Automatisch verpakken voorkomt schade bij e-commercezendingen
Automatisch verpakken voorkomt schade bij e-commercezendingen
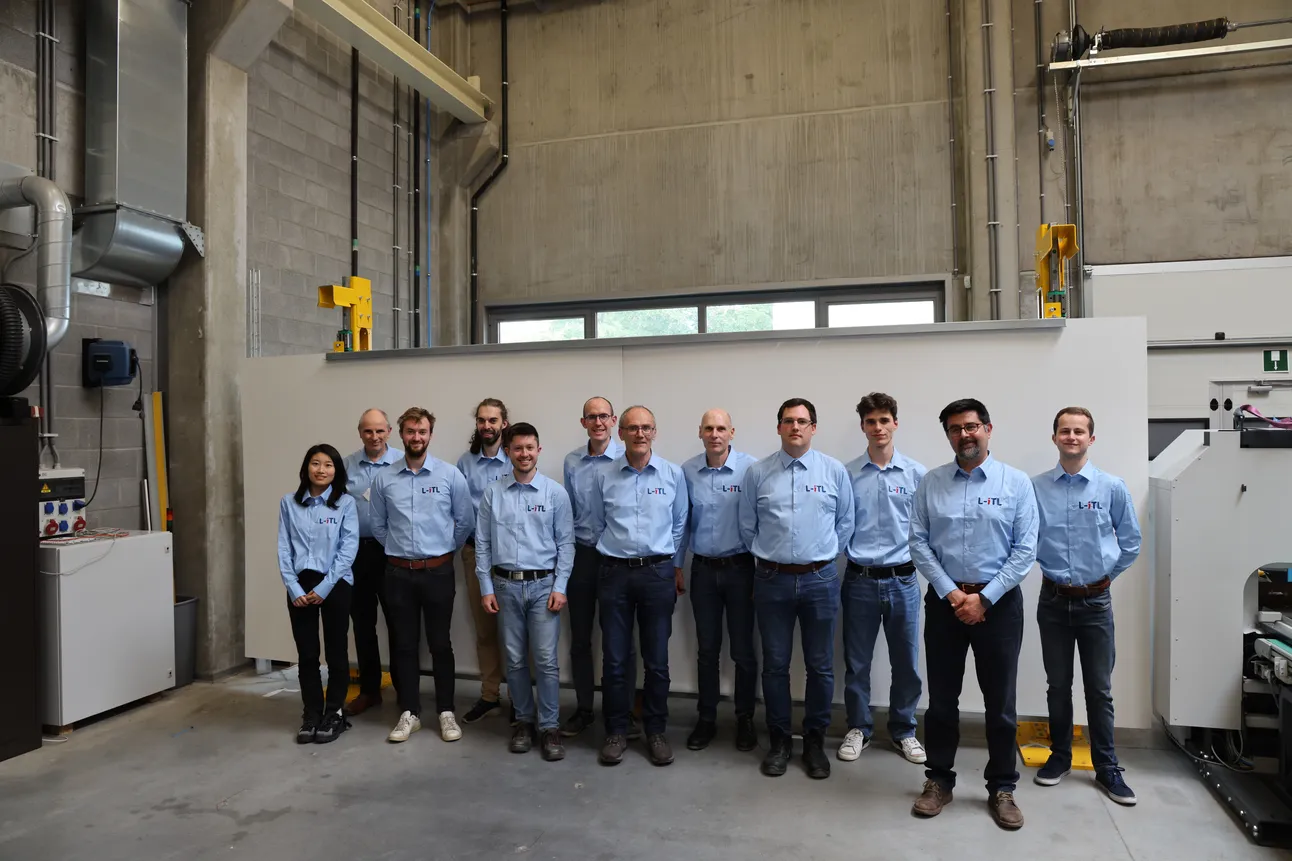
Prof. Marc Juwet (7e van links) en het L-iTL team: “Een aanzienlijk aantal logistiek medewerkers in de distributiecentra zit vandaag nog manueel bestellingen in te pakken. Als je die loonkosten uitspaart, kun je investeren in een machine om dat repetitieve werk automatisch te laten uitvoeren.”
Als er iets is dat zowel e-commercebedrijven als hun klanten kunnen missen als de spreekwoordelijke kiespijn, is het wel schade aan de geleverde producten. De claims die daarmee gepaard gaan, kunnen bedrijven vele honderden euro’s kosten. Om productschade tijdens de verzending te helpen voorkomen, bedachten professor Marc Juwet (KU Leuven) en het team van L-iTL een mogelijke oplossing.
