België komt aan de bak met fabriek in Beringen
Schoeller Allibert levert grote containers vanuit nieuwe site
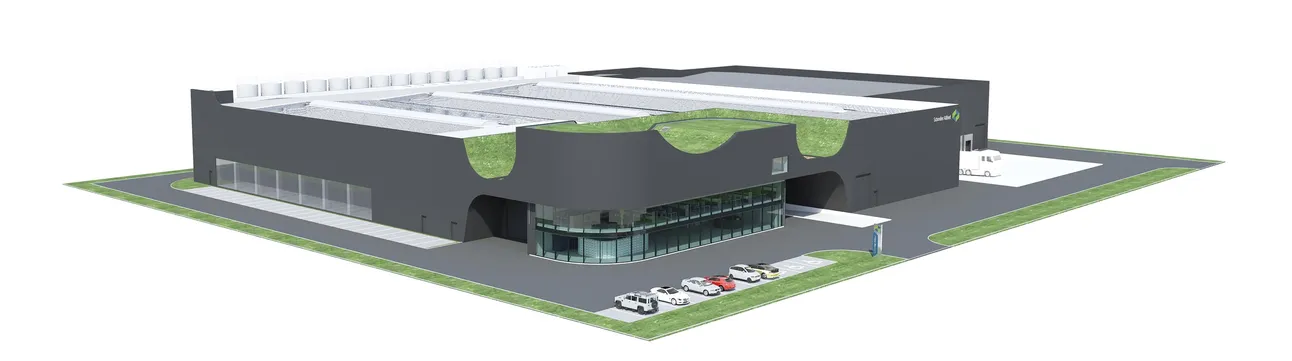
Kostenefficiëntie en duurzaamheid, dat is waarvoor Schoeller Allibert, de producent van plastic verpakkingen die 100% recycleerbaar zijn, voor staat. Het levert geen goedkope, maar wel kwalitatieve en innovatieve containers op. Aangezien het bedrijf een nultolerantie voor afval nastreeft en logistieke kosten wil reduceren, probeert het ook telkens binnen een straal van 300 kilometer een fabriek te hebben. Zo moeten de producten nooit van al te verre bestemmingen komen, wat het aantal vervuilende kilometers terugdringt. Die filosofie heeft België een fabriek opgeleverd, die sinds het najaar van 2017 grote containers produceert. Voordien moesten de grote producten uit Frankrijk en Duitsland komen, nu kunnen producten zoals de Maximus 1212 en de Magnum Optimum 595 vanuit Beringen worden geleverd.
Een bak Jupiler; u heeft er ongetwijfeld al eentje in uw handen gehad of er op zijn minst eentje in de supermarkt zien staan. Het principe van de bak is simpel: u koopt een bak met volle bierflesjes en wanneer de flesjes leeg zijn, brengt u ze met de bak terug en krijgt u statiegeld. De glazen flesjes worden gerecycleerd en ook de bierbakken worden meerdere keren hergebruikt. Een mooi voorbeeld van hoe er te midden van de wegwerpmaatschappij plaats is voor recyclage en hergebruik. Het is het principe waar de producent van die bierbakken, Schoeller Allibert, dagelijks mee bezig is. De Europese leider voor ‘returnable transit packaging’ vervaardigt plastic containers, kratten, emmers, pallets en dolly’s uit hoogkwalitatieve polymeren die 100% recycleerbaar zijn. De herbruikbare producten hebben een levensduur van gemiddeld tien jaar en wanneer ze niet meer kunnen worden hergebruikt, dan worden ze gerecycleerd. Het bedrijf probeert zo een alternatief te bieden voor wegwerpverpakkingen als karton, hout en plastic voor eenmalig gebruik. De kunstof variant is steviger dan kartonnen en houten exemplaren, lichter dan metalen verpakkingen en bovendien opvouwbaar.
