Grotere capaciteit in een kleinere ruimte
Dematic optimaliseert magazijn voor kleine onderdelen van Siemens in samenwerking met STILL
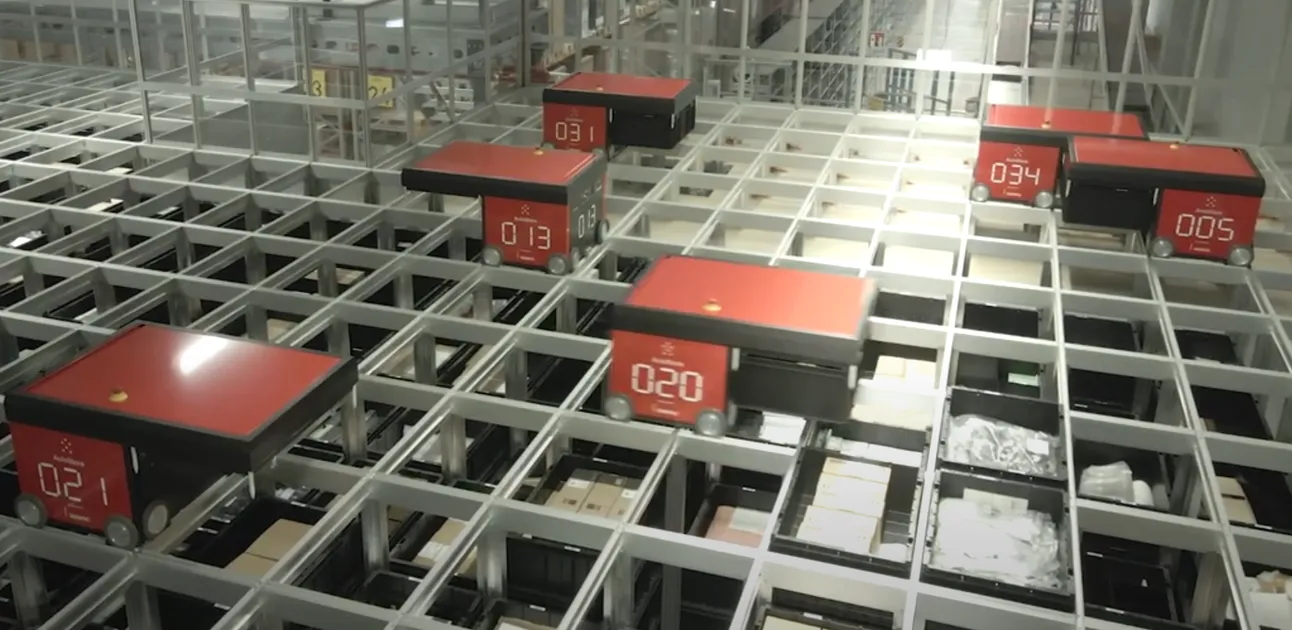
Ontwikkeling, engineering, productie, testen en pre-commissioning - de Siemens-fabriek voor combinatietechniek in Chemnitz (Siemens WKC) is toonaangevend in de schakelkastbouw voor gereedschapsmachines en productiemachines in Europa. Hier produceert het technologieconcern ultramoderne elektrische apparatuur en assemblages en apparaten voor de wereldwijde behoeften van machine- en installatiebouwers. Hieronder vallen ook projecten in de logistieke en automobielsector. Het vorige handmatige opslagsysteem voor kleine onderdelen had echter zijn capaciteitsgrenzen bereikt en daarom was Siemens WKC op zoek naar een efficiënter opslagsysteem.
Het bedrijf besloot over te stappen op een goederen-naarpersoon picking systeem van AutoStore®. Het nieuwe logistieke concept werd ontworpen door de jarenlange partner van het bedrijf, Still Intralogistik-Beratung. Dit omvatte de automatisering van het magazijn voor kleine onderdelen met het AutoStore® systeem. Siemens gaf ook opdracht aan de intralogistieke specialist Dematic voor de installatie van het compacte stukgoedpicksysteem en de directe verbinding met de transportbandtechnologie. In het WKC van Siemens worden jaarlijks ongeveer 46.000 schakelapparatuur en op maat gemaakte elektronische componenten voor de wereldmarkt geproduceerd. In de loop der jaren zijn het volume en de doorvoer in het magazijn aan de Leipziger Straße aanzienlijk toegenomen als gevolg van de toegenomen ordersituatie. Dit maakte het noodzakelijk om het hele magazijnbeheersysteem te reorganiseren: „Tot die tijd werkten we nog met een handmatig magazijn met modulaire stellingen,“ vertelt Carsten Sambo, hoofd Inkomende Logistiek, Siemens WKC. Het voormalige handmatige magazijn voldeed echter niet meer aan de huidige eisen.