Wie privé of beroepshalve geregeld online aankopen doet, heeft het wellicht al eens meegemaakt: het bestelde product komt beschadigd uit de doos. Dat is uiteraard vervelend voor jou als klant, maar evengoed voor je leverancier. Niet alleen moet die het product zo snel mogelijk opnieuw bij jou geleverd zien te krijgen, maar boven op die financiële schade dreigt hij ook nog eens imagoschade te lijden. Die is misschien minder makkelijk kwantificeerbaar, maar daarom niet minder reëel.
Logistiek testcentrum
De verpakking heeft een aanzienlijk aandeel in het vermijden van transportschade bij de levering van e-commercebestellingen. Door de kwaliteit van die verpakking te verbeteren en het verpakkingsproces te optimaliseren kan dat hardnekkige probleem in de logistiek dan ook voor een groot deel worden opgelost. Tot die conclusie kwamen ook de wetenschappers van het Labo voor innovatieve Technologie voor de Logistiek, kortweg L-iTL. In dat logistieke testcentrum van de KU Leuven, gevestigd op campus Rabot in Gent, werken een vijftiental ingenieurs sinds 2019 aan de ontwikkeling van nieuwe technologische oplossingen voor de opslag, de manipulatie, het interne transport en de verpakking van goederen.
“Aan die laatste logistieke activiteit hebben we niet toevallig al de meeste tijd en aandacht besteed”, vertelt prof. Marc Juwet. Als hoogleraar aan de KU Leuven is hij ook verantwoordelijk voor de R&D-activiteiten van L-iTL. In hun onderzoeksprojecten focussen hij en zijn collega’s op duurzame technologie in de specifieke context van e-commerce. Samen hebben zij de nodige expertise in huis om het volledige onderzoekstraject voor hun rekening te kunnen nemen, van de conceptfase tot het uitvoeren van praktijktesten voor prototypes.
Schadevrij verzenden
Diverse nieuwe verpakkingsoplossingen zijn erop gericht pakketten automatisch te verpakken om een schadevrije verzending te faciliteren. Dat kan in de toekomst mogelijk met een performante horizontale wikkelmachine, ontworpen door Ward Nica, R&D-ingenieur bij L-iTL. Die machine moet het gebruik van opvulmaterialen in de verzenddoos overbodig maken. Tegelijk helpt ze schadeclaims hopelijk definitief naar het verleden te verwijzen.
De werking van de wikkelmachine in het kort: nadat de machine de vorm van de aangevoerde producten heeft gescand, bepaalt een AI-systeem een optimaal wikkelpatroon en stuurt dat vervolgens door naar de automatische servobesturing. Na het eigenlijke inwikkelen van de producten kun je ze eventueel ook automatisch in een verzenddoos laten schuiven, klaar voor verzending.
Combinatie van retentie- en suspensieverpakking
Als uitgangspunt voor het ontwikkelen van de nieuwe oplossingen dienden bestaande innovatieve verpakkingsmethodes als ‘retention packaging’ en ‘suspension packaging’. Bij retentieverpakkingen gebruik je een flexibele folie om de producten op een stuk (golf)karton vast te wikkelen. Terwijl traditionele verpakkingsmethodes afhankelijk zijn van opvulmiddelen als noppenfolie, piepschuim of gekreukt papier om de producten na het inpakken te beschermen, zet een retentieverpakking die producten gewoon vast, houdt ze op hun plaats en beschermt ze zodoende effectiever tegen stoten.
Bij suspensieverpakkingen plaats je de producten tussen twee lagen van een beschermende folie. Net zoals het ophangingssysteem van een wagen – vandaar ook de benaming – vangt die folie de eventuele schokken en impact tijdens het transport van de producten op. Doordat ze op een centrale positie in de verpakking vastzitten, blijven de producten uit de buurt van de punten waar er impact mogelijk is.
Beide methodes, hoe innovatief ook, hebben echter hun beperkingen. Suspensieverpakkingen lenen zich bijvoorbeeld louter tot het transport van zeer lichte producten, terwijl retentieverpakkingen ook geschikt zijn voor zwaardere producten. “Uit valtesten met retentieverpakkingen blijkt bovendien dat ze toch nog kwetsbaar zijn. Met name aan de zijkanten bieden ze slechts een beperkte bescherming,” verduidelijkt prof. Marc Juwet, “zeker als er ook nog eens een scherpe rand aan de producten zit. Dat laatste geldt trouwens ook voor suspensieverpakkingen, al bieden die voor het overige wel een zeer goede bescherming tegen schokken. Een belangrijk nadeel is dan weer dat suspensieverpakkingen aan de dure kant zijn. Bovendien zijn ze moeilijk automatisch aan te brengen en te recycleren.”
