3D-technologie niet langer ‘nice to have’
Virtual reality optimaliseert productie bij Pringles
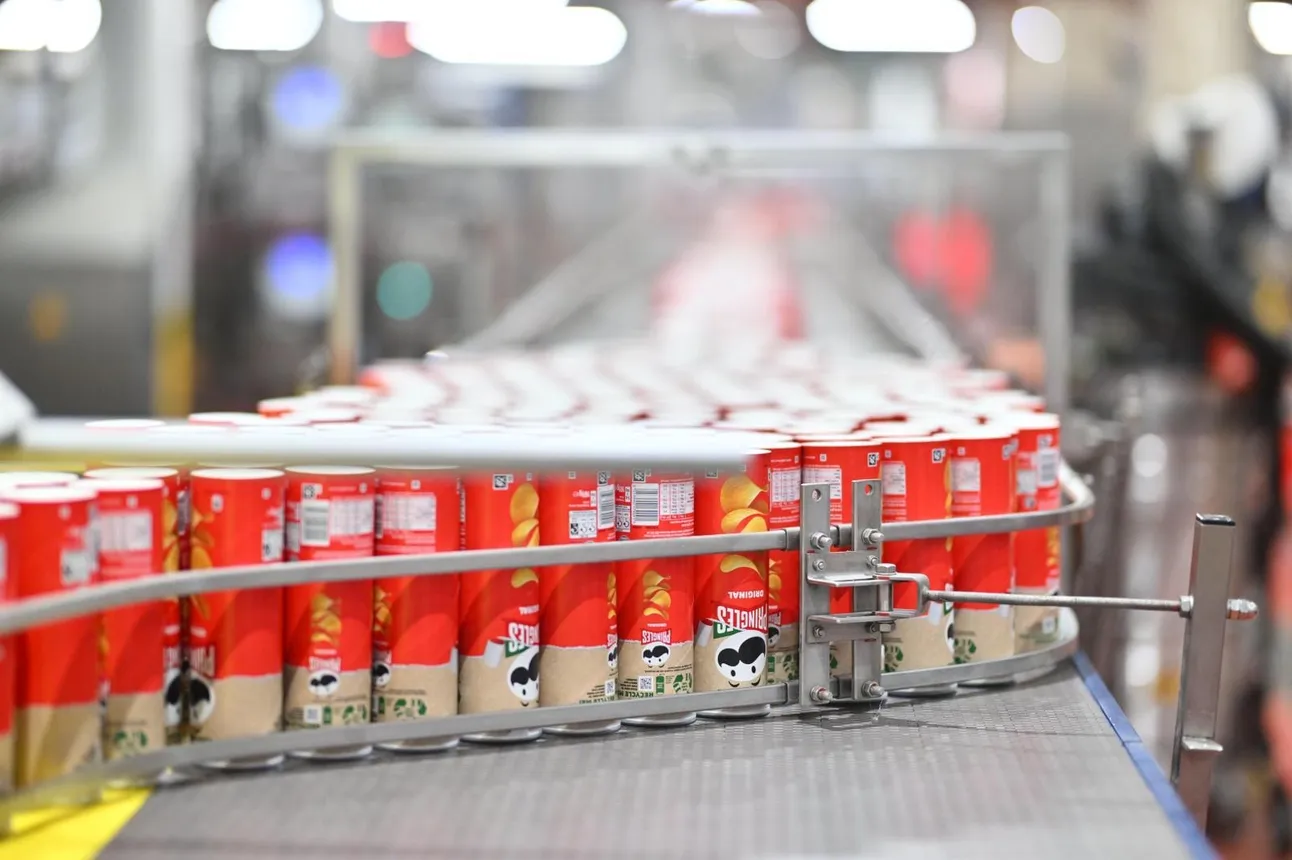
Jaarlijks rollen er in Mechelen twee miljoen tubes Pringles-chips van de band.
De Pringles-fabriek in Mechelen wil de operationele training van medewerkers – en bij uitbreiding het hele productieproces – optimaliseren met behulp van virtual reality (VR). Pringles werkt daarvoor samen met het Mechelse bedrijf Spectr BIM en studenten van de Howest-hogeschool in Kortrijk. De vestiging is daarmee een pionier binnen de wereldwijde Kellanova-groep, die de innovatie nu naar andere productiesites wil uitrollen.
