Opportuniteiten voor het grijpen
Snelle start met industriële robots in de logistiek

Volgens Michael Vermeer, general manager bij Robomotive in Roermond, zal zijn bedrijf nog dit jaar de eerste industriële robots in de magazijnen van grote bedrijven installeren. Een hele resem logistieke ondernemingen heeft immers besloten niet langer te wachten op de doorbraak van nieuwe technologieën. Ze kiezen daarentegen voor een robot die zijn kunnen al tientallen jaren heeft bewezen in de assemblagelijnen van de industrie.
Namen van klanten wil Michael Vermeer nog niet noemen, omdat de implementatie van de systemen nog niet is afgelopen. Wel geeft hij een inzicht in de motieven van die internationale spelers om de stap te zetten. “Heel lang was het in de logistiek niet nodig om voluit voor automatisering te gaan. Er waren nog voldoende goedkope arbeidskrachten om het werk te doen. Maar dat is nu niet meer het geval. Zeker in mijn streek, Nederlands Limburg, stellen we nu al tekorten vast. Onlangs nog ging een geplande investering in de regio om die reden uiteindelijk niet door. Dat heeft de logistieke bedrijven aan het denken gezet en de geest gerijpt voor meer automatisering.”
Daarnaast zijn er ook ontwikkelingen die logistieke managers de ogen hebben geopend voor een klassieke oplossing uit een andere sector. Het verschil tussen logistiek en industrie zit hem in de seriegrootte en de variatie aan producten.
M. Vermeer: “Dat verschil is wel essentieel om een goede oplossing te kunnen uitwerken. De productie van auto’s is daarvan een goed voorbeeld. Robots lassen daar de hele dag door dezelfde punten in de carrosserie van een wagen. Bij VDL Nedcar in Born, bijvoorbeeld, rolt er elke minuut een Mini van de band. Dat is één product met een groot volume en met een minimale variatie. In de logistiek komt dat haast nooit voor, het gaat er heel vaak om een zeer grote mix aan producten die dan ook in veel kleinere aantallen worden behandeld. Een robot moet die productvariatie aankunnen en tot voor kort was dat niet mogelijk. Een bijkomend verschil is de arbeidsorganisatie zelf: autofabrieken draaien 24 uur, 7 dagen per week. Dat bestaat niet in de logistiek. Er is amper ploegenwerk in de magazijnen en al helemaal geen 24/7.”
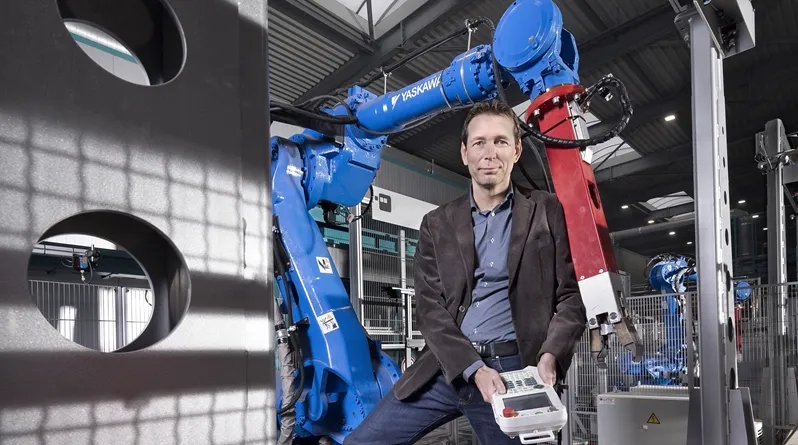
Aangepaste visie, nieuwe grijper
Robomotive maakt zich nu sterk dat het in staat is robots aan die omstandigheden aan te passen. Dat gebeurt in de eerste plaats door de robots te combineren met visietechnologie. Met name 3D-visie op basis van lasertriangulatie maakt het mogelijk dat de robot goed weet hoe een product eruitziet en hoe het moet worden opgepakt. De oudere visietechnologie zoals 2D ondervond heel wat problemen met verschillen in het omgevingslicht. Kapotte lampen of een felle zon in de werkplaats brachten het elektronische oog in de war. Dat moest dan worden opgelost door de robot in een black box te plaatsen. De 3D-lasers zijn uitgerust met hun eigen lichtbron. Het elektronische oog reageert in de eerste plaats op de lichtfrequenties die het systeem zelf heeft uitgezonden. De verwerking van die signalen is ook sterk verbeterd met nieuwe algoritmes. Robomotive test ook al jaren stereo-vision camera’s en ziet dat deze in het afgelopen jaar enorme stappen hebben gemaakt in robuustheid en performance.