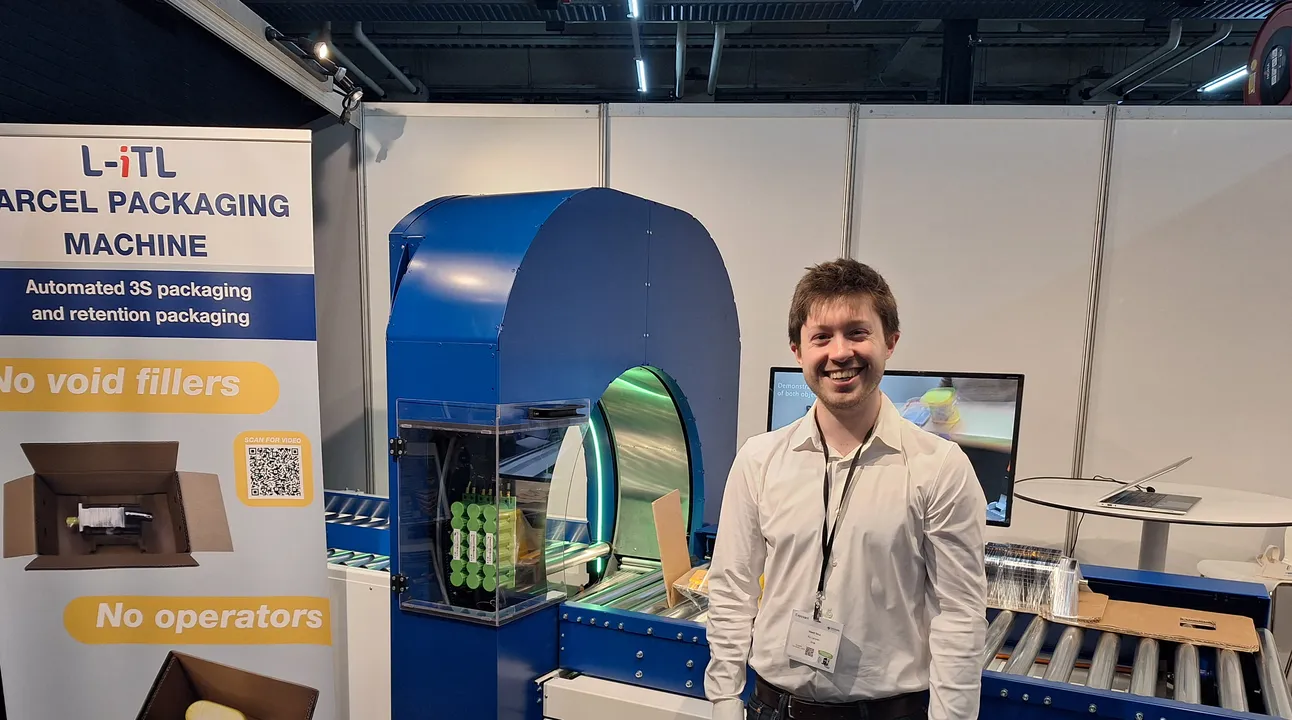
Ward Nica, R&D-ingenieur bij L-iTL, bij de horizontale wikkelmachine die hij heeft ontworpen. Deze wikkelmachine helpt schadeclaims bij e-commerceleveringen hopelijk definitief naar het verleden te verwijzen.
Advanced retention packaging
Met bovenstaande troeven en beperkingen voor ogen, beslisten de onderzoekers van L-iTL het beste van beide verpakkingsmethodes te combineren. Dat resulteerde in de ontwikkeling van twee nieuwe oplossingen. De eerste, onder de noemer ‘advanced retention packaging’ (ARP), leent zich vooral tot het verpakken van zware producten, tot 25 kilogram, die je nog gewoon met de hand kunt opheffen.
Prof. M. Juwet: “Voordat we met de ontwikkeling van die geavanceerde retentieverpakking begonnen zijn, hebben we heel veel valtesten met verschillende soorten opvulmateriaal uitgevoerd. Het opvulmateriaal dat daaruit als beste tevoorschijn kwam, was tweecomponenten polyurethaanschuim. Alleen, als je als klant zo’n doos toegestuurd krijgt, zit je helaas opgescheept met al dat schuim dat niet recycleerbaar is. De meeste bedrijven zijn daar niet mee opgezet, hoe goed het materiaal de inhoud van het pakket ook beschermt.”
