Magazijnautomatisering op kruissnelheid
Omnichanneloplossing ondersteunt Stichd bij verdere expansie
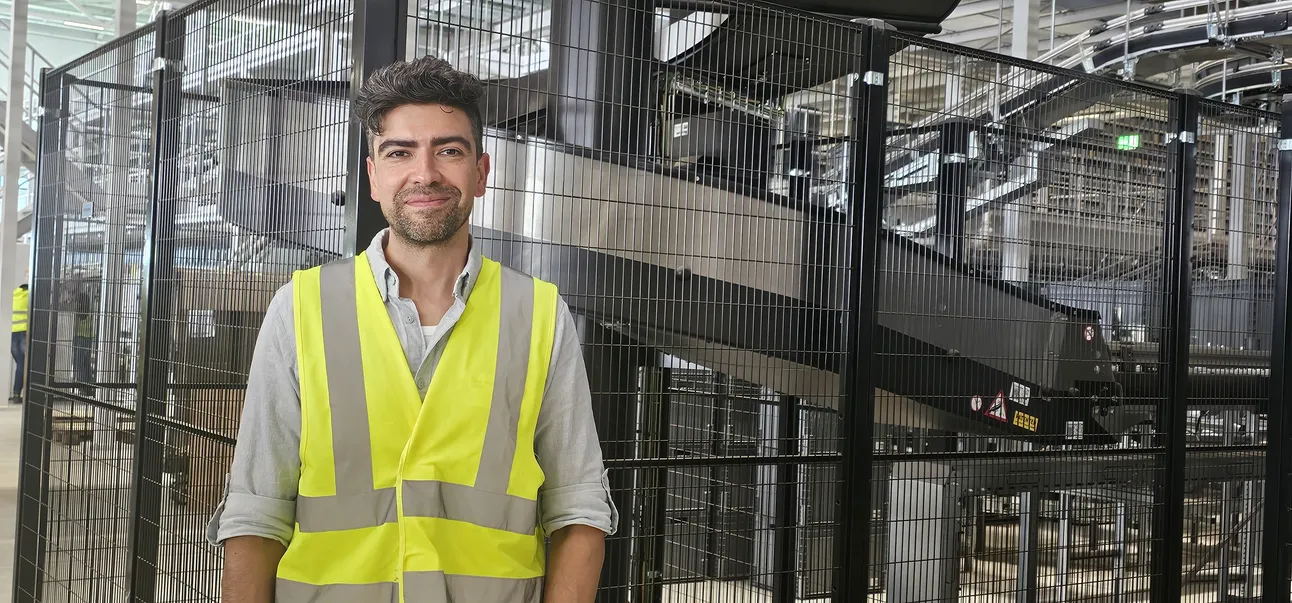
Kevin Kindt, manager operational excellence bij Stichd: “In eerste instantie bleek de grotere ruimte voldoende om de volumes te bolwerken, maar naarmate ons portfolio breder werd en de volumes groeiden, werd duidelijk dat we zouden moeten automatiseren om efficiënt te blijven werken.”
Het is alweer acht jaar geleden dat Stichd verhuisde naar een nieuw pand in het Nederlandse Tilburg. Aanvankelijk volstond de grotere ruimte om de activiteiten van het dochterbedrijf van Puma op te vangen, maar met de gestage uitbreiding van het assortiment steeg ook de nood om te automatiseren. Na een grondige analyse haalde het bedrijf het Flashpick-systeem van TGW Logistics Group in huis. Dat systeem helpt Stichd de groeikansen optimaal te benutten.
Onder het motto ‘consciously crafting convenience’ heeft Stichd zich gespecialiseerd in het ontwerp, de productie en de distributie van kwalitatieve ‘bodywear’, sokken en sinds enkele jaren ook zwemkledij. Het bedrijf startte in 1979 als een bescheiden sokkenproducent onder de naam Dobotex. In 2011 nam de Puma Group de organisatie over en sinds 2019 opereert die onder de naam Stichd. De internationale organisatie distribueert niet enkel Puma, maar ook andere ronkende namen als Levi’s, Calvin Klein en Tommy Hilfiger. Daarnaast ontwerpt, ontwikkelt en distribueert het bedrijf ‘fanwear’, in samenwerking met onder meer bekende Formule 1-teams en de bekende voetbalclub Manchester City.
