Hogere serviceniveaus, lagere voorraden
Wat mogen we verwachten van DDMRP (en wat niet)?
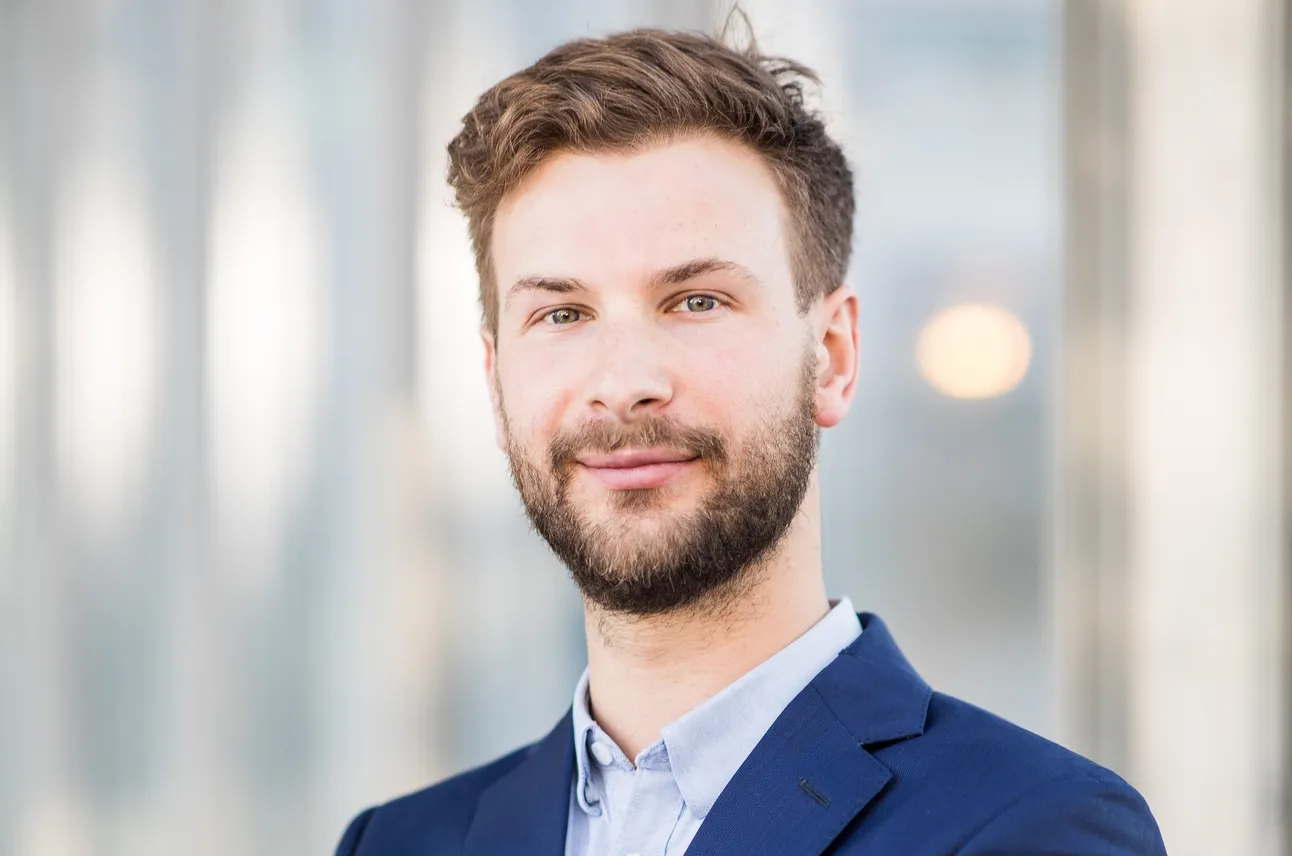
Steeds vaker rolt Demand Driven Material Requirements Planning (DDMRP) als alternatief planningsconcept over de tongen. Hoewel er nog niet gek veel bedrijven mee aan de slag zijn in België, biedt die nieuwe manier van plannen een aantal belangrijke voordelen, die zeker in de volatiele wereld van vandaag van pas kunnen komen. De hamvraag is of het interessant is dat concept ook op onze eigen processen los te laten. Een duwtje in de juiste richting kregen we alvast van François Grisay, manager bij PwC en docent Supply Chain aan de ICHEC Brussels Management School, tijdens onze virtuele editie van Supply Chain Innovations.