In de Pringles-fabriek in Mechelen rollen elke dag twee miljoen tubes van de band, goed voor 104 ton aardappelchips per jaar. Daarvoor moet de productie de klok rond draaien, zeven dagen per week, want elke ‘downtime’ resulteert in onmiddellijk verlies. Bovendien kent het bakproces een hoog risico op productieverlies. “We kunnen de oven niet zomaar aan- en uitzetten of openen voor trainingen om de werking aan de binnenkant op te volgen”, vertelt Tom De Weerdt, senior technical operations manager bij Kellanova. “Daarvoor moet de oven telkens eerst afkoelen en dat vraagt niet alleen tijd, maar ook extra energie.” Hetzelfde geldt daarna voor het opstarten van de oven.
Om de downtime tot een minimum te beperken, ging de Mechelse vestiging op zoek naar een innovatieve manier om de installaties open te stellen. Kellanova keek al snel in de richting van virtual reality en klopte aan bij het Mechelse bedrijf Spectr BIM. Dat visualiseerde de CAD-tekeningen van de machines met behulp van 3D-technologie. “3D-modelling is heel duur, maar de kostprijs van deze visualisatietechniek op basis van de CAD-tekeningen ligt veel lager. Daardoor is de terugverdientijd korter”, zegt Lode Snackaert, zaakvoerder van Spectr BIM. Het bedrijf gebruikt daarbij software van Unity. Als de productiehal van Pringles zou uitbreiden van zes naar bijvoorbeeld tien productielijnen, dan kost het dankzij de visualisatie van de CAD-tekeningen weinig moeite om ook de VR-omgeving een update te geven.
Lode Snackaert spreekt van een uniek project in België. Kellanova gebruikt de VR-technologie op een nieuwe manier. Vandaag is 3D-technologie nog vaak een ‘nice to have’ waarvan bedrijven het volledige potentieel niet benutten. Kellanova bewijst dat de technologie een belangrijke meerwaarde biedt. De samenwerking toont het potentieel van de combinatie van academische innovatie met industriële expertise om productieprocessen grondig te hertekenen.
De kracht van visualisatie
De ontwikkeling van een eerste ‘proof of concept’ verliep in samenwerking met studenten van de Howest-hogeschool. Zij stonden in voor de animaties in de VR-omgeving, zoals het draaien van de transportbanden, het bakproces en bijhorende rookeffecten. “In het verleden werkten we al met Howest samen”, zegt Tom De Weerdt. “De hogeschool staat bekend voor haar ontwikkelingen op het vlak van VR en andere visualisatieoplossingen. De studenten maakten hun eindwerk rond het project. De samenwerking verliep zo goed en de resultaten zijn zo straf dat we hen als ‘developers’ in dienst hebben genomen.” Alles bij elkaar nam de ontwikkeling amper zes maanden in beslag.
Dankzij de ontwikkelde VR-technologie voeren de teams voortaan via een interactieve visualisatie verschillende procesoptimaliseringen uit, terwijl de productieactiviteiten gewoon blijven doorlopen. “Het zorgt voor aanzienlijke tijdsbesparing en continuïteit in de productielijnen”, aldus Tom De Weerdt. “Het nieuwe VR-systeem zorgt er ook voor dat de technische teams sneller kunnen ingrijpen bij problemen. En dat biedt veel voordelen, waaronder meer efficiëntie, energiebesparing, minder afval en minder verlies van grondstoffen.”
Nieuwe medewerkers krijgen op dit moment een opleiding in een klaslokaal en in de productiehal, maar dankzij de VR-technologie kan dat binnenkort ook vanop afstand. “Je kunt wel allerlei zaken op tekeningen en slides tonen, maar wanneer je alles visualiseert, krijg je nieuwe inzichten”, licht Tom De Weerdt toe. “In de VR-omgeving visualiseer je onmiddellijk de operationele kant van de werking zonder dat medewerkers op de productievloer hoeven te komen.”
