3D-printing als voorraadoplossing
Maakt additive manufacturing verwachtingen waar?
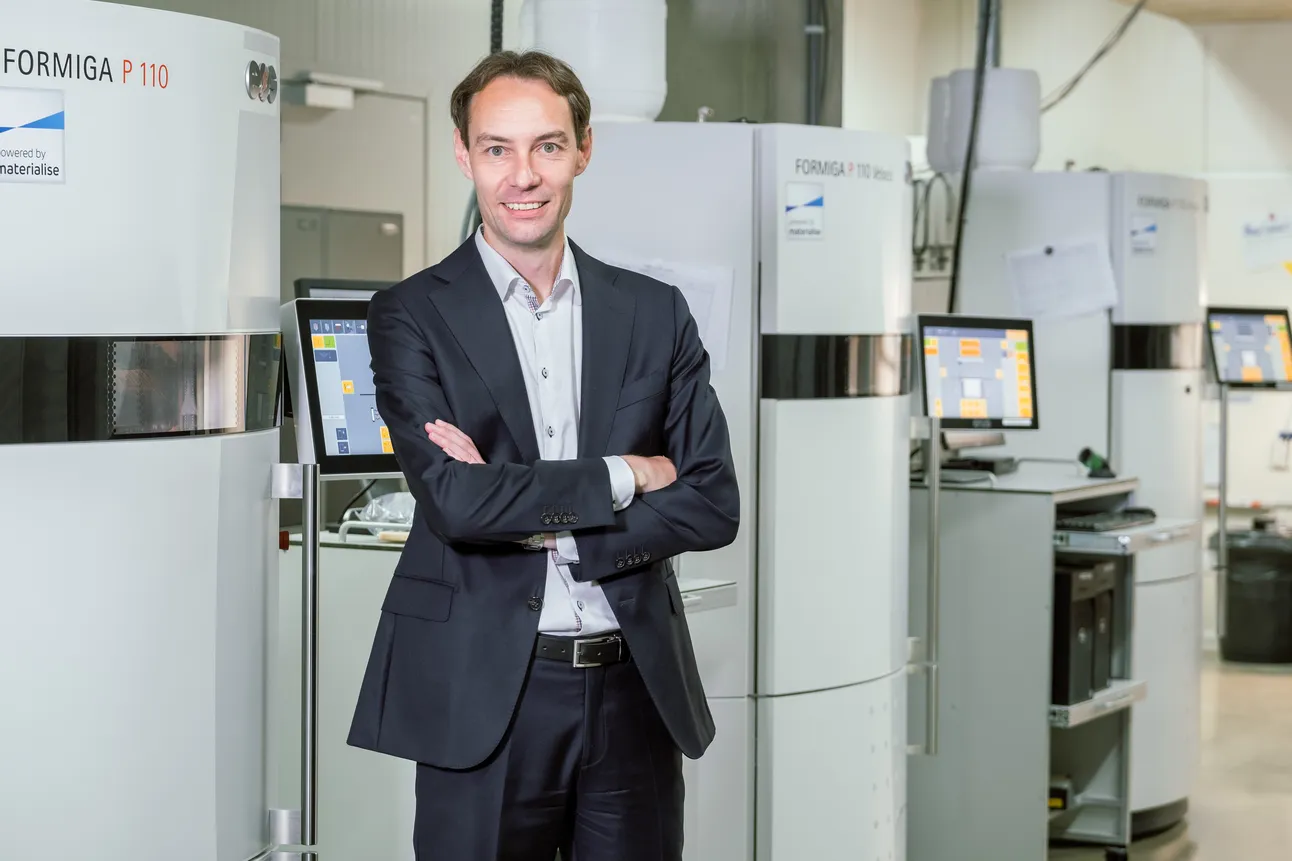
Jurgen Laudus, executive vice president bij Materialise: “Met 3D-printing spaar je de kosten voor het vervaardigen van een matrijs en de opstartkosten van de productielijn uit. Bovendien neemt je voorraadlast af.”
