Koffie met minimum aan verspilling
UCC Coffee belicht leanstrategie in food processing
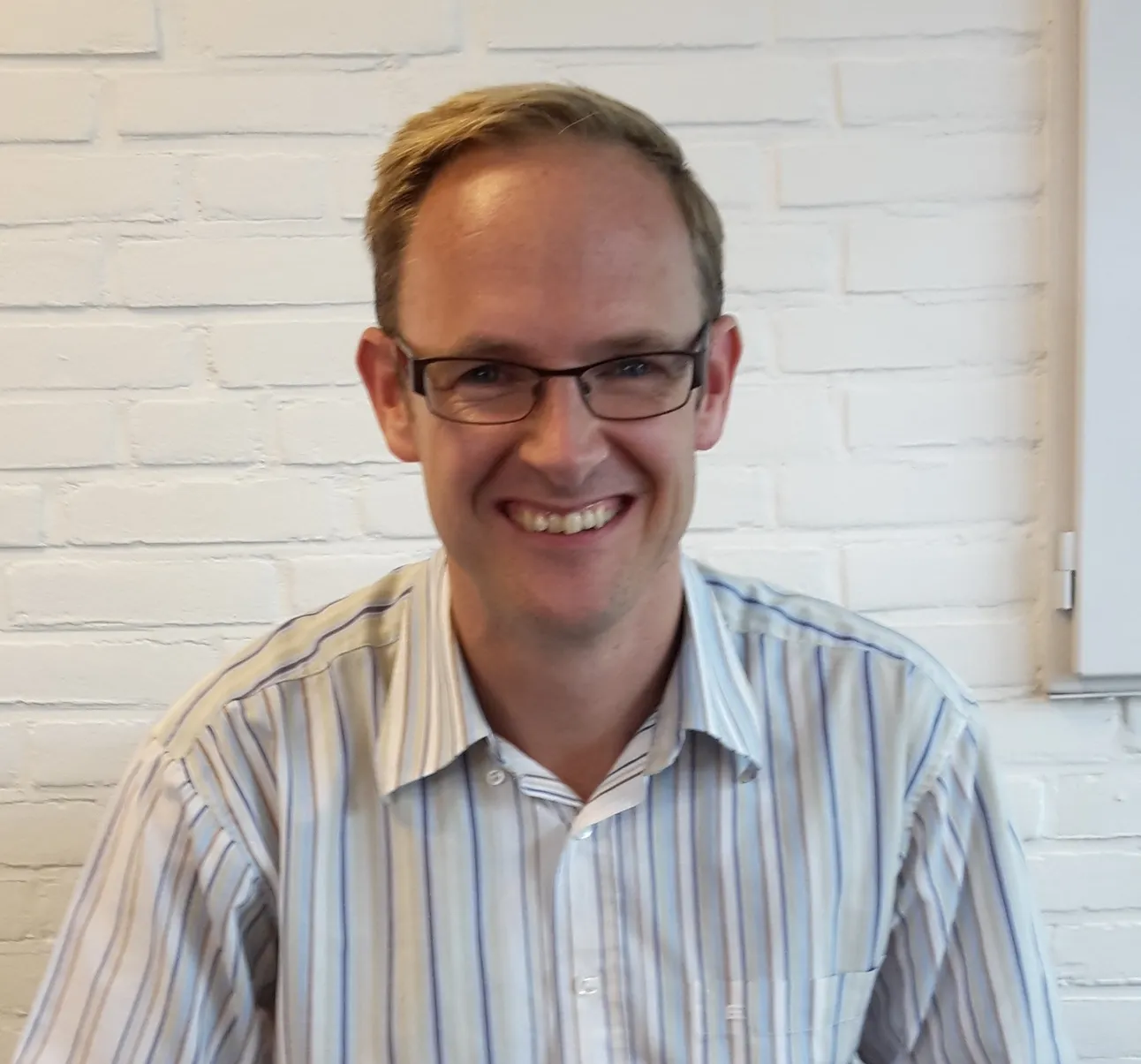
Een vijftal jaar geleden introduceerde koffiebedrijf UCC Coffee uit het Nederlandse Bolsward de leanfilosofie binnen zijn gelederen. Wat startte met een grote schoonmaak op de werkvloer, evolueerde naar een grondige optimalisering van het productieproces. Fokke Rosier, supply chain manager bij UCC Coffee Benelux, vertelt ons over zowel de kansen als de hindernissen op het pad naar een leanstrategie.