Schoeller Allibert is actief in de landbouw-, voedings-, dranken-, automobiel-, industriële sector, retail en pooling. De kans dat uw bier, groenten en fruit en zelfs auto-onderdelen ooit zijn vervoerd of bewaard in een product van Schoeller Allibert is dus groot. Het bedrijf met hoofdkantoor in het Nederlandse Hoofddorp telt meer dan 2.000 medewerkers, verspreid over 20 landen en het draait een jaarlijkse omzet van meer dan 500 miljoen euro. Het stokpaardje van het bedrijf is de 360 graden-benadering van herbruikbare kunststofverpakkingen, waarbij het duurzaamheid en kostenefficiëntie nastreeft. De logistieke kosten probeert het in te perken door bijvoorbeeld gebruik te maken van opvouwbare containers. Daarnaast creëert het toegevoegde waarde door voor elk bedrijf naar een unieke merkidentiteit te streven. Dat kan bijvoorbeeld via creatieve verpakkingen, zoals de kratten voor Warsteiner, waar het uiterlijk van een traditionele houten bierkrat met een moderne distributiecontainer wordt gecombineerd. Zo is er een gouden pigment in het plastic verwerkt en ook de merknaam is erin verwerkt en dus niet via een etiket op de krat geplakt. Dat maakt de merknaam beter bestand tegen beschadiging. Bovendien beschikt Schoeller Allibert over een recyclagedienst die gebruikte containers en kratten inzamelt, reinigt, wast en droogt om te kunnen hergebruiken. Bij alle stappen zijn de eisen aan kwaliteit en veiligheid hoog.
Schoeller Allibert telt twaalf vestigingen in Europa, waarvan de laatste vestiging nog maar recent op Belgische bodem is gebouwd. Sinds 14 augustus 2017 rollen de eerste producten van de band in de fabriek in Beringen. De productiehal is 6.500 vierkante meter groot, er is een buitenopslagruimte van 4.500 vierkante meter en het verkoop- en innovatiecentrum meet 1.200 meter. De productie in de Limburgse fabriek maakt gebruik van ‘injection mould technologie’, iets wat terugkomt in de architectuur van de fabriek (zie afbeelding). De glooiende vorm is gebaseerd op de vloeibare toestand die de kunststof tijdens het productieproces aanneemt en waarmee ze doorheen de machines vloeit. In Beringen ligt de nadruk op grote producten, zoals de Maximus 1212 voor de fruitindustrie (zie verder). Dat is ook de reden waarom de nieuwe fabriek noodzakelijk was: kleine producten konden vanuit de fabriek in het Nederlandse Harenberg worden geleverd, maar grote containers moesten vanuit Frankrijk of Duitsland komen, wat niet zo ecologisch is.
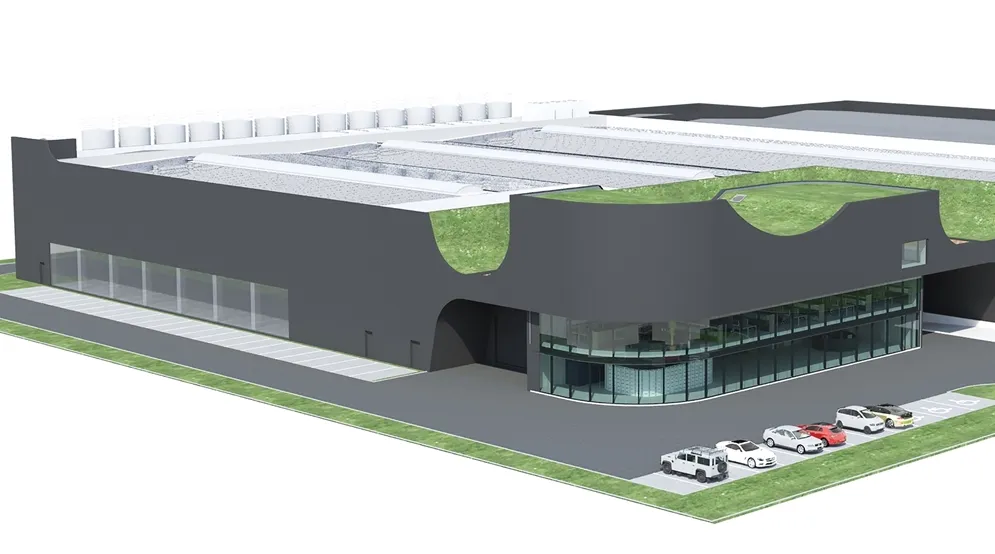
Innovatieproces in Beringen
De fabriek in Beringen beschikt over één machine waarin afwisselend een andere gietvorm kan worden vastgemaakt die telkens een andere container met een ander kleur produceert. Op termijn kunnen er vijftien machines in de productiehal worden geïnstalleerd. Het duurt op dit ogenblik nog zeven uur om van gietvorm te veranderen, maar dat zou binnenkort naar vier uur moeten kunnen worden herleid. Als de gietvorm eenmaal in de machine zit, kunnen er 700 boxen per dag worden geproduceerd en dat 24 uur per dag en zeven dagen op zeven. Op dit moment wordt de Maximus 1212, een grote kist om fruit en groenten te vervoeren, al in Beringen geproduceerd. Het opvallendste kenmerk van de Maximus 1212 zijn de vier verlagingen in de bodem van de box, wat bewegingen van het fruit en de groenten tijdens het transport vermindert. Dat resulteert niet alleen in heel wat minder beschadigde appels en peren dan bij transport in containers met vlakke bodems, het vergroot meteen ook het interne volume. Vrachtwagens kunnen zo optimaal mogelijk worden gevuld en de containers zijn lichter, zodat transportkosten en de impact op het milieu afnemen. Overal zitten er schuine openingen die de ventilatie bevorderen en op die manier schimmel weren. De openingen zorgen er ook voor dat de box snel droogt wanneer hij wordt schoongemaakt, wat tijd en energie uitspaart.