Exact tien jaar geleden publiceerde adviesbureau McKinsey dat ‘additive manufacturing’ het potentieel bezit om de structuur van de industrie en de supply chain te veranderen. Vandaag lijkt het vooralsnog niet zo’n vaart te lopen. Professor Joost Duflou van de KU Leuven wijst op verschillende beperkingen, terwijl 3D-printingbedrijf Materialise net aangeeft dat 3D-printing over de nodige maturiteit beschikt om veel productie-ecosystemen te ondersteunen.
Een rapport van McKinsey voorspelde in 2014 dat we tegen het jaar 2025 zowat dertig tot vijftig procent van de onderdelen en wisselstukken zouden produceren met behulp van 3D-printers. Dat moest een kostenbesparing van veertig tot 55 procent opleveren ten opzichte van conventioneel vervaardigde producten. “3D-printing lijkt klaar als levensvatbaar alternatief voor klassieke productieprocessen in een toenemend aantal toepassingen”, klonk het toen veelbelovend. “De voordelen ten opzichte van andere productietechnologieën kunnen leiden tot ingrijpende veranderingen in de manier waarop we ontwerpen, ontwikkelen, produceren en ondersteunen. Relatief kleine faciliteiten met mogelijkheden rond ‘on-site additive manufacturing’ vervangen in de toekomst grote regionale magazijnen.”
Is de boom uitgebleven?
Met als veelbelovende premisse ‘logistieke sector bereidt zich voor op boom 3D-printing’ ging het Vlaams Instituut voor de Logistiek (VIL) in 2014 op zoek naar de opportuniteiten van 3D-printing voor de logistiek van wisselstukken. Dat onderzoek bleek eerder ontnuchterend en concludeerde dat de grote doorbraak nog even zou uitblijven. ING hanteerde in 2021 eveneens een genuanceerde kijk. Het kondigde aan dat 3D-printing pas tegen 2040 vijf procent van alle productiegoederen zou vertegenwoordigen en zag nog een nood aan technologische doorbraken.
Volgens professor Joost Duflou van het departement werktuigkunde aan de KU Leuven is de toepasbaarheid van 3D-printing binnen de supply chain nog altijd beperkt. “De snelheid van hoogwaardig 3D-printen van metalen stukken is nog steeds laag en de afwerkingsnauwkeurigheid vergt vaak nabewerkingen”, weet hij. “Dat proces heeft veel meer voeten in de aarde dan even snel een bestand afdrukken. Dat maakt het dan ook moeilijk om flexibel onderdelen op maat te printen als oplossing voor wisselstukbeheer.”
De KU Leuven deed de afgelopen jaren onderzoek naar het gebruik van snelle en goedkope 3D-printoplossingen. De researchers focusten zich hoofdzakelijk op het vervaardigen van wisselstukken in polymeren bij het herstel van elektrische en elektronische apparaten. “De mogelijkheden zijn hier nog beperkt vanwege de relatief lage sterkte-eigenschappen die je met dergelijke ‘fused deposition modelling’ systemen verkrijgt”, geeft de professor aan.
Niet waarom, maar hoe
Het Belgische Materialise geldt als een van de pioniers op het vlak van 3D-printing. Het bedrijf startte als een spin-off van de KU Leuven en richt zich in hoofdzaak tot de medische en industriële sector. Jurgen Laudus, executive vice president van de industriële tak van Materialise, geeft aan dat 3D-printing wel al op verschillende manieren als voorraadoplossing wordt toegepast. “De materiaaleigenschappen vormen geen belemmerende factor en de mogelijkheden zijn erg uitgebreid. We merken dat de meeste productiebedrijven zich bewust zijn van de potentiële meerwaarde. In de sector gaat het niet langer om de ‘waarom-vraag’, maar eerder om de ‘hoe-vraag’. Producenten vragen zich vooral af welke stukken in aanmerking komen en hoe ze die kunnen integreren.”
