door diverse ingrepen uit te voeren en technologie in te zetten die investeringen vraagt.
Zou je bij een automatisch systeem 200 lijnen per uur picken, dan dalen de pickingkosten naar 0,15 euro per orderlijn. Met het verschil tussen beide kosten per gepickte orderlijn kun je vrij eenvoudig de financiële haalbaarheid van beschikbare oplossingen berekenen. Daarbij komt nog dat je door te automatiseren, kosten vermijdt doordat het proces kwalitatiever verloopt en je achteraf minder fouten – en dus klachten – hoeft recht te zetten. Hoe duurder (en hoe schaarser) magazijnmedewerkers, hoe beter de case voor automatisering.
Inloggen/registreren
Om deze content te lezen, moet u zich inloggen.
Log in of registeer nu via onderstaande knop en krijg toegang tot deze inhoud.