Een ander product dat in Beringen wordt geproduceerd, is de Magnum Optimum 595 voor de supply chain van de automobielsector. Het betreft een grote container die opvouwbaar is, waardoor er 208 lege containers in een standaard vrachtwagen kunnen, tegenover 78 gevulde containers. Aan de container kan de Optiframe spacer van Schoeller Allibert worden toegevoegd, zodat de hoogte met 105 millimeter toeneemt. Aangezien de container minder weegt (36 kilogram) en uitgekiende afmetingen heeft (1200 x 1000 x 595 millimeter), wordt er optimaal gebruik gemaakt van de ruimte in de vrachtwagen, zodat de logistieke kosten en de voetafdruk naar beneden kunnen. De manier waarop de container moet worden opgevouwen, is niet onderhevig aan een bepaalde volgorde van inklappen. De wanden klikken in elkaar zodra ze in elkaars buurt komen, wat ergonomisch interessant is voor de arbeiders en uiteindelijk arbeidskosten bespaart. Voor extra bescherming kan er voor een deksel tegen stof worden gekozen. Op vraag kan RFID worden toegepast om te weten waar de producten zich bevinden, want er zijn zones waarop labels en tags kunnen worden aangebracht. Tot slot is de Magnum Optimum 595 samengesteld uit losse onderdelen, zodat alle onderdelen gemakkelijk kunnen worden vervangen, wat de levensduur en onderhoudskosten ten goede komt.
Schoeller Allibert zegt zelf niet de goedkoopste, maar wel de meest kwalitatieve containers te produceren. Om het verschil te kunnen maken zet de producent constant in op innovatie. In Beringen zijn er 43 medewerkers actief in het research en development departement.
Patrick Breukers, global innovation director, legt uit hoe belangrijk het is om innovatief en tegelijk realistisch te zijn: “Voordat we een gietvorm van 1,5 miljoen euro aankopen, moeten we honderd procent zeker zijn dat het product werkt. We kunnen geen testproduct met die gietvorm maken, vandaar dat we op voorhand heel veel analyses uitvoeren om het ontwerp te verifiëren. De conceptdesigners zijn de creatieve geesten die de volledige vrijheid krijgen om innovatieve ideeën uit te denken. Zij maken een ontwerp dat terechtkomt bij de productdesigners, die het onderwerpen aan risicoanalyses zoals ‘failure mode’ and ‘effect analysis’, ‘proof of concepts’ en de sterkte van het systeem berekenen via ‘finite element analysis’. Zij hebben een zo laag mogelijk risico en zo hoog mogelijke efficiëntie voor ogen, terwijl de conceptdesigners de bewakers zijn van innovatie en esthetische meerwaarde. Bij elk nieuw product wordt gezocht naar een goede balans tussen structuren en procedures aan de ene kant en creativiteit aan de andere kant.”
De vernieuwingen staan niet enkel in het teken van producten verbeteren die er nu al zijn, maar er wordt ook gekeken naar de uitdagingen van de markten en strategische groeimogelijkheden. Een van de uitdagingen is dat de legplanken in elke supermarkt andere dimensies hebben. Een andere uitdaging bestaat in goederen die met verpakking en al rechtstreeks de retail binnenkomen, zonder dat ze in een rek worden gelegd.