Kort samengevat is DDMRP een plannings- en executieconcept dat een antwoord wil bieden op de onvolkomenheden die eigen zijn aan de traditionele voorspelling gedreven Material Requirements Planning (MRP). De essentie van de methodiek is dat ze focust op de werkelijke vraag van klanten. Vooral in complexe, volatiele en servicegeoriënteerde productieomgevingen voelt dit concept zich in zijn element. De methode werd voor het eerst volledig omschreven in de laatste editie van Orlicky’s Material Requirements Planning (McGraw-Hill, 2011).
“Je hebt mensen die fan zijn van DDMRP, anderen beweren dan weer dat het concept niets nieuws onder de zon biedt. The Demand Driven Institute stelt dat er wel degelijk voldoende innovatie in zit”, zegt François Grisay. “Mijn standpunt is dat DDMRP verschillende bestaande theorieën met elkaar combineert waarvan bewezen is dat ze goed werken. Om te beginnen doet DDMRP nog steeds een beroep op de push-logica van MRP als backbone. Die wordt gecombineerd met de lean filosofie, die pull-gericht is. Last but not least wordt daar de Theory of Constraints aan toegevoegd. Die managementtheorie, ontwikkeld door Eliyahu Goldratt, stelt dat we de knelpunten in elk proces eerst moeten oplossen vooraleer het proces kan worden voortgezet. Het DDMRP-concept combineert in feite het beste uit die drie werelden."
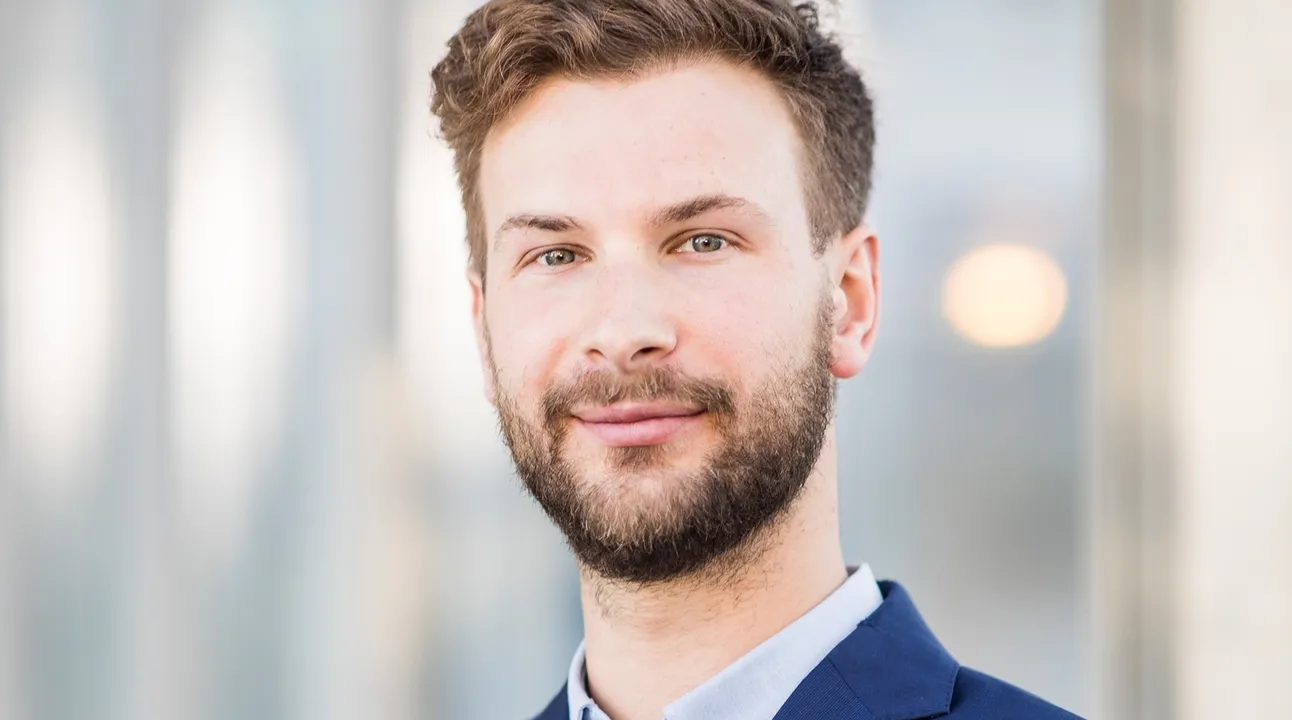
Planningsconcept met potentieel
Gebruikers van het eerste uur zijn bijvoorbeeld Coca-Cola, Shell, Unilever en Nestlé. “Toen Coca-Cola DDMRP in Zuid-Afrika implementeerde, zorgde dat voor enkele opmerkelijke verbeteringen. Zo steeg het serviceniveau met 12%, terwijl het voorraadniveau met 27% daalde. Dat heeft de organisatie doen besluiten het concept ook in andere landen te implementeren”, illustreert François Grisay.
