Logistieke efficiëntie is relevanter dan ooit
Toyota Productie Systeem (TPS) als basis voor lean manufacturing
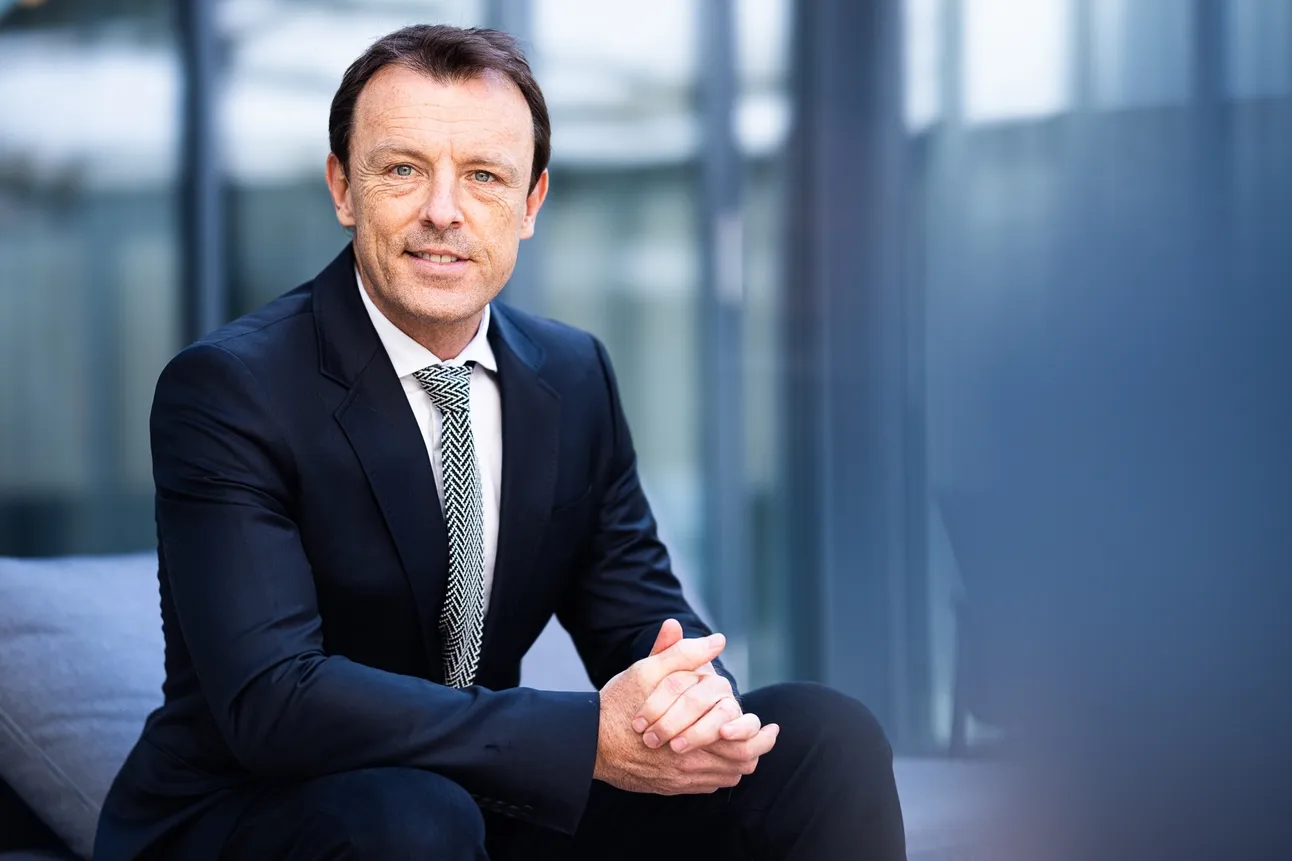
Het Toyota Productie Systeem (TPS) geldt algemeen als de roots van lean manufacturing. Het systeem is erop gericht de beste kwaliteit, de maximale veiligheid en de kortste doorlooptijd te realiseren door verspilling te elimineren. Maar hoe functioneert TPS vandaag en helpt het om de hedendaagse disrupties te beantwoorden? Jean-Christophe Deville, head of Toyota Vehicle Logistics Group, licht toe hoe de supply chain van de Japanse autofabrikant een onderscheidende factor vormt.
