Innovating with Industry 4.0
Bringing together an ecosystem of partners showcases the value of prescription smart glasses for Signify.
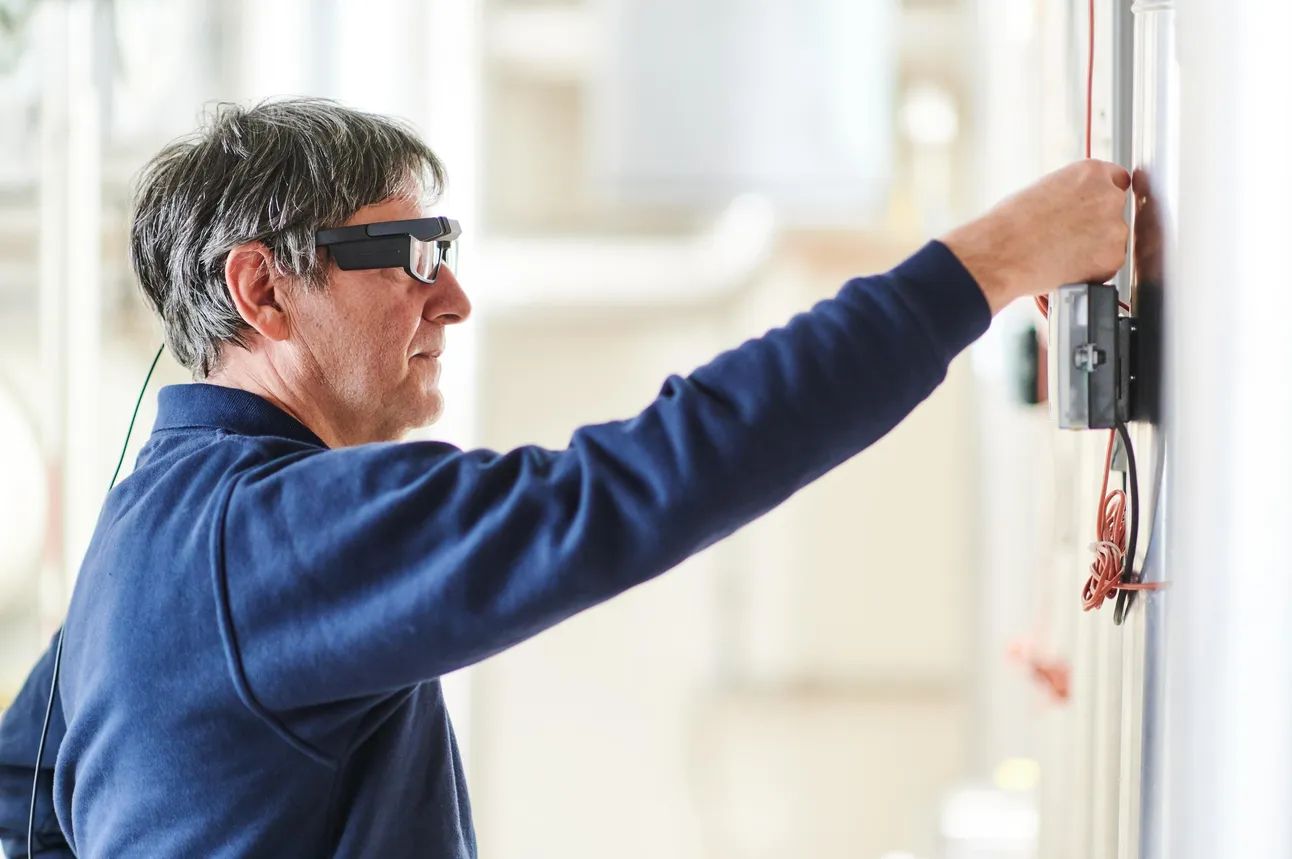
High-intensity discharge (HID) lamps have been around for more than 100 years, used both commercially and in homes. While largely replaced by more modern light-emitting sources in private properties, they’re still widely employed in commercial spaces by owners looking to reduce operational expenses and optimise their investment in infrastructure. Their replacement for other applications however means demand has and continues to slow substantially.
With HID lamps its main product, Signify in Turnhout has unsurprisingly seen its business shrink over the last few years. Despite this, it continues to invest. "The Turnhout facility’s always been a leader in automation and has always invested in the future. We’re continuing to invest in improving our processes to keep cost prices flat. We want to be the last man standing as it were; the last factory in the world producing HID lighting. We also want to keep our people fit for a job outside Signify," explains Lars van der Meulen, Signify Plant Manager.
