Het belangrijkste proces
Optimaal orderverzamelen in het magazijn
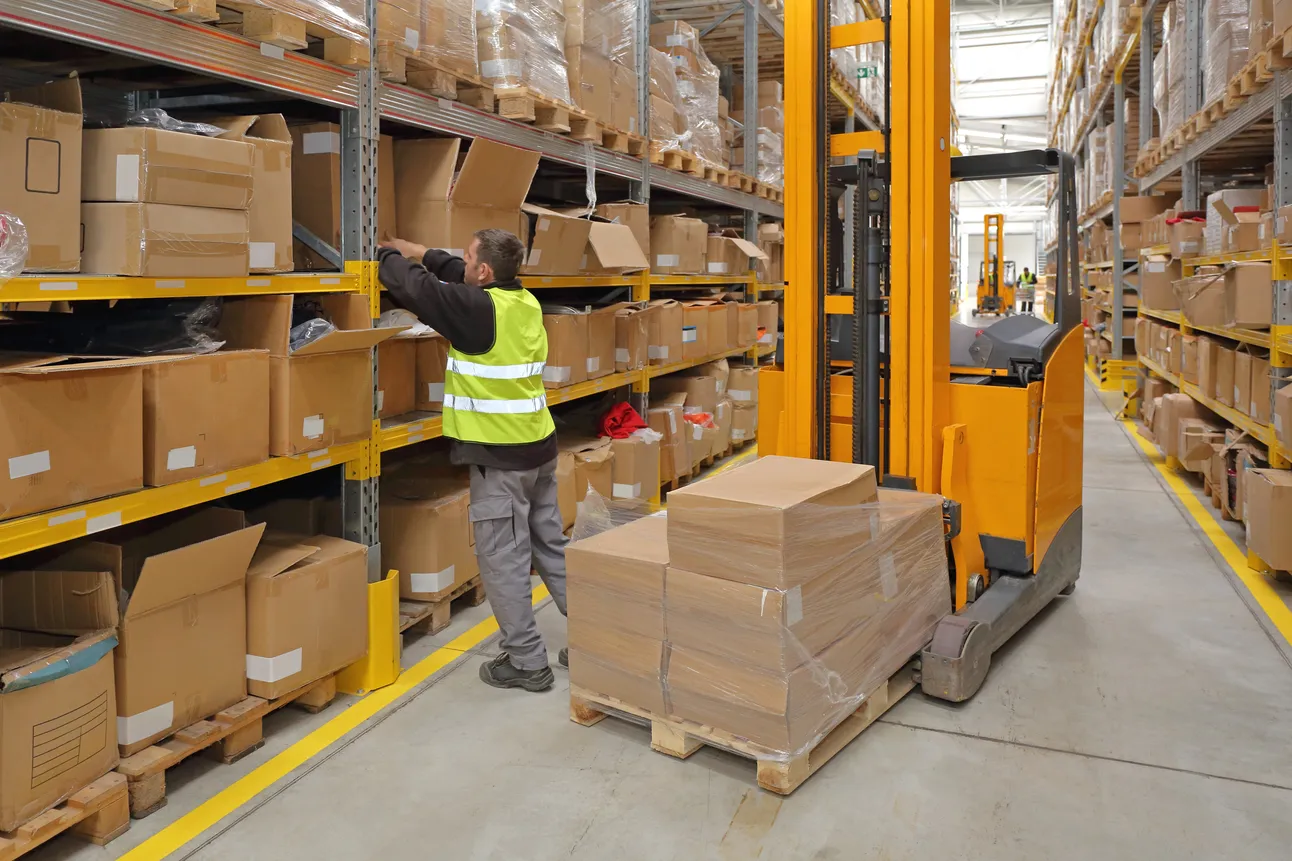
In een conventioneel magazijn bestaat de belangrijkste activiteit in het verzamelen en verzendklaar maken van orders. Het magazijn wordt immers afgerekend op zowel service als kosten. Service levels worden veelal gemeten op basis van klachten van klanten. En die klachten hebben vaak betrekking op het niet ontvangen van het juiste product of van de juiste hoeveelheden. En wat de kostenzijde betreft: in het gemiddelde magazijn maakt de loonmassa zestig tot zeventig procent van de totale kosten uit. Van die zestig tot zeventig procent komt nog eens gemiddeld zestig procent op rekening van het orderverzamelen en verzendklaar maken. Als we de kosten willen drukken en efficiënter willen werken, kijken we best eerst naar de grootste kostenposten. Vandaar de drang om dit proces zo optimaal mogelijk, maar ook zo kwalitatief mogelijk uit te voeren.