Stichd telt vandaag dertien kantoren wereldwijd en kan rekenen op zevenhonderd medewerkers met in totaal 52 nationaliteiten. Het zwaartepunt van de activiteiten ligt in Europa, waar Stichd in elk land een verkoopentiteit heeft. In de andere continenten wordt met distributeurs gewerkt. Naast het distributiecentrum in Tilburg heeft Stichd nog dc’s in Mexico en Maleisië, die worden geoutsourcet.
Eerst meer ruimte, dan automatisering
Toen het vorige magazijn in Tilburg te krap werd, verhuisde de organisatie in 2016 naar een nieuw magazijn, aan de andere kant van de stad. Met zijn ruim 50.000 vierkante meter is dat ongeveer drie keer zo groot als het oude pand. Het nieuwe magazijn, dat liefst 41 laadkades telt, fungeert vandaag als centraal fulfilment center voor Stichd en wordt ondersteund door het hoofkantoor in ’s-Hertogenbosch. Er worden ruim 33.000 SKU’s (stock keeping units) opgeslagen. Vanuit Tilburg worden meer dan 150 landen bediend. Op itemniveau worden bijna tachtig miljoen packs per jaar verkocht, wat neerkomt op 600 packs per minuut.
Al bij de verhuizing acht jaar geleden vroeg Stichd zich af of automatisering een interessante piste was. Voor de nodige analyses werd het adviesbureau Groenewout in de arm genomen. “Op dat moment bleek de grotere ruimte voldoende om de volumes te bolwerken, maar naarmate ons portfolio breder werd en de volumes groeiden, werd duidelijk dat we zouden moeten automatiseren om efficiënt te blijven”, vertelt Kevin Kindt, manager operational excellence bij Stichd. “Mochten we op een conventionele manier blijven werken, zouden de medewerkers elkaar op den duur voor de voeten lopen. Om een idee te geven van de groei: tien jaar geleden realiseerden we nog een omzet van zo’n honderd miljoen euro, nu zitten we op meer dan vijfhonderd miljoen. Omdat we de analyses met Groenewout elk anderhalf jaar hadden herhaald, hadden we een goed beeld van het kantelpunt richting automatisering.”
De volgende stap was de selectie van een geschikte automatiseringspartner. “Met twee leveranciers hebben we verregaande gesprekken gehad”, vertelt Kevin Kindt. “Uiteindelijk hebben we gekozen voor TGW Systems, de Nederlands-Belgische entiteit van de groep, met kantoor in Oud-Gastel. We hadden vooral behoefte aan een bewezen oplossing, die de efficiëntie, flexibiliteit en de betrouwbaarheid van onze processen kon verhogen. Bij TGW was het vertrouwen het grootst dat we aan het juiste adres zaten. Bovendien was TGW ook verantwoordelijk voor de automatisering van het nog veel grotere distributiecentrum van Puma in Duitsland, wat ons vertrouwen sterkte.”
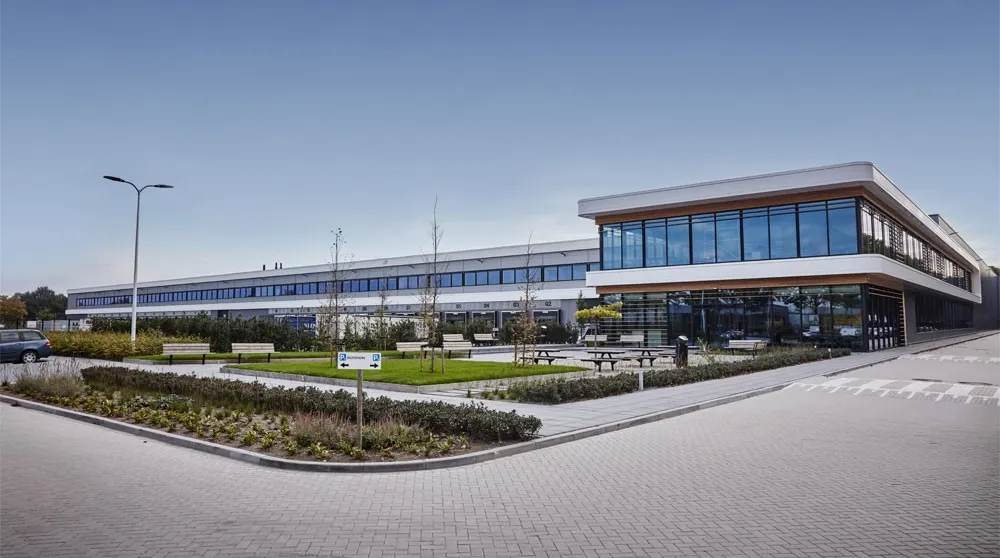
Het nieuwe magazijn in Tilburg is 50.000m² groot en telt 41 laadkades. Er worden ruim 33.000 SKU’s opgeslagen.