Als we er de sectoren bijnemen waar DDMRP vandaag wordt toegepast, zien we dat vooral FMCG-bedrijven er al mee aan de slag zijn, gevolgd door industriële productie, chemie en farma & life science. Figuur 1 geeft de gemiddelde resultaten weer binnen de genoemde sectoren, grote en kleinere bedrijven door elkaar genomen (zie figuur 1). Daarbij zien we dat de voorraadniveaus met de komst van DDMRP in elke sector sterk dalen, de grootste winst op het vlak van serviceniveaus wordt geboekt in de industriële productie.
Logischerwijs haalt een bedrijf het meest uit DDMRP wanneer de maturiteit op het vlak van planning niet erg hoog is. Dat weerspiegelt zich bijvoorbeeld in een laag serviceniveau, een hoog voorraadniveau of een lage forecastaccuraatheid. Verder zal in die omgevingen plannen dikwijls gepaard gaan met een zekere nervositeit en vaak veranderende prioriteiten.
Ook bedrijven met een complexe planning zullen makkelijker voordeel uit DDMRP halen. Die complexiteit kan zich uiten in een grille vraag, een onbetrouwbare bevoorrading, een complexe Bill of Materials in productieomgevingen en/of een netwerk met verschillende niveaus in distributieomgevingen. Kamp je met een hoge complexiteit en heb je een lage maturiteit op het vlak van planning, dan biedt DDMRP uiteraard het hoogste potentieel.
François Grisay: “Dat bedrijven die aan de slag gaan met DDMRP vooral hun serviceniveaus zien verbeteren en tegelijk hun voorraadniveaus zien verlagen, is best bijzonder. Voor de meeste bedrijven is het immers een grote uitdaging om die twee zaken in evenwicht te krijgen."

Fietsen door het DDMR-concept
Hoe DDMRP precies werkt, illustreert François Grisay aan de hand van een simulatie. Die is gebaseerd op een fictief bedrijf dat elektrische fietsen produceert. Om de fietsen te vervaardigen, zijn verschillende onderdelen nodig zoals frames, wielen, batterijen en verschillende verven. Als de nodige stukken eenmaal aanwezig zijn, kan de producent de fietsen assembleren en schilderen.