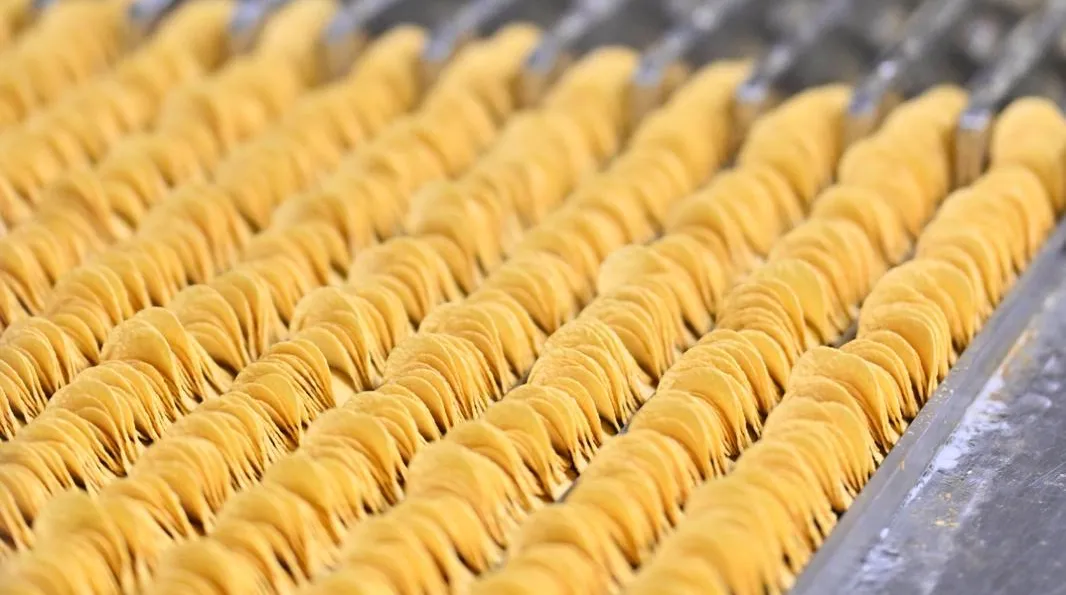
Elke downtime in de productie leidt onmiddellijk tot verlies.
Gekoppeld aan data
“De VR-omgeving biedt ons veel meer flexibiliteit bij de training die we voor onze mensen voorzien en ze laat ook een risicovrije simulatie toe van complexe scenario’s die anders te gevaarlijk zijn”, aldus de operations manager. “Zo willen we ook scenario’s simuleren die zich in het verleden hebben voorgedaan, om te zien wat beter kan. In het kader van ‘troubleshooting’ hebben we zo ook meer data om het probleem aan te pakken.” De VR-toepassing maakt gebruik van echte productiedata uit de eigen productiehal, zoals de temperaturen en olieniveaus.
De VR-replica van de productiehal is tot in de kleinste details uitgewerkt. Dat is meteen wat de toepassing zo innovatief maakt en van doorsnee VR-toepassingen onderscheidt. Door de VR-omgeving aan de productiedata te koppelen, kunnen defecten sneller worden opgespoord. Als pakweg een klep in de machine niet meer schakelt, dan is dat op de VR-beelden zichtbaar en kunnen productieoperatoren het probleem vlot detecteren. “Zonder VR zouden we enkel de leidingen zien”, zegt Tom De Weerdt.
De toepassing biedt techniekers en operatoren ook de optie om bepaalde toevoerlijnen te selecteren en bijkomend te visualiseren. “Gezien de wirwar van leidingen in de productiehal is dat geen overbodige luxe. Dankzij de technologie kunnen ze heel snel door de hal bewegen, wat in de realiteit niet mogelijk is, of kunnen ze gesloten stukken van de installaties blootleggen en zo de mechaniek bekijken. Zeker in de context van opleidingen is dat een van de grootste troeven.”
Voortrekker op vlak van innovatie
Het nieuwe project maakt deel uit van een grotere investering van Kellanova Europa die gericht is op het verbeteren van de operationele efficiëntie en het stimuleren van innovatie binnen het Europese productienetwerk aan de hand van geavanceerde technologieën zoals ‘digital twins’, artificiële intelligentie en smart manufacturing. De VR-toepassing plaatst de Mechelse vestiging alvast op het voorplan wat innovatie betreft. Andere plants kijken met grote ogen naar de ontwikkelingen en tonen interesse om de toepassing over te nemen. Maar evengoed kiest de fabriek ook op andere vlakken voluit voor innovatie. Zo wist ze haar waterverbruik met de helft terug te dringen door de bouw van een recuperatie-installatie voor afvalwater. Dat gebeurde in samenwerking met Pantarein uit Mechelen. Daarnaast introduceerde Pringles in Mechelen ook als eerste een duurzame verpakking met papieren bodem.
