Automatische material handling systemen met groen randje
Duurzaamheid vanuit het perspectief van TGW
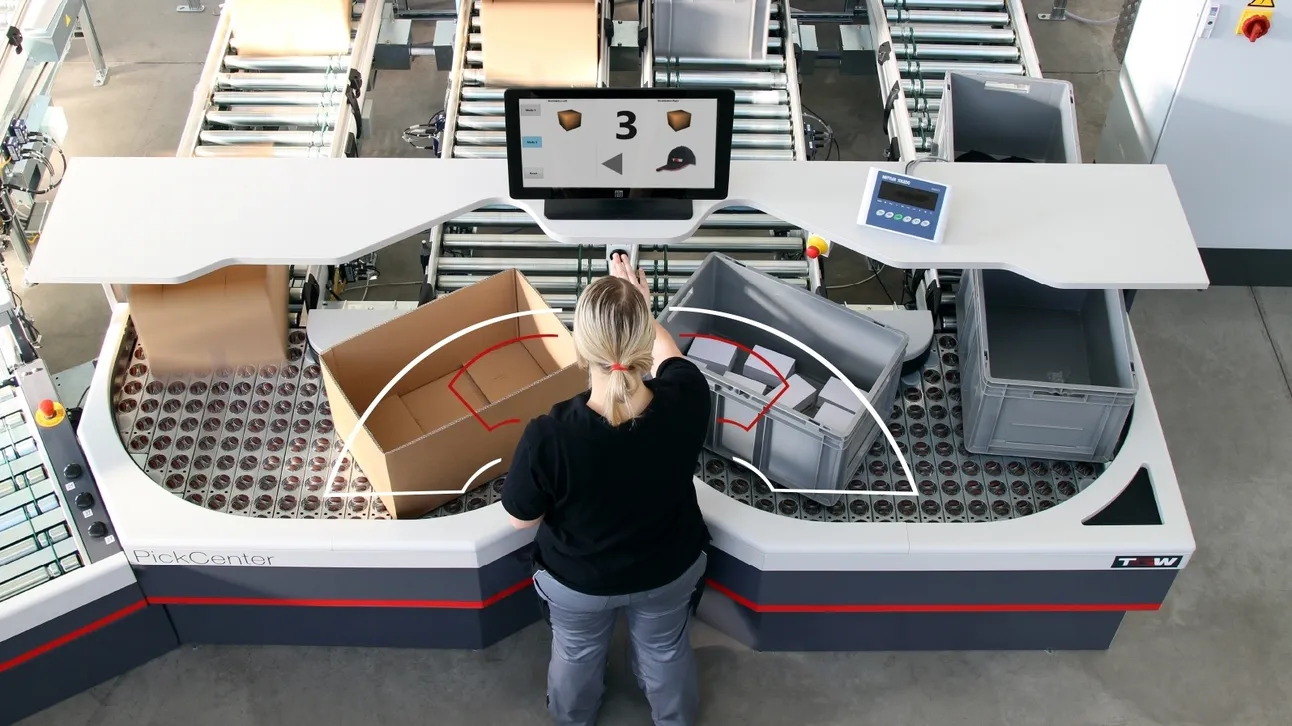
Op zich zijn automatische magazijnen al duurzamer dan conventionele magazijnen. Van nature laten ze immers toe compact te werken en ze hebben ook geen licht of verwarming nodig om hun werk naar behoren te doen. Bovendien zijn automatische material handling systemen vandaag vaak uitgerust met tal van minder zichtbare ecologische snufjes, zoals energieterugwinningssystemen. In welke mate de gunstige ecologische voetafdruk van automatische material handling systemen zowel de CAPEX (capital expenditures) van het magazijn an sich als de OPEX (operating expenses) tijdens de levensduur van het systeem ten goede komt, vernemen we van Hans De Sutter, managing director bij TGW Systems.
De lage beschikbaarheid van gronden dwingt steeds meer bedrijven ertoe hun activiteiten op zo weinig mogelijk oppervlakte uit te voeren. Automatische magazijnsystemen kunnen in die context zinvol zijn, aangezien zij toelaten meer te doen op minder plaats. Bovendien kunnen we de beschikbare verticale meters met een automatisch systeem vaak veel beter benutten.