Operaties in en rond de FlashPick
Samen met TGW bracht Stichd de processen in kaart. Op basis daarvan werd de meest geschikte oplossing uitgewerkt. De FlashPick bleek de geknipte omnichanneloplossing om de verdere groei te ondersteunen. Het systeem laat immers toe meerdere verkoopkanalen – e-commerce, groothandel en retail – met dezelfde efficiëntie te bedienen. Omdat bij de bouw van het pand al rekening was gehouden met mogelijke automatisering, was ingecalculeerd dat daarvoor een extra compartiment aan het bestaande pand kon worden toegevoegd.
Het systeem bij Stichd bestaat uit een shuttlemagazijn van twaalf meter hoog met vijf gangen en twintig niveaus, met evenveel Stingray-robots. In het magazijn zijn 60.000 opslaglocaties voorzien. Via de shuttles en de liften worden voorraadbakken verzameld, die vervolgens naar de PickCenterOne-stations gaan. De producten voor de verschillende orders worden op de pickstations via de zogenaamde 1-op-1-techniek rechtstreeks in de kartonnen verzenddoos gelegd, wat zorgt voor een erg hoge efficiëntie. Eenregelige orders worden samen in een bak verzameld. Die bakken gaan vervolgens naar paktafels om per order uitgesorteerd en verpakt te worden. Die kleine orders gaan doorgaans in een zak of een enveloppe naar de klant.
Deze orderpickzone – waar tot 4.600 bakken per uur kunnen worden verwerkt – werd ingericht op een mezzanine die via een conveyorsysteem met het shuttlemagazijn is verbonden. In totaal doorkruist ongeveer vier kilometer aan KingDrive-conveyors van TGW het magazijn voor een autonoom en energie-efficiënt intern transport. Het WCS (warehouse control system) van TGW, dat is gekoppeld met het WMS (warehouse management system) van Stichd, controleert alle processen die gelinkt zijn met de automatisering.
Het FlashPick-shuttlemagazijn wordt gevoed met dozen die komen uit het rekkenmagazijn met bijna 35.000 locaties. Het gaat hier om duizelingwekkende volumes. Om een idee te geven: jaarlijks komen er zo’n 2.500 containers met dozen het magazijn binnen, wat neerkomt op ruim tien containers per dag. Een groot deel van die dozen wordt vanuit het smallegangenmagazijn naar aparte werkstations gebracht, de zogenaamde decanteerstations. Daar snijden medewerkers de dozen open om de producten vervolgens naar de voorraadbakken over te hevelen. Die gevulde bakken gaan dan via de conveyor naar het shuttlemagazijn. Het feit dat dit inboundproces strikt van het orderpickproces wordt gescheiden, zorgt voor een hoge efficiëntie.
Om de opslagcapaciteit van de FlashPick optimaal te benutten, wordt de voorraad van de bakken op gezette tijdstippen geconsolideerd. Die taak neemt de PickCenter Rovolution, een gerobotiseerd pickstation, op zich. Die robot voegt de inhoud samen van bakken met dezelfde referentie die voor minder dan de helft gevuld zijn. “We hebben ook bekeken of zo’n gerobotiseerd pickstation de orderpicking kon overnemen, maar dat bleek in ons geval niet optimaal”, vertelt Kevin Kindt. “Artikelen picken is voor de robot geen probleem, maar een medewerker schikt de artikelen tijdens het picken automatisch ook netjes in de verzenddoos. Dat doet een robot niet, waardoor een robotpicker gemiddeld meer dozen per order nodig zouden hebben. Aangezien elke extra doos hogere kosten voor papier en volume betekent, geven we voor het orderpickproces nog steeds de voorkeur aan menselijke orderpickers.”
