Meten is weten
Tips voor doelgericht Value Stream Mapping
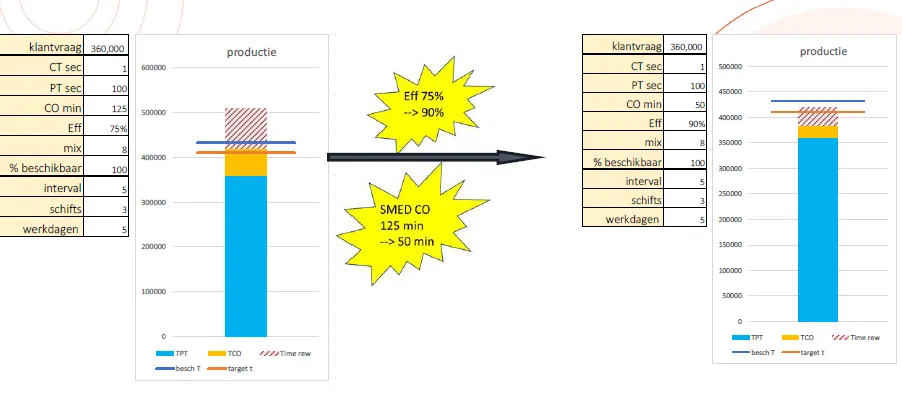
Value Stream Mapping Colorful Stickers Data Stockfoto 2148833039 | Shutterstock
Zorg ervoor dat tools als 5S en een effectief visueel management al goed functioneren voor je aan de implementatie begint. Als dat nog niet het geval is, integreer ze dan in je implementatieplan. Het is immers onbegonnen werk om in een chaotische productieomgeving naar een ambitieuze toekomstige situatie toe te werken.
In tijden van hoge kostendruk zijn efficiënte productieprocessen cruciaal. Het grootste potentieel voor verbetering ligt vaak niet in de productie zelf, maar in alles wat erom heen hangt. Value Stream Mapping is een krachtige tool om pijnpunten te identificeren en een solide basis voor optimalisering te leggen. Vanuit zijn praktijkervaring deelt Rik Desmet, trainer en coach bij PVO, tips om aan de slag te gaan en succes te boeken met Value Stream Mapping.
Binnen Lean Management visualiseert Value Stream Mapping de stroom van materialen en informatie doorheen het (productie)proces. Het doel bestaat erin verspilling te identificeren en te elimineren, wat resulteert in meer gestroomlijnde en efficiënte processen. “Om je processen te verbeteren, moet je weliswaar weten waar je problemen zitten. Dat is de basisgedachte van Value Stream Mapping”, begint Rik Desmet. “Verder is het belangrijk de kosten van elk probleem te kennen. Value Stream Mapping helpt je op basis van de impact van elk probleem prioriteiten te stellen. Dat maakt het een krachtig instrument voor ‘operational excellence’ en continue verbetering.”
Visueel overzicht
Value Stream Mapping biedt een visuele weergave van alle stappen die producten doorlopen, van grondstof tot eindproduct, en omvat zowel de fysieke als de informatiestromen. “Vergelijk het met een routeplanner’, illustreert Rik Desmet. “Als je blind op je systeem vertrouwt, kun je nog wel eens verkeerd rijden. Met een kaart heb je een helder overzicht, waardoor de kans groter is dat je op een efficiënte manier je bestemming bereikt. Een Value Stream Map onthult snel de belangrijkste bronnen van verspilling in je processen. Denk maar aan overtollige voorraden, onnodige wachttijden, overbodig transport of overproductie. Met dat inzicht kun je vervolgens gerichte verbeteringen doorvoeren.”
Productfamilies bepalen
Rik Desmet onderscheidt vier basisstappen bij het opstellen van een Value Stream Map. Eerst bepaal je de productiefamilie waar je je pijlen op wil richten. Daarna analyseer je de huidige situatie en vervolgens de toekomstige situatie. Ten slotte implementeer je verbeteringen die waarde toevoegen aan het proces.
“Je productfamilie(s) definiëren is een cruciale eerste stap”, meent Rik Desmet. “Een productfamilie bestaat uit producten die op een vergelijkbare manier door de productie stromen. Je moet er als het ware één flow mee kunnen maken. Als een bepaald product tien minuten van de machinetijd in beslag neemt en een ander pakweg twee uur, dan wordt het lastig om ze binnen dezelfde flow mee te nemen. Uiteraard is het mogelijk meerdere productfamilies te definiëren, maar dat zal de oefening complexer maken. Het is dan ook belangrijk daar een balans in te vinden. In de praktijk zal dat vaak een kwestie van ‘trial & error’ zijn.”