Lean manufacturing is tegenwoordig in veel bedrijfsmiddens ingeburgerd. Het idee vond zijn oorsprong in de eerste helft van de vorige eeuw, met het concept van Jidoka of intelligente automatisering, dat Toyota’s stichter, Sakichi Toyoda, ontwikkelde. Tien jaar later volgde ‘just in time’, om in tijden van schaarste op een efficiënte manier auto’s te produceren. Jidoka en just in time vormen vandaag nog steeds twee belangrijke pijlers binnen het Toyota Productie Systeem. Het TPS en het daaruit volgende ‘lean manufacturing’ verwierven wereldwijd erkenning via het boek ‘The machine that changed the world’ uit 1990, het resultaat van vijf jaar onderzoek onder leiding van het Massachusetts Institute of Technology (MIT).
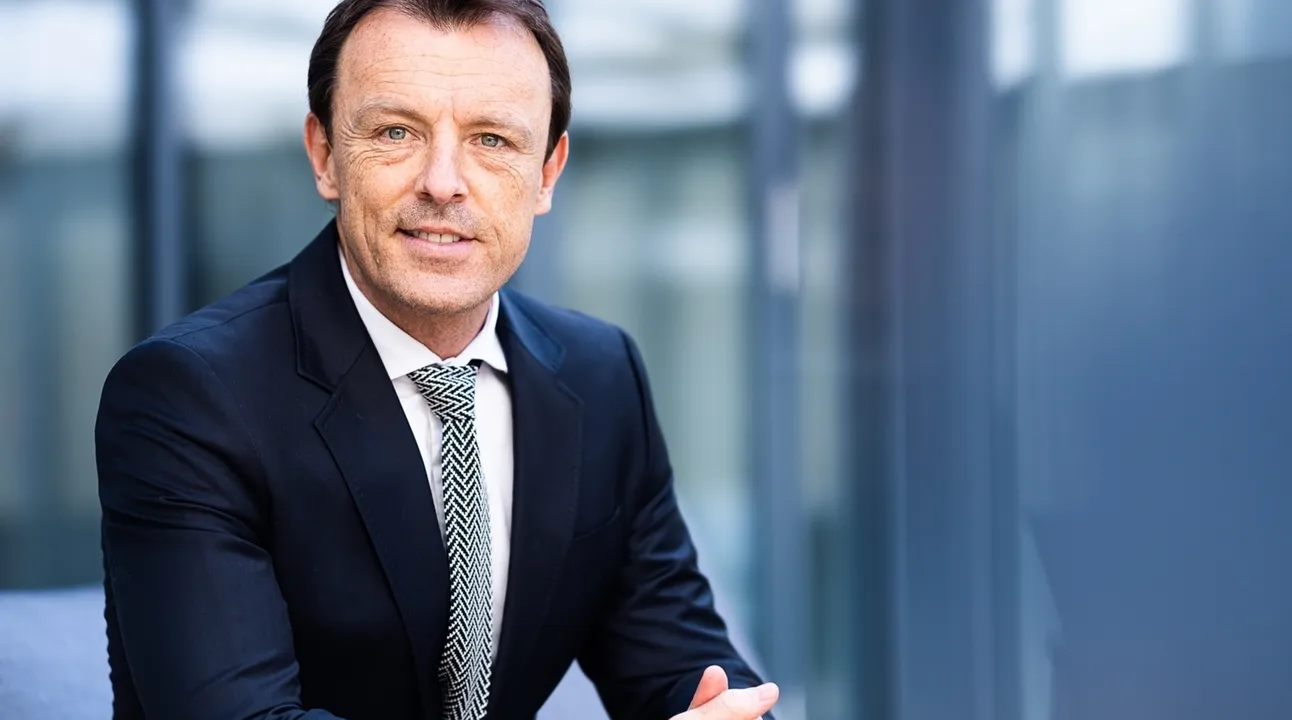
Just in time versus just in case
“TPS vormt de ruggengraat van onze organisatie”, legt Jean-Christophe Deville uit. “Het ondersteunt en leidt ons in alles wat we doen. Dat komt onder meer tot uiting in het ‘sell one, buy one’-principe. Wanneer de klant een wagen koopt, brengt dat een trigger in onze organisatie teweeg. Die zet zich door van onze depots, over de centrale magazijnen tot de leveranciers. Wanneer we een onderdeel nodig hebben, bestellen we niet meteen een volledige pallet, maar alleen het exacte aantal items dat we op dat moment nodig hebben. We werken dus niet volgens ‘just in case’, maar volgens just in time. Dat betekent niet dat we geen voorraad hebben, we beogen gewoon de juiste voorraad. De bufferstock is er niet zomaar, maar heeft altijd een doel. Het is de hoeveelheid die we nodig hebben om just in time te kunnen leveren. In het ideale scenario stemt het aantal aanwezige onderdelen exact overeen met wat onze operaties vereisen.”