Het orderverzamelproces maakt evenwel deel uit van een totaal magazijnconcept en moet dan ook in de totale werking worden geïntegreerd. Een wijze basisfilosofie is om het pickingproces zo optimaal mogelijk op te zetten en alle daaraan gekoppelde activiteiten er op af te stemmen en mogelijk suboptimaal te laten opereren. Herbevoorrading van de picking is zo’n typisch proces. Dat moet tijdig gebeuren om pickefficiëntie te halen, maar is dan niet noodzakelijk optimaal op het gebruik van handling toestellen afgestemd.
Orderpicking op één hoop gooien is uiteraard niet evident. Oplossingen om kleinere goederen in bakken of dozen te verzamelen liggen mijlenver af van oplossingen om dozen op klantenpallets te stapelen. Als die dozen dan ook nog eens grillige vormen hebben of ‘oversized’ zijn, is de complexiteit nog groter.
We kunnen vijf belangrijke punten onderscheiden die een rol spelen wanneer we de complexiteit van het pickingproces willen optimaliseren:
- De karakteristieken van de te picken goederen op het vlak van stapelbaarheid, populariteit (ABC), combineerbaarheid in picking en transport, schadegevoeligheid, samen in orders gevraagd, enz. Dat wordt meestal opgevangen door de volgorde waarin wordt gepickt: van zwaar en groot naar licht en klein om af te sluiten met de ‘uglies’ of moeilijk stapelbare goederen. Dit omwille van de stapelbaarheid, maar ook om schade te vermijden.
- Het profiel van de orders. Het aantal lijnen in een order per artikelprofiel bepaalt mee hoe de picking moet worden opgezet: welke goederen in welke zone, in welke pickronde, in welk soort transportverpakking en dus pickeenheid en dergelijke meer. Evaluatie van discrete orderpicking versus ‘wave picking’ of ‘batch picking’ is ook deel van deze evaluatie.
- De loopafstand. Hoe korter de pickroute, hoe hoger de productiviteit en hoe lager de kosten. ‘Goederen-naar-de-mens’-oplossingen zorgen voor quasi onbestaande loopafstanden, maar vragen hogere investeringen. Ook de evaluatie om enkel op grondniveau of ook in de hoogte te picken moet hier worden meegenomen en heeft een directe link met het aantal te picken goederen en hun opslagvolume.
- De grijpactie of het compleet nemen van een orderlijn, of in het geval van batch picking te nemen voor meerdere orders en uit te splitsen. De grijpactiviteit is afhankelijk van het type goederen (met name afmetingen en vorm) en het aantal te nemen goederen per picklijn.
- De grootte van de picklocatie. Hoe groter, hoe langer de pickroute; hoe kleiner, hoe meer herbevoorrading. Een juiste balans is hier belangrijk, maar tegelijk wil je niet te veel types aan picklocaties definiëren om de complexiteit van de WMS-aansturing onder controle te houden.
De combinatie van die elementen op artikelniveau zal samen met het plaatsen van die goederen volgens ABC resulteren in het optimaal opzetten en inrichten van de pickingzone in een conventionele oplossing. Profielen van goederen en orders kunnen evenwel veranderen en ook het gamma aan artikelen kan wijzigen. Het inrichten van een conventionele picking is dus een erg belangrijke magazijntaak en bepalend voor de efficiëntie.
Dikwijls gebruiken we een model waarbij we het artikelvolume en de populariteit van de goederen tegenover mekaar zetten (zie figuur). Grotere artikelen komen dan typisch op pallets terecht om van en naar te picken, voor kleinere artikelen zijn er veel mogelijkheden en oplossingen voorhanden, zowel conventioneel als geautomatiseerd. In elk geval moet het picksysteem op het opslagsysteem zijn afgestemd en omgekeerd.