Stroomopwaarts mappen
Bij het ‘mappen’ van de huidige situatie neem je de drie basiscomponenten van Value Stream Mapping onder de loep. Om te beginnen is dat natuurlijk je productstroom. Daarnaast neem je de informatiestroom mee, waarbij je data kunt halen uit je ERP-systeem, planningstools, en dergelijke. De derde component is de tijdslijn, die je inzicht geeft in productietijden, wachttijden, enzovoort.
Rik Desmet: “Een goede raad: ga de vloer op om zoveel mogelijk informatie te verzamelen. Je computerdata zijn zeker nuttig, maar kunnen misleidend zijn en zijn vaak onvoldoende om je een perfect beeld te geven. Door stroomopwaarts door de afdeling te lopen, identificeer je sneller anomalieën. Ga je stroomafwaarts, dan zullen de volgende stappen in het proces vaak logisch lijken. Werk je stroomopwaarts, dan zul je je automatisch meer vragen stellen bij de verschillende stappen en zul je de oorzaken van problemen sneller ontdekken. Kijk en luister ook goed naar wat er op de vloer gebeurt. Besef dat je problemen die je niet waarneemt, later ook niet zult kunnen oplossen.”
“Voor elk proces verzamel je de relevante data: de procestijden, cyclustijden, ‘changeovers’, ‘rework’, stilstanden, enzovoort. Wil je ook inzicht in de voorraad, vertaal die dan naar het aantal dagen voorraad”, gaat Rik Desmet verder. “Heb je meer data nodig, voeg die er dan zeker aan toe, maar beperk je wel tot data die voor jou relevant zijn. Anders ben je niet meer lean aan het werken. Op basis van de verzamelde data kun je dan de nodige berekeningen in Excel maken.”
De doorlooptijd is de som van de totale procestijd (m.a.w. de som van alle gemeten procestijden) en de wachttijden (m.a.w. de tijd dat het product tussen de processtappen door op de volgende handeling wacht). “Maak je die oefening correct, dan komen de pijnpunten al snel bovendrijven”, zegt Rik Desmet. “Denk maar aan uitzonderlijk hoge wachttijden. Procestijden zijn doorgaans al geoptimaliseerd, maar wachttijden worden vaak over het hoofd gezien. Value Stream Mapping kan daar verandering in brengen. Uiteraard is het best mogelijk dat je proces geen mooie, rechte lijn is. Ook parallelle processen kun je mappen, maar dan zal wellicht een meer geavanceerde Value Stream Mapping nodig zijn.”
Komen er pakweg vijftig pijnpunten naar boven, dan is het natuurlijk onmogelijk die allemaal tegelijk aan te pakken. Het is dan ook cruciaal dat je je problemen categoriseert, zodat je eerst diegene kunt afhandelen die je het meest kosten.
Na de identificatie van de belangrijkste problemen kun je analyses en strategieën beginnen te ontwikkelen om verspilling in het proces te verminderen of te elimineren. Dat kan bijvoorbeeld door de processen te herzien, voorraadniveaus te optimaliseren of efficiëntere communicatiesystemen op te zetten. Daarbij is het essentieel dat je een duidelijk beeld hebt van de gewenste toekomstige situatie.
R. Desmet: “Veel mensen beginnen op dit punt te brainstormen. Hoewel ik daar zeker geen bezwaren tegen heb, is het praktischer om de toekomstige situatie op een gestructureerde manier in kaart te brengen. Zo voorkom je dat je belangrijke problemen over het hoofd ziet.”
De bedoeling is ook om een toekomstige situatie te creëren die je een betere structuur biedt om optimalisering door te voeren en die een betere connectie tussen processen mogelijk maakt. “Vaak zie je in de huidige situatie dat productieafdelingen uit veel losse entiteiten bestaan”, vertelt Rik Desmet. “Er wordt iets geproduceerd dat vervolgens ‘over de muur wordt gegooid’ naar de volgende stap. In die fase is het belangrijk dat je erover nadenkt hoe je de verschillende stappen beter kunt verbinden voor een efficiëntere werking.”
Huidige versus toekomstige situatie
Rik Desmedt adviseert om uit te gaan van een ‘to-be scenario’ dat drie tot zes maanden in de toekomst ligt: “Als de doelen te ver weg worden gezet, ontbreekt de urgentie om eraan te beginnen”, waarschuwt hij. “Uiteraard kun je daarnaast ook toewerken naar een ‘ideale situatie’, die bijvoorbeeld drie jaar verder ligt.”
Verder noemt hij het raadzaam de huidige situatie naar de toekomstige te vertalen aan de hand van drie keer drie basisvragen vanuit verschillende invalshoeken: klantgerichte vragen, productiegerichte vragen en organisatiegerichte vragen.
Klantgerichte vragen
- Wat zijn de behoeften en verwachtingen van de klant?;
- Hoe wordt waarde gedefinieerd vanuit het perspectief van de klant?;
- Hoe kan de doorlooptijd van het product (of dienst) voor de klant worden verkort?