Met ARP hebben de professor en zijn collega’s naar eigen zeggen hun ambitie waargemaakt om een oplossing te ontwikkelen die even goed beschermt als dat tweecomponentenschuim. “Om zeker te zijn dat het werkt, hebben we meer dan vijfduizend valtesten uitgevoerd”, aldus de professor. “Naargelang de bescherming die je nodig hebt, kun je het aantal lagen golfkarton aanpassen aan het product dat erop vast gewikkeld zit. Je hoeft je dus niet tot één enkele kartonlaag te beperken. Ook aan het probleem van de scherpe randen hebben we een mouw weten te passen. We wikkelen het product op zo’n manier aan het karton vast dat de folie niet kan scheuren, ook al steekt er aan het product bijvoorbeeld een scherpe punt uit.”
Meest kostenefficiënte oplossing
Gaat het om verpakkingen voor e-commercezendingen, dan moet je die natuurlijk ook aan een voldoende hoog tempo kunnen produceren en vullen. “We mikken op tien dozen per minuut. En dat kan volledig automatisch gebeuren”, benadrukt professor Juwet. “Dat maakt die verbeterde vorm van retentieverpakking eens zo interessant. Zeker als je weet dat een aanzienlijk aantal logistiek medewerkers in de distributiecentra vandaag nog manueel bestellingen zit in te pakken. Als je die loonkosten uitspaart, kun je investeren in een machine om dat repetitieve werk automatisch te laten uitvoeren. Dat is ook waar wij met dit project op gemikt hebben.”
Aan het einde van de rit kwam advanced retention packaging als de meest kostenefficiënte oplossing uit het onderzoek tevoorschijn. De verpakking zelf is ook volledig recycleerbaar: de folie kan bij het PMD en het karton bij het oud papier. Dat alles verklaart meteen ook waarom de oplossing vandaag al bij een aantal bedrijven in gebruik is, vermoedt Marc Juwet. “Voor zware producten, zoals een motor, is de druk vanuit de markt het grootst. Daarbij duikt nu meestal tweecomponentenschuim op, maar dat creëert veel afval bij de klant en daarmee ook veel ongenoegen. Advanced retention packaging biedt hetzelfde niveau van bescherming als dat polyurethaanschuim, maar dan zonder de nadelen.”
3S packaging: Specific, Sustainable, Suspension
Het tweede verpakkingsalternatief dat de professor en zijn collega’s ontwikkelden, onder de noemer ‘3S packaging’, is bij uitstek geschikt om verschillende lichte producten op één kartonnen tray in te pakken. “Het verschil met de bestaande suspensieverpakking is dat we die kartonnen tray op zo’n manier vouwen dat je aan de onderkant van de verzenddoos een luchtlaag krijgt die als een soort bufferzone fungeert om de producten extra te beschermen”, legt prof. Marc Juwet uit.
De drie S’en uit de naam van de nieuwe verpakkingsmethode staan voor ‘Suspension’, omdat de producten ook hier als het ware in de doos zweven of opgehangen zijn; ‘Sustainable’, omdat de gebruikte folie en karton zowel gerecycleerd als recycleerbaar zijn; en ‘Specific’, omdat de oplossing voor elke individuele verpakking het aantal wikkelingen en de wikkelkracht apart berekent. “Het resultaat is een product dat ook in deze verpakking stevig vastzit en waarbij scherpe randen of uitsteeksels evenmin een probleem vormen”, aldus prof. Marc Juwet. “Het maken en vullen van de verpakking kan ook hier semi- of volautomatisch gebeuren, aan een ritme van tot twintig verpakkingen per minuut. Dat alles maakt ook ‘3S packaging’ een kostenefficiënte oplossing die bescherming biedt op het niveau van een vulling met piepschuim.”
Automatische verpakkingslijn
Tot slot stelt professor Juwet nog een verpakkingslijn voor waarmee je zowel de productie van beide nieuwe verpakkingsoplossingen als het verpakkingsproces zelf kunt automatiseren.