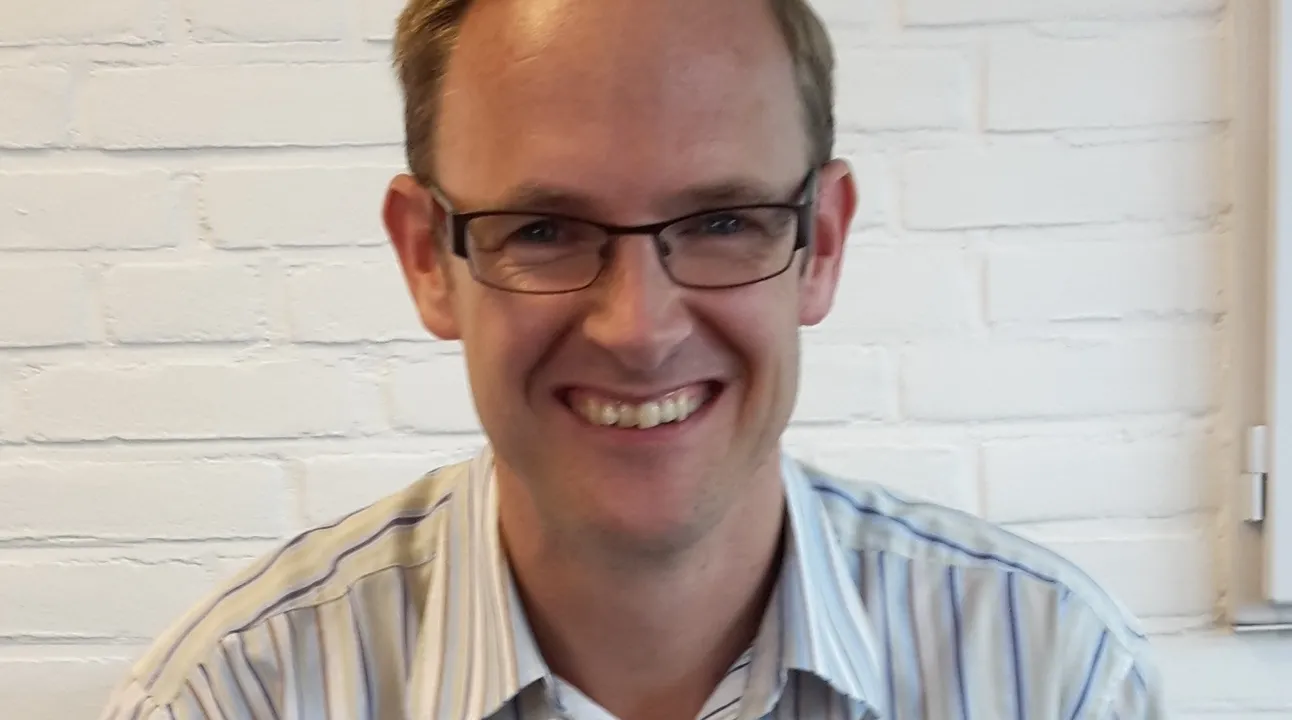
UCC Europe produceert en distribueert koffie, koffiemachines en diensten voor de detailhandel en de out-of-home markt. Dat de naam UCC Coffee u wellicht weinig zegt, komt omdat de fabrikant vooral huismerken en koffie in individuele porties levert. Klanten van het bedrijf zijn hotels, restaurants, cafés en onafhankelijke bedrijven.
In 2012 werd de Europese organisatie – die toen nog United Coffee heette – ingelijfd door het Japanse UCC Coffee. Met een jaarlijkse productie van 177.000 ton koffie behoort UCC Coffee tot de top zes reguliere koffiebranders wereldwijd. UCC Europe, met hoofdkantoor in London, produceert op zes locaties in vijf Europese landen. De fabriek in Bolsward is met 40% van het Europese volume de grootste site. Van daaruit worden de Benelux, Scandinavië, Duitsland en Oost-Europa beleverd.