Productiegerichte vragen
- Welke stappen in het productieproces voegen echt waarde toe?;
- Waar zit de verspilling in het proces en hoe kan die worden geëlimineerd?;
- Hoe kan de flow van het productieproces worden verbeterd?
Organisatiegerichte vragen
- Hoe zijn de processen binnen de organisatie gestructureerd?;
- Hoe kunnen de communicatie en de informatieoverdracht tussen de afdelingen worden geoptimaliseerd?;
- Welke veranderingen zijn nodig om een cultuur van continue verbetering te ondersteunen?
Aan de hand van een voorbeeld illustreert Rik Desmet hoe je de huidige situatie tegenover de gewenste toekomstige situatie kunt zetten (zie figuur). Aan de linkerkant staat de huidige situatie, aan de rechterkant de toekomstige. De figuur geeft visueel weer of het mogelijk is aan de jaarlijkse vraag van de klant te voldoen. De blauwe horizontale lijn geeft een indicatie van de totale beschikbare tijd, de rode lijn de beoogde productietijd om aan de klantvraag te voldoen. Die rode lijn ligt uiteraard lager dan de blauwe om ruimte te laten voor onvoorziene omstandigheden. Het blauwe deel van de balk toont de productietijd, de oranje balk de omsteltijden en het deel met de rode dwarsstrepen de problemen die zich voordoen.
R. Desmet: “In dit voorbeeld kom je in de huidige situatie tijd te kort om aan de klantvraag te voldoen. Je kunt tijd toevoegen door bijvoorbeeld in het weekend of in meer ploegen te werken. Zo zal de blauwe lijn hoger komen te liggen. Maar dat brengt natuurlijk kosten met zich mee. Een andere optie is de productie-efficiëntie te verbeteren. Dat kan bijvoorbeeld via een ‘Kaizen burst’. Zo wil men in dit voorbeeld de efficiëntie verhogen van 75 naar 90 procent. Daarnaast is het plan om aan de omsteltijden te sleutelen, zodat die van 125 minuten naar 50 minuten dalen. Een andere mogelijkheid is het verkleinen van de blauwe balk door producten in een andere familie te plaatsen, als dat mogelijk en nuttig is. Uiteindelijk krijg je zo een model waarin je verschillende mogelijkheden tegenover elkaar kunt afwegen, zonder ze al meteen in de praktijk te testen.”
Tijd om waarde toe te voegen
Wanneer er een consensus is bereikt rond de gewenste toekomstige situatie, kan de implementatiefase starten. Om de planning en de voortgang visueel weer te geven, is een Gantt-grafiek of een andere tool aan te raden. “Het is trouwens pas in deze fase dat er echt waarde aan de organisatie wordt toegevoegd”, benadrukt Rik Desmet. “Bereid je wel voor op het intensieve werk dat nodig is om zo’n implementatie te leiden en succesvol te maken.”
Een grondige voorbereiding is in elk geval een must. Zorg ervoor dat tools als 5S en een effectief visueel management al goed functioneren. Als dat nog niet het geval is, integreer die dan in je implementatieplan. Het is immers onbegonnen werk om in een chaotische productieomgeving naar een ambitieuze toekomstige situatie toe te werken.
R. Desmet: “Heb je die tools al geïmplementeerd, verifieer dan ook eerst of ze naar behoren functioneren. Bieden de borden genoeg informatie? Worden ze daadwerkelijk gebruikt? Kom je een bord tegen dat al een jaar geen update heeft gekregen, verwijder dat dan meteen. Als het een geruststelling kan zijn: continue verbetering hoeft helemaal niet ingewikkeld te zijn. Zo kun je met een eenvoudig Kamishibai-bord normale en afwijkende omstandigheden duidelijk en snel identificeren.”
Het is uiteraard belangrijk de verbeteringen in je langetermijnstrategie te verankeren. Daarbij kunnen andere hulpmiddelen, zoals het bekende achtstappenplan, van pas komen.
Tot slot adviseert Rik Desmet ook finance meteen in het hele verhaal te betrekken. “Ga na of de financiële opvolgparameters in lijn liggen met de lean-aanpak. Maak finance ook duidelijk dat het belangrijker is om stromen op te volgen dan vierkante meters. Een productiegebied kan op zichzelf efficiënt functioneren, maar als het niet goed met andere productiestappen is geconnecteerd, kan dat toch voor problemen zorgen. Ook hier kan Value Stream Mapping een handig hulpmiddel zijn om zulke zaken op een heldere en visuele manier te verduidelijken.
TC
Premium
Deze inhoud is enkel leesbaar voor ingelogde Value Chain abonnees.
Heeft u een abonnement op het Value Chain informatiepakket? Meldt u aan via onderstaande knop en lees het gewenste artikel of magazine online.