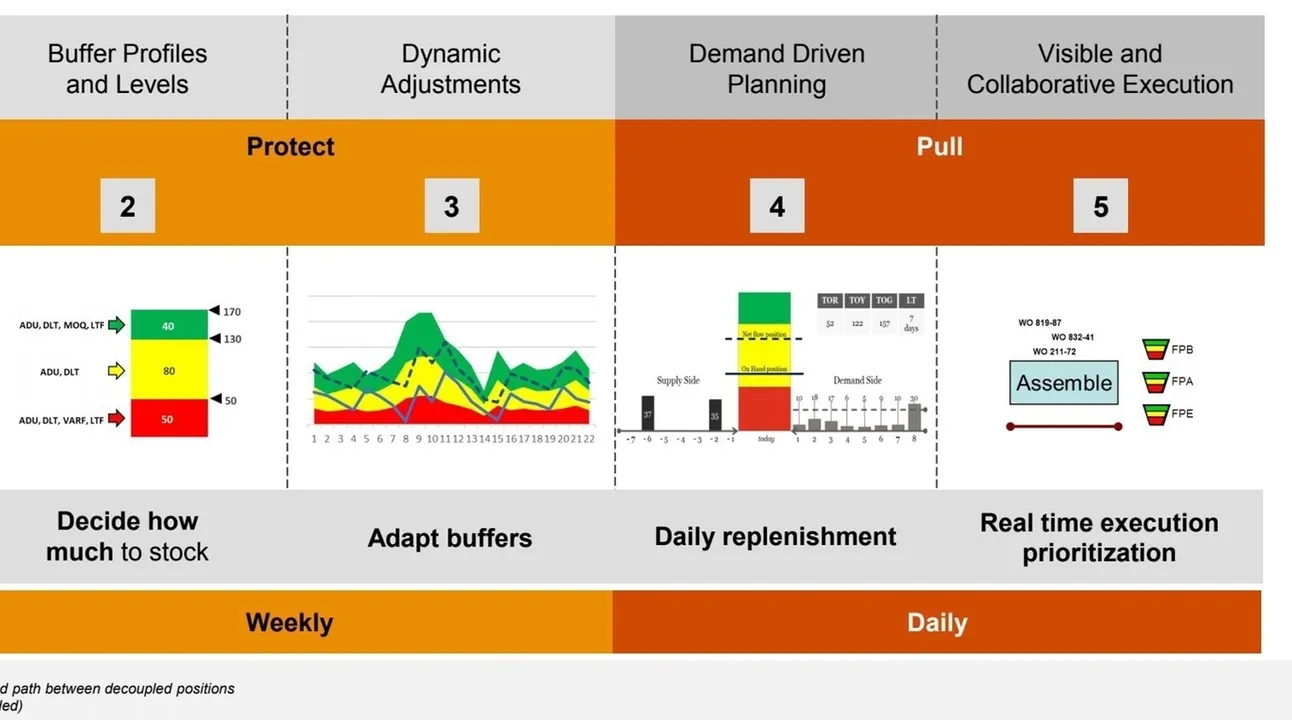
Traditionele MRP …
In de set-up nemen we drie verschillende fietsen mee: zwarte, gele en rode. “Hoewel het hier om een vrij eenvoudige supply chain gaat, kan er flink wat fout lopen. In de simulatie bedraagt de cumulatieve leadtime van aanlevering, assemblage en verven dertig dagen. Voor de aanlevering van de grondstoffen zijn twintig dagen nodig, voor de assemblage vijf dagen en om de fiets te verven nog eens vijf”, legt François Grisay uit. “Stel dat de batterij vijf dagen later komt dan voorzien, dan zijn onze grondstoffen pas na 25 dagen beschikbaar voor assemblage. Wat er dan typisch gebeurt, is dat er druk wordt gezet op de assemblagelijn. Dan wordt bijvoorbeeld gevraagd die klus in drie dagen te klaren. Maar vervolgens blijkt het verven van de zwarte fietsen een bottleneck te vormen, waardoor de cumulatieve leadtime alsnog langer wordt. Zulke frustrerende voorvallen zien we in de praktijk heel vaak.”
Laten we even inzoomen op de forecast die in deze set-up nodig is om de vraag te voorspellen. Die moet minimaal dertig dagen voordat de vraag binnenkomt, worden gemaakt. In een traditionele MRP-set-up voeren we wekelijks of tweewekelijks de MRP-runs uit, waarbij we telkens de vorige forecast met de nieuwe overschrijven.