De menselijke kant van lean
Een van de belangrijkste redenen voor de site in Bolsward om lean in de organisatie te lanceren, was de extreem hoge kostendruk binnen het marktsegment. “Als private labelproducent willen we in de eerste plaats kwalitatieve koffie bieden tegen een zeer scherpe prijs. Dat maakt ons erg kostengedreven. Daarbij komt nog dat we een vrij complexe, divergerende bedrijfsstructuur hebben. We starten met een veertigtal soorten groene koffiebonen, die we eerst branden en vervolgens verpakken in uiteenlopende hoeveelheden en verpakkingen. We stemmen ook heel veel eindproducten specifiek op de wensen van de klant af”, begint Fokke Rosier. “Voor ons was de kennismaking met de leanfilosofie – nog vóór we door een Japans bedrijf werden overgenomen trouwens – een logische stap in onze zoektocht naar manieren om beter met die kostendruk binnen deze complexe omgeving om te gaan.”
In eerste instantie werd besloten de lean basisprincipes op de werkvloer toe te passen. “We hebben het personeel in onze fabriek bewust gemaakt van verspilling of ‘waste’. We hebben hen uitgelegd hoe ze verspilling kunnen herkennen en hoe ze die kunnen vermijden. Met name het lean manufacturing begrip 5S (sorteren, schikken, schoonmaken, standaardiseren en systematiseren) hebben we hier nauwgezet naar de praktijk vertaald. Dat resulteerde in overzichtelijke werkplekken, vaste opruimmomenten, schaduwborden voor gereedschappen, het erkennen van verdienstelijke medewerkers, enzovoort. Alleen al die bewustmaking heeft ons al meteen enkele belangrijke ‘quick wins’ opgeleverd. De fabriek is nu ordelijker en overzichtelijker. Het omstellen van machines duurt daardoor minder lang, waardoor de organisatie uiteindelijk haar output heeft zien stijgen.”
Lean naar de productielijn
Een tweetal jaar geleden was UCC Coffee klaar voor de volgende fase. “Op dat moment hebben we lean tot een van de strategische pijlers binnen ons meerjarenplan verheven. Zo wilden we lean verder in het DNA van ons bedrijf laten doorsijpelen”, vertelt Fokke Rosier. “Aan het Lean Management Instituut hebben we gevraagd ons daarbij te helpen. We hebben toen mensen uit verschillende departementen samengebracht voor een ‘snelkookpansessie’. Een hele week lang hebben we toen intensief alle verbeteringspotentieel doorgelicht. Uiteindelijk bleek dat een heel goede manier te zijn om in korte tijd te bepalen wat voor ons de volgende stap zou worden.”
Binnen een proefproject zou de leanmethodiek op één bepaalde productielijn worden losgelaten: de zogenaamde Rovema-productielijn, waar hele gebrande koffiebonen in een zak rollen.
Fokke Rosier: “Dat was een heel uitdagende lijn, met kleine runs en een groot aantal setuptijden. Er passeerden ook heel veel verschillende SKU’s (Stock Keeping Units) op die lijn. Bovendien was de complexiteit er hoog omwille van de rits mogelijke verpakkingen en de gestage groei van het assortiment. Ook was het moeilijk een goede forecast voor die producten te maken, vooral omwille van het hoge aantal promoties. Verder hadden we geen goed inzicht in de set-uptijden van die lijn. Dat alles zorgde voor heel wat frustratie binnen de organisatie."