Tegen de 95 procent van het e-fulfilmentproces wordt door de automatisering verwerkt. Aan het eind van de rit worden de kartons op de juiste hoogte afgesneden en automatisch gesloten door twee geautomatiseerde verpakkingsmachines. Tot slot worden de orders die klaar zijn voor verzending handmatig in de vracht- of bestelwagens geladen.
Goed geïntegreerde VAS-zone
Slechts een klein deel van de orders wordt nu nog op de traditionele manier verzameld, bijvoorbeeld volle dozen voor grotere orders. Daarnaast is en blijft de manuele VAS-zone (value added services) erg belangrijk voor Stichd. Meer dan zestig procent van de gepickte orders passeert langs die zone, waar de producten aan ruim honderd werkstations van prijsstickers en klantspecifieke labels worden voorzien. Ook de controle van orders – voor pickers die net zijn gestart ligt die frequentie hoger dan voor vaste krachten – vindt aan die werktafels plaats.
Hoewel de VAS-activiteiten handenarbeid blijven, heeft de naadloze integratie van dit proces in de geoptimaliseerde goederenstroom ook in deze zone tot een belangrijke efficiëntieverbetering geleid.
K. Kindt: “Na het pickproces stuurt de magazijnsoftware de dozen automatisch naar de VAS-zone. Alle dozen krijgen onderweg de nodige labels of tags mee en worden netjes verdeeld over de verschillende, ergonomisch ingerichte werkstations, waar de medewerkers de opdracht krijgen om de nodige handelingen te verrichten. Die manier van werken verloopt veel meer gestructureerd dan vroeger, toen de medewerkers gewoon pallets met dozen, een lijst en een krat vol stickers kregen. Nu geven we in de software met onze ‘competentiemeter’ elke medewerker ook een score – van een 1 voor de starters tot een 5 voor vaste medewerkers – zodat we de taken op basis van de moeilijkheidsgraad kunnen verdelen. Bij de inrichting van de werkplekken hebben we ook goed naar onze medewerkers geluisterd. Zo staan de tafels naar elkaar toe gekeerd, wat sociale interactie tijdens het werk mogelijk maakt. In de zones waar veel mensen werken, hebben we met grote raampartijen ook voor veel daglicht gezorgd. Dat alles leidt tot meer tevredenheid en een hogere productiviteit.”
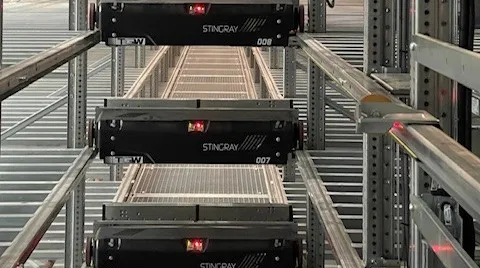
Het systeem bij Stichd bestaat uit een shuttlemagazijn van twaalf meter hoog met vijf gangen en twintig niveaus, met evenveel Stingray-robots. In het magazijn zijn 60.000 opslaglocaties voorzien.
Hogere efficiëntie, meer rust
Tegenwoordig draait het geautomatiseerde magazijn op kruissnelheid. Intussen heeft het ruimschoots bewezen de groei aan te kunnen. Zowel de grootvolume B2B-orders als de B2C-orders worden vlot door de oplossing verwerkt. Ook ondersteunt het systeem de verwerking en verdeling van alle fanwear, zoals petjes en shirts, een activiteit die Stichd sinds 2015 op zich neemt. Die fanwear wordt onder andere via de eigen website ‘Fuel For Fans’ verkocht.