In een eerste stap gaat de machine de kartonnen drager op de juiste manier aanmaken. Dat wil zeggen: het karton op het juiste formaat versnijden, er vouwlijnen op aanbrengen en indien nodig het karton in verschillende lagen op elkaar leggen tot de vereiste dikte is bereikt. In een tweede stap komen de bestelde producten op de kartonnen tray op de transportband, manueel of via een robot, en gecentreerd. In een derde stap gaat een scanner de producten automatisch detecteren, scannen en wegen. Bij stap vier schiet een software in actie die het gepaste wikkelpatroon berekent en daarbij rekening houdt met eventuele scherpe randen en punten, het gewicht en de positie van de producten. De vijfde stap is dan het eigenlijke wikkelproces, dat aan hoge snelheid verloopt.
Prof. M. Juwet: “Het verschil met bestaande machines is dat wij de kracht in die wikkelfolie om de vijf graden aanpassen, zo’n zeventig keren per toer dus. Net daardoor krijgen wij die producten echt muurvast op die tray gewikkeld. Zo komt de bestelling ook uit de machine, waarna je ze enkel nog in een doos hoeft te stoppen en die dicht moet plakken. Opnieuw: manueel of automatisch, naargelang je behoefte of je budget. De verpakkingslijn is immers modulair. Je kunt dus manueel een doos nemen en de tray met de producten erin schuiven, maar dat kan evengoed machinaal gebeuren. Die extra module is vrij eenvoudig toe te voegen.”
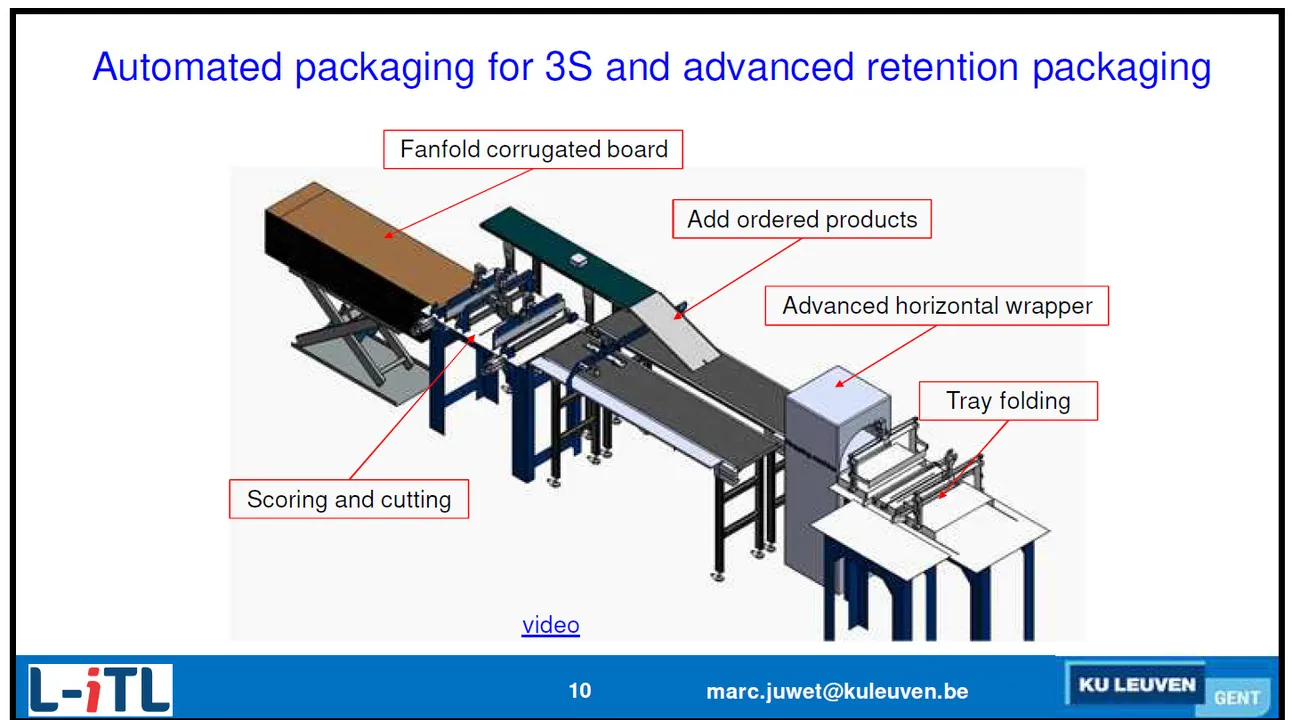
Automatisch verpakken voor 3S en advanced retention packaging
Bron: L-iTL – KU Leuven-Gent
Missie volbracht
Bij het ontwerpen van de automatische wikkelmachine hadden de professor en zijn team drie belangrijke doelstellingen voor ogen. Om te beginnen moest ze het gebruik van opvulmaterialen in de verzenddoos overbodig maken. Daarnaast moest ze de inzet van personeel voor het verpakken van de bestellingen overbodig maken of op zijn minst reduceren. En last but not least moest ze ervoor zorgen dat de bestellingen tijdens de levering geen schade meer konden oplopen.