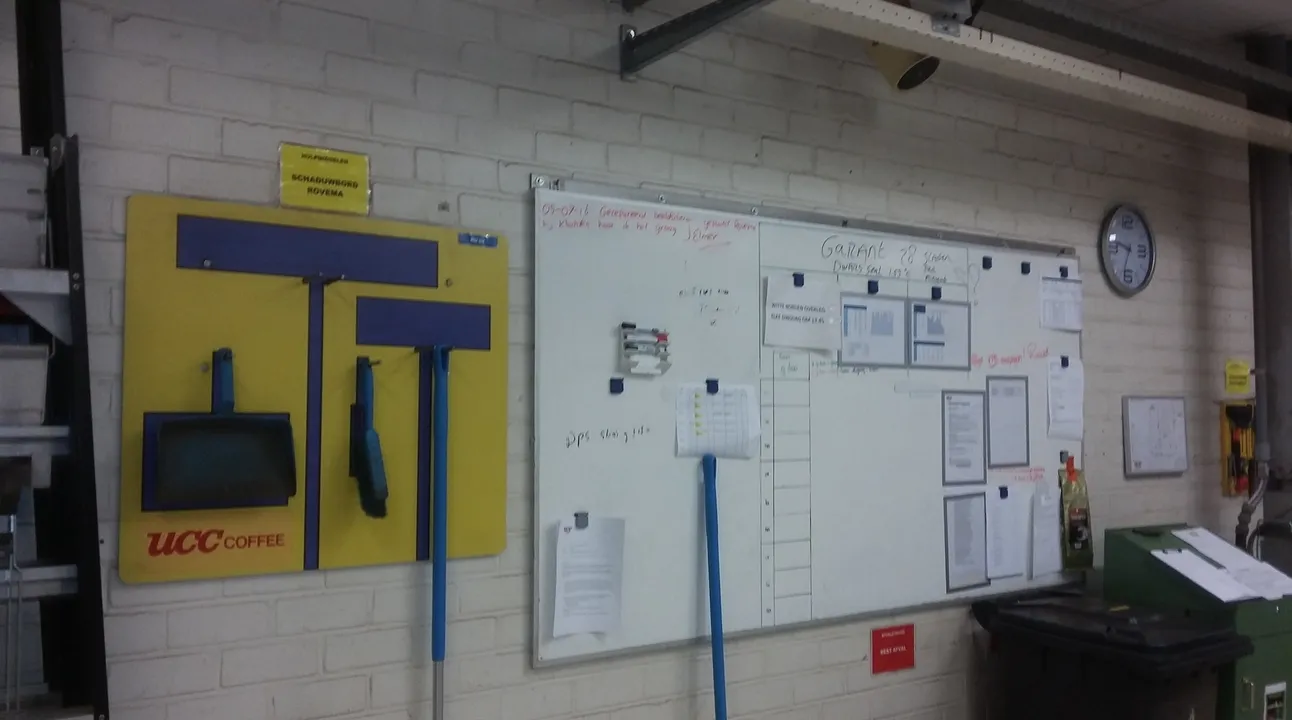
Duidelijkheid via stroomanalyse
UCC had bij het pilootproject meerdere doelstellingen voor ogen: “We wilden zien of we met minder personeel op die lijn konden werken. Als we erin slaagden onze activiteit op de lijn meer voorspelbaar te maken, zou onze technische dienst minder ad hoc onderhoud hoeven doen. Daarnaast wensten we vaste momenten voor machine setups in te voeren en de tijd die we nodig hadden voor de productieplanning te beperken. Tot slot wilden we ook de voorraden indijken.”
Samen met het Lean Management Instituut werd een ‘stroomanalyse’ gemaakt, waarbij de verschillende productstromen een kleurcode kregen naargelang het volume.
“Op basis van de verkoopdata hebben we onze goederenstroom gesplitst in een groene, gele, blauwe en rode stroom. Waarbij de meest interessante de groene is: snellopers met een vrij goed voorspelbare vraag. Aan de andere kant is er de rode stroom, waarvoor bekeken moest worden of het niet mogelijk is die te elimineren of de volumes te verhogen. Vooral belangrijk is om niet al te veel aandacht aan die rode stroom te geven.”
Daarnaast werden alle productgroepen binnen het assortiment geanalyseerd en werd bekeken welke clusters artikelen dezelfde eigenschappen hebben. Op die manier werden er per verpakkingsgrootte families samengesteld. Doel was een zicht te krijgen op de capaciteit die nodig was voor elke familie en de volgordes op de lijn aan te passen met het oog op minimale omsteltijden.
Switch in planningsmethodiek
De oefening resulteerde in een zogenaamd ‘planningswiel’, waarin dertien productiefamilies in een optimale planningscyclus werden gepuzzeld. Elke twee weken komt UCC Coffee terug bij dezelfde planningsfamilie in het wiel.
UCC Coffee wilde elke productfamilie een vast capaciteitsslot geven. “Zo kon de familie ‘verpakkingen van 8x1kg’ bijvoorbeeld de hele maandag en de helft van de dinsdag toegewezen krijgen”, illustreert Fokke Rosier. “Op die manier zouden we ook vaste tijdsstippen voor de machine-setup kunnen bepalen. Bijkomend voordeel was dat de aanvoer verpakkingsmateriaal gemakkelijker zou kunnen worden georganiseerd.”