F. Grisay: “Voorspelt de nieuwe forecast hogere volumes dan de vorige, dan krijg je stress in de tent. Dan kan bijvoorbeeld blijken dat je te weinig grondstoffen hebt. Voorspelt de nieuwe forecast veel lagere volumes, dan kunnen de fabrieksmedewerkers de indruk krijgen dat ze voor niets hard aan het werken zijn. Blijkt aan het einde van de rit dat de vraag daadwerkelijk hoger ligt dan de forecast, dan kan dat uitmonden in een out-of-stock-situatie. Is er overstock doordat de vraag uiteindelijk veel lager ligt, dan wordt het misschien moeilijk om er vanaf te raken. De combinatie van een zeer volatiele vraag met een traditioneel MRP-systeem kan bij de planner voor nervositeit en complexe situaties zorgen.
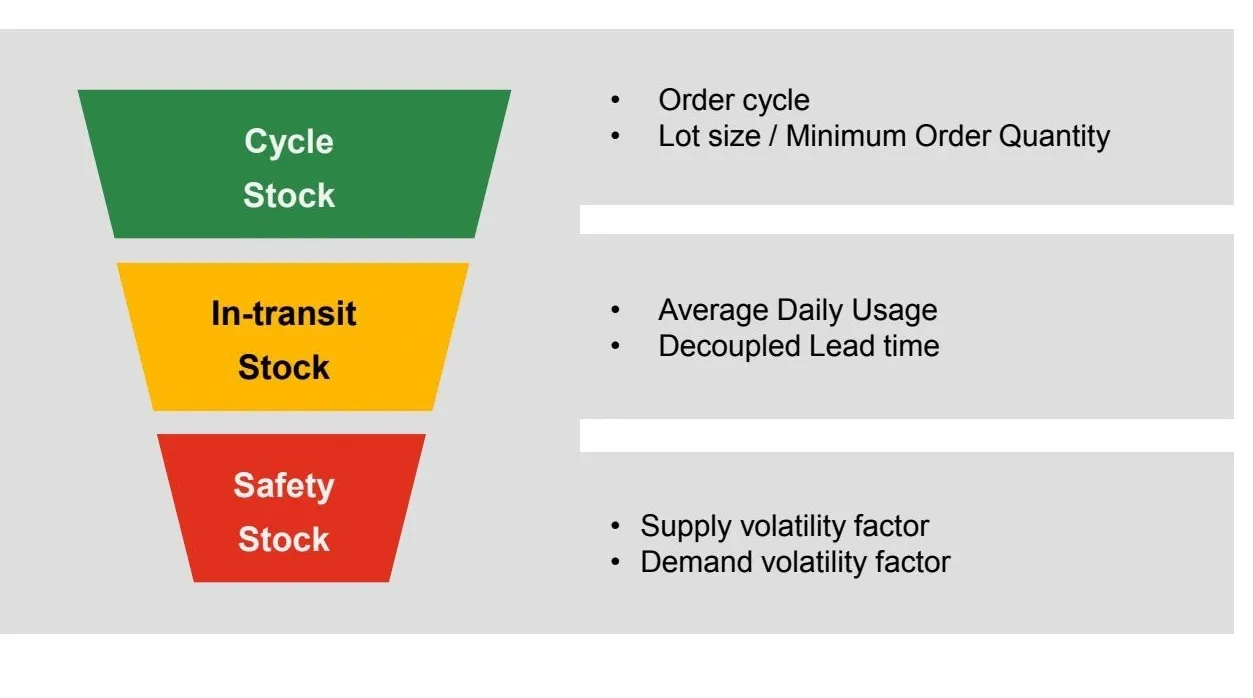
… versus DDMRP
Wat gebeurt er nu als we DDMRP op dezelfde set-up afvuren?
F. Grisay: “De achterliggende idee van DDMRP is dat de planning gebeurt met het oog op het zo snel mogelijk doen stromen van de goederen doorheen de supply chain. Belangrijk daarbij is dat sterk wordt ingezet op de strategische plaatsing van voorraden op ontkoppelpunten. Zo kan relevante informatie op cruciale momenten meteen worden meegenomen om een vlotte goederenstroom te garanderen.”
Binnen een DDMRP-proces kunnen we verschillende fases onderscheiden, waar we hier dieper op ingaan. Figuur 2 geeft die fases schematisch weer.