Als voorbeeld van hoe additive manufacturing in de praktijk werkt, wijst Jurgen Laudus op het parcours van de fabrikant van landbouwmechanisatie CNH Industrial. “De producent van voertuigen en machines tastte al lange tijd de mogelijkheden van 3D-printing af. De covidpandemie heeft die intenties in een stroomversnelling gebracht. Door de moeizame of in sommige gevallen zelfs volledig weggevallen aanvoer van onderdelen, bleek het onmogelijk om de producten nog tijdig af te werken en uit te leveren.”
CNH had bijgevolg drie opties. Het bedrijf kon onvolledige assemblages bouwen en ze opnieuw bewerken zodra de onderdelen arriveerden, tegen een kostprijs van meer dan 1.750 euro en met het risico op laattijdige leveringen. Het bedrijf kon ook de assemblage volledig stopzetten tot de onderdelen arriveerden, tegen een kostprijs van ongeveer 189.000 euro. Of CNH kon het onderdeel 3D-printen aan vijftien euro per stuk in plaats van de gebruikelijke twee euro, wat resulteerde in een totale kostprijs van 806 euro, maar met een doorlooptijd van slechts een week.
Functionele onderdelen
“Door te kiezen voor additive manufacturing slaagde CNH er met beperkte extra kosten toch in zijn deadlines te halen en de klanten tevreden te stellen”, vertelt Jurgen Laudus. “Na die succesvolle samenwerking maakten we samen met CNH werk van een volledig geïntegreerde additive manufacturing-strategie.”
De case illustreert naar zijn mening perfect de mogelijkheden van 3D-printing. “De techniek passen we binnen productie- en voorraadomgevingen het vaakst toe voor onderdelen in plastic en metaal. Het gaat meestal om functionele stukken die je van buitenaf niet waarneemt.”
Jurgen Laudus beaamt dat een 3D-geprint onderdeel significant duurder uitvalt dan een via massaproductie vervaardigde component. Al moet je het plaatje volgens hem ruimer bekijken. “Je bespaart de kosten voor het vervaardigen van een matrijs en de opstartkosten van de productielijn. Bovendien neemt je voorraadlast af. Het volstaat om een beperkte stock aan te houden en die via additive manufacturing flexibel aan te vullen. Voor veel onderdelen met een formaat dat in een schoendoos past, zal de kosten-batenanalyse gunstig blijken. Voor grote stukken of onderdelen waar esthetiek of gladheid essentieel zijn, is 3D-printing dan weer minder aangewezen.”
Andere praktijkcases van Materialise situeren zich onder meer in de brillen-, brandstof- en luchtvaartindustrie. “Een bijkomend pluspunt is dat je geen hoge volumes hoeft te produceren”, vervolgt Jurgen Laudus. “Klanten starten niet zelden met een kleine serie, om nadien verder op te schalen. De voorbereiding en het printwerk voeren wij meestal uit, maar het gebeurt ook dat de klant na verloop van tijd een eigen installatie wil plaatsen. We bieden de bedrijven dan praktische ondersteuning. Wat niet werkt, is het installeren van een huis-tuin-en-keukenprinter. Machine- of productonderdelen moeten aan bepaalde specificaties voldoen. Je kunt niet riskeren dat je de vereiste kwaliteit of levensduur niet bereikt omwille van een geprint onderdeel dat het na verloop van tijd laat afweten.”
Hoewel professor Duflou niet onverdeeld overtuigd is van de toepasbaarheid van 3D-printing bij het vervaardigen van reserveonderdelen en wisselstukken, gelooft hij sterk in de mogelijkheden om te personaliseren. “Er bestaan tegenwoordig al heel wat mooie voorbeelden van medische toepassingen van additive manufacturing. Ze komen tegemoet aan de noden van individuele patiënten”, concludeert hij.