Wat het VR-project betreft, is het nu al uitkijken naar de volgende stappen. “We willen het toepassingsgebied graag uitbreiden naar andere kritische taken zoals onderhoud en we kijken ook naar het gebruik van mixed reality.”. Daarbij zien medewerkers de echte omgeving, aangevuld met extra ‘visuals’ voor bijkomende (realtime) informatie. “Bij de eerste initiaties waren onze medewerkers alvast erg enthousiast”, besluit Tom De Weerdt. “Het is belangrijk om hun het potentieel van de technologie spontaan te laten ontdekken en naar hun feedback te luisteren. In de toekomst willen we ook de hardware opschalen en meer VR-brillen aankopen.”
FF
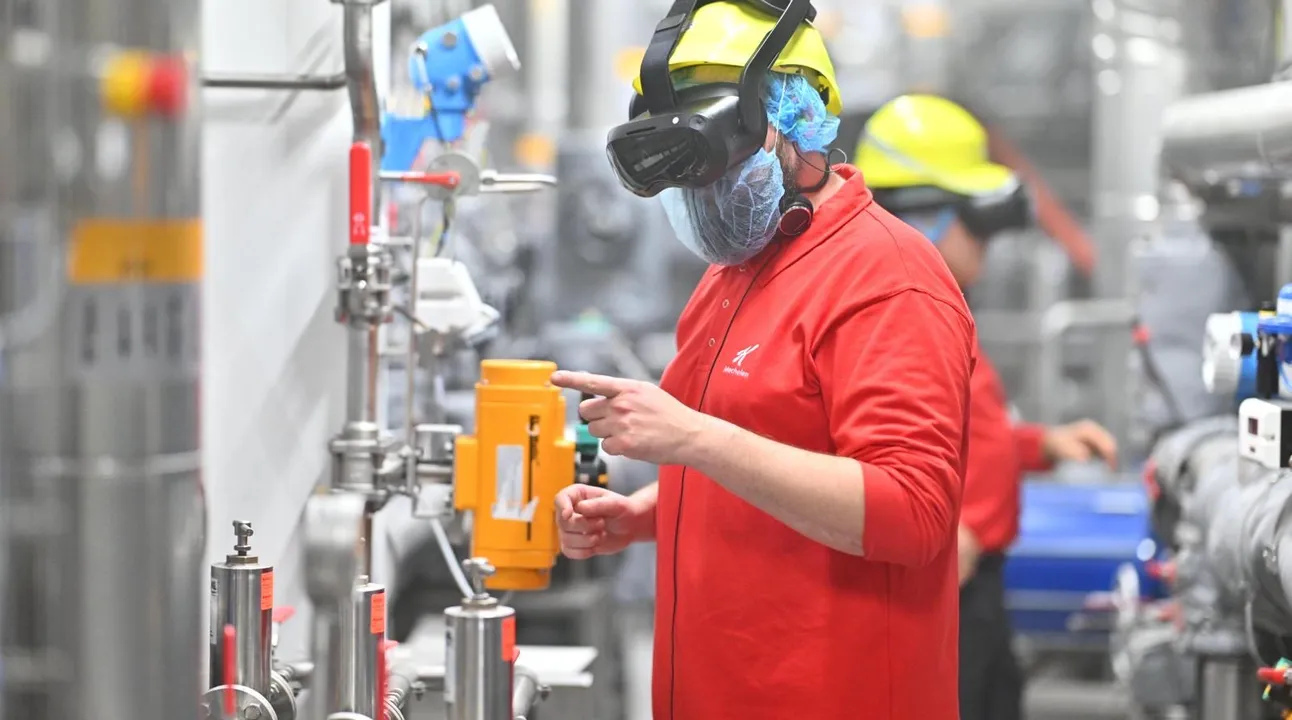
Dankzij de VR-toepassing kunnen operatoren onderdelen van de installatie zien die normaal onzichtbaar zijn.
Premium
Deze inhoud is enkel leesbaar voor ingelogde Value Chain abonnees.
Heeft u een abonnement op het Value Chain informatiepakket? Meldt u aan via onderstaande knop en lees het gewenste artikel of magazine online.