M. Vermeer: “Daarnaast hebben we met Robomotive een universele grijper ontwikkeld die veel verschillende producten kan pakken. Die grijper werkt met vacuüm, maar is zodanig aangepast dat kleine onvolkomenheden – een lek in de grip, een schuine greep – niet verhinderen dat de robot het product oppakt. We hebben die techniek aangepast naar analogie met de werking van een stofzuiger. Die blijft ook zuigen als er objecten de zuigmond deels of volledig blokkeren. Zo zijn we erin geslaagd ervoor te zorgen dat een robot met die grijper producten tot 23 kilogram kan oppakken. In Nederland is dat, volgens de Arbowet voor welzijn op het werk, het maximale gewicht dat een persoon mag heffen zonder hulpmiddel. En het doet er dus niet toe of de verpakking los zit, er openingen in het product zitten of als het object zelf poreus is. De grijper is op dat vlak erg vergevensgezind.”
Geen CAD-bestand nodig
In het verleden had Robomotive al industriële pickrobots geïnstalleerd, onder andere bij Dyka, fabrikant van kunststofbuizen en accessoires. Daar stond al een industriële robot die aan een hoge snelheid een bak met bochten kon leegmaken. Toch was het systeem daar anders. De robot had een CAD-bestand van het product en wist op een tiende van een millimeter nauwkeurig hoe de objecten in de bak eruit zouden zien. De grijper wist ook altijd precies hoe hij zo’n bocht moest pakken. “Maar in de logistiek is dat geen typische situatie”, weet Michael Vermeer. “Er zijn vaak veel meer producten die moeten worden gepickt. Het is ook onmogelijk de CAD-file te krijgen van 40.000 producten van een heel assortiment in een distributiecentrum. Dat assortiment wijzigt dan nog eens snel ook. Onze robot is nu in staat te reageren zoals een klein kind dat een snoepje mag pakken uit de trommel van oma. Daarin zitten verschillende lekkernijen zoals lolly’s, koekjes en karamellen. Het kindje kan die perfect pakken, zonder dat het al die dingen vooraf kent, maar louter op basis van wat het ziet. Dat is wat onze algoritmes nu ook doen: ze gaan flexibel om met een situatie zoals ze is. In feite zijn ze niet zo nauwkeurig als de vroegere systemen, maar dat hoeft ook niet.”
Michael Vermeer verwijst daarbij ook naar de website van het bedrijf waar een filmpje te zien is waarin de nieuwe robot een bak met heel verschillende objecten krijgt voorgeschoteld en er een voor een zaken uit pakt en op een transportband legt. Het is een hele stap voorwaarts gezien de bestaande voorbeelden van pickrobots die in de praktijk vaak alleen dezelfde netjes gestapelde doosjes konden pakken.
M. Vermeer: “De innovatiemanagers bij de logistieke dienstverleners die ik nu ontmoet, hebben de voorbije jaren alle mogelijke nieuwe technologieën uitgeprobeerd, met name de alternatieve robots die met mensen kunnen samenwerken. Ze komen steevast tot de vaststelling dat de technologie niet rijp is. Zij willen nu starten met een project dat binnen enkele weken een bijdrage levert aan de productiviteit van het bedrijf. Dat kan voorlopig alleen met een technologie die zich heeft bewezen.”