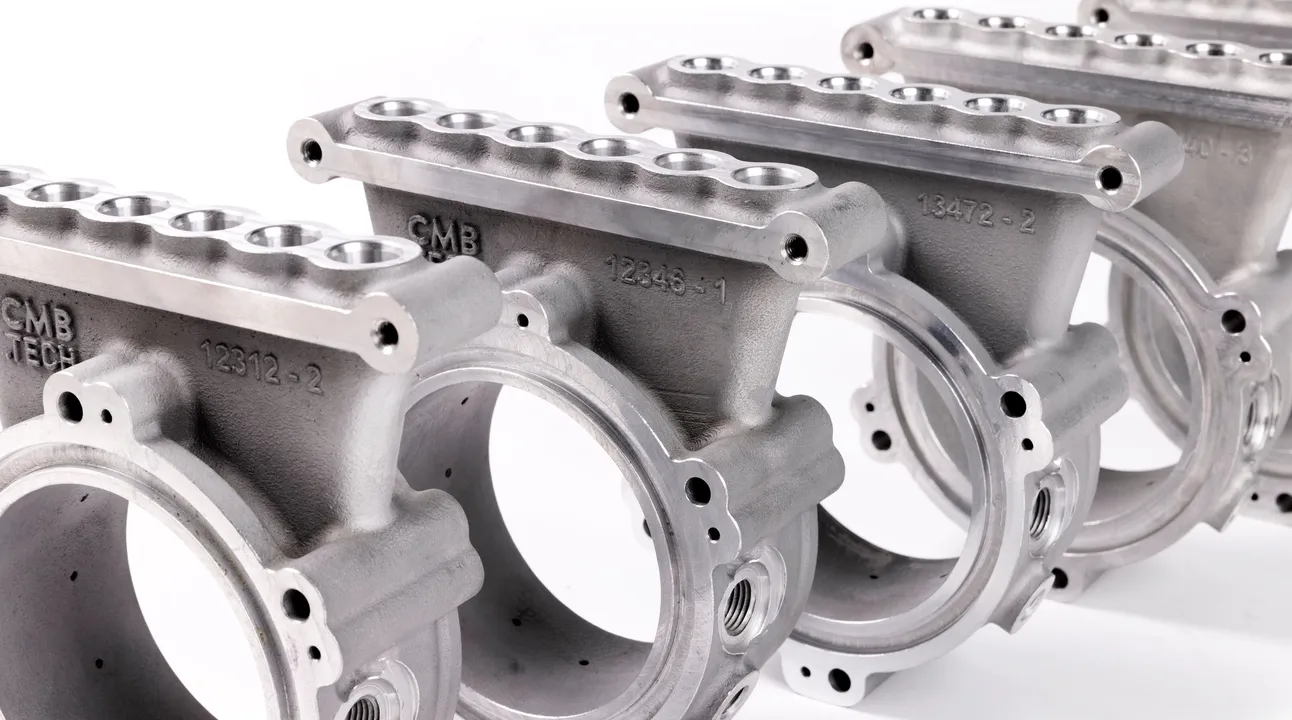
Foto: CMB.TECH
3D-printing en de transportsector
Projecten met een omvangrijke schaalgrootte vinden we vooral terug in de transportsector. De Duitse spoorwegmaatschappij Deutsche Bahn onderhoudt bijvoorbeeld een digitaal magazijn met virtuele technische tekeningen van reserveonderdelen. Die onderdelen kan het op verzoek laten printen bij het 3D Printing Platform van leverancier Essentium in Neumunster. Momenteel zijn er ongeveer duizend modellen beschikbaar. DB wil dat aantal verhogen tot tienduizend onderdelen in 2030. Het moet Deutsche Bahn helpen om de leveringssnelheid te verhogen en de kosten te verlagen. Door onderdelen met een kleine oplage op aanvraag te maken, hoort een voordeel te ontstaan ten opzichte van de productie en opslag in grote hoeveelheden.
MAN Truck & Bus, de in München gevestigde producent van bedrijfsvoertuigen, werkt dan weer samen met BASF-spin-off en digitaal platform Replique om reserveonderdelen te 3D-printen. Het stelde MAN in staat een bronzen spruitstuk voor een scheepsmotor te vinden dat niet op voorraad was, terwijl de gietmal voor het onderdeel evenmin beschikbaar bleek.
KD
Inloggen/registreren
Om deze content te lezen, moet u zich inloggen.
Log in of registeer nu via onderstaande knop en krijg toegang tot deze inhoud.