“Wij ervaren effectief dat organisaties het steeds belangrijker vinden om hun beschikbare kubieke meters optimaal te benutten. Niet alleen zijn er in ons land niet veel grote lappen grond op strategische locaties meer beschikbaar, compact bouwen heeft ook een directe positieve impact op de nodige investeringen”, begint Hans De Sutter. “Bovendien liggen de kosten om de operaties te runnen een pak lager in meer compacte magazijnen, denken we maar aan verwarming, verlichting en koeling. We beschouwen het dan ook als onze taak om op dat vlak mee te denken met onze klanten en oplossingen steeds compacter en duurzamer te maken, zonder aan de efficiëntie te raken. Als Oostenrijks bedrijf heeft TGW trouwens altijd al aandacht gehad voor zo duurzaam mogelijke oplossingen. In dat land gaat er van nature al meer aandacht naar het milieu dan in veel andere landen. Die duurzame filosofie zit dan ook in onze organisatie verweven. Momenteel hebben we een 300-tal mensen binnen Research & Development die duurzaamheid steeds als belangrijke parameter meenemen bij hun ontwikkelingen.”
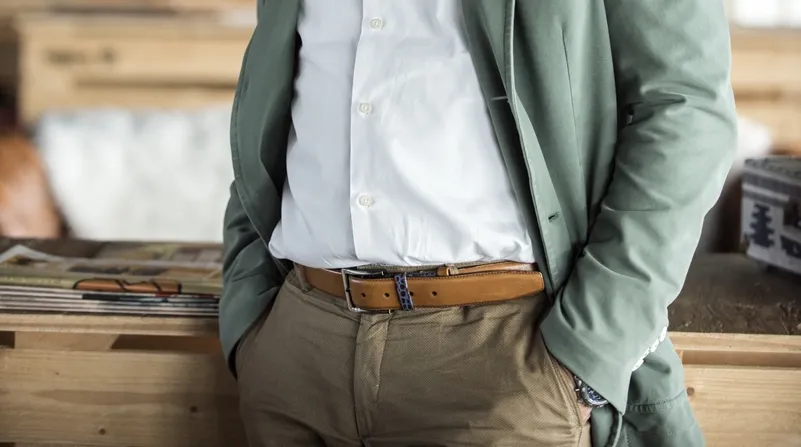
Hogere kranen, snellere liften
Bij TGW volgen de technologische ontwikkelingen die bijdragen tot de duurzaamheid van automatische systemen zich dan ook in sneltempo op. “Recent hebben we bijvoorbeeld een Mustang-miniloadkraan op de markt gebracht die maar liefst 25 meter hoog kan reiken. Dat is drie meter hoger dan de vorige versie. Op die manier kan de beschikbare hoogte nog beter worden benut”, illustreert Hans De Sutter.
“Ook onze shuttlesystemen gaan steeds hoger. Een shuttle-installatie van 25 meter hoog is al lang geen uitzondering meer. Bij TVH in Waregem zijn we bijvoorbeeld zo’n hoog shuttlesysteem aan het bouwen. Een mogelijk nadeel is wel dat, hoe hoger zo’n systeem is, hoe minder ‘throughput’ je logischerwijs uit een gang haalt. Bij een shuttlesysteem worden de bakken namelijk op de verschillende niveaus door hetzelfde paar liften opgehaald. Hoe meer niveaus, hoe lager de snelheid dus. Dat capaciteitsverlies proberen we te compenseren door steeds snellere liften te ontwikkelen. Met onze nieuwste liften halen we zelfs voor hoogtes van pakweg 25m een hoge performantie van 1.000 dubbele cycli per uur.”