Jean-Christophe Deville drukt het verschil tussen just in time en just in case plastisch uit. “We produceren auto’s in een hoog tempo, in sommige fabrieken rolt er elke 55 seconden een nieuwe auto van de band”, zegt hij. “Bij een just in case-scenario zouden we in elke fabriek de oppervlakte van een voetbalveld tot vier meter hoog moeten volstouwen met onderdelen. In Europa beschikken we over negen productiefaciliteiten, wat dus een grote druk op onze operaties en werkkapitaal zou zetten. Dat willen we absoluut vermijden.”
Om de voorraad tot de essentie te beperken, spelen ‘demand planning’ en ‘forecasting’ een essentiële rol. “Onze strategie bestaat er niet in auto’s te produceren en die dan in de markt te duwen. Onze werkwijze is sterk vraaggedreven”, gaat hij verder. “We baseren ons op historische data en actuele informatie, wat ons in staat stelt de nodige assumpties en marges te voorzien.”
De aanpak van Toyota krijgt wereldwijd navolging. De globale automobielsector is het voorbije jaar richting een just in time-aanpak geëvolueerd, stelt Jean-Christophe Deville vast. “De vraag naar auto’s overstijgt vandaag het aanbod, omwille van de schaarste aan onderdelen en de vertragingen bij de producenten”, weet hij. “Dat leidde ertoe dat elke speler zijn voorraad al dan niet noodgedwongen heeft gereduceerd. Wie over een voorraad van zes maanden beschikte, ziet die nu teruggeschroefd naar een stock voor één tot twee maanden. Op die manier kun je dus ook spreken van een just in time-scenario. Aangezien Toyota standaard lage voorraadniveaus kent, hoefden we minder ingrijpend te schakelen.”