De bedoeling was binnen elke productfamilie eerst de groenestroomproducten te produceren en pas daarna de rest. “Belangrijk is dat we die belangrijke producten zo constant mogelijk produceren en die ook elke productiecyclus maken. Voor de andere categorieën zouden we een welbepaalde capaciteit reserveren. Die capaciteit hadden we ruim gedimensioneerd. Is er capaciteit over, dan zouden we kijken of het interessant is om bepaalde producten op voorraad te maken.”
Theorie versus praktijk
Op bepaalde punten is UCC Coffee zeker in zijn opzet geslaagd. “De identificatie en reductie van de complexiteit binnen het assortiment vormden in elk geval een goed uitgangspunt voor de optimalisering. We hebben het voorbije anderhalf jaar circa 35 SKU’s van de Rovema-lijn weten te bannen”, zegt Fokke Rosier. “We zijn er ook in geslaagd vaste productievolgordes te verwezenlijken en de setuptijden te minimaliseren.”
Toch konden ook een aantal punten niet worden afgevinkt. “Het is ons helaas niet gelukt vast te houden aan vaste capaciteitsslots en vaste onderhoudstijden. Nog steeds halen we heel vaak zaken naar voren, zodat we voorraad en dus ook ‘waste’ creëren. Dat komt vooral omdat we te maken hebben met een zeer grillige vraagkarakteristiek. De eigenlijke verkoop verschilt te veel van de forecast. Met name onverwachte promoties gooien vaak roet in de planning. Daarnaast moeten we ook rekening houden met de eigenheden van onze producten. Zo moet onze geroosterde en gemalen koffie binnen een bepaalde tijdsspanne worden verpakt. Zulke zaken krijgen vaak prioriteit op de planning in het verpakkingsproces. Ook lastig zijn decafeïneproducten en biokoffie. Daar zitten allerlei schoonmaakregels voor de lijn aan vast, los van de omsteltijden. Die zaken zorgen ervoor dat je een theoretisch perfect uitziend leanconcept niet altijd naadloos in de praktijk kunt omzetten.”
Ook softwarematig liep alles niet van een leien dakje. “We werken momenteel met een ERP-pakket waar we in de loop der jaren veel maatwerk aan hebben toegevoegd. Om de nieuwe manier van werken te ondersteunen, hebben we onder meer bij de planning een paar menu’s toegevoegd, die een bepaalde volgorde in de scheduling voorschrijven. Daarnaast hebben we een procedure in het leven geroepen om nieuwe masterdata aan te passen en te onderhouden, om zo te vermijden dat er fouten in het systeem sluipen”, aldus Fokke Rosier. “De rol van IT in zo’n transformatieproces mag je niet onderschatten. Aangezien het wel duidelijk is geworden dat ons ERP tegen zijn grenzen aanloopt, zijn we intussen ook naar een nieuwe ERP-oplossing op zoek gegaan. Of we dan de planning binnen het ERP gaan opvangen of daarvoor beter een apart pakket inzetten, daar zijn we nog niet uit.”
De voordelen die uit het pilootproject zijn voortgevloeid, heeft UCC doen besluiten nog meer productielijnen lean te maken: “Bij elke omschakeling worden de baten tegenover de inspanningen afgewogen. Intussen kunnen we ongeveer de helft van de productielijnen lean noemen. Ook daar werpt de nieuwe manier van werken zijn vruchten af. Zo hebben we in de theeafdeling, waar we vooral omverpakken naar kleinere hoeveelheden, de gemiddelde bezetting zelfs kunnen verlagen.”
Volgens Fokke Rosier kunnen we dus gerust stellen dat – ondanks de toegevingen hier en daar – de leanstrategie loont. “We inspireren intussen ook andere Europese productiesites. Ook daar is er interesse om in de toekomst meer lean te gaan werken. Binnen ons Japanse moederbedrijf zit lean uiteraard nog meer in de organisatie ingebakken. We kunnen heel veel van hen leren, maar kunnen en zullen niet alles een op een toepassen. Daarvoor is onze cultuur te verschillend. We beseffen dat er nog werk aan de winkel is. Samen met het Lean Management Instituut zijn we nu aan het bekijken waar er nog verbeteringspotentieel schuilt. Dat we na de geboekte successen nog verdere stappen zullen zetten, is dus wel zeker”, besluit hij.