Kan het duurzaamheidsaspect een reden zijn om voor ofwel een miniloadsysteem ofwel een shuttlesysteem te kiezen? “We spreken hier over twee heel verschillende systemen, die elk hun specifieke eigenschappen hebben. Shuttlesystemen winnen weliswaar terrein omdat ze een zeer hoge throughput garanderen. Toch blijven miniloadsystemen – die vooral een zeer hoge opslagcapaciteit garanderen – hun waarde in de markt bewijzen”, legt Hans De Sutter uit. “Dat is ook de reden waarom wij in innovatieve miniloadsystemen blijven investeren. Sowieso kunnen beide systemen heel compact opslaan, bijvoorbeeld door drie bakken of dozen na elkaar in een gang te herbergen. In dat opzicht zijn het allebei duurzame systemen, maar dus elk met hun specifieke troeven. Er zijn zelfs magazijnen waarbij een shuttlesysteem vanuit een miniload wordt herbevoorraad. In omgevingen waar volle containers uit het Verre Oosten worden ontvangen en heel veel goederen ineens moeten worden ingeslagen, kan zo’n combinatie prima werken, bijvoorbeeld voor seizoensgebonden activiteiten zoals fashion en apparel.”
De meerwaarde van energierecuperatie
Veel equipment van TGW is ook voorzien van technologie om energie te recupereren. Dat geldt meer bepaald voor alle miniloadkranen, shuttles, liften en conveyors van de leverancier. Dat betekent dat die systemen bij het afremmen energie opslaan in zogenaamde ‘supercaps’, condensatoren die op strategische locaties in de systemen worden ingebouwd. Die energie kunnen de systemen vervolgens hergebruiken bij het accelereren. Bij shuttlesystemen, bijvoorbeeld, worden zowel energie als data via ‘power rails’ aan de zijkant van het rek aan- en afgevoerd naar zulke supercaps op centrale locaties.
Het KingDrive-conveyorsysteem van TGW – dat een paar jaar geleden op de markt is gezet – is eveneens een sterk staaltje op het vlak van duurzame ontwikkeling. De KingDrive beschikt over een gemotoriseerde roller, wat inhoudt dat de motor in de roller is ingebouwd. Elke roller wordt dan ook individueel aangedreven. Dit systeem zorgt ervoor dat tandwielen overbodig zijn, wat maakt dat de roller minder slijtagevoelig is en minder energie nodig heeft. In vergelijking met andere gangbare systemen op de markt verbruikt het conveyorsysteem van TGW 20 à 30% minder energie. Die nieuwe conveyortechnologie zorgt er tevens voor dat het systeem 60 à 70% minder onderdelen heeft. Daarnaast zal een conveyorrol alleen bewegen als die een doos of bak te verplaatsen heeft. Ook dat spaart energie. Volgens Hans De Sutter zorgen al die elementen samen ervoor dat deze nieuwste generatie conveyors vandaag tot de meest zuinige op de markt behoren. “De zuinigheid van dit systeem was voor Zalando een argument om voor dit type conveyors te kiezen”, klinkt het.
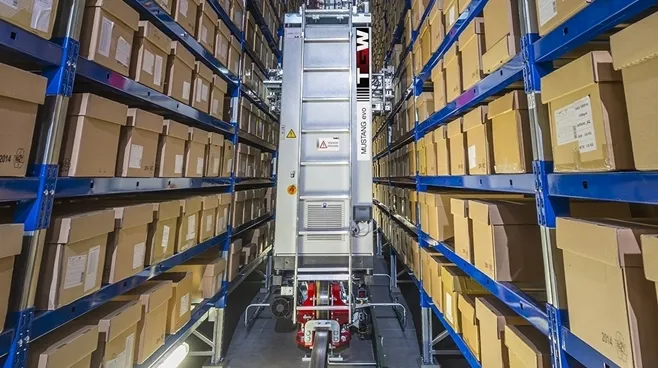
Oog voor Total Cost of Ownership
Op de vraag of bedrijven vandaag wel gevoelig zijn voor onderliggende, duurzame technologische evoluties, krijgen we een bevestigend antwoord. “Bedrijven beseffen steeds vaker dat die technologieën niet alleen inzetten op duurzaamheid an sich, maar dat ze ook toelaten fors te besparen op het vlak van operationele kosten. Met andere woorden, dat duurzame technologieën een positief effect hebben op de Total Cost of Ownership (TCO) van een automatisch systeem. We gebruiken vaak de ijsberg als illustratie, waarbij de CAPEX slechts het topje is, terwijl onder het water heel veel operationele kosten schuilen. Daartoe behoren bijvoorbeeld energieverbruik, onderhoud, de kosten voor het logistieke vastgoed, enzovoort. Op veel van die factoren hebben duurzame technologieën een kostengunstige invloed. Natuurlijk helpt dat om de aandacht voor duurzaamheid bij organisaties te verscherpen.”