Dankzij de automatisering kan Stichd meer doen, zonder meer mensen te hoeven inschakelen. “Om een idee te geven: we hebben zes PickCenterOne-stations geïnstalleerd, terwijl we in het conventionele magazijn dertig orderpickers nodig hadden. Tijdens de piekperiodes liep dat aantal zelfs op tot zestig”, illustreert Kevin Kindt.
Verder brengt de automatisering rust in het magazijn. Er werken nog steeds heel wat mensen op de site in Tilburg – 150 en 200 tot 250 in de piekperiodes – maar ze lopen elkaar niet in de weg en ze kunnen op een heel ergonomische manier werken. Ook niet onbelangrijk: tot nu toe kan Stichd nog steeds vasthouden aan een enkele shift en een werkweek van vijf dagen. In die tijd verwerkt het bedrijf zo’n 30.000 orderlijnen per dag. “Dat we niet met meerdere shifts werken, is vrij uniek in de regio. Heel wat medewerkers vinden dat fijn. Ook dat is een manier om mensen aan te trekken en te behouden”, voegt Kevin Kindt eraan toe.
Voordelen van gefaseerde implementatie
Wanneer Kevin Kindt terugblikt op het verloop van de implementatie, kan hij amper struikelblokken noemen. “We hebben veel te danken aan het feit dat we het volledige traject op een heel doordachte manier hebben aangepakt. Daardoor hebben we relatief lang over het project gedaan, maar het heeft er zeker ook voor gezorgd dat we onaangename verrassingen onderweg hebben kunnen vermijden.”
Zo werd TGW in maart 2020 geselecteerd, maar werd het contract pas eind dat jaar officieel getekend. “We hebben negen maanden de tijd genomen om het functionele design helemaal goed te krijgen. In mei 2021 zijn we met de constructie van de installatie van start gegaan en bijna een jaar later – in maart 2022 – zijn we met de testen van het systeem gestart. Veel bedrijven onderschatten die fase. Pas zes maand later – in september 2022 – heeft de installatie het overgenomen van de oude manier van werken en sinds begin 2024 draaien we op volle toeren.”
Groeiperspectieven
Al van bij het ontwerp van het logistieke centrum werden groeimogelijkheden voor de automatisering voorzien. Zo kan de capaciteit van het shuttleblock worden verdubbeld tot 120.000 opslaglocaties. Het is ook mogelijk die verdubbeling in twee fasen te realiseren.
“Dat die verdubbeling er zal komen, is wel zeker. Alleen weten we nog niet wanneer dat precies zal zijn”, besluit Kevin Kindt. “Maar dat belet ons niet tussendoor stappen te zetten om de efficiëntie verder te verbeteren. Zo krijgen onze zes PickCenterOne-stations nu versterking van een zevende station. Daarnaast hebben we het aantal decanteerstations opgetrokken van drie naar zeven, wat een nog snellere herbevoorrading van ons shuttlesysteem mogelijk maakt. Ook zijn we de VAS-zone nog aan het uitbreiden. Het is voor ons ook een hele geruststelling dat we zulke optimaliseringsslagen kunnen doen zonder de lopende operaties te verstoren.”
TC
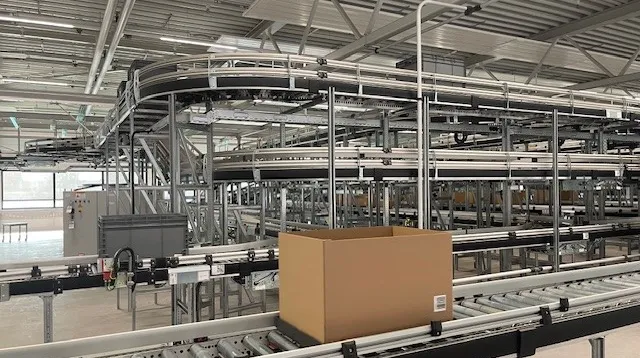
In totaal doorkruist ongeveer vier kilometer aan KingDrive-conveyors van TGW het magazijn voor een autonoom en energie-efficiënt intern transport.
Inloggen/registreren
Om deze content te lezen, moet u zich inloggen.
Log in of registeer nu via onderstaande knop en krijg toegang tot deze inhoud.