Patrick Breukers ziet nog een aantal trends waarop kan worden ingespeeld: “De booming e-commerce heeft als gevolg dat er heel wat verpakkingen nodig zijn om aan huis te leveren. Nu zijn dat vaak houten kisten of kartonnen dozen, maar met onze plastic alternatieven willen wij ook onze rol kunnen spelen in thuisleveringen. Verder worden drones steeds vaker ingezet om pakketjes te leveren, bijvoorbeeld met medicijnen. Het is een tendens waarop we willen meedrijven via een container die door drones naar de juiste bestemming kan worden gebracht. Tot slot zien we dat het belang van ‘post-consument’ toeneemt, wat betekent dat producten na gebruik door de consument moeten kunnen worden hergebruikt of verwerkt. De kwaliteit van het materiaal en de levenscyclus staan voorop.”
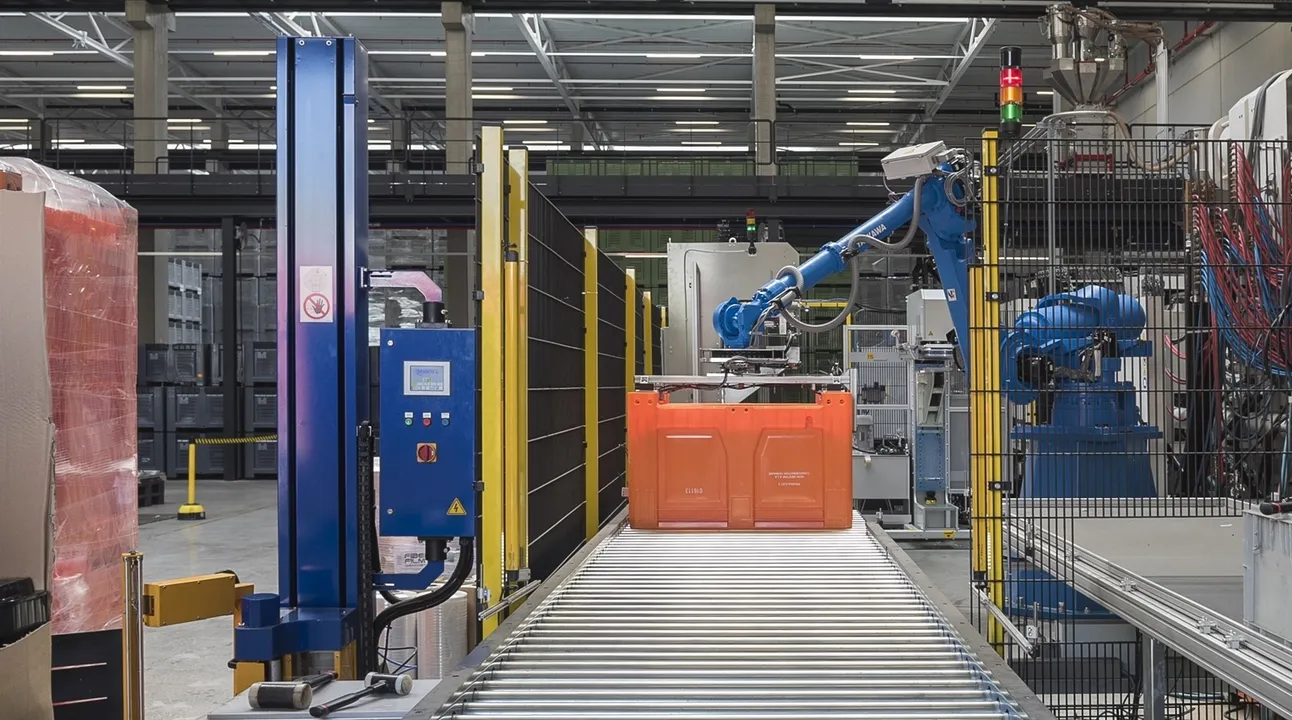
Toekomstmogelijkheden
Volgens Ludo Gielen, chief marketing en innovation officer, wordt er wereldwijd 600 miljard euro besteed aan de productie van verpakkingen, waarvan slechts 5 miljard euro aan herbruikbare verpakkingen. Hij is er dan ook van overtuigd dat Schoeller Allibert nog veel groeimarge heeft. “De returnable transit packaging groeit elk jaar met ongeveer vijf procent, wat niet slecht is als je weet dat het een huzarenstukje is om bedrijven ervan te overtuigen op lange termijn te denken en duurzame materialen te kiezen”, meent hij. “Maar ik geloof er wel in dat het op termijn zal lukken, want de congestie op de wegen en de logistieke kosten oefenen een steeds grotere druk uit. Onze containers kunnen bijvoorbeeld in Italië met tomaten worden gevuld en na levering in een Belgische supermarkt, opnieuw met spruitjes worden gevuld. Dat noem ik een duurzame oplossing.”