Automatisering van het productiemagazijn met AutoStore®
Siemens ging daarom op zoek naar een nieuwe oplossing: „Ons doel was om planning en productie zo efficiënt mogelijk te organiseren. Tegelijkertijd moesten de doorlooptijden worden verkort en natuurlijk de kosten worden verlaagd“, legt Carsten Sambo uit. Een andere vereiste was dat de nieuwe opslagsystemen, inclusief de transportbandtechnologie, geïnstalleerd zouden worden op dezelfde vloeroppervlakte in het bestaande gebouw en tijdens de lopende werkzaamheden. Als jarenlange partner van Siemens nam Still Intralogistics Consulting in eerste instantie de planning van het logistieke concept voor zijn rekening. Dit omvatte de automatisering van het magazijn voor kleine onderdelen met een AutoStore® systeem om de levering van kleine onderdelen voor de productie te verbeteren. „We hebben al zeer goede ervaringen opgedaan met dit opslagsysteem in de Siemens fabriek in Bad Neustadt (EWN),“ zegt Carsten Sambo. Vergeleken met het vorige handmatige systeem kan er tot vier keer meer voorraad worden opgeslagen. Na slechts een korte introductiefase bereikte de Siemens WKC ook een orderverzamelprestatie van 75 ophaalposities (AP) per uur en werknemer. Dit was voorheen slechts 30 AP. Met behulp van het systeem moet deze prestatie met nog eens minstens 15 procent worden verhoogd.
Als wereldwijde distributiepartner van AutoStore® en met de bijbehorende uitgebreide ervaring en expertise, werd Dematic ingeschakeld. Het zusterbedrijf van de KION Group kreeg van Siemens de opdracht om AutoStore® en een directe verbinding met de transportbandtechnologie van Dematic te implementeren als systeemintegrator voor de grootst mogelijke automatisering van de materiaalstroom en dus een geoptimaliseerde productiebevoorrading. Een groot voordeel van de oplossing voor het verzamelen van stukgoederen is dat deze zeer weinig ruimte in beslag neemt. Siemens kan de gewonnen ruimte benutten voor de opslag van grotere materiaalstukken, zoals behuizingen voor schakelapparatuur. STILL leverde een stellingsysteem voor het magazijn met ongeveer 12.000 opslaglocaties en 2.100 vierkante meter platformruimte als onderdeel van het totale logistieke concept.
Capaciteiten aanzienlijk verhoogd
Het door Dematic geïmplementeerde transportsysteem heeft twee niveaus. In de zone voor inkomende goederen worden de pakketten eerst gescand en via een lift naar het bovenste niveau getransporteerd. Daar worden de goederen automatisch en willekeurig verdeeld over de acht transferstations. Lege AutoStore® containers worden vervolgens via het onderste niveau naar de werkstations getransporteerd. Na het vullen worden de containers naar het automatische magazijn voor kleine onderdelen getransporteerd. Om ervoor te zorgen dat ze het maximaal toegestane gewicht van 30 kilo niet overschrijden, wordt er vooraf een gewichtscontrole uitgevoerd. De AutoStore® robots storten en halen de bakken automatisch in één stap op via transfercellen. Het compacte AutoStore® magazijn voor kleine onderdelen neemt zelf slechts 760 vierkante meter in beslag. Het bevat in totaal meer dan 45.000 bakken, die verdeeld zijn in verschillende compartimenten en dus verschillende producten kunnen bevatten.
