Opslag in lijn met kwaliteitstandaard bij Hessing
Geconditioneerde opslag bij VersFabriek
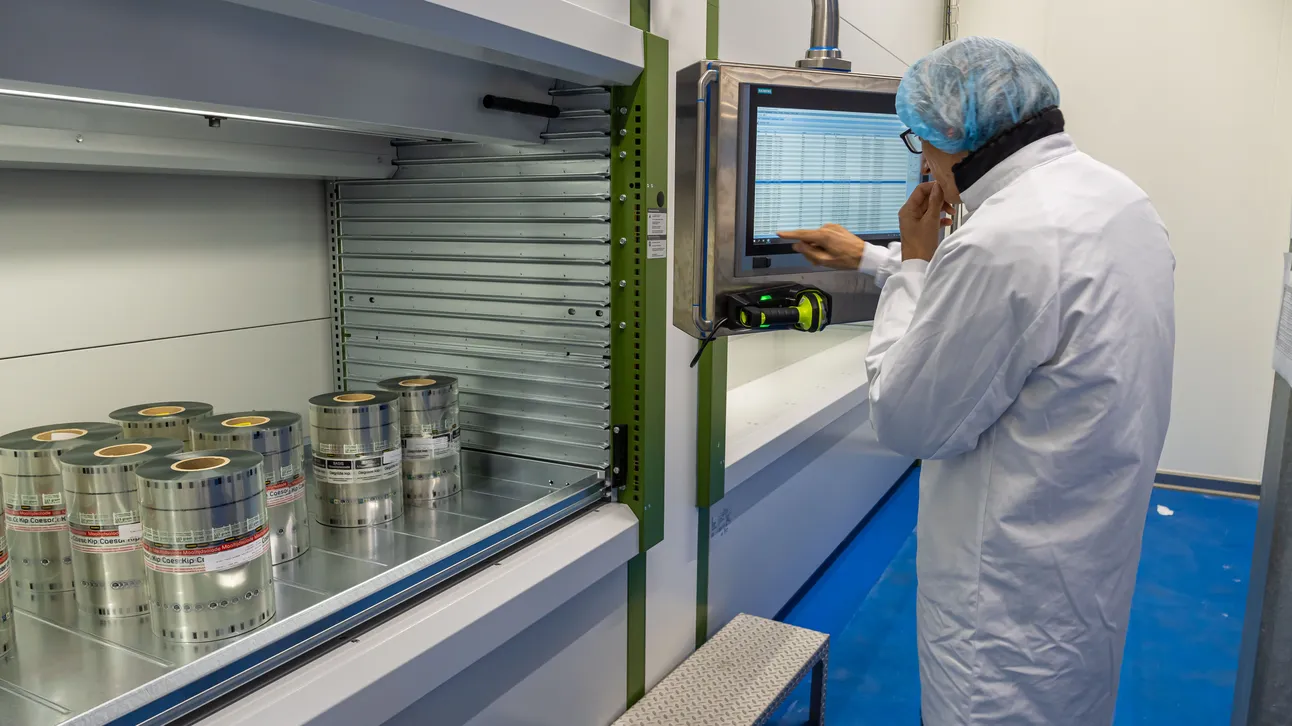
Hessing verwerkt superverse groenten en fruit tot panklare groentes of maaltijdsalades. In Greenport Venlo hebben ze de meest duurzame én modernste Groente VersFabriek van Europa geopend. Hier rollen dagelijks duizenden versproducten van de band af. Zo’n moderne fabriek kan natuurlijk niet zonder automatisering. Sterker nog: Hessing heeft op deze locatie zoveel mogelijk geautomatiseerd.
Ruud Jenniskens, Projectleider interne logistieke automatisering binnen Hessing, is nauw betrokken geweest bij dit project. “Vanuit Hessing is er een duidelijke visie op automatisering. Op deze locatie is goed nagedacht over waar automatisering een positieve bijdrage kan leveren aan de efficiëntie of aan het werkgemak van onze medewerkers”.
Compacte opslag
“In een magazijn van 45.800 m2 denk je wellicht niet direct aan compacte opslag” vervolgt Ruud. “Toch wilden we deze ruimte zo efficiënt mogelijk benutten, juist om ook de loopafstanden te verkleinen. Daarom zijn we de hoogte in gegaan. Zonder de geautomatiseerde opslagkasten zou de benodigde opslagruimte nog veel groter zijn.
Zo zijn er in totaal zeven Kardex Shuttles in gebruik genomen, die elk hun eigen toepassing hebben. Dit zijn vier shuttles voor verpakkingsmaterialen, 2 voor de opslag van TGT-monsters en 1 voor de Technische Dienst waarin gereedschappen en onderdelen opgeslagen worden. De TGT-monsters en de verpakkingsmaterialen waren extra uitdagend, omdat deze in een high care omgeving staan en dus moeten voldoen aan strenge vereisten.”
Opslag dicht bij de productie
Aad van Winden, Projectleider bij Hessing was verantwoordelijk voor het proces rondom de verpakkingsmaterialen van producten. Hij legt uit waarom ook hier automatisering een belangrijke rol speelt: “Onze verpakkingsmaterialen variëren van saladeschalen, folies, etiketten en sleeves. In totaal zijn dit zo’n 2.000 SKUs. Een grote uitdaging was dat veel producten [MA1] iedere dag geproduceerd worden waardoor we alle verpakkingsmaterialen elke dag nodig hebben.
Onze productielijnen hebben continu toevoer nodig van verpakkingsmaterialen en labels. We merkten dat er veel tijd verloren ging in het op en neer lopen tussen de opslaglocaties en onze productielijnen. We zochten een oplossing met een hoge opslagdichtheid. Dit werden de plateauliften. Dankzij deze liften liggen alle verpakkingsmaterialen zo dicht mogelijk bij de productie.”
Geconditioneerde opslag in een high care omgeving
In deze installatie wordt er op twee manieren bijgedragen aan de kwaliteitstandaarden van Hessing. De eerste is de geconditioneerde opslag. De plateauliften voor verpakkingsmaterialen vormen de scheiding tussen de medium care en high care afdeling waardoor kruisbesmetting voorkomen wordt. Binnen de Kardex Shuttle wordt met overdruk gewerkt om ervoor te zorgen dat er geen verontreinigde lucht naar de high care afdeling gaat.
Voor de TGT-monsters geldt zelfs dat de samples onder constante temperatuur van 0-4 graden of 4-7 graden opgeslagen worden. De houdbaarheid wordt daar 7 dagen lang onder vaste conditie gecontroleerd. Zo draagt deze installatie bij aan de garantie van verse producten.
Het tweede belangrijke punt om te voldoen aan de kwaliteitsstandaard is de tracking van producten door het hele proces. Door de integratie van de plateauliften met het ERP en MES systeem kunnen materialen op productieorders geregistreerd worden. Zo is inzichtelijk welke materialen voor welke order gebruikt worden en is het hele proces in de fabriek te traceren.[MA2] [AvW3]
“De efficiëntie en traceerbaarheid zijn voor ons de twee belangrijkste voordelen van de Kardex Shuttles. Met deze oplossing kunnen wij de versproducten sneller verwerken, zonder in te leveren op kwaliteit” sluit Aad af.