Case Study
A Leading Sportswear Brand
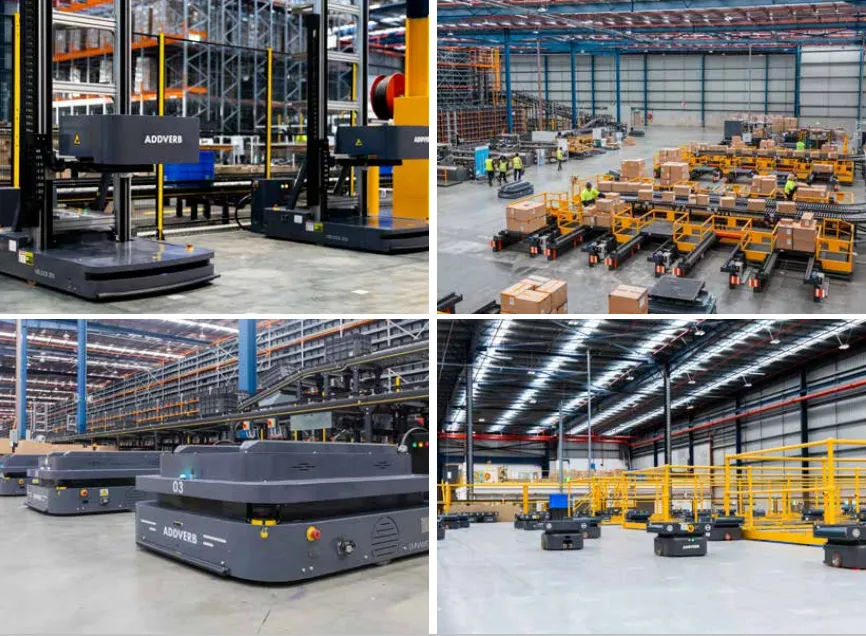
One of the world's leading sports brands, needed an innovative warehouse automation solution to manage its omnichannel fulfilment operation in ANZ and required flexibility to manage seasonal peak demand. The operations required a smooth process flow to manage large number of SKUs, high dispatch volume and handle returns efficiently, and an intelligent warehousing software for accuracy and real-time visibility of inventory.
Objective
Solution Implemented Their facility handled varied SKUs in the form of shœs, apparel and accessories and needed a solution that could be flexible enough to perform operations for both B2B and B2C orders and support omnichannel operations. Their inventory consisted majorly of 60% footwear, 30% apparel, and 10% accessories. Their objective was to develop a robust automation solution that could efficiently manage the operations by reducing the time and cost of fulfilment and drive-up accuracy. Returns handling was a critical process for the customer and they wanted to streamline the returns from different channels and process the return quickly and in a cost-effective manner. They required to optimise the storage space of the warehouse and also wanted to prioritise the order flow as per dispatch requirement thereby ensuring reliable and accurate fulfilment and increase the velocity of material movement inside the warehouse.
Solution Implemented
To meet the objective of Efficiency, Reliability, and Accuracy for omnichannel fulfilment operations, Addverb designed an innovative solution that combined the power of both fixed and flexible automation. The solution comprised of Autonomous Mobile Robots for material movement in the warehouse, Automated Storage and Retrieval Systems like Pallet Shuttles and Carton Shuttles to optimise space utilisation and manage order prioritisation. Multi-Carton Picking Robot system was used to streamline the returns. A combination of Carton Shuttle and Sorting Robot was used for fast order consolidation and Sorting Robot was used for quick dispatch of orders and cater to B2C customers. Additional systems like mixed case palletisers, ergonomically designed Box-It workstations, and strategically planned conveyor lines helped in the seamless integration of fixed and flexible automation. The entire orchestration was effectively performed with our Warehouse Execution System (Concinity) which integrated various robotics and automation systems to ensure smooth flow of material for faster fulfilment. With its AI enabled alogrithms, Concinity optimised order fulfilment by dynamically creating efficient picking and routing strategies. It also provided real time visibility and status of inventory through the entire flow.
Improvement in Key Results (KPIs)
For a solution this large and involving a wide array of robots to automate the operations of the complete warehouse, the KPIs are unmatched and enviable across any omnichannel fashion & sports warehouse.
1,00,000 Pieces Dispatched per day to 2,500 unique distribution nodes.
Pick-by-Light Technology For efficiently palletising operations with up to 60 available open pallet positions.
16,500 Pallet Positions For multi-deep storage and retrieval of pallet loads (Mother-Child ASRS).
86,400 Tote Positions To maximise throughput in storage and retrieval of totes (Carton Shuttle ASRS).
Robotic Depalletiser That can perform depalletisation of up to 420 cartons/hour/robot.
AMRs and Multi-Carton Picking Robot For swift movement of material in the warehouse with minimal human intervention.
Double-layer Sortation System Where 3,600 eaches are sorted per hour and there are 300 bin locations with 150 on each level.
Warehouse Control System To manage the end-to-end operations in a warehouse.