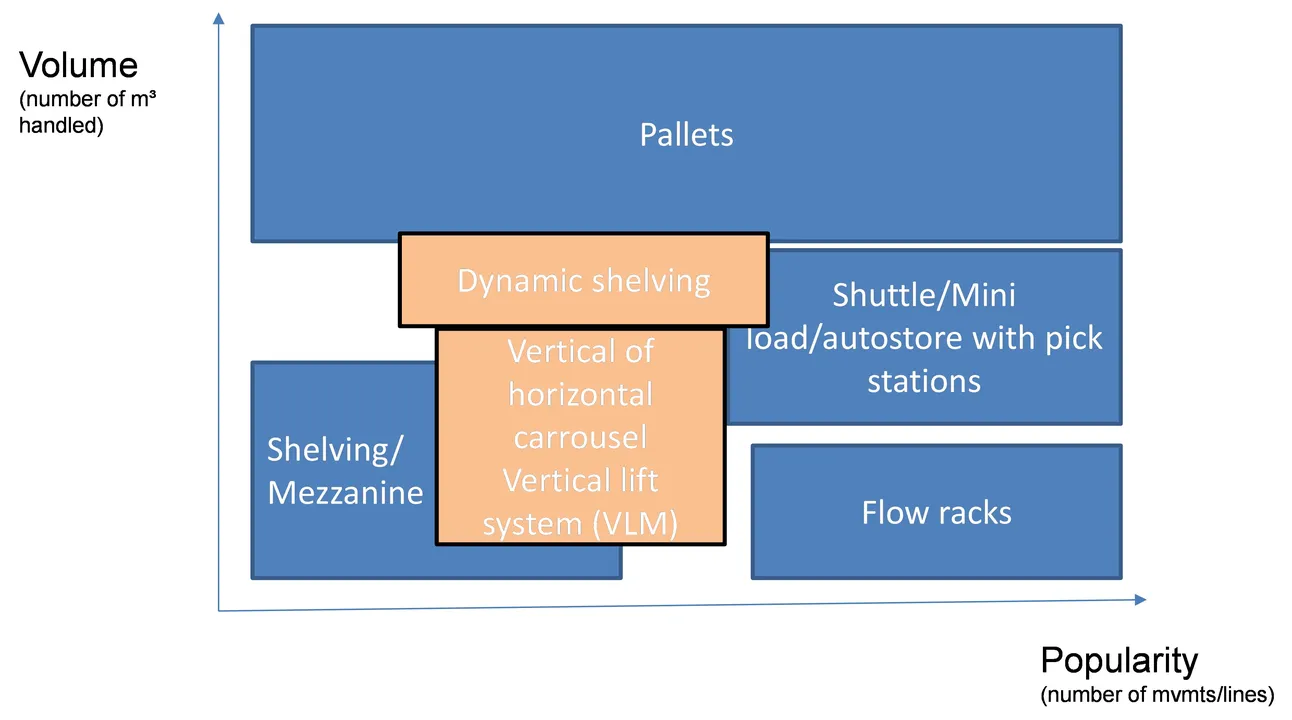
Artikelvolume en populariteit van goederen tegenover mekaar gezet
Keuzes bij colli picken van pallets
Picken van palletlocaties naar klantenpallets wordt typisch opgezet via een pickroute door het conventionele magazijn, waarbij keuzes moeten worden gemaakt zoals:
- in een slang door de gangen bewegen en aan beide zijden van de gang tegelijk picken;
- of elke gang langs het rek op en af lopen;
- op één of meerdere niveaus picken;
- het type toestel om de picking te realiseren afhankelijk van de pickhoogte: handpallettruck, orderpicker, stapelaar (bijvoorbeeld om in het pickproces te kunnen ‘replenishen’ van een niveau boven de picklocatie), hoogtepicker, trekker e.d.;
- informatie naar de picker en confirmatie van de opdracht via picklijst, handheld scanner, voice of smart glasses. Een interessante variant met zeer goede productiviteit zijn handscanners met een display, via bluetooth gekoppeld met een ander toestel. Scanning met wificonnectie wordt gebruikt om de kwaliteit van het werk te verbeteren, om transacties in real time te bevestigen en geoptimaliseerd opdrachten te communiceren en zo de productiviteit te beïnvloeden.