“Vooral aan dat laatste aspect hebben we heel veel aandacht besteed”, besluit professor Juwet. “En tot dusver hebben we daarover nog geen enkele klacht ontvangen. De bedrijven die de oplossing vandaag al gebruiken, zeggen dat ze goed werkt. Daarbij komt dat diezelfde oplossing perfect beantwoordt aan de nieuwe regelgeving rond verpakkingen. En als je ten slotte ook de kostprijs in rekening brengt, dan komt onze oplossing ook nog eens goedkoper uit dan wat die bedrijven tevoren gebruikten.”
JDP
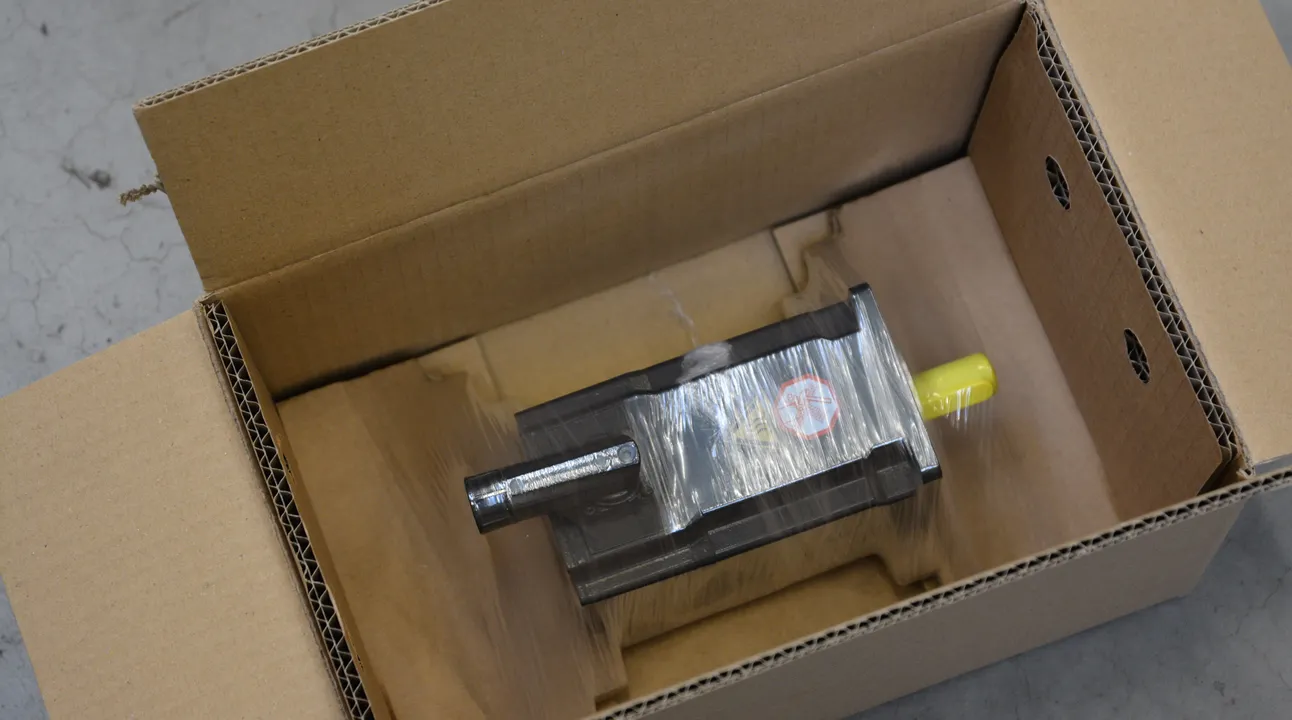
Advanced retention packaging: meerdere lagen golfkarton dienen als buffer voor de ingepakte motor.
Premium
Deze inhoud is enkel leesbaar voor ingelogde Value Chain abonnees.
Heeft u een abonnement op het Value Chain informatiepakket? Meldt u aan via onderstaande knop en lees het gewenste artikel of magazine online.