Case Study
Empowers Global Beverage Giant to Build a Smart Warehouse
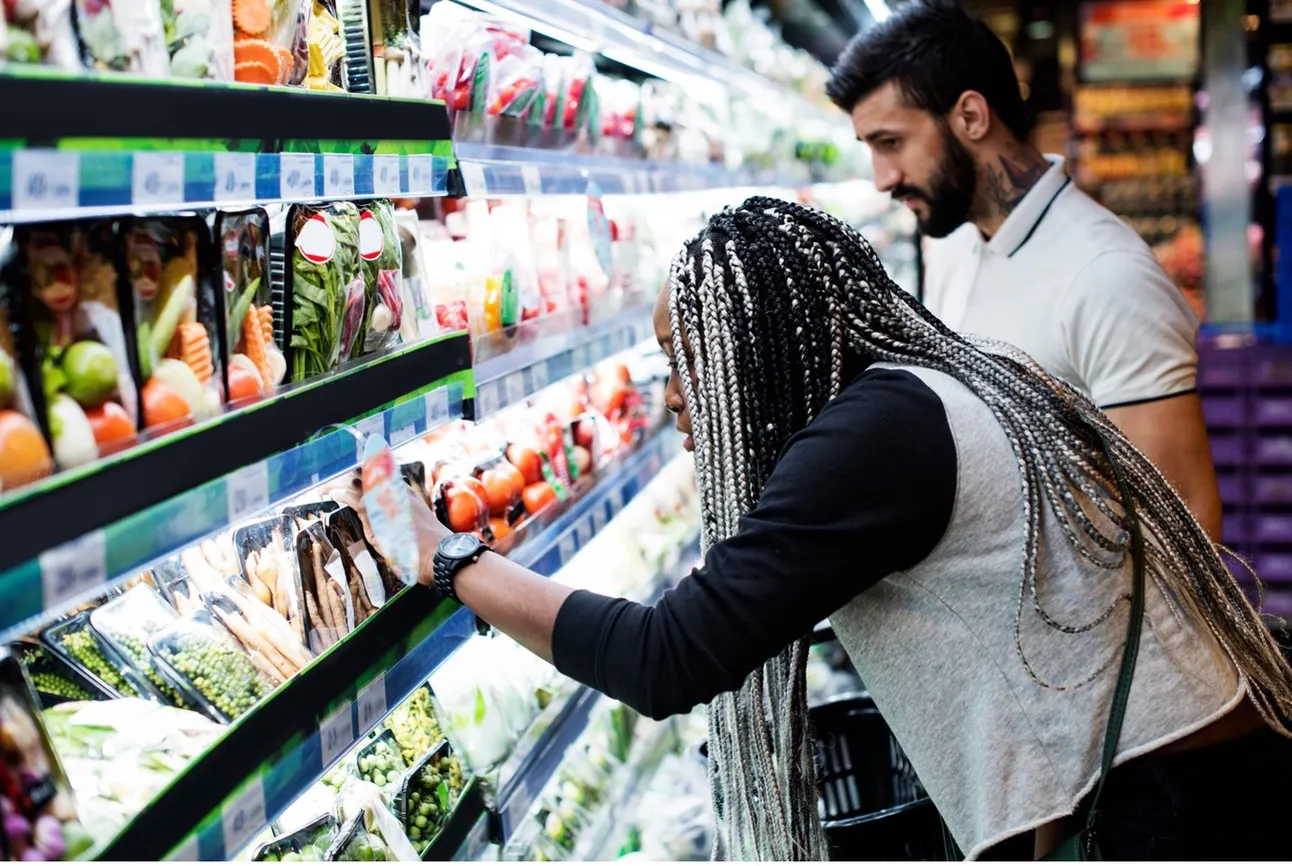
Due to the natural suitability of beverage materials for pallet solutions, we designed a tailored smart warehousing system for the customer based on the Storage Mix subsystem. This solution increases storage density, enhances inbound and outbound efficiency, reduces operational costs, and helps optimize the customer’s supply chain warehousing system.
The customer’s storage area has an irregular shape. The Storage Mix subsystem, powered by Atomix’s four-way pallet shuttles, enables flexible layouts to fully utilize warehouse space, achieving a space utilization rate of over 90%.
In warehouses with heights below 10 meters and separated inbound/outbound areas, traditional pallet automation solutions require numerous devices to meet storage and operational needs, leading to low utilization rates.
Different materials and batches require distinct storage conditions. In high-density storage, honeycomb inefficiency can drastically reduce slot utilization. Atomix’s intelligent material and slot allocation algorithms optimize warehouse zoning, minimizing idle slots and reducing storage waste.
The system intelligently connects storage locations and inbound/outbound processes to maximize operational efficiency. By dynamically adjusting the number of devices and utilizing an advanced scheduling system, Atomix ensures smooth and efficient material flow throughout the warehouse.