Afhankelijk van het orderprofiel en dus het aantal stops, maar ook rekening houdend met afmetingen en gewichten en de technologie die ter ondersteuning wordt gebruikt, wordt met dergelijke oplossing een productiviteit tussen de 150 en 250 of meer dozen per uur per operator gehaald.
Alternatieven zijn toestellen die de orderpicker volgen of die autonoom van de ene naar de andere locatie voortbewegen en waar de picker dus achter loopt. Die toestellen kunnen uitgerust zijn met een display dat aangeeft hoeveel er van welk artikel moet worden gepickt. In de toekomst zullen we wellicht kunnen beschikken over robots die een pallet voortbewegen en een arm hebben om dozen over te stapelen.
Gekoppeld aan een geautomatiseerd magazijn (kranen, shuttle, e.d.) kennen we toepassingen met pickstations. Een pallet komt uit de voorraad naar dat station en de operator neemt er een aantal dozen van om op een klantenpallet te plaatsen. Daarmee win je enerzijds verplaatsingstijd, maar heb je anderzijds wel tijdverlies doordat de pallets iedere keer op het station moeten worden gepositioneerd. Als alternatief kan een automatisch gevoede pickstraat worden voorzien waarlangs de operator met een toestel loopt om de picking uit te voeren. Resultaat: geen wachttijden en beperkte verplaatsingstijden, maar ook een beperkt aantal pickers per zone.
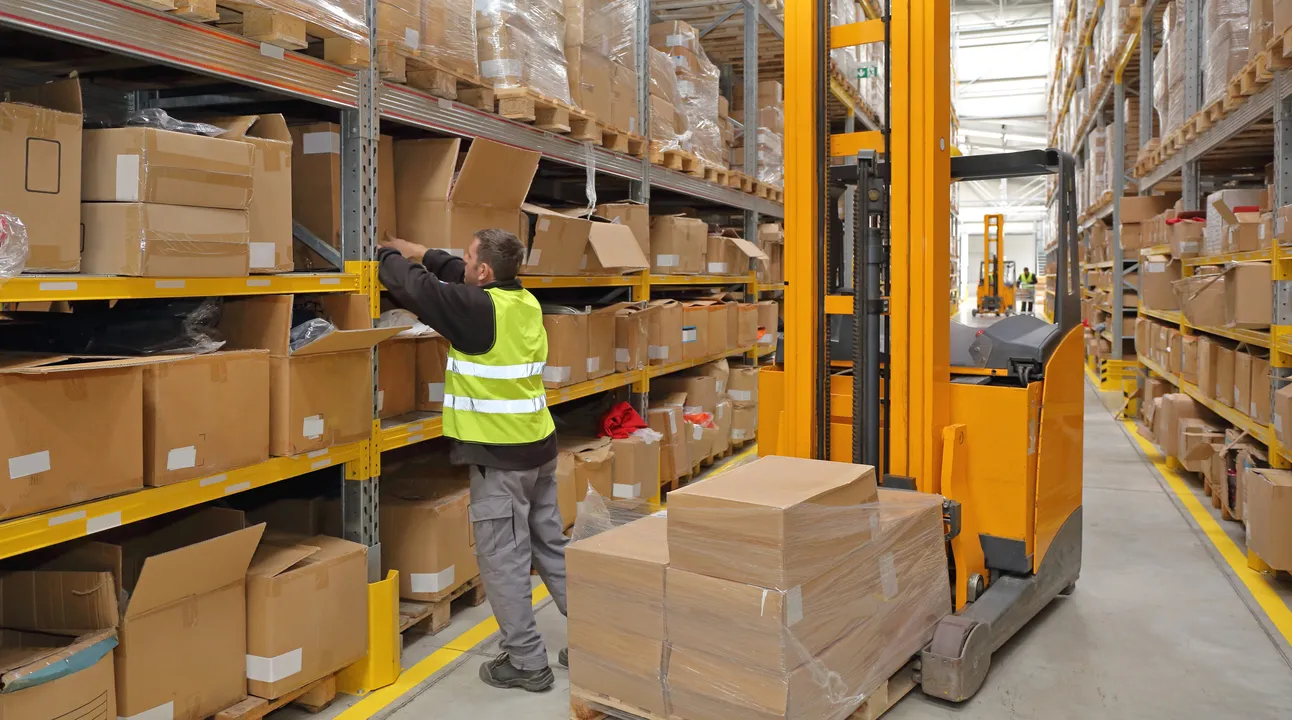
Oplossingen om kleinere goederen in bakken of dozen te verzamelen liggen mijlenver af van oplossingen om dozen op klantenpallets te stapelen. Als die dozen dan ook nog eens grillige vormen hebben of ‘oversized’ zijn, is de complexiteit nog groter.