Stap 1: de voorraden strategisch positioneren
Om te beginnen moeten we zorgen voor een strategische positionering van de voorraden. “Vaak stoppen we heel wat moeite in het bepalen van de voorraadhoogtes, maar we vergeten onszelf de vraag te stellen waar we die voorraden dan het best plaatsen. Dat is echt de basis van DDMRP: bepalen waar we de ontkoppelpunten het best leggen. Dat is een oefening die we bijvoorbeeld jaarlijks kunnen doen.”
Stap 2 en 3: de stroom vrijwaren
In de tweede stap bepalen we de bufferprofielen en -niveaus. Daarbij moeten we ons in de eerste plaats de vraag stellen hoelang de klant op zijn elektrische fiets wil wachten. “In deze set-up is dat zeven dagen. We kunnen er uiteraard voor kiezen alle fietsen vroeger klaar te hebben dan wanneer de klant ze nodig heeft. Maar als we het voorraadniveau binnen de perken willen houden, is dat niet zo’n goed idee. Wel is het verstandig om van onze blockbuster – de zwarte fiets waar het schilderwerk een bottleneck vormt – voldoende afgewerkte goederen aan te houden. Hier zullen we dus een ontkoppelpunt voor zwarte fietsen creëren”, legt François Grisay uit. “Voor de rode en gele fietsen zien we sterkere schommelingen in de vraag. Voor die producten kunnen we aan ‘postponement’ doen en een aantal geassembleerde fietsen op voorraad houden. Die verven we dan pas geel of rood op het moment dat de klantenorders effectief binnenkomen. Hier ligt het ontkoppelpunt dus bij de geassembleerde fietsen.”
Blijkt dat sommige leveranciers het lastig hebben om ‘on time in full’ te leveren, dan kunnen we ook voor die grondstoffen een veiligheidsvoorraad aanleggen. In deze set-up blijkt dat het geval te zijn voor de batterijen. Daarvan kunnen we dus maar beter extra voorraad in huis hebben om onderbrekingen in de keten te vermijden.
Belangrijk is natuurlijk om te weten hoeveel extra voorraad we best aanhouden op die ontkoppelpunten. In DDMRP-taal spreken we hier over de ontkoppelde leadtime. “Dat betekent dat we voor elke voorraadpositie moeten bekijken welke leadtime we moeten beschermen. Die ontkoppelde leadtime is enerzijds gebaseerd op de assemblagetijd en anderzijds op de langste leadtime van de leverancier. In deze set-up zullen we bijvoorbeeld de leadtime voor de geassembleerde fietsen vijftien dagen beschermen.”, legt François Grisay uit. “Een ander belangrijk begrip bij DDMRP is het dagelijks gemiddelde verbruik. Voor onze blockbuster, de zwarte fiets, zijn dat tien eenheden, voor de gele en de rode komen we aan vijf eenheden. Die aantallen moeten we dan aggregeren om bijvoorbeeld het gemiddelde aantal nodige frames en verf te berekenen. De manier om de nodige voorraden te berekenen, is vergelijkbaar met de klassieke voorraadmanagementbenadering (zie figuur 3), met de cycle stock, de in-transit stock en de safety stock. Alleen is het bij DDMRP gemakkelijker om die berekeningen te maken.”
De buffervoorraden moeten uiteraard worden aangepast wanneer dat nodig blijkt. Dat gebeurt op een dynamische manier in de derde stap. “Om te beginnen zal er bij elke update van het gemiddelde dagelijkse verbruik een automatische aanpassing plaatsvinden. Die update kunnen we dagelijks of wekelijks doen. Daarbij hanteren we een rollende horizon van de gemiddelde consumptie, bijvoorbeeld over de laatste maand”, legt François Grisay uit. “Daarnaast zullen de voorraadniveaus moeten worden aangepast als er belangrijke veranderingen in de vraag worden verwacht. Denken we maar aan seizoenschommelingen, promoties en de in- of uitfasering van producten. Dat zijn typisch zaken die meegenomen worden in je Sales & Operations Planning om vervolgens door te geven aan de DDMRP.”
Stap 4 en 5: toevoegen van pullbenadering
Ook typisch bij DDMRP is de zogenaamde Net Flow Position. Die geeft aan welke hoeveelheden opnieuw moeten worden besteld en wordt berekend door de ‘on-hand’ voorraadpositie te vermeerderen met wat er op order is, om daar vervolgens de reële vraag van af te trekken.
