Digital manufacturing
How adoption of digital technologies is growing in Maintenance & Asset Management
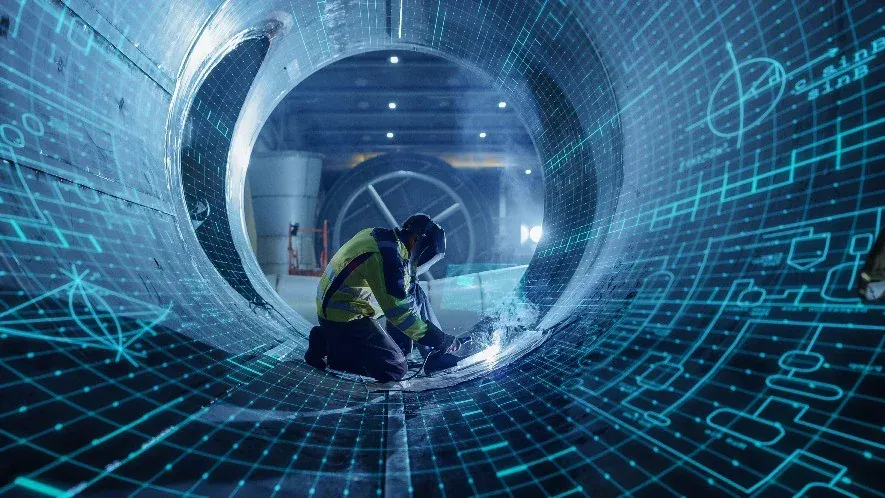
The adoption of digital technologies has gained momentum in the field of maintenance and asset management in recent years. A 2023 survey conducted by PwC and Mainnovation focuses on five key technologies that are gaining a foothold in the sector. The key technologies are mobile maintenance, predictive maintenance, digital twins, augmented reality and 3D Printing. Comparison of implementation levels show that mobile maintenance is a mature technique, predictive maintenance is emerging but digital twins, augmented reality and 3D printing are still new and not yet ready to be optimally applied in the field.
Mobile maintenance stands out
With an overall score of 39%, mobile maintenance shows the highest implementation within the sector. Mobile maintenance has been facilitated by developments in smart devices, Wi-Fi, UI, security, etc. over the past two decades, and the rapid development by EAM/ERP software suppliers of reliable, safe, user-friendly apps.
Implementation is highest in Infrastructure & Fleet (50%) and Service providers (48%) — sectors where many employees are often in the field, far away from their desks, so the need for mobile solutions is higher. However, Food & Pharma also has a high implementation level (50%), showing that the technology is also applicable in a factory setting.
Implementation lags in the Heavy Process industry (22%), where any device has to be safe to use in potentially explosive atmospheres (ATEX). In this context, mobile maintenance is used primarily for work order registrations (70%) and inspections (42%).39%
of implementation within mobile maintenance, scores the highest overall.
Predictive maintenance is upcoming
After mobile maintenance, predictive maintenance has the highest implementation level (17%). This technique is gaining popularity; implementation has almost doubled since 2018.
Service providers are also in the lead in applying predictive maintenance (38%). Service providers, mainly original equipment manufacturers (OEMs), focus on a specific group of asset types that exists in high numbers. This makes it easier to offer specific digital solutions related to these assets. Food & Pharma also shows a relatively high adoption (19%) compared to the other industrial sectors. In this sector many companies use standard equipment. This means they can benefit from the knowledge and services provided by OEMs about predictive maintenance.
AR, 3D printing and digital twin still in start-up phase
For these digital solutions, implementation is low. Digital twin solutions (10% implementation) were only recently introduced in Maintenance & Asset Management. Augmented reality (8%) is highly dependent on reliable software and hardware (AR glasses) but they are still not entirely fit for maintenance activities. OEMs could bring AR to the next level by providing a standard solution including all data references and manuals. Finally, 3D printing (8%) is mostly applied at locations that are hard to reach and when there is a clear economy of scale.
Adoption is seen as a change project, not IT
In companies adopting digital technologies, it is often not considered as an IT development but as a business change project. Adoption is often driven by wider business pressures, such as labour shortage or availability of obsolete machine parts, or by opportunities, such as improving uptime or accessing expertise remotely rather than having experts on site at every location. When it comes to implementation, key success factors include cultural change, data availability, data analytics capabilities and support from the workforce.
Costs can be easy to calculate, but business benefits harder to quantify
The survey also asks whether the potential of digitalisation is being fully exploited, and what is hindering companies from faster adoption? Responses indicate that most companies feel digital technologies are beneficial but it can be difficult to build a strong business case: while the costs may be relatively easy to calculate, the benefits or value can be harder to quantify.
About the survey
PwC and Mainnovation conducted surveys on predictive maintenance (PdM) in 2017 and 2018. The 2023 survey was conducted as a follow-up and to see if the maintenance and asset management sector in Northwest Europe is also adopting other digital solutions. 127 companies in Belgium, Germany, the Netherlands and Norway were surveyed, as well as South Africa for comparison. Respondents came from five industrial sectors (service providers, food & pharma, infrastructure & fleet, heavy process industry, discrete manufacturing).
The survey report includes the results of the survey and a ‘Roadmap to Digitalisation’, identifying six steps for successful implementation of digital solutions in maintenance and asset management. It also includes articles on:
- data management in the Port of Rotterdam, Netherlands
- mobile maintenance at the Shell Energy and Chemicals Park Rhineland, Germany
- digitalising the mining industry, South Africa
- a 3D printing pilot at a PepsiCo plant in Europe.
Northwest Europe versus South Africa
In Europe, Maintenance & Asset Management increasingly has a voice in the boardroom, where digital adoption is approached from an added-value perspective instead of considering it ‘just a technical necessity’. South Africa is an emerging country, from a digital perspective, but is following developments in Europe. There is a strong focus on cost reduction due to the weaker economic situation and challenges such as the energy crises, brain drain and limited budget for innovation.
Digitalisation is a journey every company needs to make for themselves. But we believe that implementing one or more of these five digital solutions can help companies to achieve the full potential of digitalisation in operations while creating value for the business.