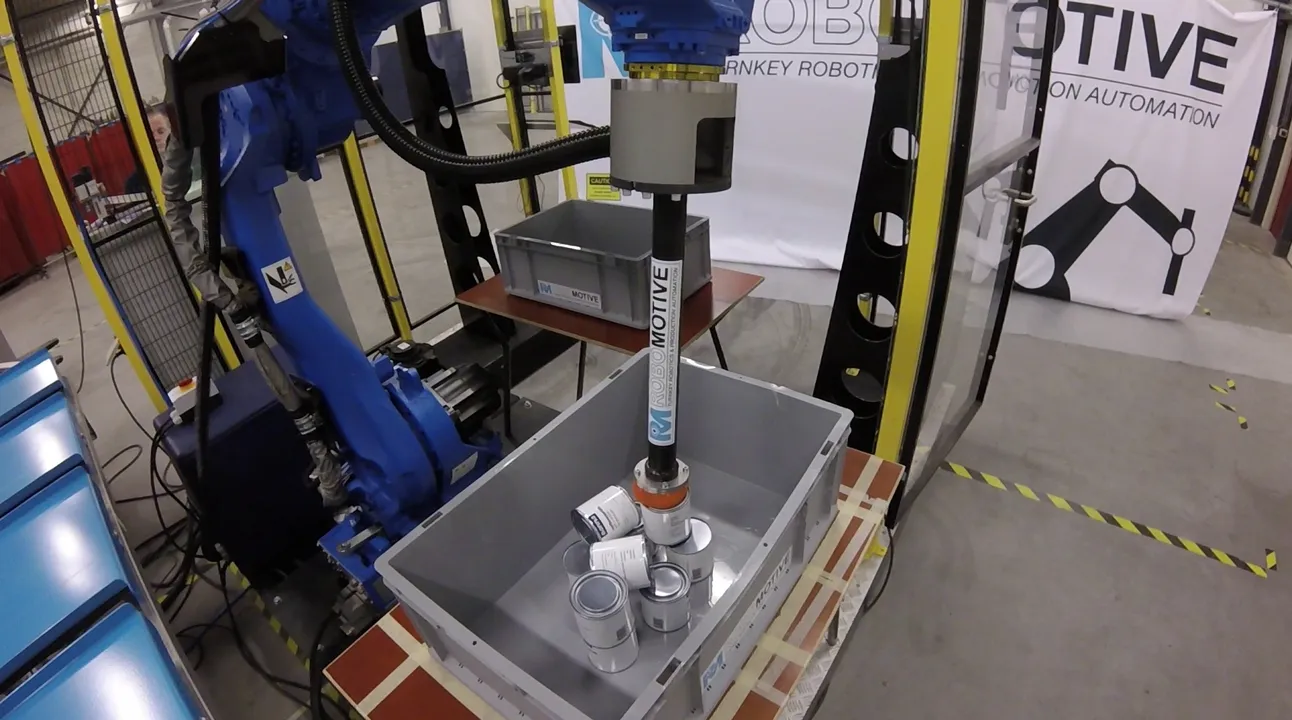
Aangepaste organisatie
Maar de keuze voor die industriële robots brengt ook een aantal consequenties met zich mee. Gewoonlijk zijn die robots erg krachtige machines met een groot bereik en vaak zeer snelle bewegingen. Ze kunnen bijvoorbeeld van een pallet van twee meter hoogte de producten picken en ze wegzetten aan een snelheid die vergelijkbaar is met die van een mens. Dan moeten een 900-tal picks per uur mogelijk zijn. De kracht en de snelheid waarmee ze werken, maken dat ze gevaarlijk zijn voor de mensen die daar in de buurt komen. Net als in de industrie moeten ze dus van hun omgeving worden afgeschermd door een hek zodat er geen interactie mogelijk is tussen mens en robot.