F. Grisay: “Dat laat toe de herbevoorrading te laten triggeren door de echte vraag. Die vraag wordt vertegenwoordigd door de verkooporders en niet door de forecast, zoals bij de klassieke MRP-benadering het geval is. Die herbevoorrading via de demand driven planning vormt de vierde fase.”
Het is meegenomen dat de berekeningen met het oog op de herbevoorrading binnen het DDMRP-concept gemakkelijker zijn dan bij de traditionele aanpak. Dat komt doordat planners in de eerste plaats prioriteiten te zien krijgen. “Als het voorraadniveau voor een product in het rood zakt, weet de planner dat de herbevoorrading sneller moet gebeuren dan voor producten die nog een gele kleur hebben. In een traditionele MRP-set-up worden geen prioriteiten meegegeven, enkel een leverdatum. Bovendien krijgen planners die met een klassiek MRP werken niet zelden berichten die elkaar tegenspreken, wat tot verwarring kan leiden”, klinkt het. “Samengevat zullen we in de vijfde fase van de DDMRP realtime plannen en prioriteren.”
Een belangrijk voordeel van de realtime aanpak die DDMRP biedt, is dat de totale supply chain kosten vaak verminderen omdat we minder te kampen krijgen met last minute orders die snel – en dus vaak met een duur transportmiddel – moeten worden verscheept.
F. Grisay: “Maar voor alle duidelijkheid: het is niet omdat je DDMRP invoert, dat je helemaal geen forecasting of S&OP meer nodig hebt. DDMRP is in feite niet meer dan een planningsmethode voor de korte termijn, die in de eerste plaats helpt om je productie te schedulen en je voorraad beter te beheren. Een benadering op langere termijn – waarbij DDMRP en S&OP zeer nauw samenwerken en een forecasting richting geeft – is dus nog steeds nodig.”
TC
Extra info bij het artikel
Pragmatische aanpak
Hoewel DDMRP verschillende voordelen biedt, mogen we uiteraard niet onbezonnen naar die nieuwe aanpak overstappen. Daarom werkte PwC een pragmatische aanpak voor de overstap uit. “Om te beginnen is het belangrijk dat het bedrijf heel goed weet wat DDMRP precies inhoudt”, weet François Grisay. “Er bestaan nog heel wat misverstanden rond DDMRP. Die moeten eerst worden weggewerkt voordat je de volgende stap kunt zetten.”
In een tweede fase volgt een ‘Proof of Value’ “Dat is in feite een kleine business case, waarbij we bedrijven vragen hun data van het voorbije jaar met ons te delen. Vervolgens berekenen met een eigen Excel-tool wat DDMRP met die data zou doen. Die resultaten vergelijken we dan met de traditionele benadering. Uiteraard gaat het hier om een inschatting, maar het geeft wel al een richting aan”, legt François Grisay uit. “Komen daar positieve resultaten uit, dan zetten we binnen de Proof of Concept in één site een pilootproject op. Normaal gesproken zal dat project parallel met het bestaande systeem lopen. Daarvoor gebruiken we meestal een andere zelf ontwikkelde Excel-module. Zijn er te veel data, dan doen we een beroep op de software van Anaplan, waarin we ook een DDMRP-module hebben voorzien. Zo creëren we als het ware een DDMRP-schaduw van het bestaande systeem.”
Is het pilootproject een succes, dan kan worden beslist op verschillende sites een DDMRP-tool te implementeren, inclusief de site waar het pilootproject heeft plaatsgevonden.
F. Grisay: “Op dat moment wordt vaak gekozen voor de tool in Anaplan, die we finetunen op basis van de specifieke vereisten van het bedrijf. Maar uiteraard is er ook andere software die daarmee overweg kan. Tot slot is het belangrijk de processen op de nieuwe situatie af te stemmen en het veranderingstraject in je organisatie in te bedden. Het is immers cruciaal dat de betrokken partijen op alle sites helemaal mee zijn met DDMRP-verhaal. Alleen zo kun je garanderen dat de overstap ook echt zal slagen.”