Een oplossing waar Ludo Gielen volledig achterstaat en die hem ertoe aanspoorde zelf als Limburgse ondernemer acht miljoen euro op een totaalbedrag van vijftien miljoen euro in de vestiging in Beringen te investeren.
Schoeller Allibert investeert fors in innovatie, waardoor het per maand gemiddeld één nieuw product lanceert. In de volgende drie jaar zitten er 35 nieuwe producten aan te komen en nog eens 26 projecten zijn in ontwikkeling. Bij alle producten is het uitgangspunt dat de ontwerpen innovatief moeten zijn en zo meerwaarde creëren. Er wordt ook telkens voor ogen gehouden dat de logistieke kosten en het afval moeten verminderen.
Ludo Gielen: “We willen een bedrijf zijn dat geen afval produceert. Daarom proberen we in de eerste plaats afval te voorkomen. Als dat niet mogelijk is, proberen we de hoeveelheid afval zo laag mogelijk te houden en waar mogelijk producten te hergebruiken. De laatste optie is recycleren, maar nog liever dan recycleren, kiezen we ervoor het materiaal te herstellen. Ik ben ervan overtuigd dat onze filosofie in de komende jaren bij meer bedrijven zal aanslaan.”
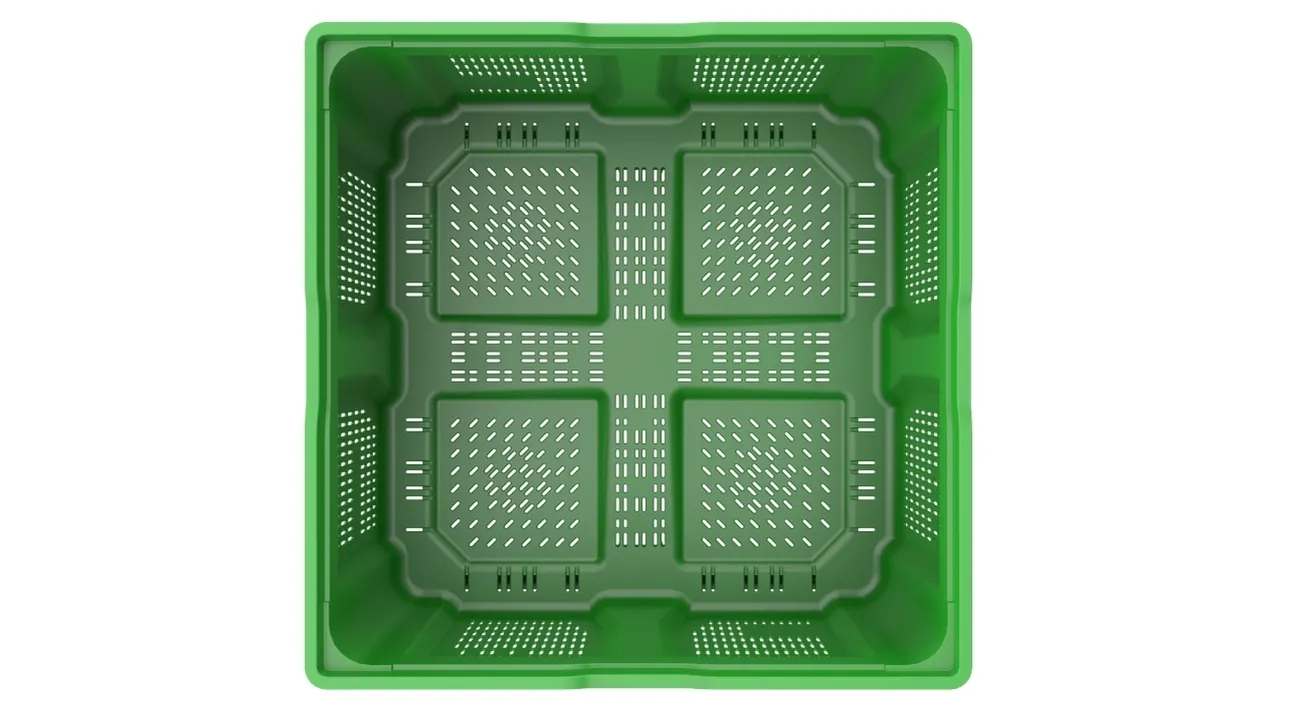