Daarnaast benadrukt Hans De Sutter dat we bij de optimalisering van de TCO ook de invloed van het Warehouse Control System niet mogen onderschatten. “Via een weldoordacht WCS is het bijvoorbeeld mogelijk de routes van bakken te optimaliseren, zodat je er steeds zeker van bent dat ze de meest optimale weg over het conveyorsysteem volgen. Via die software wordt ook de opslag geoptimaliseerd, zodat de producten die op dat moment het snelst lopen, steeds op de meest gunstige locaties zullen liggen. Met de juiste software kun je de capaciteit binnen een shuttlesysteem dus optimaal benutten. Ook binnen het ‘decanting proces’ – d.w.z. oversluizen van binnenkomende goederen in bakken – helpt de software voor een maximale vulgraad van de bakken te zorgen. Zo heb je een minimum aan bakken nodig om goederen in het automatisch systeem op te slaan. Omwille van het strategische belang van de bovenliggende software voorzien we bovenop onze automatische systemen binnen onze TGW Software Suite dan ook een eigen WCS en ook WMS (Warehouse Management System).”
Ergonomische werkposten
Verder vormt ook de aandacht voor het welzijn van medewerkers een belangrijk aspect van duurzaam ondernemen.
H. De Sutter: “Als we nieuwe systemen lanceren, schakelen we vaak externe bureaus in om te zien welke ergonomische impact een systeem op de medewerkers heeft. We besteden er vooral aandacht aan dat we de werkposten zo ergonomisch mogelijk inrichten. Daar spelen we sterk op in met PickCenter ONE, waarbij de orderverzamelaar enerzijds de bak met goederen uit het automatisch orderverzamelsysteem voor hem gepresenteerd krijgt en anderzijds de verzenddoos krijgt waarin één of meerdere goederen moeten komen. Daardoor kan de orderpicker heel snel, foutloos én op een erg ergonomische manier de goederen verzamelen. Met het PickCenter ONE kan een orderverzamelaar aan een constant tempo tot 600 orderlijnen per uur verzamelen, terwijl dat cijfer bij veel andere systemen rond de 300 orderlijnen schommelt. Uiteraard is ook hier een goed WCS onontbeerlijk om de bakken en dozen zo efficiënt mogelijk tot bij de orderverzamelaar te krijgen.”
Voor de toekomst ziet TGW met name een belangrijke evolutie richting robotisering binnen magazijnomgevingen.
H. De Sutter: “Een tweetal jaar geleden hebben we ons met de overname van het Duitse robotbedrijf CHM Automatisierungstechnik op die evolutie voorbereid. Je kunt je misschien de vraag stellen of robots niet het werk van medewerkers inpikken, maar we stellen vast dat het op locaties met veel magazijnen – het Nederlandse Venlo, bijvoorbeeld – niet eenvoudig is om voldoende werkkrachten te vinden. In Waalwijk, bijvoorbeeld, heeft het nieuwe magazijn van bol.com – ondanks de sterke automatisering – op piekmomenten nog steeds tot 2.000 medewerkers nodig. In zulke omgevingen kan extra hulp van robots welkom zijn. Robots zullen trouwens niet zozeer pickers vervangen omdat ze het werk sneller kunnen doen, maar eerder omdat ze dag in dag uit beschikbaar zijn. Als we spreken over robotisering binnen magazijnen, hebben we het trouwens niet enkel over robotpicking. Intussen worden al geregeld robots gebruikt om te (de)palletiseren of om gemengde pallets samen te stellen. Dat zijn vaak arbeidsintensieve taken, waar veel medewerkers zich niet toe geroepen voelen. Met de overname van het robotbedrijf beschikken we nu ook over een stevig platform om verdere ontwikkelingen op die verschillende domeinen op te drijven.”