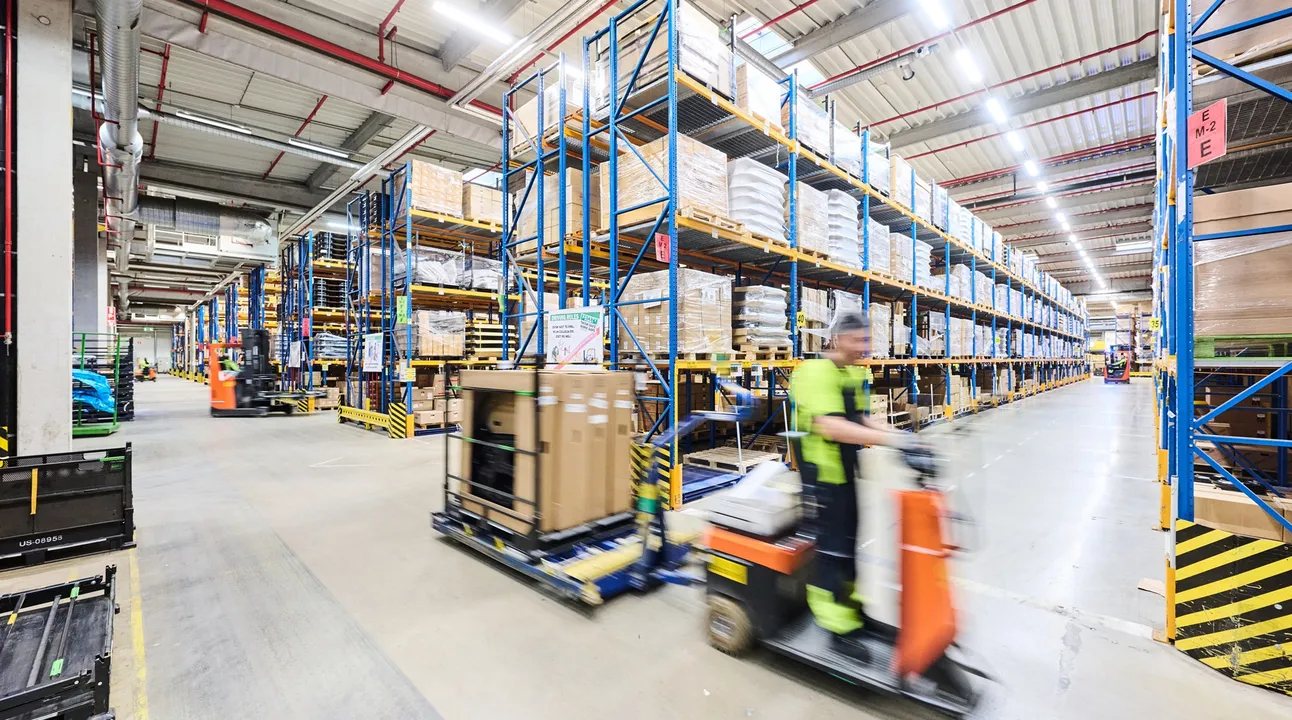
TPS als wapen tegen disrupties
Zoals dat in nagenoeg elke sector het geval is, raakten de verschillende disrupties ook de automobielsector. “Ik zit al enkele decennia in het vak, maar maakte nog nooit zo’n perfecte storm van gebeurtenissen mee”, aldus Jean-Christophe Delville. “Van weersinvloeden, over een gezondheidscrisis, tot logistieke congestie: echte stabiliteit was er de voorbije jaren nooit. Ik ga er van uit dat we dergelijke volatiele tijden als het nieuwe normaal moeten beschouwen. Een organisatie kan er zich dus maar beter tegen wapenen.”
TPS omvat een geheel eigen aanpak om met die disrupties om te gaan. Dat illustreert Jean-Christophe Deville aan de hand van het geblokkeerde Suezkanaal door het containerschip Ever Given. Obeya, wat staat voor ‘grote kamer’ in het Japans, vormt het vertrekpunt. “We verzamelen met alle belangrijke beslissingsnemers in één ruimte en focussen ons op concrete uitdagingen. We definiëren het probleem, gaan na wat we moeten oplossen en hoe we dat het best aanpakken. Zo’n meeting kan wekelijks plaatsvinden, maar organiseren we indien nodig zelfs meermaals per dag. We slaagden er op die manier al snel in om in te schatten op welke locatie onze onderdelen zich bevonden.”
Toyota nam tijdens de crisis door de blokkade van het Suezkanaal een drastische beslissing. “We kozen ervoor onze productie stop te zetten”, legt Jean-Christophe Deville uit. “Dat mag misschien eigenaardig lijken, maar voor ons was het volstrekt logisch. Overal traden vertragingen op. Geen enkele speler slaagde er nog in zijn magazijnen accuraat te bevoorraden. Dan kun je ervoor opteren auto’s te produceren die niet volledig afgewerkt zijn, met als doel ze achteraf volledig op punt te zetten. Dat past evenwel niet binnen onze filosofie. We produceren geen auto’s voor 99 procent, aangezien dat een risico op kwaliteitsverlies met zich mee brengt. Bovendien is de kans op desorganisatie bij een heropstart groot. Door onze keuze om de productie stop te zetten, konden we bij het vrijgeven van het Suezkanaal opnieuw met een propere lei beginnen. Daardoor konden we vlotter heropstarten dan veel andere fabrikanten. Niet toevallig slaagden we erin marktaandeel te winnen in tijden van crisis.”