Veel oplossingen voor picking van kleingoed
De meest performante magazijnen picken kleingoed rechtstreeks in de verzendverpakking en passen dus ‘cubing’ toe. Daarbij worden het volume en de juiste afmetingen van de verzendverpakking bij het begin van de picking berekend. Voor het picken van kleingoed ligt de keuze wat complexer omdat daar zowel conventioneel als geautomatiseerd veel mogelijkheden en variaties bestaan. Discrete orderpicking, zonepicking, batch picking en wave picking worden bepaald door het aantal SKU, het volume aan lijnen versus het aantal bestemmelingen, maar ook de combineerbaarheid van artikelen in orders. Ook de schadegevoeligheid van de producten bij het vastnemen speelt een rol om bijvoorbeeld al dan niet voor wave picking te kiezen.
Bij conventionele oplossingen kan, afhankelijk van het aantal SKU’s, het verbruiksprofiel in de picking per SKU, het aantal lijnen per order, het aantal stuks en het volume per lijn, de maatvoering en het gewicht van de SKU, enz., worden gekozen voor legborden, legborden met tussenvloeren (mezzanine), schuifladen, storeganizer, mobiele rekken of flow racks. De breedte van de looppaden hangt af van het feit of mensen elkaar moeten kruisen of voorbij kunnen en van de toestellen die bij het picken worden ingezet. In conventionele oplossingen halen we dikwijls een productiviteit tussen 60 en 80 lijnen per uur, tot zelfs 130 of meer afhankelijk van de situatie en de ondersteuning. Die ondersteuning kan bestaan uit displays op de rekken, picken met lijsten of picken met toestellen zoals vermeld bij palletpicking.
Semiautomatische oplossingen zoals horizontale carrousels of verticale liften brengen de goederen naar de mens over de breedte van enkele machines. Ideaal is dat gekoppeld aan een trolley of rek om voor meerdere orders tegelijk te kunnen picken. Bij discrete orderpicking kan één operator aan twee of meer machines tot 100 lijnen per uur picken. Bij batch picking met uitsplitsen via bijvoorbeeld ‘drop-to-light’ kan de productiviteit oplopen tot 150 en meer lijnen per uur.
Geautomatiseerde oplossingen brengen de goederen uit het geautomatiseerde magazijn naar een pickstation. Dat geautomatiseerde magazijn kan een miniload, een shuttle, een exotec, een AMR-oplossing met rekjes-naar-de-mens of een soortgelijke oplossing zijn. Daaraan worden pickstations gekoppeld om van een voorraad unit naar een klantenorder in doos of bak te picken. Daarbij zijn ook snelheden van 150 à 200 tot zelfs tegen de 300 lijnen per uur te halen, opnieuw afhankelijk van de artikelen en de situatie.
In de volgende editie gaan we dieper in op de keuzes die we moeten maken bij een picksysteem voor kleinere goederen.
Inloggen/registreren
Om deze content te lezen, moet u zich inloggen.
Log in of registeer nu via onderstaande knop en krijg toegang tot deze inhoud.