Het orderverzamelproces begint met het afroepen van de productie, d.w.z. het aanleveren van de goederen aan de interne logistieke afdeling, die de materialen klaarmaakt voor productie en ze beschikbaar stelt voor de productie. De orders worden verzameld door 34 mobiele robots die bovenop het AutoStore® systeem rijden. Ze picken de dozen van het rooster en brengen ze één voor één naar de haven zodat de werknemers hun pickactiviteiten zonder onderbreking kunnen uitvoeren.
Voorheen moesten ze lange afstanden afleggen om de afzonderlijke items te verzamelen. Met hetzelfde aantal werknemers kan Siemens nu meer orders in minder tijd verwerken dankzij AutoStore®. „Tegelijkertijd zorgt het systeem voor aanzienlijk minder fouten bij het picken“, zegt Carsten Sambo.
TECHNISCHE GEGEVENS
- 8 overslagstations
- Vloeroppervlak van het AutoStore® systeem: 760 m2
- 45.000 containers
- 34 robots
- 5 orderverzamelpoorten
- 7.000 verschillende orderverzamelposities per dag
Uitgerust voor de toekomst
Het AutoStore® systeem kan tot vier keer meer voorraad opslaan op hetzelfde oppervlak dan conventionele opslagsystemen. „Het voordeel van het systeem is dat het de opslagdichtheid maximaliseert. Het speciale kenmerk van dit kubusopslagsysteem is een zelfdragend aluminium raster, waarvan het modulaire ontwerp het mogelijk maakt om containers dicht naast en op elkaar te stapelen. Het is ook decentraal georganiseerd. Dit betekent dat als er een robot uitvalt, het systeem blijft draaien zonder dat er een storing optreedt,“ legt Carsten Sambo uit en hij voegt eraan toe: „In de AutoStore® hebben we dagelijks afroepen van meer dan 7.000 verschillende pickposities. Om ‚s ochtends snel over de benodigde goederen te kunnen beschikken, hebben we een prognosefunctie geprogrammeerd voor het ophalen of verplaatsen van de nachtploeg.“ De behoeften voor de volgende dag worden ‚s nachts gecontroleerd. De vastgestelde materialen worden overgebracht van de onderste niveaus van het AutoStore® systeem naar het bovenste gedeelte van het rooster. „Dit zorgt ervoor dat de benodigde containers snel toegankelijk zijn aan het begin van de vroege dienst.“
Het concept voor het nieuwe intralogistieke proces werd ontwikkeld in nauwe samenwerking met alle betrokkenen. Uiteindelijk vat Carsten Sambo het als volgt samen: “Met het nieuwe magazijn zijn we ideaal uitgerust voor de toekomst, omdat er al tijdens de planningsfase rekening werd gehouden met de schaalbaarheid. Het vergroten van de opslag- en orderverzamelcapaciteit en het efficiënter maken van de handling en het hele magazijnbeheer werden optimaal ingevuld.” Het feit dat de productiebevoorrading zonder onderbreking kon worden gehandhaafd, was een persoonlijk hoogtepunt voor de projectmanager van Siemens.
VOORDELEN VOOR DE KLANT
- Vier keer meer voorraad op hetzelfde vloeroppervlak
- Geen onproductieve routes meer
- Lager foutenpercentage
- Gedecentraliseerde organisatie van de robots minimaliseert stilstandtijden
- Het modulaire ontwerp maakt eenvoudige uitbreiding mogelijk
- Prognosefunctie en nachtdienstverplaatsing zorgen voor snellere toegang tot de benodigde goederen
OVER DE KLANT
De Siemens-fabriek voor combinatietechniek in Chemnitz (WKC) heeft een lange traditie op het gebied van schakelkastbouw voor werktuigmachines en een groot aantal sectoren in de algemene machine- en installatietechniek. Hieronder vallen ook projecten in de logistieke en automobielsector. Het dienstenpakket omvat het hele spectrum van applicatie-engineering, materiaallogistiek en assemblage van elektrische apparatuur tot testen en pre-commissioning. Leveringen vinden plaats aan klanten over de hele wereld. De specifieke omvang van de diensten wordt individueel bepaald door de respectieve klant op basis van de bestelling. WKC is ook een erkend competentiecentrum voor de klimaatregeling van schakelapparatuur, beschikt over een eigen warmtelaboratorium met bijbehorende mogelijkheden voor belastingtests en is een gecertificeerde UL-panelenwinkel.