Vertrouwensband met leveranciers
Een andere belangrijke component binnen TPS is de nauwe relaties met de leveranciers. Jean-Christophe Deville was jarenlang aankoopverantwoordelijke bij Toyota en stuurde die relaties zelf mee aan. “De band met onze leveranciers is om verschillende redenen bijzonder”, meent hij. “Een mooi voorbeeld is de korte betalingstermijn van 45 dagen die we hanteren. We vinden namelijk dat onze partners niet als onze bank moeten optreden. Een andere onderscheidende factor is openheid. We verwachten dat onze leveranciers de deuren van hun productiefaciliteiten altijd voor ons open stellen.”
Toyota stuurt negentig ingenieurs de baan op om leveranciers te bezoeken en hun onder meer de waarden van TPS bij te brengen. Openheid behelst ook een transparante communicatie. “We bieden onze leveranciers graag inzicht in de weg die Toyota wil inslaan”, klinkt het. “Op die manier ontstaat een grotere betrokkenheid. Van onze partners vragen we dan weer de nodige toewijding. We verwachten dat het management en de bestuursorganen van de leveranciers dicht bij de organisatie staan en weten wat zich binnen de bedrijfsmuren afspeelt. Evenzeer willen we dat onze leveranciers voor ons toegankelijk en bereikbaar blijven.”
Loyaliteit geldt als een onderscheidende factor. “We begrenzen het contact met onze leveranciers niet in de tijd”, vervolgt Jean-Christophe Delville. “Waar veel bedrijven jaarlijks van partner wisselen, niet zelden met besparing als oogmerk, kiezen wij ervoor onze leveranciers voor lange tijd aan ons te binden. Dat creëert zekerheid voor beide partijen. Die keuze betaalt zich in tijden van crisis ook vanzelf terug. Net omwille van dat vertrouwen beschouwen onze partners Toyota als een prioritaire klant, waardoor we bij disrupties op nauwgezette leveringen kunnen rekenen.”
Slimme automatisering en menselijke component
Jidoka of intelligente automatisering vertaalt zich in een sterke digitalisering van de supply chain. “Je kunt niet volgens het just in time-principe werken wanneer je niet exact weet hoeveel auto’s zich op een bepaalde locatie bevinden of er niet in slaagt de vraag in te schatten. Software helpt ons daarbij, maar de grootste toegevoegde waarde schuilt beslist in onze mensen”, aldus Jean-Christophe Delville. “Iedereen draagt TPS in zijn of haar DNA. Wanneer iets fout loopt in de supply chain, moedigen we onze medewerkers aan om meteen in te grijpen en indien nodig de machines onmiddellijk stil te leggen. Hoewel dat ons mogelijk tijd en geld kost, willen we onder geen beding inboeten aan kwaliteit en veiligheid.”
Jean-Christophe Deville is sinds anderhalf jaar verantwoordelijk voor de logistiek binnen het autoluik van Toyota. “In de huidige context van disrupties is er aan uitdagingen geen gebrek. Ik stel vast dat het topmanagement van Toyota het belang van onze afdeling erkent. Het beschouwt de manier waarop je een voertuig levert als een strategische determinant”, zegt hij. “De eisen voor de supply chain liggen ook almaar hoger. Wie vandaag een balpen van één euro bestelt, weet precies waar die pen zich bevindt en wanneer ze zal worden geleverd. Bij een auto van enkele tienduizenden euro’s is dat inzicht veel beperkter. Andere sectoren pushen ons dus om onze performantie dagelijks naar een hoger niveau te tillen.”
Inloggen/registreren
Om deze content te lezen, moet u zich inloggen.
Log in of registeer nu via onderstaande knop en krijg toegang tot deze inhoud.