M. Vermeer: “Daar moet je geen compromissen zoeken: laat die robots achter het hek en laat ze dan hun echte potentieel volledig gebruiken. Er is wel nog interactie met die robots nodig om nieuwe producten aan te brengen of pallets en containers weg te halen. Bij bepaalde klanten hebben we dat opgelost met een AGV die een lege bak weghaalt en een volle in de plaats zet.”
Michael Vermeer wijst erop dat dit type robots geschikt is om continu te werken. In de industrie gebeurt dat ook. “Om het volle potentieel eruit te halen, zou ook de logistiek dat moeten doen. Ik zie dat men nog niet gewend is om het werk op die manier te organiseren. Enerzijds zou zo’n 24/7 regime goed zijn voor de optimalisering van de return on investment van de robot, anderzijds moet de komst van die robots het misschien net mogelijk maken.”
Toekomstvisie
In zijn recente projecten ziet Michael Vermeer heel wat opportuniteiten voor robots die logistieke taken kunnen uitvoeren volgens het principe ‘pick, process, place’. Iets nemen of wegzetten uit een bak, doos, rolcontainer of enige andere logistieke drager. Het proces kan bestaan uit verplaatsen, scannen, enzovoort. “Ik raad mijn klanten aan te beginnen met de eenvoudige dingen. Er is zoveel laaghangend fruit in de magazijnen die ik bezoek, dat het echt niet nodig is om ingewikkelde constructies te verzinnen. Maar het kan wel. Wij hebben in ons atelier intussen al een robot die we met een AGV kunnen oppakken en verplaatsen. In de toekomst zien we dus heel wat mogelijkheden waarbij robots erg flexibel van plaats kunnen veranderen en daar dan nieuwe taken uitvoeren. Een overkoepelend magazijnbeheersysteem zorgt dan voor een optimale indeling van robots met daarbij AGV’s die producten komen brengen en weghalen. Je configureert de fabriek in functie van een optimale workflow en je kan dat zo vaak je wilt, herhalen. Ik zie dat managers steeds meer af willen van een vaste infrastructuur in een magazijn of werkplaats. Rollenbanen en paternosters en andere logistieke apparaten zijn moeilijk verplaatsbaar. Voor logistieke dienstverleners die om de drie jaar een andere klant bedienen, is dat niet ideaal. De topmensen willen daarom liever investeren in technologie die flexibel en toch robuust genoeg is om nog vele jaren mee te gaan. Ze vragen ons dat ook: bewijs ons dat die robot straks een andere taak kan uitvoeren. En dan laten we zien dat zoiets perfect mogelijk is.”
Volgens Michael Vermeer zijn de huidige robots in de fabrieken nu al heel performant en blijven ze met een minimum aan onderhoud continu werken. Er bestaat ook een levendige tweedehandsmarkt voor robots. Zij krijgen dan een nieuw leven, vaak in kleinere bedrijven waar ze dan heel andere taken uitvoeren dan voorheen. Die robots zijn dus inherent multifunctioneel.
M. Vermeer: “Daarbij moet je dan ook bedenken dat die oude robots vaak blind zijn. Ze zijn niet uitgerust met visietechnologie. De nieuwe robots die wij nu installeren, beschikken wel over die 3D-visie en krijgen daardoor nog eens extra flexibiliteit.”
Robomotive werkt tegelijk nog aan nieuwe algoritmes om ook het plaatsen van producten bijvoorbeeld op een pallet te verbeteren. “De huidige palletiseerrobots zijn erop voorzien steeds dezelfde dozen te plaatsen. Wij willen echter dat de robot ook verschillende types dozen toch zo efficiënt mogelijk op een pallet zet. Dat is de Tetris-problematiek en we zijn er gerust op dat we ook die hebben opgelost”, besluit Michael Vermeer.