Identifying the value of Industry 4.0
To help Signify achieve its ambitions, it’s working with five other parties to explore what Industry 4.0 could mean for the plant. In particular, the use of smart glasses for inspections on the shop floor, making the process voice-activated and entirely handsfree. The results of the project could have far-reaching implications not just for Signify, but for manufacturing firms around the world.
"For technicians, it’s quite important when they’re executing instructions or inspections that their hands are free to use tools, smart glasses enable that. There’s also the potential for remote assistance; people in a different location can see, via the lenses of the camera embedded in the glasses, what the person in the field’s facing and can talk to them in a handsfree call, shortening the time to solve an issue," says Peter Verstraeten, CEO of Proceedix, the platform that digitalises work instructions and checklists so they can be executed via handhelds, smart glasses and PCs.
Turning hype into reality
Johan De Geyter, CEO, Iristick concurs, "In the future, people will really rely on this. Instead of sending out a specialist technician to do the maintenance on a windmill for instance or a doctor having to physically consult on a patient with a colleague, they’ll call on this technology." Iristick’s the manufacturer of smart glasses used to support handsfree workers. He adds, "I think Industry 4.0’s a hype that’s becoming reality. Our smart glasses are one of the key technologies that can be used to enhance the operation functionality of handsfree workers."
"Smart glasses are going to conquer the world," states Guido Groet, CCO, Luxexcel, the 3D-printing company 3D prints lenses and is looking to make the eyewear of the future. "The same way that phones have changed and smartphones are now part of everyone's life. I believe there’s going to be a transition from the phone towards your glasses. This project is a good example of a real-life application," he notes.
Bridging the gap
Luxexcel’s the only firm in the world able to 3D print lenses. And it’s not just plain lenses they print, but corrective ones, a key element in the evolution toward the more common use of smart glasses - today, three out of four people require prescription glasses.
"You can’t make smart glasses if you don’t address the prescription of people's eyes. Our technology bridges the gap between the technology and prescription lenses, bringing it into one product, preferably something that looks like a traditional pair of glasses," Guido Groet says.
Connecting the dots
Acting as a bridge is something that PwC also actively seeks to achieve, especially to bring new technologies and innovation to bigger industrial manufacturers. "We try to identify the key value drivers for clients and how new technology can help them realise greater value. With a unique view on what’s valuable for shareholders and what makes sense from a strategic point of view, we’re able to translate that on a tactical level, meaning we can help identify the value of technology on a shop floor and explain to a management team, in an understandable way, why it’s valuable to the firm," says Jochen Vincke, Partner, PwC Belgium.
PwC Belgium’s role in the project has been to facilitate the process and bring parties together. "PwC’s always on the lookout for new technology, especially in the industry 4.0 environment. We really see PwC as an enabler to make projects successful. Its main strength is to bring all the parties to the table and connect the different dots to make it of real benefit to all stakeholders, including from a usability perspective and all other elements that are crucial to the success of a project," enthuses Johan De Geyter.
Taking manufacturing to new levels
Jochen Vincke goes further, "Guru-style consulting doesn’t exist anymore. We really need to find good partnerships and create ecosystems where we explore together to find new business cases and create innovation to bring manufacturing to the next level." That’s entirely the remit of the Open Manufacturing Campus (OMC) in Turnhout where Signify and Luxexcel are located.
As Signify has reduced capacity over the years, the OMC has renovated old production halls for use by smaller, fledgling firms and is actively supporting OMC residents with their growth ambitions. As such, its role has been to help facilitate collaboration between parties.
"We help start-ups grow faster by using our network and the competencies we still have here on site. This project is a great example of this. People who need corrective lenses aren’t a high priority for companies developing augmented-reality glasses. Luxexcel has the technology to print the lenses and Iristix develops the glasses themselves. Bringing the two together opens up a whole new market for both," explains OMC Operations Manager Leo Oelbrandt.
Simplifying inspections for Signify
For Signify’s service department, the creation of this specific ecosystem enables technicians on the shopfloor to inspect assets in a voice-controlled, handsfree way using glasses corrected to their specific prescription, meaning they can see "normally" with them also. They no longer have to record findings on paper or archive paper logs. Their hands are free to use tools as required. They can automatically keep track of statistics and see the evolution of trends. And they’ve complete proof that everything’s been inspected how it should be.
For Signify, "it simplifies administrative work for our people and frees them up to do other tasks. It’s a great initiative that I think other firms can also benefit from in the future," concludes Lars van der Meulen.